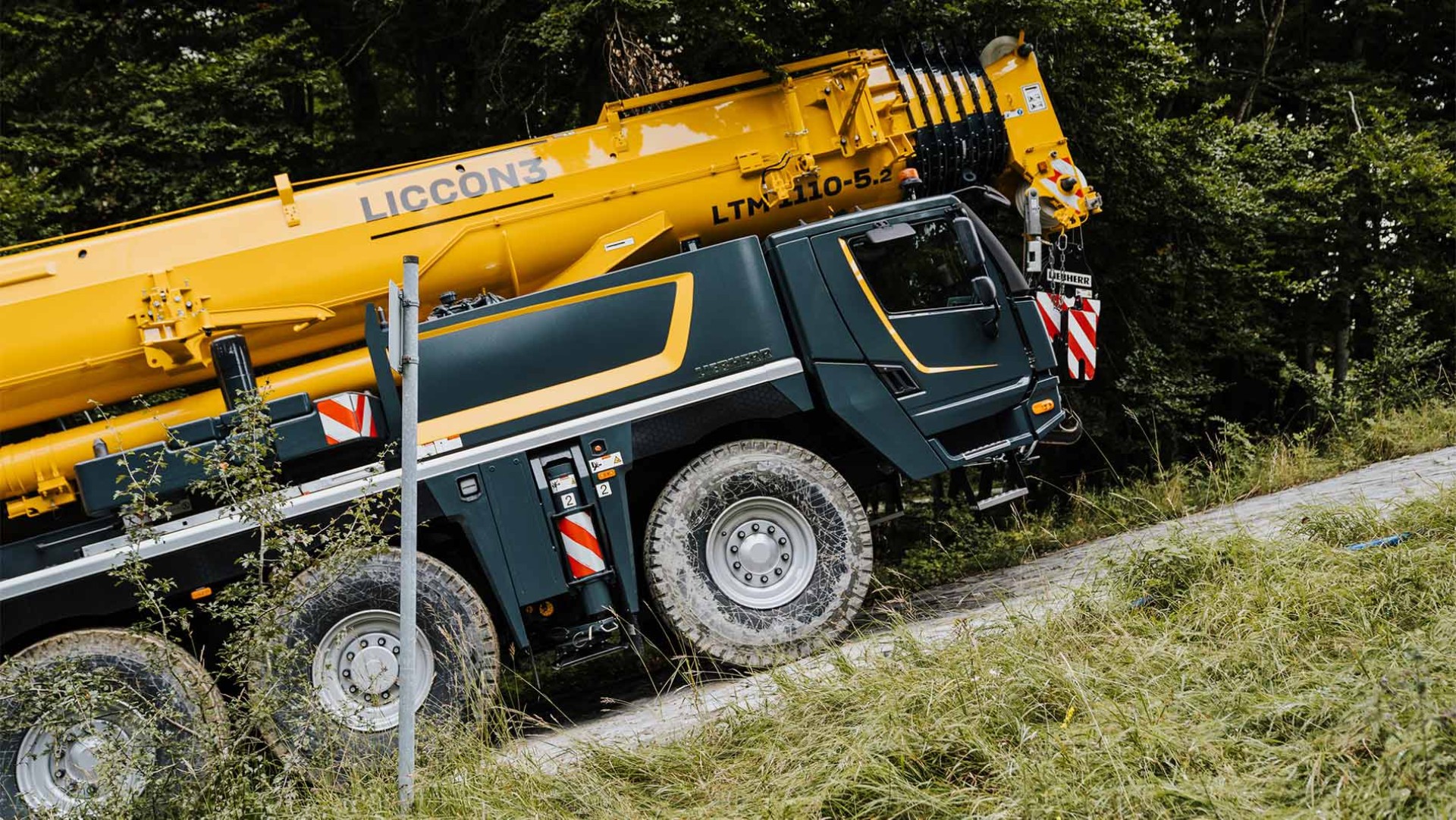
6 minutes | magazine 01/2022
Simply explained: TraXon DynamicPerform
Martin Dony from our Crane Chassis Development and Design Department explaines the advantages of TraXon DynamicPerform.
