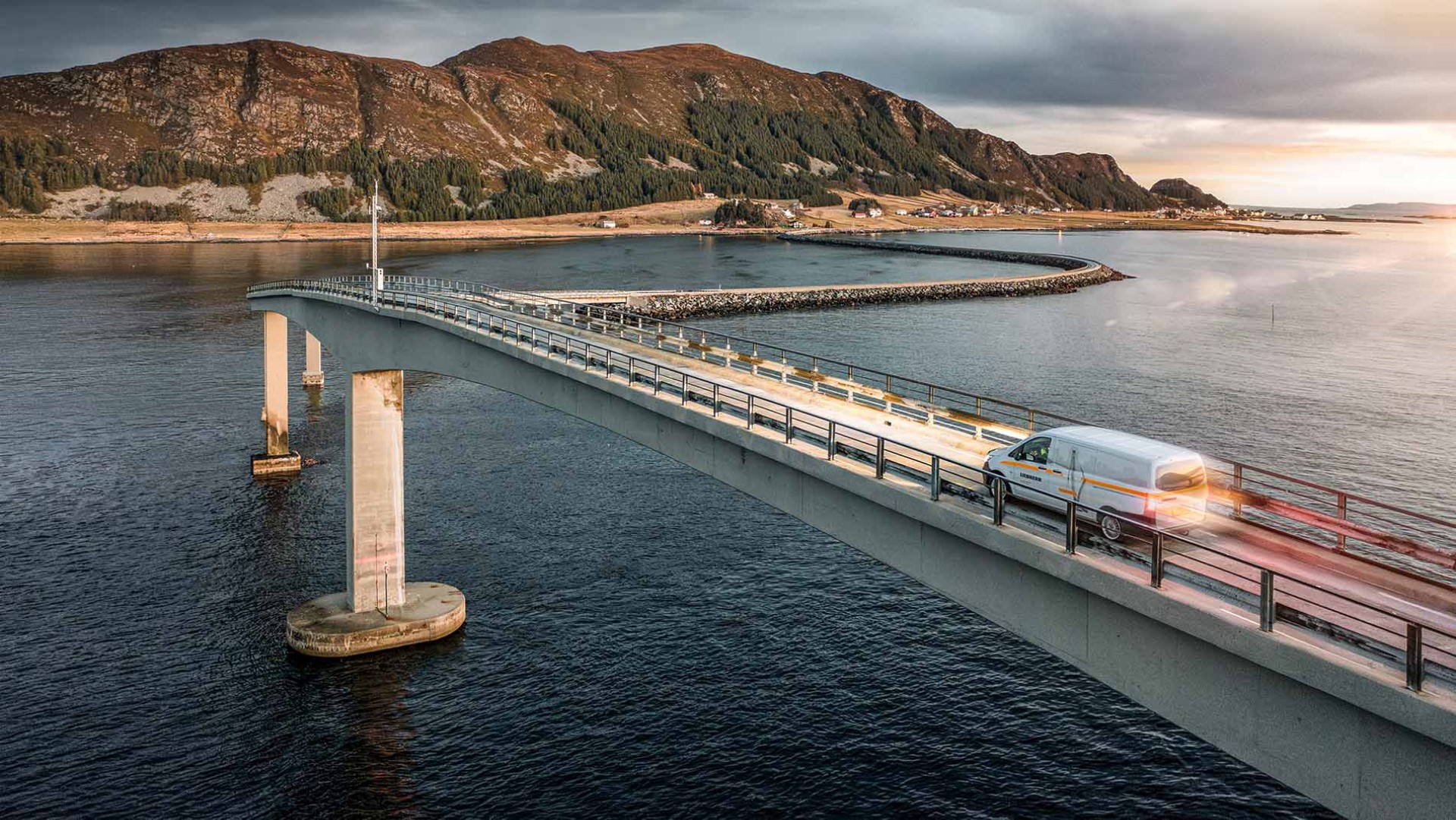
4 minutes - magazine 01 | 2024
Service 24 / 7
Our work is not done when we deliver the cranes to our partners and customers. Maintenance and, if necessary, repairs for all the Liebherr cranes in use around the world are of course also included.
