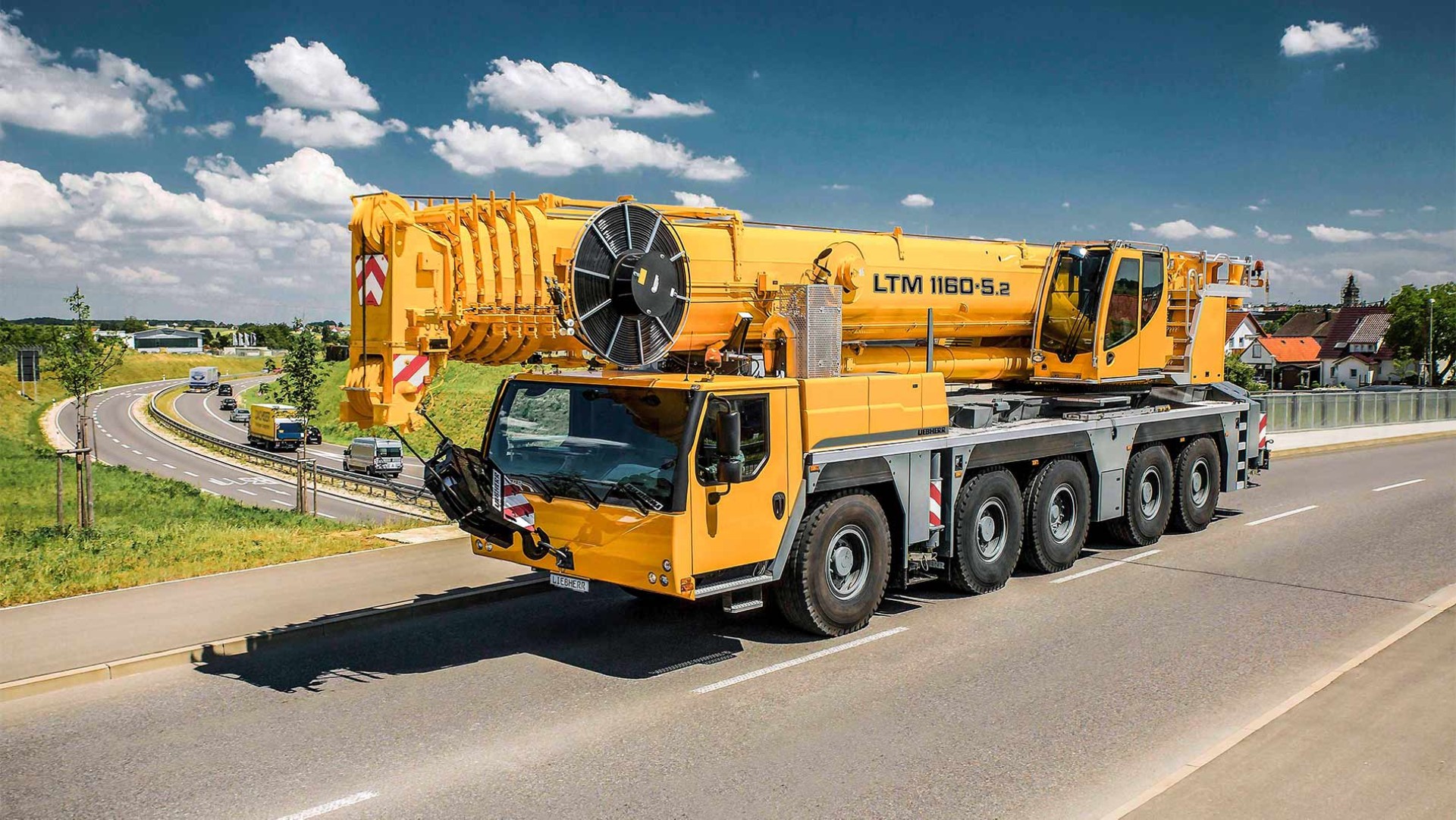
26 minutes | magazine 01/2022
From cradle to grave
In the last edition of UpLoad, we started a series of articles under the heading “Sustainable”. In this edition, we report on an interesting study carried out in collaboration with economics consultancy, Frontier Economics. It analyses how emissions of greenhouse gases from mobile and crawler cranes can be reduced by using alternative power units.
