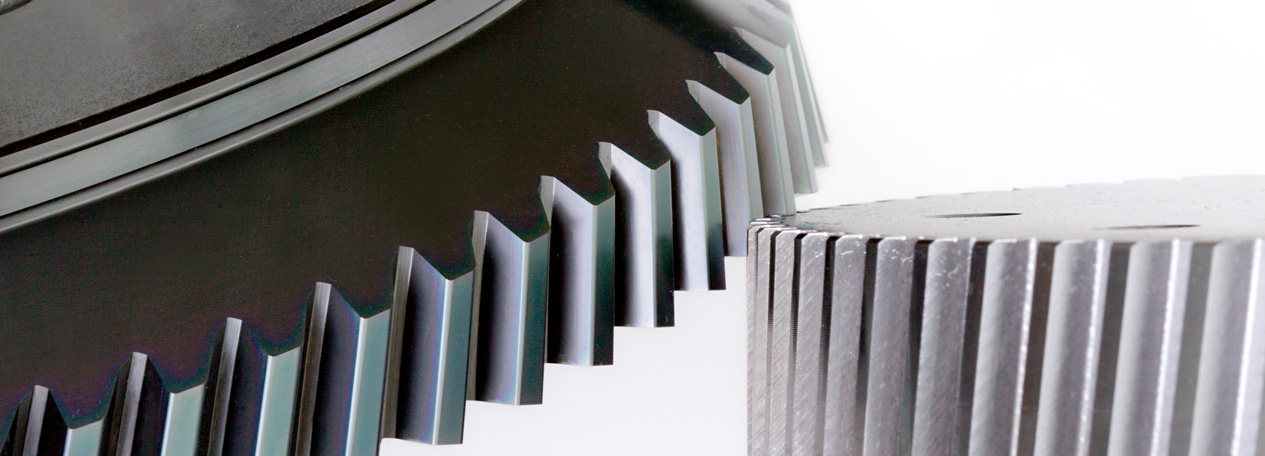
Gear skiving tools: a question of trust
Gear skiving is considerably more productive than gear shaping and more flexible than broaching, but it also has its pitfalls. Minimal errors in tool design can be decisive for the success or failure of the manufacturing process. Comprehensive competence is required here, so that the user can be confident that his processes will work and that highest-quality components will be produced.
The success of gear skiving lies in the significantly higher efficiency and productivity of this process compared with shaping and the considerably higher flexibility and lower investment compared with broaching. However the requirements for the tools are extremely high. Excellent quality is a must, since minimal details in tool design can be decisive as to whether machining will work successfully.
We have a holistic view of the process and know exactly which adjustments we have to perform in order to make it work.
Trusting the tool manufacturer is key
Practical experience has shown that the mathematical mastery of the process and its coordination with the tool and machine is the key to success. It’s a good thing, then, if you can trust the expertise of your tool supplier. Liebherr knows the entire process of gear skiving intimately. With the Skiving3 technology package, the gear specialist is combining its expertise with regard to the tool design, machines and technology of gear skiving.
“We have a holistic view of the process and know exactly which adjustments we have to perform in order to make it work”, says Haider Arroum, Sales Team Leader for Gear Cutting Tools at Liebherr.