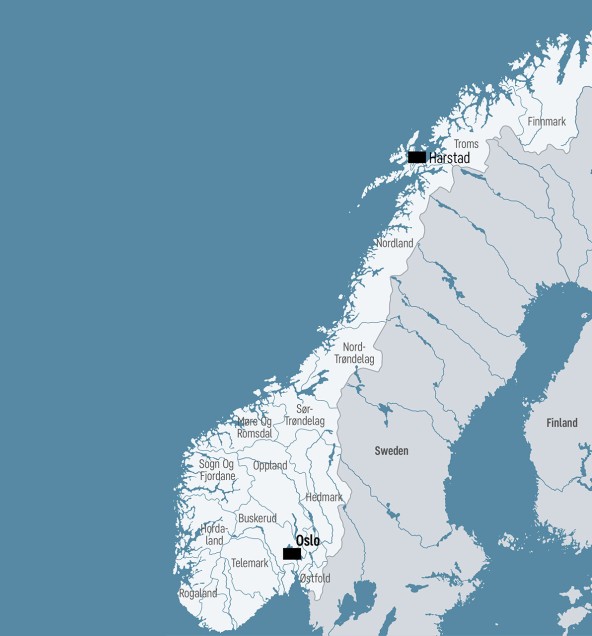
“We are focussing strongly on the green transformation.“
In this issue, we report that we manufactured over 2,000 mobile and crawler cranes at our plant in Ehingen last year. An achievement that we are – admittedly – quite proud of. But our work is not done when we deliver the cranes to our partners and customers. Maintenance and, if necessary, repairs for all the Liebherr cranes in use around the world are of course also included. So far, there are around 44,000 of them, most of which are still in daily service. Globally, over 1,000 men and women are responsible for servicing our products alone. This includes warehouse and workshop personnel, operations managers and, of course, our service technicians. They all ensure that our cranes are running and that downtimes are kept to a minimum. In most countries, we provide mobile crane services through our own branches. In some markets – including Belgium, Sweden and Norway – we work with long-standing sales and service partners who are responsible for both sales and customer service. In Norway, Ing. Hans P. Øen AS carries out these tasks for us. We meet the company’s Managing Director, Thomas Bohlin, for a chat in Fosnavåg, Norway.
Thomas Bohlin, you visited the first Liebherr mobile crane with LICCON3 control delivered in Norway on a construction site here: the LTM 1110-5.2 from our partner Sunnmøre Kranservice AS. How do you personally like the new crane?
Thomas Bohlin: I think the new LICCON3 crane is a fantastic machine. Many improvements have been implemented in it. Convenience and operation are at a completely new level. But I particularly like the new chassis design. Good ergonomics, good lighting.
What special advantages and possibilities does this new crane model offer specifically for your customers in Norway?
An important feature of the new mobile crane is that it can drive on the road with an axle load of less than 8.2 tonnes. In Norway, great importance is attached to the axle load of the vehicles, because we have many narrow and unfortunately also bad roads. The LTM 1110-5.2, like the LTM 1090-4.1, has the potential to become one of the main machines in our market. We have modified the new crane from Sunnmøre Kranservice in our workshop so that the outriggers can be removed if necessary. Even the boom can be removed. This means that it can easily drive on narrow roads and over small bridges here in western Norway.
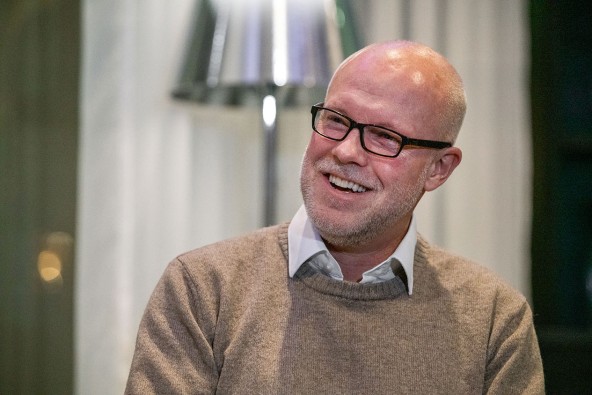
Thomas Bohlin
This vehicle is part of a large-scale field test with ten LTM 1110-5.2 machines.
We were lucky enough to get this LICCON3 crane from the pre-series here. Among other things, it is tested for operation in cold conditions and should be able to work at temperatures as low as minus 40 degrees. The machine is connected to the plant in Ehingen via a modem. This means that any errors can be read out there and solutions found should problems occur.
Mads Indresøvde, Managing Director of Sunnmøre Kranservice AS, was very pleased with the new crane. And about the service that your company offers Liebherr customers here in the Norway. Can you briefly outline your work?
Ing Hans P. Øen AS has been looking after the needs of Ehingen Liebherr customers in Norway for 45 years. Engineer Hans P. Øen founded the company in 1979. I’ve been running the business since the turn of the millennium. Products from the Liebherr plants in Biberach and Nenzing have since been added. However, the plant in Ehingen is by far our main supplier. Around 90 percent of the machines we sell in Norway come from there. But we also have MK mobile construction cranes from Biberach and hydraulic cable excavators as well as LR crawler cranes from our colleagues in Nenzing in our portfolio.
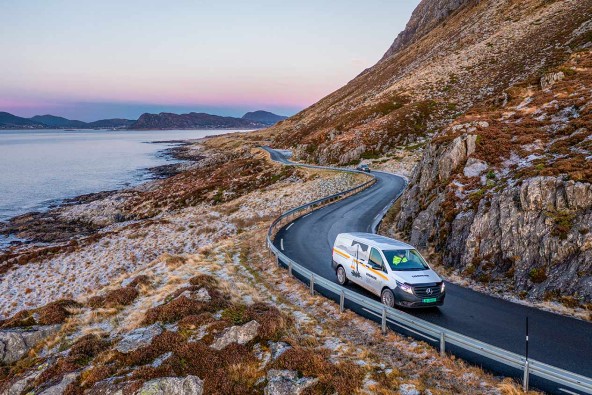
As mentioned earlier, you’re not only Liebherr’s sales partner in Norway, but are also responsible for service in Norway.