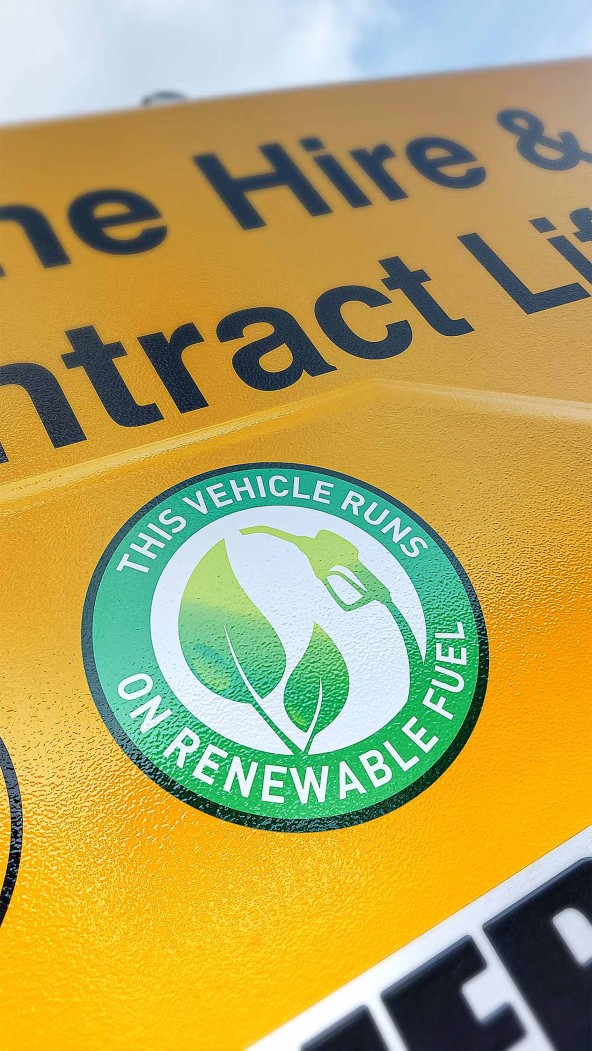
Interview
The background and results of the study are explained by Technical Director Dr Ulrich Hamme and Crane Vehicle Department Manager Phillip Federle. They also provide some insight into things that have already been done.
Why did Liebherr ask an economic consultancy to analyse sustainable power units?
Dr. Hamme: Our economy must be restructured to achieve climate protection targets and comply with the greenhouse gas limits. Mobile cranes are a vital component for the process of change to establish a decarbonised economy, for example for erecting wind turbines and modifying infrastructure. However, mobile cranes also emit greenhouse gases. To ensure that the remaining greenhouse gas budget can be used efficiently, mobile cranes are one of the things that must be subjected to holistic life cycle analyses.
Liebherr’s motivation and objective was to conduct a comprehensive greenhouse gas life cycle analysis of Liebherr construction machines, particularly of its mobile cranes. The technical expertise and product competence required for this process is provided by Liebherr. The economic competence and expertise of comprehensive energy considerations and assessments for life cycle analyses comes from renowned, experienced economics consultancy Frontier Economics.
The entire life cycle must be analysed to enable alternative power units for mobile cranes from an ecological perspective.
Federle: Liebherr and Frontier Economics have conducted an analysis for mobile cranes to determine what quantities of greenhouse gases they cause over their entire life cycle. Because although they are a driving force in the decarbonisation process and are essential for expanding renewable energy types such as wind power, they are also an emitter. The analyses by Frontier Economics are restricted to a scientific calculation of greenhouse gas emissions by various drive technology types, but do not reflect whether these approaches are technically feasible and effective.
What does a life cycle analysis actually comprise?
Federle: The emissions which are directly emitted by a vehicle can be calculated relatively easily from the volume of fuel inserted into the vehicle. Using the example of electric vehicles, the initial analysis shows zero CO2. However, if we operate electric vehicles using electricity generated with coal, we have simply shifted the emissions to a different zone and have not reduced them – a fact that is often ignored, whether that is deliberate or otherwise.
Energy generation and supply must not be ignored as does not matter to the environment when and why emissions are produced. That is why a holistic approach is required. However, it is not possible to produce a holistic picture unless you include the production process. During this process, CO2 are generated, for example for steel, by ore extraction and at the steel rolling mill, taking recycled material into account, to the point at which the material is cut to be fitted onto the crane. And that applies to all materials, whether they be rubber, copper, electronic components, textiles or aluminium. The subject of waste disposal for components is the final aspect. Only now do we really know that emissions do not simply disappear. So there is no point saying pretty words to try and conceal that fact. That means that everything has to be covered – from cradle to grave as we say in the industry.
