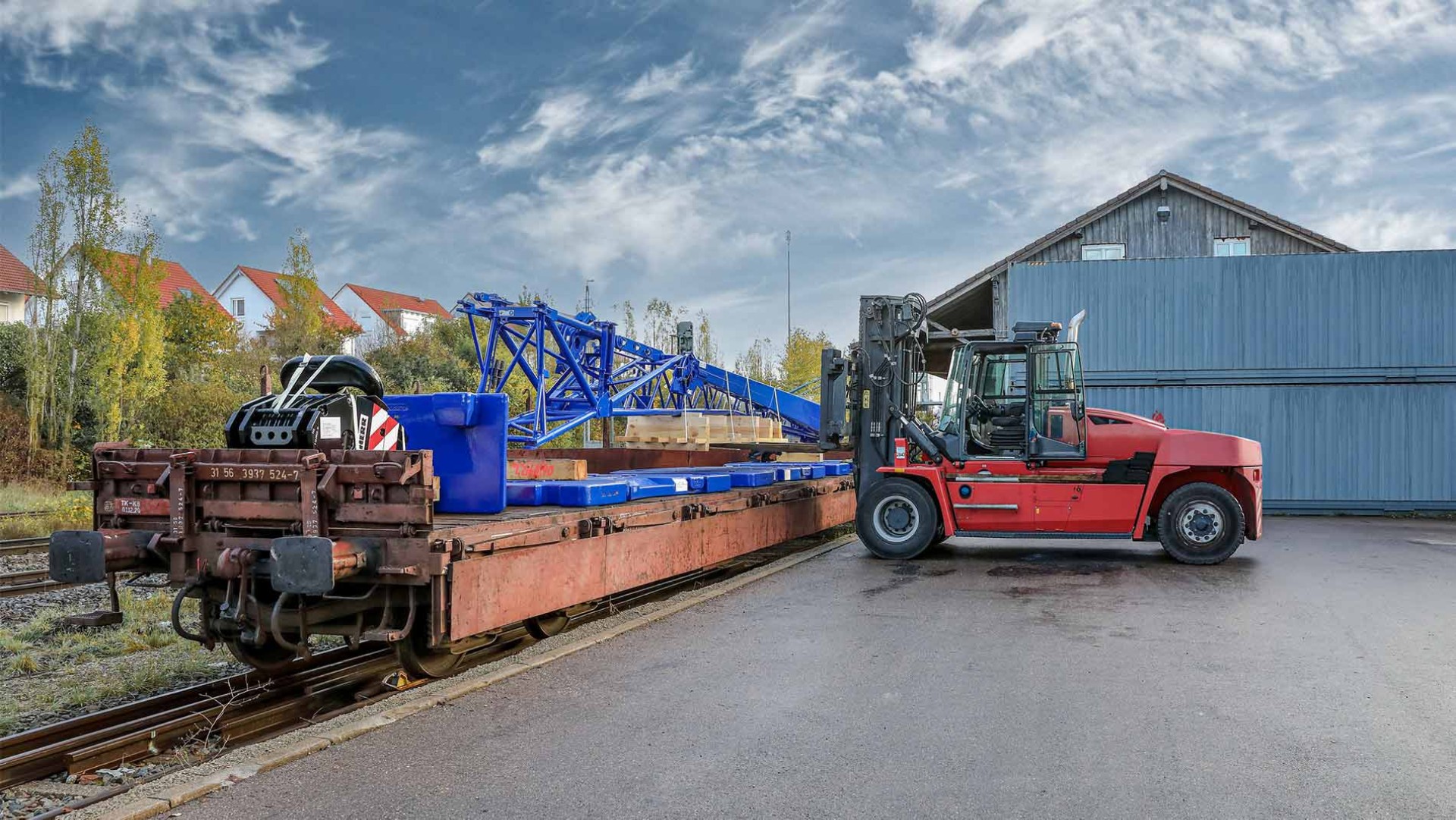
8 minutes - magazine 01 | 2023
Chuff, chuff, chuff, the railway…
Road, rail and sea – our cranes make their way from Ehingen to Erdenet, for example, by a whole range of different routes.
