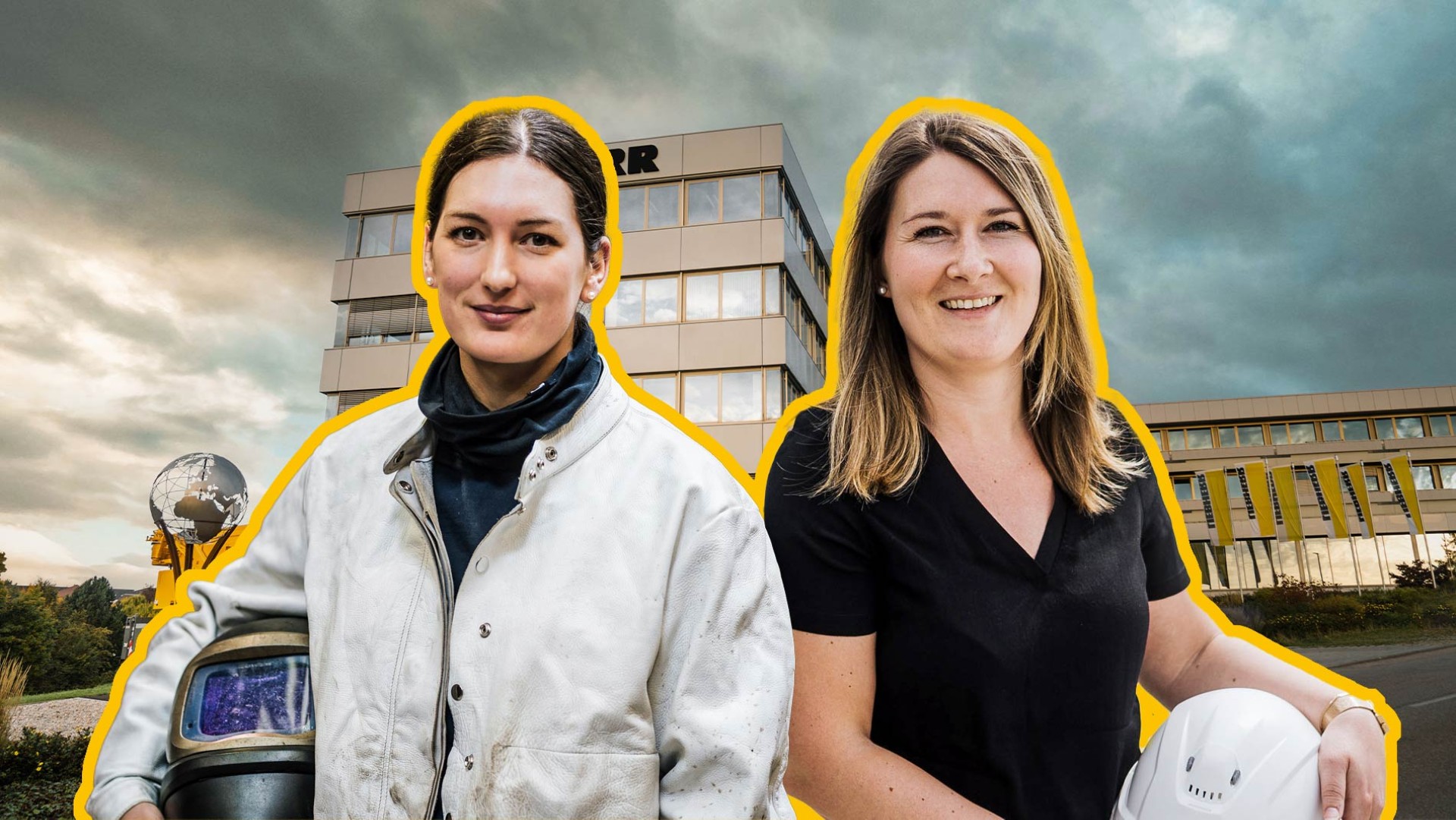
7 minutes | magazine 02/2022
In conversation
Stable and quick-witted? Then head for the crane industry.
It’s a man’s world...
...that can still be said about some industries. The crane sector is one of them as well – and yet a change is noticeable: female engineers and fitters, designers and welders can also be found at Liebherr-Werk Ehingen (LWE). And it is undoubtedly a benefit to talk to them about careers, everyday working life and working together as a team.
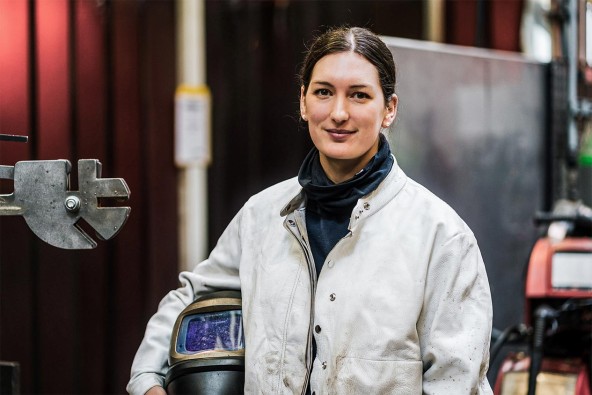
Kathrin Prinz - welding trainer at our Welding Competence Centre (SKZ)
Ms Prinz, together with your two colleagues, you are in charge of welding training and quality at LWE. How did you get this job?