Simulation software for optimal tool design
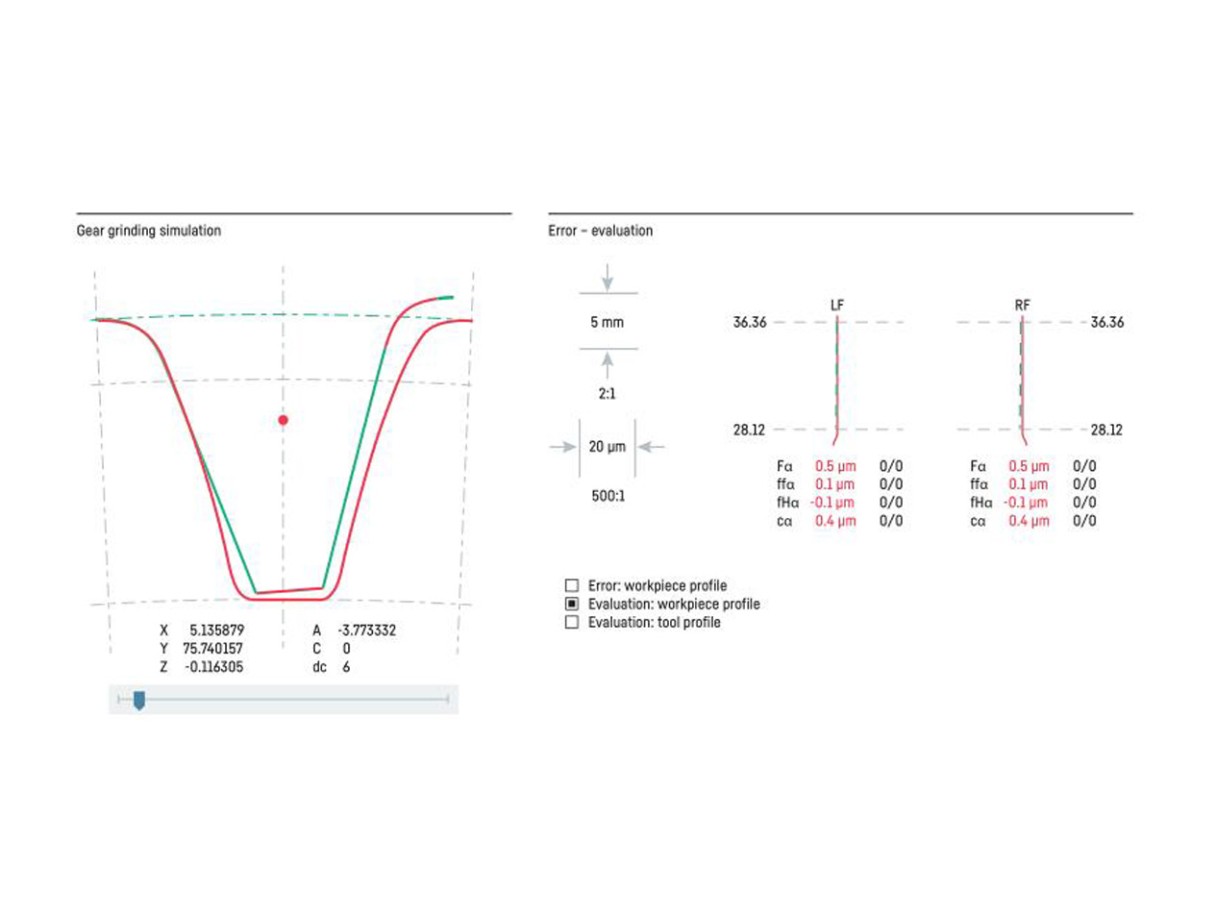
Liebherr’s gear skiving tools are available in conical and cylindrical form and can be optionally manufactured from powder-metallurgical high speed steel (PM-HSS) or full carbide. For process-optimized tool design, Liebherr uses specially developed software, which simulates the manufacturing process, calculates the required tool profile and then controls the gear grinding machine in order to generate the desired profile characteristics on the gear skiving tools. The software detects the profile, taking into account the crossed-axis angle and rake face offset, collision avoidance and the optimum rake and clearance angle for the entire process. This enables optimum quality and process reliability to be achieved for all gears.
“First time right” instead of “Trial and error”
Whether it is for large-volume production or smaller batch sizes, this means more safety and reliability for the user’s manufacturing process from the very first minute – at competitive prices. Perfect coordination between simulation and production technology ensures short delivery times. “Liebherr continually invests in the optimization of quality, tool life and process reliability. Our customers value us as a reliable partner that can also implement individual special features”, Arroum emphasizes.