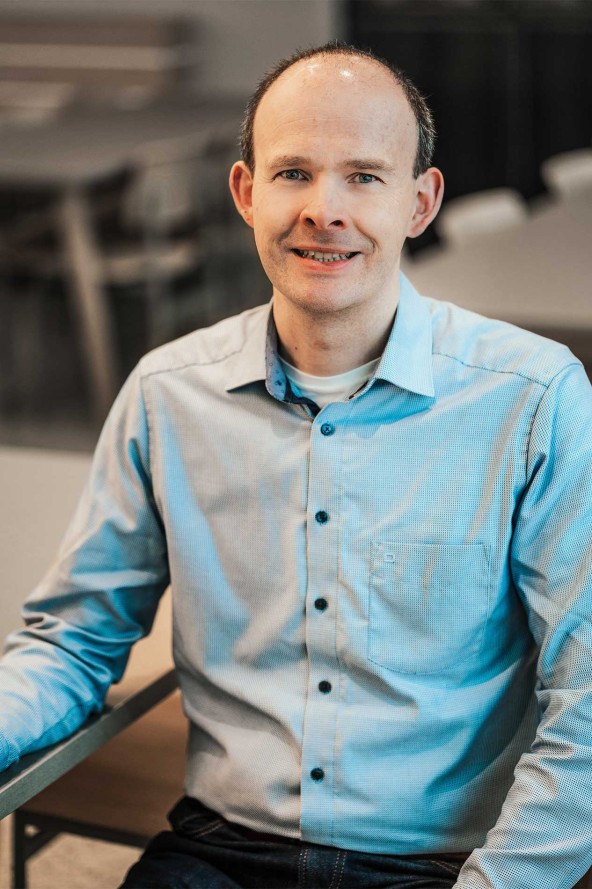
Martin Dony - Crane Chassis Development and Design Department
The wet starting clutch
At Bauma 2019, we announced a new gearbox to make starting and manoeuvring mobile cranes possible with zero wear – TraXon DynamicPerform. Since then the new gearbox has undergone a period of intense testing and advanced development. Now it is ready for widespread use. First of all, it will be installed in the new LTM 1110-5.2, after which we will start to install it gradually in our mobile cranes with between three and five axles, starting with other 5-axle models. Martin Dony, an engineer in our Crane Chassis Development and Design Department, explains exactly what DynamicPerform is and what benefits the new gearbox delivers in practice.
DynamicPerform is not actually a new gearbox at all, it is the new clutch module for ZF’s TraXon gearbox. The main benefit in short is that it delivers zero wear for starting and manoeuvring with centimeter accuracy and with no overheating.
Before I tell you exactly how it works, I would like to go back a little in the history of gearboxes in Liebherr mobile cranes. Until around 20 years ago, we had automatic transmissions in all our mobile cranes, in different sizes depending on the weight of the vehicle. Thanks to the integral torque converter, using the clutch generated zero wear. However, the downsides to these gearboxes included their great weight and high price as well as high fuel consumption and low speeds due to the low number of gears.
In 1999, we launched the first automated manual gearbox for Liebherr mobile cranes in the LTM 1100/2, which at the time was part of ZF’s new AS-Tronic gearbox family. The electronic gearbox control system enabled automatic clutch and gearshift operations to take place without the driver having to do anything. Twelve or sixteen gears delivered better gearshift quality to improve the operation of the diesel engine within its optimum engine speed range and led to more economical driving with lower fuel consumption.
However, many crane drivers first had to get used to the much more challenging gearshifts with the dry clutch. The increased friction during starting and manoeuvring meant that the clutch lining could suffer wear and the clutch could overheat. This was the reason that the vehicles were fitted with a two-stage distributor gear. Whilst the second stage is normally used to increase the torque and therefore to enhance gradeability, the lower gear ratios in a crane vehicle are generally used to reduce travel speed. This enables the clutch’s friction to be reduced during manoeuvring, thus minimising the wear on the friction lining.
In 2017, the AS-Tronic gearbox was replaced by the modular TraXon gearbox system. This completely newly developed gearbox series delivered improvements in terms of the transferred torque and efficiency, whilst also significantly reducing noise emissions. At the same time, new functions such as Hill Start Aid and the "ECODrive” program, a gearbox setting to improve fuel consumption, were introduced.
But even with this new gearbox system, there was no zero wear starting and gearshift clutch for more lightweight vehicles. As the torque converter for the TC Tronic HD and TraXon Torque gearbox, which we use all our 6-axle cranes and above, is too heavy and too expensive for smaller mobile cranes, we have been looking for an alternative for some considerable time. When ZF had examined the possibility of developing an oil-cooled multi-disc starting clutch in the course of its initial development, the “wet starting clutch” project for mobile cranes and special vehicles was started and Liebherr became involved in the ZF development in the role of lead customer.
