Press releases | 02/18/2025
Innovations in Liebherr wheel loaders: autonomous operation and hydrogen drive
- World premiere in digitalisation: “Liebherr Autonomous Operations” allows driverless wheel loader operation
- Autonomous system particularly suitable for repetitive, monotonous and hazardous wheel loader tasks
- Trade show premiere for alternative drive technologies: L 566 H large wheel loader is the first operational prototype with hydrogen drive
- Liebherr hydrogen engine makes it possible to emit no greenhouse gases and almost no nitrogen oxides in future
- Nominated for the Innovation Award in the category “Digitalization”
At Bauma 2025, Liebherr-Werk Bischofshofen GmbH will be showcasing two innovations which represent the latest advancements in digitalisation and drive technologies – the “Liebherr Autonomous Operations” system and the first large wheel loader with a hydrogen engine. The autonomous solution, which is at an advanced stage of development, allows completely driverless operation and is particularly suitable for monotonous routine tasks and operations in hazard zones. In addition, Liebherr's autonomous system is currently one of few products still under consideration for the Innovation Award at bauma, the leading trade fair in the construction industry. Alongside this groundbreaking debut, Liebherr will also be presenting pioneering advancements in drive technologies: the L 566 H is the first prototype of a large wheel loader with a hydrogen engine, thus expanding the range of alternative drive systems. After Bauma 2025, Liebherr will begin a two-year trial of this machine at STRABAG, one of Europe’s leading construction technology groups.
“Liebherr Autonomous Operations” redefines efficiency and safety in the use of wheel loaders and will allow fully autonomous operation in future. The autonomous system allows repetitive and monotonous wheel loader tasks to be carried out easily and intuitively without an operator. Visitors to Bauma can watch live demonstrations of the autonomous wheel loader prototype several times a day. The technology will undergo further field tests before the machine is available to the market.
In the field of alternative drives, Liebherr-Werk Bischofshofen GmbH will also be introducing the L 566 H, the first large wheel loader with a hydrogen engine. After many years of research, this innovative drive technology has proven to be ideally suited to heavy vehicles. Visitors can see the hydrogen-powered large wheel loader at the Liebherr stand. Models from other series, ranging from the smallest, the L 504 Compact, to the largest, the L 586 XPower®, complete the line-up of Liebherr wheel loaders at this year’s Bauma. They include the L 507 E, the group’s battery-electric wheel loader.
Autonomy revolutionises wheel loader operation
“Liebherr Autonomous Operations” is particularly suitable for repetitive wheel loader tasks and can perform monotonous jobs such as repeatedly loading hoppers or transporting materials from A to B without an operator. This helps counteract the difficulty of finding staff for monotonous routine tasks. As a result, employees can devote themselves to more varied tasks, meaning that working time can be organised more effectively. “At the same time, it can create space for employees to focus on more complex activities that require human expertise,” says Dr Manuel Bös, Head of Emerging Technologies at Liebherr-Werk Bischofshofen GmbH. In addition, challenging tasks such as working in the hazardous area of a quarry can be performed by the autonomous system without endangering employees.
Simple operation and robust technology
Operators can plan deployments of the autonomous wheel loader using the “Autonomous Job Planner” web application developed by Liebherr. “You don’t need any special IT skills to initiate the wheel loader deployment. The system is very intuitive and user-friendly, and requires only a few inputs for the job,” explains Bös. The machine perceives its surroundings, piles and obstacles using 3D environmental sensors – without having to use drones or separate surveying technology – and plans the work cycle accordingly.
The autonomous system then carries out the task independently, automatically adapts to the changing environment and does not require GPS reception, which means it can be used indoors, underground, at high quarry faces or under tree cover. “In these operations, conventional GPS-based systems reach their limits, while Liebherr Autonomous Operations can be used anywhere – from a confined industrial hall to an open quarry,” says Bös. In addition, the self-driving wheel loader can operate independently around the clock, enabling continuous material handling at any time.
Efficiency and predictability
The autonomous system delivers machine operation with consistent performance and efficiency right from the start and throughout the entire duration of use, regardless of the time of day. “Due to the consistent performance of the autonomous wheel loader, all processes are easier to plan and can be made more efficient,” says Bös. “The software-controlled autonomous wheel loader operates in a particularly machine-friendly way, significantly reducing component and tyre wear as well as fuel consumption. This reduces ongoing operating costs. Additionally, the operator can seamlessly switch between conventional manual cab operation and fully autonomous operation, thus maximising machine utilisation,” adds Bös.
Prototype L 566 H: the first large wheel loader with a hydrogen engine
Liebherr is open to all kinds of technology, and extensive studies have shown that hydrogen propulsion is an optimal solution for operating large wheel loaders without CO2 emissions. This is why Liebherr has developed the L 566 H, the world’s first large wheel loader with a hydrogen engine. It is based on the proven L 566 XPower and thus also features the power-split XPower travel drive. For smaller vehicles up to about 15 tonnes, battery-electric solutions are often suitable. However, for larger machines with an operating weight of up to 40 tonnes and high energy demands, Liebherr uses the hydrogen engine as a powerful and efficient drive system.
Liebherr develops hydrogen engines like that of L 566 H at its components division’s own engine plant in Bulle, Switzerland. These engines will not only make it possible to emit zero greenhouse gases and almost no nitrogen oxides, but will also offer excellent efficiency. Another advantage comes from the thermal and mechanical interfaces, which are comparable to those of a diesel engine. This represents a significant step forward in the sustainable development of large machines with alternative drives.
Trial as pilot project for reducing emissions
Liebherr is providing STRABAG with the L 566 H prototype as a test machine for daily use over a period of two years. At the Gratkorn quarry in Austria, the large hydrogen powered wheel loader is expected to save up to 100 tonnes of CO₂ annually, equivalent to about 37,500 litres of diesel. This collaborative pilot project between Liebherr and STRABAG shows how alternative fuels can be used to reduce emissions in a sector where decarbonisation is difficult. Green hydrogen, produced using wind, water or solar energy, can be a key step on the way to becoming carbon neutral. What makes the two-year test deployment at the Gratkorn quarry such a showcase project is, above all, the joint approach of Liebherr and STRABAG: two companies that are actively pushing decarbonisation forward.
Contacts
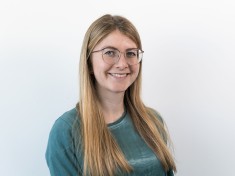
Liebherr-Werk Bischofshofen GmbH
5500 Bischofshofen
Austria