How railways are reducing emissions.
It may sound a bit run of the mill, but in reality not only is it 8,400 km away, a journey that takes six weeks, but also requires intricate planning, short term adjustments and a good deal of sensitivity about geopolitical and climate issues. For all these reasons, shipping cranes by rail has been a reliable, sustainable and climate-friendly option for us for decades. And because of this, in this edition – after the voyage by ship in the last UpLoad, we decided to take you on a rail journey. All aboard!
The whole thing starts several times a week at around 4 pm at Ehingen Station. Its location is only around 2,500 metres from our plant, and after Deutsche Bahn’s loading manager has done his work, checking that the load in the wagons does not exceed the maximum of 56 tonnes, our goods set off on their journey to Kiel, Lübeck, Rostock, Hamburg, Bremerhaven and Antwerp. All the equipment for a mobile crane occupies between one and three wagons and it travels in first class all the way. The basic machine is actually driven to the ports because the loading dimensions for railway wagons in Western Europe are simply not big enough to accommodate it.
Cranes to the CIS countries are shipped through the port of Kiel to Klaipeda in Lithuania where they are loaded onto wide-gauge wagons. It takes experienced engineers around a week to remove the counterweight plates, folding jib, small parts and sometimes even the wheels. They also provide support to the loading personnel for lashing the components safely and properly using strong steel cables. Once again, everything has to be checked by the loading manager before it can get underway.
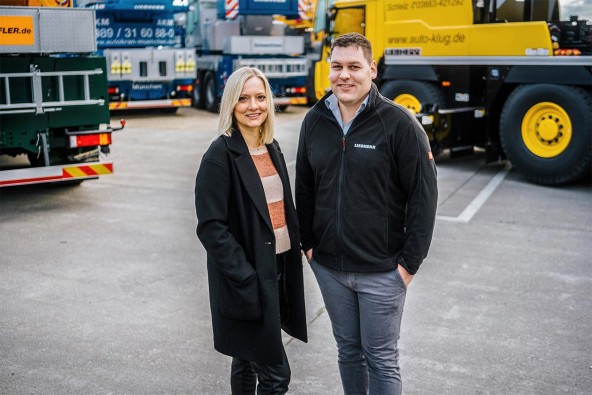
Melanie Spomer and Jens Bachmann provide insight into the shipment of cranes by rail.
“During rail transport, there are some enormous forces and vibrations”, explains Jens Bachmann. He is the Crane Shipment Team Manager at Liebherr and is responsible for transporting telescopic cranes, mainly to countries outside the EU. “We have been sending many of our cranes by rail to our customers for decades. Initially, it was done to save costs as a railway wagon can hold as much as two and a half trucks. Today, however, this method is also an ecological one, which is why it is being used more and more. A railway wagon causes around 60 percent less CO₂ emissions than a lorry and that includes transporting components to the railway station.” The loading area is another positive for Jens Bachmann as he can load 18.6 metres (rather than 13.6) on a railway wagon from Ehingen.
“Although the journey takes a little longer, the procedure is simpler!” adds his colleague Melanie Spomer, who is a Crane Shipment Executive, who deals with the CIS states, Saudi Arabia, the UAE, Oman and Qatar among others. She is also acutely aware of the challenges posed by global heavy haulage. “When they are being shunted, the wagons really crash to each other, even though the German wagons have springs that buffer most of the forces. Nevertheless, we always pack everything really well for the long journey from Klaipeda. Small parts such as windscreen wipers and headlights are placed in wooden crates, which also protects them from theft. We secure painted, non-packed components on pallets. Our control system, the most sensitive part of a crane, is pretty much insensitive to being shaken around for days because it has very good protection from vibration.”