When I was young, I worked in a metalworking shop with 10 men during the school holidays. After school, I actually wanted to study architecture, but instead I followed my father’s wishes (he manages a woodworking shop) that all his children should first learn a trade “as a good basis!” So I trained as a metalworker and technical designer at the metalworking shop. After another three years there, I moved to a welding training centre run by the Deutscher Verbandes für Schweißen und verwandte Verfahren e. V. (DVS) (German Federation of Welding and Associated Processes) where I was in charge of welding journeymen and master craftsmen examinations and whilst working there I underwent training as a master craftsman, welder and welding centre manager. Before I came to LWE, I worked at a construction company as a master craftsman and welding supervisor in structural steelwork.
Kathrin Prinz (29) is a welding trainer at our Welding Competence Centre (SKZ). This is where she teaches apprentices the basics and where experienced welders have to come to pass a welding examination every three years. The customer service engineers who work in Germany and elsewhere at LWE’s sales and service sites also have to take examinations at the Ehingen SKZ.
So how did you end up at Liebherr?
Whilst I was training as a welder, we were given the opportunity to visit the Liebherr plant in Ehingen. I was very interested in the challenges posed by using high-tensile fine grained steel. And also, how Liebherr was developing and driving forward this whole sector.
Do you still get your hands dirty at the SKZ?
Yes. Welding is challenging and it requires training and lots of experience. In particular, I demonstrate various welding positions for new apprentices. Some of the apprentices and those taking the exams are fairly reticent or withdrawn initially. But when we’ve been working together for a week, we soon find a way of getting on.
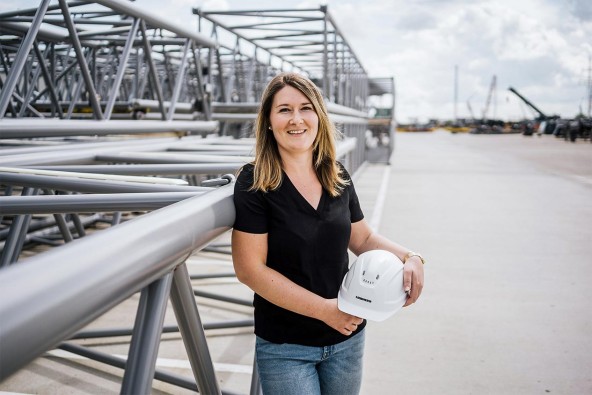
Jennifer Enderle - designer
Ms Enderle, you are a boom designer. How did you get here?
I became interested in technology and engineering very early in life. I attended an all-girls grammar school and for one year every Friday afternoon I went to the “Student Engineering Academy (SIA)”, where I was introduced to electrical engineering, robotics, injection moulding and other exciting things. The working group at the time made me really interested in pursuing engineering as a job. When I then found out about the Ulm Model sandwich course, a combination of a full degree course combined with a full apprenticeship, I thought the concept, pay and the good prospects for finding a job at the end and getting into a job at a good level were all great. And, of course, Liebherr is a company with a fascinating product which offers a very wide range of training.
Jennifer Enderle (31) holds two qualifications – a Bachelor of Engineering and a certificate of proficiency as an industrial mechanic. She works as a designer. In a team comprising 17 colleagues, only one of whom is female, she develops fly jibs for the Liebherr telescopic cranes of the future to ensure that they always comply with the current safety and customer requirements.
I have worked as a designer of fly jibs since 2016 – from designing individual components and detailed design of the entire assembly to the decision of what we do in what position and using what production process – the whole thing is part of our planning process. The requirements placed on the product are easy to list – safety, functionality, customer benefits, economy, compliance with all standards and always attempting to make everything even easier and safer. We deal with almost every department in the company and are always learning new things! And whilst we’re talking about learning – for the last nine months, I have been the training officer in my department, in other words I am the person to come and see about training and internships for students. It’s always fun working with school and university students and seeing how they develop and work out what they want to do so quickly.
Do you think there are any differences between you and your (male) colleagues?
Kathrin Prinz: I think there are differences between large and small companies. In a small company everybody knows everybody else and you quickly gain familiarity with each other. In a large company, you often talk to people that you don’t know. That sometimes causes reservations the first time you actually meet in person. But at the second meeting the whole thing is very different. I think over time we will stop making any distinctions between male and female – and as far as I’m concerned that is proper equality!
Jennifer Enderle: I really can’t remember any preference or disadvantage that I experience because I’m a woman either during my training or at work although, until the start of this year, I was the only woman in our team. At some point I hope that people will actually stop mentioning that women are getting into engineering!
Does the women's quota then tend to go in the wrong direction?
Jennifer Enderle: In theory, it will certainly mean that women take up some higher positions. However, in practice that’s actually not a good thing because it makes people ask the wrong questions: Has she got the job because she’s a woman? Can she actually do the job? As far as I’m concerned, I want to impress people with my strengths and competence, not with my gender.
Kathrin Prinz: I have no problem whatsoever working with men. When I was at school, however, I always thought it was great that I wasn’t the only girl. Everybody expects you to be the best in the class and there is real pressure on you – some of which you create yourself. In my courses I find that the mood in mixed groups is better and the working atmosphere is calmer. To ensure a good mix in the industry, it is essential that parents realise that vocational training and learning a trade are serious alternatives to going to university.
And regardless of gender, what characteristics should somebody have if they want to go into the crane industry?
Kathrin Prinz: Confidence and the ability to stand on their own feet are important and a sense of humour is certainly helpful. And then, of course, you need to be fascinated by the product.
Jennifer Enderle: That’s right. They also need technical understanding, assertiveness and a high tolerance for frustration. That’s because not everything works first time and sometimes you have to do start right from the beginning again. The ability to learn and flexibility are a real benefit in this case!
This article was published in the UpLoad magazine 02 | 2022.