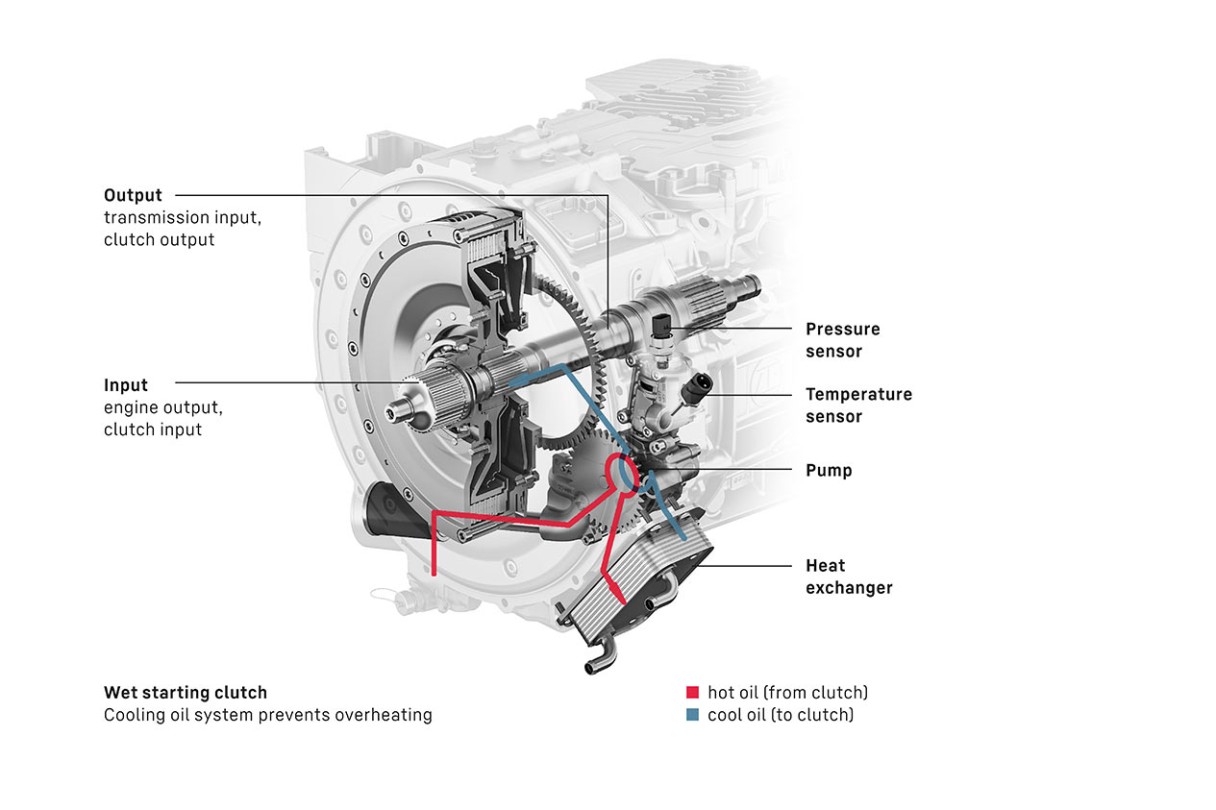
DynamicPerform takes the strain off the crane driver and reduces maintenance costs.
„Wet starting clutch“
The main function of the clutch between a diesel engine and gearbox is to balance the speed between the drive and output sides. At the beginning of the starting process, the diesel engine initially turns at slightly higher than idling speed. The section of the drivetrain downstream of it (gearbox, gear shafts, distributor gear, axles and wheels) remains at a standstill. If the clutch is now slowly closed, the friction forces between the clutch surfaces transfer the speed of the diesel engine to the output side and cause the downstream drivetrain to start moving. As the output side is not yet turning at the same speed as the drive side, a large proportion of the drive energy is converted into heat energy due to friction. The speed of the output side gradually increases and the speed of the vehicle continues to rise. The friction heat is generated up to what is known as the bite point after which the speed of the output side is identical to that of the drive side.
When using a dry clutch, the heat energy is absorbed by the pressure plate (steel compound) and the clutch lining. The pressure plate only cools slowly due to the low level of heat transfer between steel and air. If the lining disc is exposed to great heat frequently, it will wear more quickly. However, DynamicPerform is based on the principle of a wet multi-disc clutch whose typical feature is the parallel arrangement of multiple friction linings. This enables the multi-discs to absorb more heat energy. Cooling the discs with a flow of oil enables the heat to be dissipated quickly. The oil in the clutch transfers the energy in an oil-water heat exchanger to the diesel engine’s coolant circuit which then dissipates in the cooling system.
The new clutch module has an integral control unit for the oil cooling system. ZF has developed special temperature models for the particular requirements of a mobile crane in its software and tested them exhaustively together with Liebherr. Pressure and temperature sensors enable the condition of the clutch to be monitored so that protective functions can be activated in critical situations. Tests in a refrigeration chamber at temperatures as low as minus 40 degrees have confirmed that DynamicPerform works reliably even in extremely low temperatures.
Clear advantages
So what are the benefits of the clutch for everyday use? All starting manoeuvres generate zero wear, which means that none of the clutch’s components suffer any wear at all. Even hard starts, such as starting on gradients, can be carried out multiple times in short intervals. Finally, for manoeuvring with centimeter precision, for which only a fraction of the engine speed is transferred by the clutch to the drivetrain, the friction on the clutch also creates zero wear as a result of the oil cooling system. The dissipation of the heat prevents the clutch overheating and increases the availability of the vehicle.
Crane drivers can now concentrate fully on the manoeuvres without having to think about the stress on the clutch. Crane contracting companies benefit from the long service life and the easy maintenance of the clutch. The oil can be changed using the same service interval as other jobs, thus reducing downtimes to a minimum. This therefore saves costs on maintenance work. The whole thing means that innovative technology has made mobile cranes just a bit better.
This article was published in the UpLoad magazine 01 | 2022.