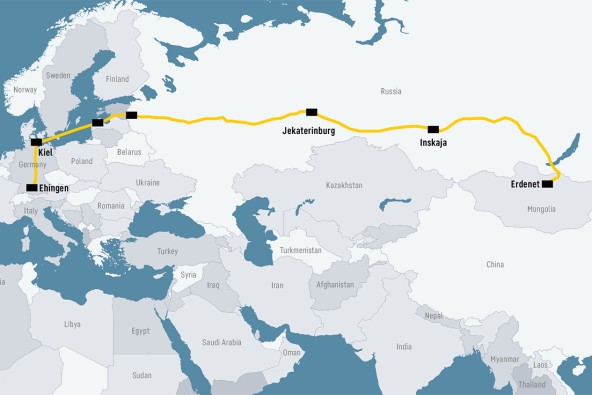
“For days” is really not an exaggeration. One of Melanie Spomer’s customers is the Erdenet Mining Corporation, which is based in Erdenet, which we mentioned at the start. Although the name begins with an E, it is a long way from Central Europe like Ehingen, as it is actually in the least densely populated country in the world – Mongolia. It is 400 km from there to Lake Baikal, 1,400 km to Beijing and over 8,400 km to Ehingen, if you consider distances in crane routes. “The whole route takes around six weeks and can be described pretty quickly”, says Melanie Spomer. “The basic machine is driven to the port in Kiel where it meets up with the equipment which is shipped to the port station by rail. Both then travel on a ferry to Klaipeda in Lithuania, where they are met by our engineers. They then load the goods onto the wide-gauge wagons and send them to Erdenet, which is 6,618 km from Klaipeda. It takes 23 days before the engineers there receive the crane.”
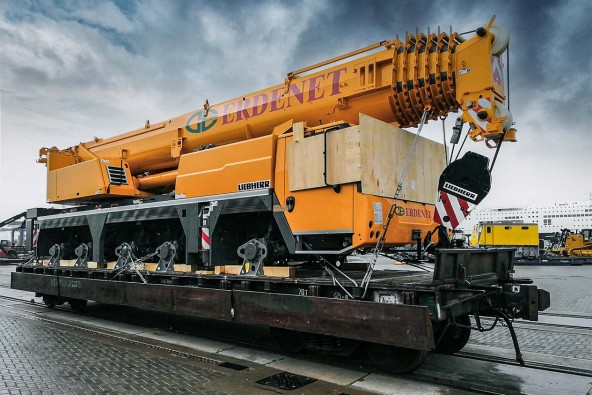
This LTM 1110-5.1 is on the 6,600 kilometre journey to Mongolia on a wide gauge wagon.
Hopefully undamaged. “The biggest challenge is actually handing the crane over to the customer undamaged after over 8,000 km, lots of access by various parties and the complicated dismantling and assembly procedure. But planning the route through war and crisis zones also takes a bit of time!” Currently the company is also having to deal with sanctions and transit regulations. “There are always new rules that we have to observe. We have had to study the facility to transport equipment through Russia just as much as asking whether we should transport it by ship to Mongolia via China”, adds Jens Bachmann. This was one of the alternatives that was dismissed, along with diverting around Russia via Georgia and Kazakhstan. “We therefore continuously adapt ourselves and our routes to suit new situations and circumstances and we always have to be open to alternatives.” Ultimately there is often a choice between a route subject to current uncertainty and a diversion, which increases the risk of damage due to the fact that everything has to be unloaded and reloaded multiple times.
However, all these imponderables have not resulted in the company looking anywhere other than at the rail option – from Ehingen Station to the ports, a trip covered by around 200 wagons from the plant every year. Almost exactly the same number arrive at the freight track separated from the passenger traffic every year for the mobile and crawler crane manufacturer – normally filled with heavy material such as sheet steel from Austria, Sweden and Saxony-Anhalt.
And even though the wagons may crash noisily into each other occasionally whilst they are being shunted – Liebherr’s rail transport policy reduces the number of trucks that the residents have to put up with by around 700 per year – together with all those emissions. And that actually equates to around 300 tonnes of CO₂ equivalent per year, the same level of emissions generated by around 200 commuters per year for their daily drive to a workplace 20 kilometres from home.
This article was published in the UpLoad magazine 01 | 2023.