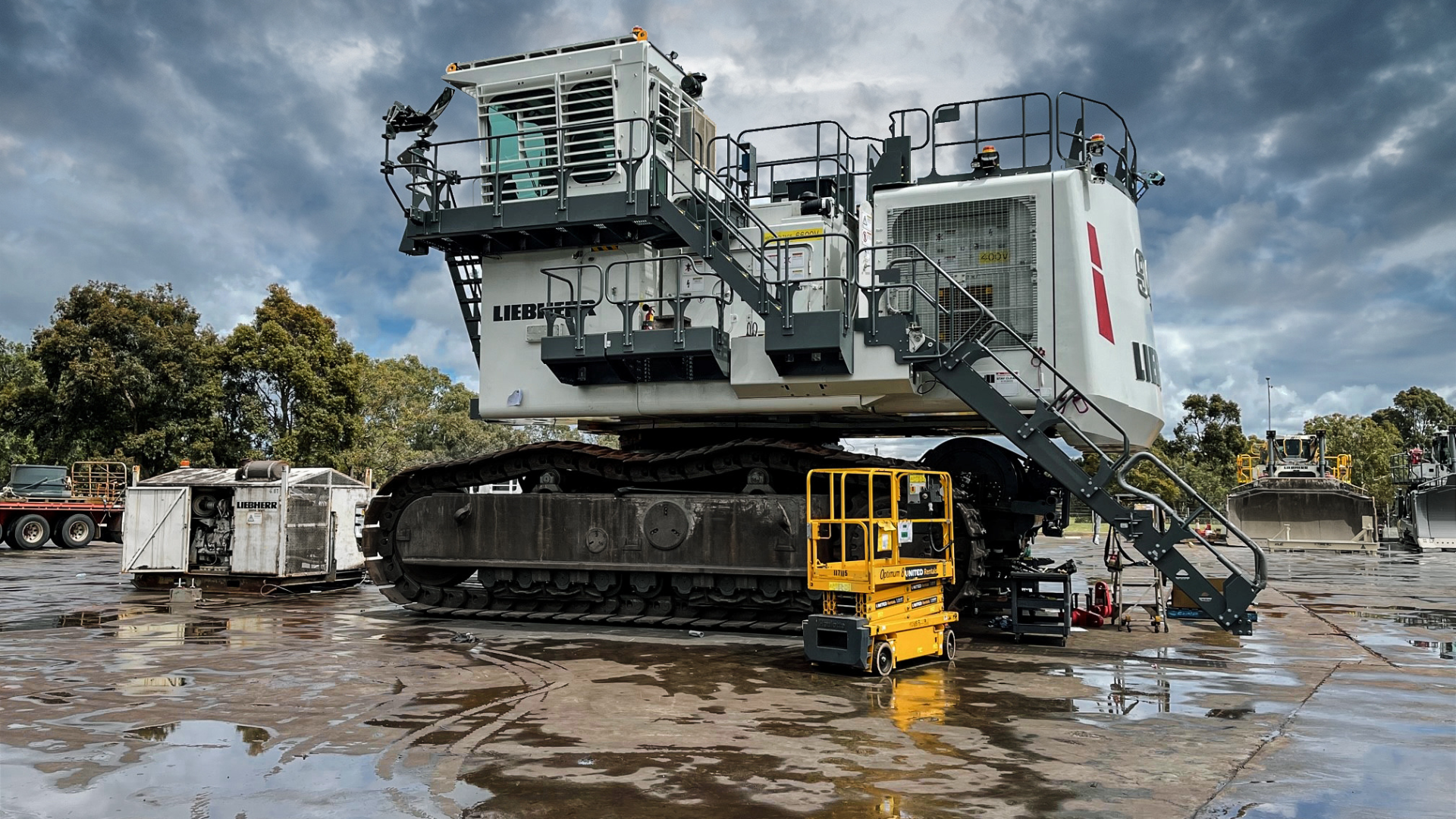
Charging towards the future: the first R 9400 repower
In 2023, Liebherr Mining achieved its first repower of a diesel-drive machine to electric drive. The R 9400 – now an R 9400 E – is the first Liebherr electric excavator to operate in Australia. Offering the option of repowering diesel equipment highlights Liebherr’s commitment to decarbonising its products.