Yes, that’s true. At Ing. Hans P. Øen AS, 14 employees take care of our customers’ concerns. Six service technicians are available on site or at the customer’s premises in the event of technical problems with the machines. A 24-hour service, 365 days a year. When we receive a call from a customer, we often have a long distance to travel. Norway is a very long country – around 2,500 kilometres from north to south. Our branch is located in Honeføss, about 40 kilometres from Oslo. We have stationed a fully equipped service vehicle in Harstad so that we can be ready for action as quickly as possible in the north of the country if necessary. We fly there and then drive to our customers in northern Norway.
A major issue in your country is the transformation towards renewable energies. Your country is driving this change forward with great vigour.
Indeed. We are focussing very strongly on the green transformation here. The city of Oslo, for example, has decided to only allow access to emission-free vehicles in large parts of the city centre from 2025. Property developers, the city of Oslo and government clients are increasingly demanding low-noise and low-emission machines. Our customers have recognised this and seeking the right machine. We delivered our first LTC 1050-3.1E to Skoveng in Lillestrøm near Oslo in the autumn. This is a crane that can be operated entirely with electricity on the construction site.
What is the response to this LTC 1050-3.1E compact crane? Have you already received feedback from the customer?
Yes, it is consistently positive. As expected, the machine works almost silently and without emissions. We will be seeing this crane model more often on construction sites in the capital in the future. We have already sold a total of ten of these cranes in Norway. All to customers operating in the Oslo area.
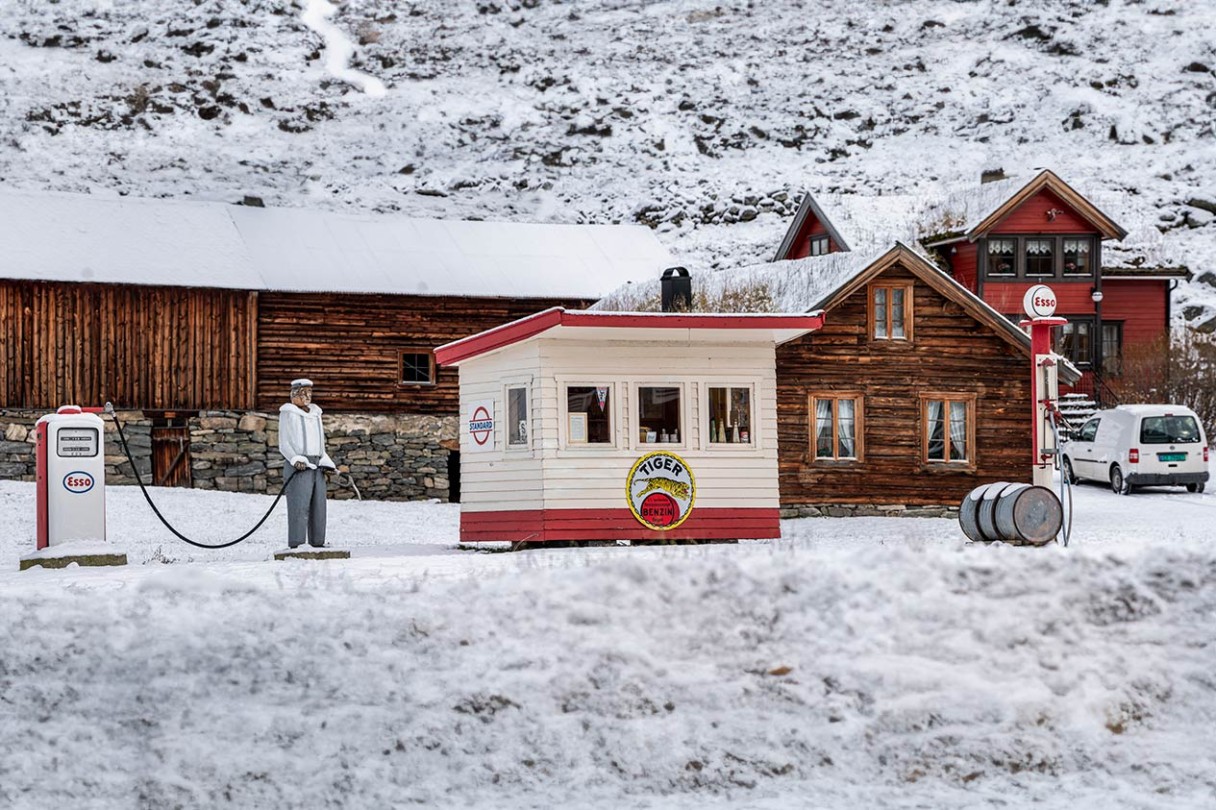
Soon to be a relic from bygone days? Decorative imitation petrol station on Europastrasse E16. Norway is taking a bold approach to restructuring its energy policy.
This article was published in the UpLoad magazine 01 | 2024.