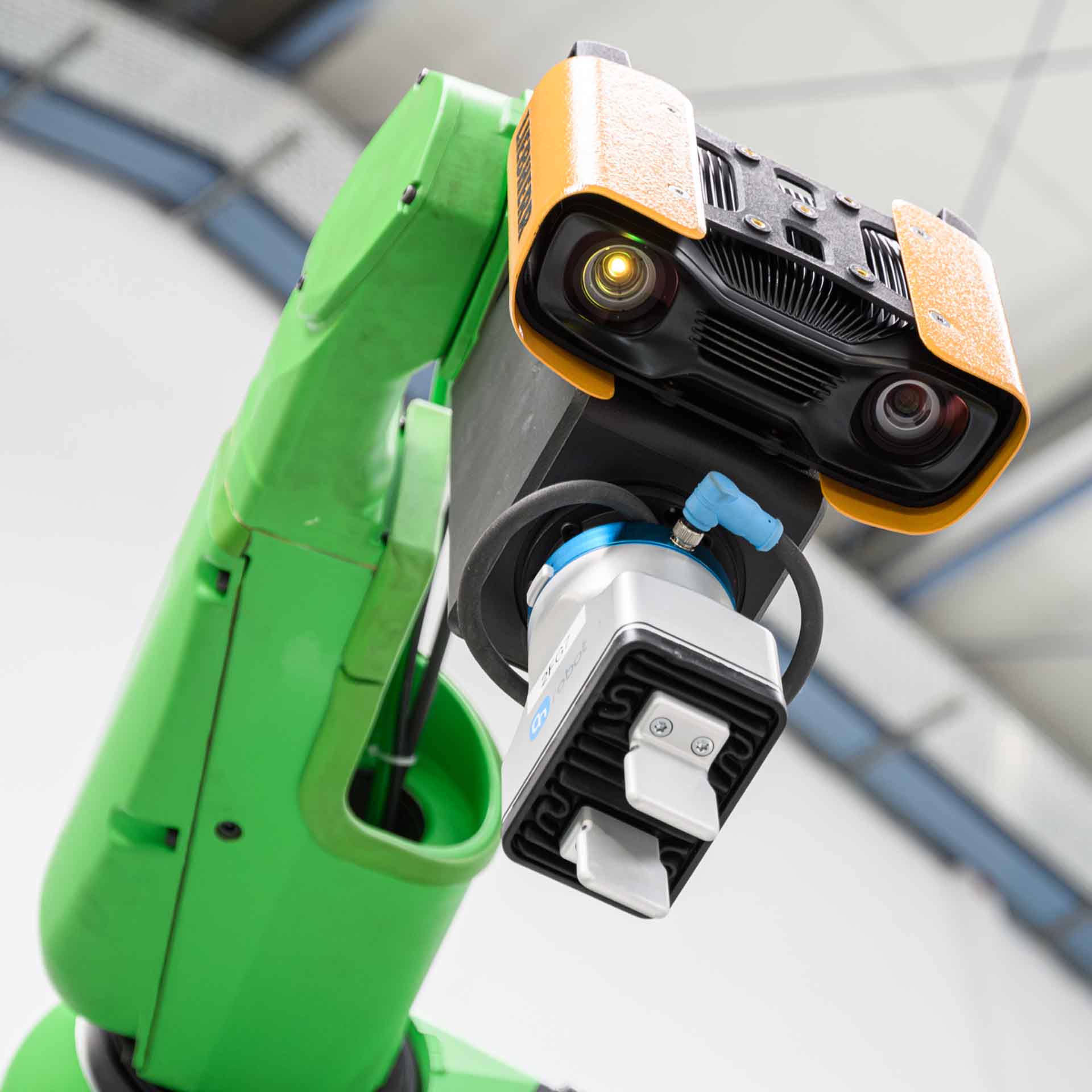
AI supported image processing in bin picking
Liebherr-Verzahntechnik GmbH is taking the plunge into artificial intelligence (AI) with its latest version of LHRobotics.Vision bin picking software. Filtering out irrelevant image data enables faster and more accurate detection of unsorted workpieces when removing them from containers.
The LHRobotics.Vision intelligent software is integral to the technology package for bin picking – the robot supported removal of unsorted parts from a container. It is available in two functional forms: The basic license includes collision-free gripping and picking function for workpieces and the pro license offers this plus placement planning. A simulation tool allows procedures to be virtually tested and optimized – with everything on a clearly arranged and intuitive interface. Thanks to its open sensor interface, the software is also compatible with vision systems from different manufacturers.
Component detection – the challenge
LHRobotics.Vision includes an AI supported optimization function for search parameters for which trade publication inVision commended it in 2023 as one of the top innovations for industrial image processing systems. However, detecting a component’s position remained a challenge: For example, uneven crate bases could obscure the difference between the base and the component, especially in the case of flat parts like plates.
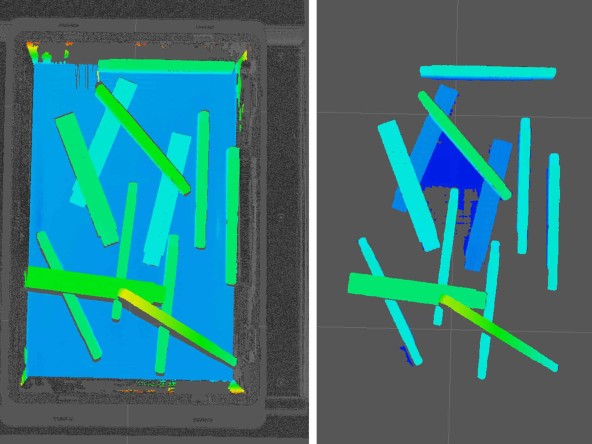
Image data of the point cloud before and after AI-supported segmentation
AI for greater precision
Workpiece detection has now been further enhanced: The point cloud registered by the camera, that is the image dataset which defines the form and position of the workpieces, is divided into segments by AI. This classifies the data by its relevance. Irrelevant information such as data about the base or walls of the container is eliminated prior to processing. This means that the software only looks for the workpieces in the defined areas, considerably accelerating processing.
Optimized data structure
“A lot of data requires a lot of computing power and results in a higher error rate,” explains Sebastian Wendt, Product Manager for Automation Systems at Liebherr-Verzahntechnik GmbH. “The reduced data volume ensures faster processing and considerably reduces the error rate – even when removing plates. At the same time, the optimized data structure enables the containers to be emptied at a higher rate.” The feature has been developed over the last year and has been tested intensively. It is compatible with all versions of LHRobotics.Vision as well as all equivalent vision systems, and is available as of now as an optional additional function.