Repowering a mining machine involves altering its existing energy source. Customers may simply wish to update an existing diesel internal combustion engine to another, more fuel-efficient engine and/or fuel source. Alternatively, customers may be looking to adapt their machines so they can run on zero emission energy sources like electricity.
Converting diesel-drive machines – such as the R 9400 – to electric power can help mining operators to accelerate the transition of their fleets to zero emission technologies without needing to discard the mainframe of these machines. Repowering to an electric excavator can also offer the additional benefits of faster loading cycle times and improved hydraulic pump component life, thanks to the constant shaft speed of the electric motor.
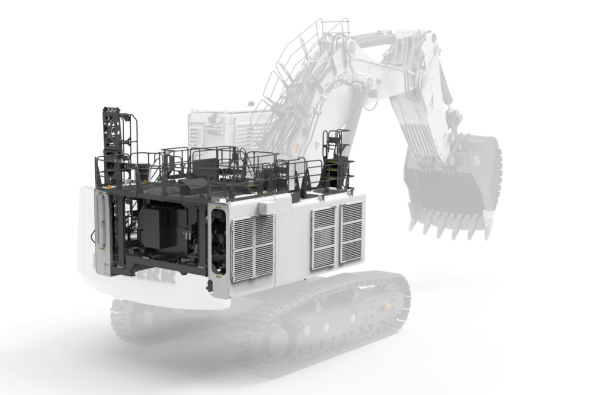
The road to repower
Because Liebherr takes a modular approach to building its larger mining equipment, repowering a diesel-drive excavator like the R 9400 can be completed in a matter of weeks.
“Approximately 60% of an electric-powered Liebherr mining excavator is the same as a diesel-driven machine, which helps to simplify the repowering process” explains Chris Di-Nardo, Project Manager, New Machine Deliveries, Liebherr-Australia Pty. Ltd. “Once this R 9400 had been removed from its operations in Western Australia, the base machine was returned to our branch in Perth, where the conversion could begin.”
Among the changes necessary for the R 9400 to become an R 9400 E, the diesel powerpack and fuel tank needed to be removed and replaced with their electric counterparts – in this case, an electric-drive powerpack and a high voltage electric cabinet respectively. Components needed in the diesel-drive R 9400 - like the water-cooling radiators, fans, exhaust, and air intake systems - were made redundant with the introduction of the electric-drive powerpack. However, the rotary connection was a unique case: in order to accommodate the high voltage interface between the upper- and undercarriage of the R 9400 E, an entirely new rotary connection needed to be installed.
In order to simplify major machine maintenance for customers, Liebherr recommends that repowers occur when a machine is due for a major service or component exchange. So while the R 9400 was being transitioned from diesel to electric power, major components that had achieved service life were also exchanged. Performing major maintenance in this way also has the benefit of making the process more cost-effective for customers.
Once the new electric-drive modules were installed, connections completed, and systems checked, the repowered R 9400 E was then 'powered up' to energise the excavator’s operational systems. The R 9400 E requires 6,600 volts at 50 hertz for its power up process and then the electric motor and hydraulics can be 'started and run up'. To minimise the inrush current needed to start the electric motor, Liebherr developed a specialised system that consists of high voltage transformers. This system of transformers reduces the current required from the customer’s power grid to avoid excessive network disturbance.
Repowering the R 9400 was an exciting challenge for our team, but one that they quickly overcame.
Shared expertise ensures success
Although the repower process is not overly complicated, specific expertise from Liebherr’s excavator factory in Colmar, France, was required to support the Liebherr team in Australia with its first diesel to electric repower project.
“Repowering the R 9400 was an exciting challenge for our team, but one that they quickly overcame,” says Di-Nardo. “Most of the people working on this project had only worked with diesel powered machines previously. However, thanks to the combined efforts of more experienced team members here in Australia and the engineering assistance from our excavator factory, the team was able to complete the project tasks safely and on time.”
Repower projects such as this are not limited to mine sites that can easily transport their mining equipment to a local Liebherr workshop. Liebherr can also travel to remote mine locations and complete these repowers on site, meaning a wider range of customers can take advantage of this service. And now, after the successful completion of its first repower of a diesel excavator to electric drive, Liebherr Mining has demonstrated the efficacy of this solution for any customers that wish to explore repowering as a way to meet their zero emissions targets.