“The highest degree of accuracy is required when machining high precision blades for turbines”, explains Marc Weiß, Senior Manager Flexible Production Systems at MTU Aero Engines in Munich. The company is among the leading group of manufacturers of civil and military aerospace propulsion systems of all performance classes as well as stationary industrial gas turbines. Turbine blades are cast parts, usually made of nickel-based alloys that are difficult to cut. Highly complex geometries need to be machined with extremely high precision. During operation, the blades have to endure the most extreme conditions – tremendous centrifugal forces, temperatures close to melting point and heavy vibrations. A break could lead to destruction of the power plant. For this reason, extremely strict quality requirements apply for all steps of the manufacturing process. For the development of a new, highly automated production system, therefore, only partners that were able to guarantee the highest level of quality and reliability were considered.
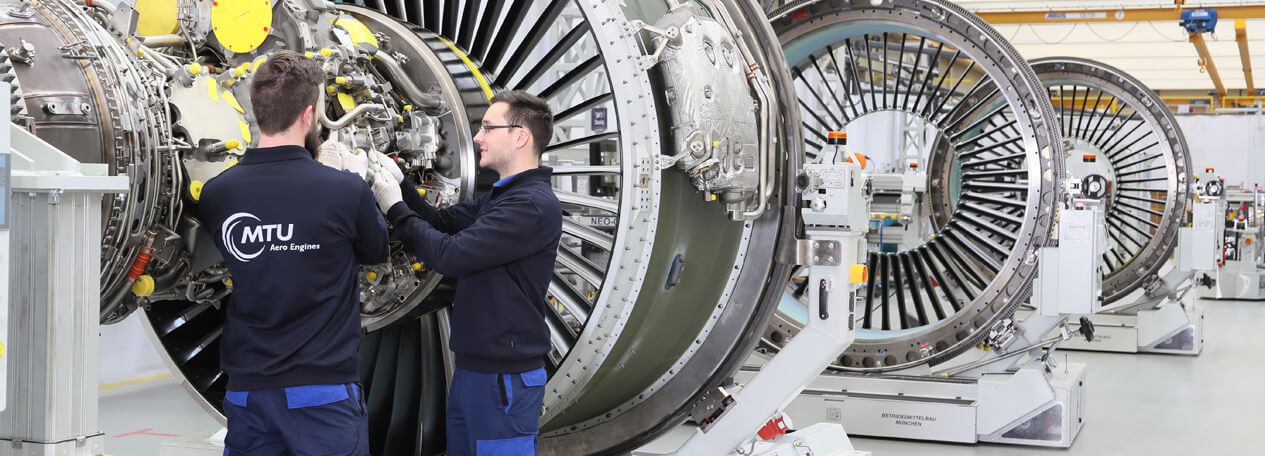
Breakthrough in automated machining of turbine blades
The aircraft propulsion systems of today are wonders of technology. Above all else, the blades in the hot gas area have to withstand loads that, until fairly recently, seemed uncontrollable. Since air travel is rapidly growing in demand around the world, the production technology employed until now needs to be modernised. The Munich-based company MTU Aero Engines turned to a team of innovative suppliers including Liebherr, BLOHM, AMT and SOFLEX to achieve this.
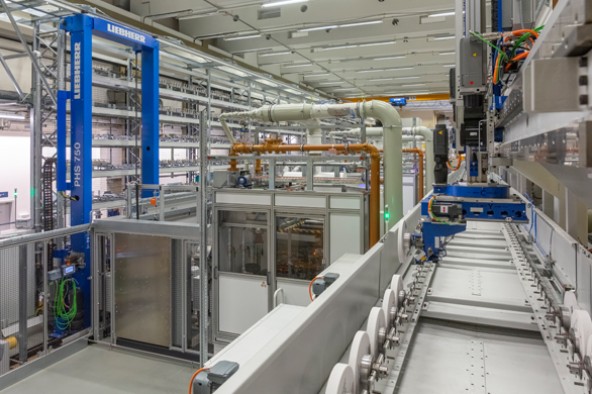
A quantum leap in automation
“The requirements of MTU were vast and necessitated more than a ten-fold increase in staff productivity”, remembers Michael Appel, Regional Sales Manager for Automation Systems at Liebherr-Verzahntechnik GmbH in Kempten. Productivity had to be massively increased in order to meet the enormous increases in demand. In the past, one employee was needed to manually operate one to two machines in a production chain of individual stations. In contrast, the new solution relies on just one employee to achieve a very high processing depth at four parallel-operating, fully-automatic grinding machining cells. Each cell consists of a PROKOS XT 6-axis grinding machining centre from BLOHM, which is supplied by a robot from AMT. The robot receives workpieces, clamping fixture, dressing tools and gripper tongs from a fully-automatic Liebherr pallet handling system (PHS). Thanks to its 250 pallet slots, it is able to supply the machining centres for at least 66 hours unmanned to allow the systems to work through a complete weekend also with flexitime operation. A loading portal (LP) - also from Liebherr - runs on the other side of the manufacturing cells via which the machines can be supplied with tools and grinding discs. The “brains” of the outfit is a control system from SOFLEX, which networks all of the plant units together and enables self-organised production to the furthest degree. This new flexible production system (FFS) can machine a mixture of about 15 different component types in any number required. Moreover, the workplace for the machine operators has also been laid out in a disabled-friendly manner.
The system that we have created together is very complicated and way more advanced than the technology employed to date
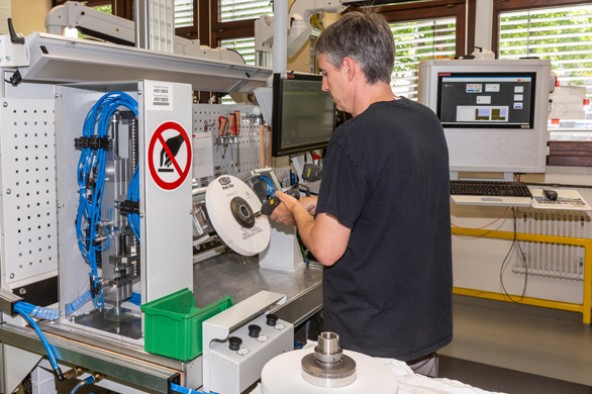
Close partnership with engineering
“The actual challenge for Liebherr was to select our modular automation components in such a way and to link them with the other systems that a smooth interaction was facilitated”, adds Michael Appel. Liebherr also took on the responsibility for CE certification of the entire system. Cooperation in the very small, but very efficient engineering team was coordinated by MTU. The partner organisations, in each case are among the top providers in their markets, worked on equal footing as a team. They exchanged ideas and developed the decisive characteristics of the system in dialogue. This also included details like an auxiliary function for the operator where a laser pointer indicates the position to which the next part to be sorted belongs.
Criteria for partner selection
“The system that we have created together is very complicated and way more advanced than the technology employed to date”, says Marc Weiß enthusiastically. Reportedly, Liebherr impressed not just by having suitable products in the area of automation: The fact that the technology used is very well established and has proven itself very well in practice among many users was also important. A particular highlight was said to be the competence of the sales department. Technically, Mr Appel proved to be an extremely capable partner who became heavily involved and was able to provide many good ideas. The ramp-up of the overall system went successfully and the results so far have met the planning specifications. With the new system, MTU considers itself to be well equipped for the requirements of the future and the expected shortage of skilled workers.