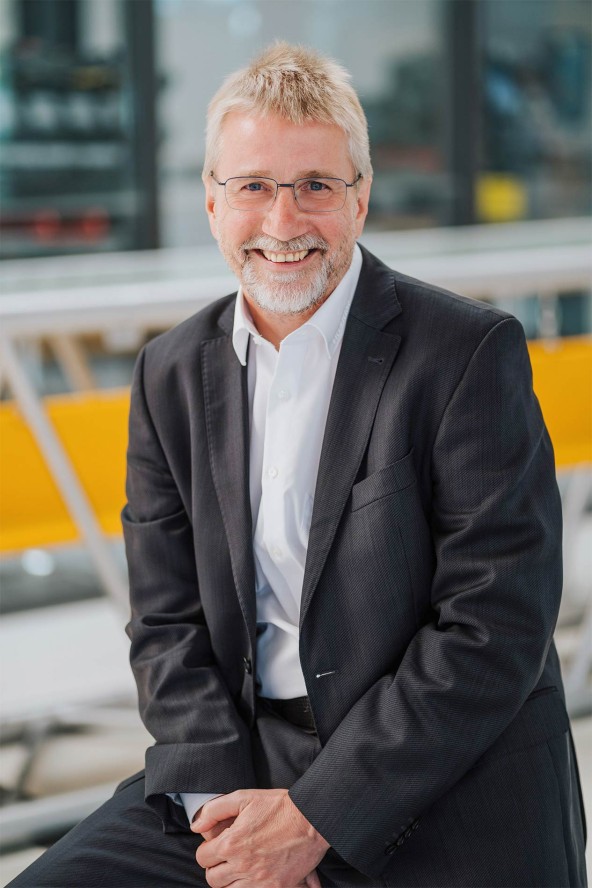
Dr. Ulrich Hamme - Managing Director Design and Development
Dr. Hamme: Despite the fact that mobile cranes have a major role to play in converting the economy, they are nevertheless also greenhouse gas emitters, and therefore part of the problem. They also have to be operated and manufactured on an increasingly carbon-neutral basis. An informative greenhouse gas analysis must therefore consider emissions throughout their life cycle. Life cycles of mobile applications such as the mobile crane involve at least the following five stages:
- Production (cradle-to-gate)
- Energy production (well-to-tank)
- Infrastructure expansion
- Mobile crane use (tank-to-wheel)
- Scrapping or recycling (end-of-life)
What did the studies show?
Dr. Hamme: The study of the mobile crane, for which we used an LTM 1160-5.2 as a typical example, showed us when it generated emissions and what volumes were generated. We also saw how these emissions were generated and how different materials or usage scenarios contribute to CO2 emissions. Naturally, we cannot simply remove components from a crane to reduce emissions. And the same goes for functions which the customer requires. But it shows us where we should direct our focus.
Federle: What is more, in the study, we not only calculated the current crane with all its components, but also calculated it with alternative power units so that we could compare them. We only studied those alternatives which appear to be practical at the current time. There are certainly other, technically very interesting approaches in the market which are also being discussed. However, we are not currently expecting that these will come into the reckoning with the relevant infrastructure over the next 10 to 15 years.
As of now, we can reduce CO2 emissions by around 75 % over the entire life cycle with HVO.
But what contribution can these alternative power units make?
Federle: We use the current crane with a diesel engine generating 100 % emissions as a reference. The results show that with our current knowledge and technology, the greatest CO2 reduction can be achieved with hydrogenated vegetable oil. The use of hydrogenated vegetable oil, known as HVO, enables us to achieve CO2 reductions of around 75 % over the entire life cycle. E-fuels, which constitute an equivalent technology for the crane, enables reductions of over 60 % of emissions to be achieved.
Dr. Hamme: A hydrogen internal combustion engine would actually increase emissions if it uses the hydrogen we produce today as it is normally produced using natural gas. That makes it senseless from an ecological point of view. For this reason, we decided to consider this technology with a future scenario using green, imported hydrogen. That would enable us to reduce well over half the emissions. A fuel cell results in the same tendency as a result of the fact that it uses hydrogen as the fuel, but this scenario highlights the better efficiency level of this technology.
A battery-electric power unit can also not contribute to reducing emissions using our current electricity mix. We therefore conducted another calculation in which we assumed that we could use 100 % green electricity. This produced CO2 reductions of over 40 %. This clearly shows that the battery production process accounts for a very large proportion of the emissions.
Why do green electricity and green hydrogen still produce emissions if they are green by name and by nature?
Dr. Hamme: This is where unfortunately the holistic approach is simply ignored. If you erect a wind turbine today, the vast majority of the foundation and tower is made of concrete and steel. However, these raw materials cannot (yet) be produced on a CO2-neutral basis. This means that on day one, a wind turbine has a CO2 rucksack which, of course, must be applied to the kilowatt hours it generates over its service life. This approach also applies to solar cells.
In addition, overhead cables and transformer stations also have to be considered. This means that a whole host of things are included in the final account. Unfortunately, we have to get away from the idea that the things that are currently described as “CO2-neutral” or “green” actually produce zero CO2. It is the same in practice as alcohol-free beer. It still contains small quantities of alcohol. With this in mind, I am looking forward to finding out how the first cities want to become CO2-neutral by 2030 as local CO2 neutrality actually does nothing for our ecology. As long as a cement plant remains the same although it is not in the town, the environment has gained nothing.
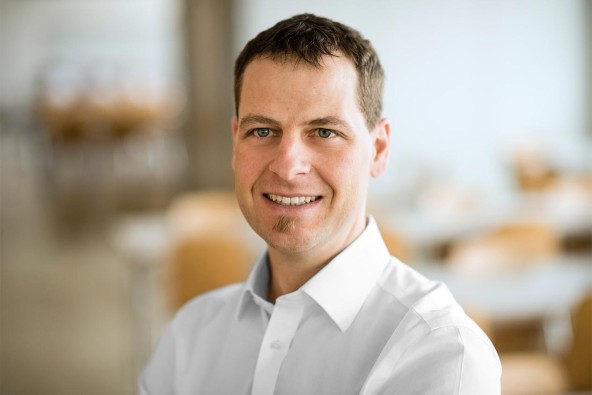
Phillip Federle - Head of Crane Vehicle Design Department
Why does fuelling cranes with HVO do even better than the version involving e-fuels?
Federle: That is definitely to do with the HVO that we use here in Ehingen. It was absolutely plain to us at the start that we must not use HVO produced using palm oil or palm oil residues. For this reason, we at Liebherr only buy HVO which is certified as being produced from waste – in actual fact from vegetable oils. That means that the waste at the current time involve no CO2 rucksack. Emissions only have to be added for our crane from its conversion into fuel, its transportation and storage. If we were to plant sunflower oil specially for this purpose, the potential savings would be a little lower. With e-fuels, on the other hand, you always first have the emissions from the construction of the wind turbine or solar plant which means that this type of fuel will always generate slightly higher emissions.
What hurdles or limits are there to HVO?
Dr. Hamme: The main limit for this fuel is definitely its limited availability. The volume of waste is obviously limited and this means that as far as we can see, it will never be possible to produce HVO in the quantity we would require to replace the diesel we currently consume. Values could certainly be increased a little by planting sunflowers or rape but it must be ensured that we never go so far that we find ourselves cutting down the rainforest to plant palm oil simply to protect the environment! This limit will certainly be the cause of more discussion among politicians and in general society.
Some truck manufacturers have decided to go for hydrogen-powered fuel cell power units and are investing millions of euros in their development. Large amounts are also being invested in expanding the production of green hydrogen. How do you view this technology in the medium and long term for mobile and crawler cranes?
Dr. Hamme: We are, of course, monitoring the developments in hydrogen engines and fuel cells for all applications, for example in commercial vehicles and construction machines, very closely. At our engine plant in Switzerland, we are currently commissioning the first prototypes of a hydrogen engine on a test bench. This is where we have housed the hydrogen expertise available within the Liebherr Group. In a similar way to battery-electric power unit, there is no hydrogen technology that is available for immediate use in mobile cranes.
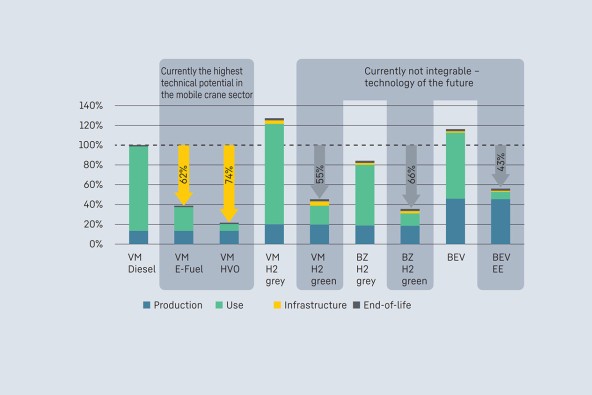
Comparison of CO2 emissions by various types of power unit (using the LTM 1160-5.2 as an example) (VM=Internal combustion engine, BZ=Fuel cell and electric motor), BEV=Battery and electric motor, EE=Electricity from renewable sources)
Federle: Fuel cell power units are not really suitable for mobile cranes which experience very uneven stresses and high load collectives. Hydrogen engines may therefore be more interesting. The lack of clarity overall is still so great that it is not currently possible to define any realistic targets. One of the core problems is storing the energy on a crane. There is not enough weight or volume available for hydrogen in gaseous form or for liquid hydrogen which has to be cooled to very low temperatures.
Dr. Hamme: There are still a great many questions to be answered in terms of storage technology, refuelling logistics and supply infrastructure. We must wait and see and watch closely what development routes are taken in the near and distant future, particularly for commercial vehicles and construction machines.
Are the different approaches involving hydrogen and batteries the wrong technical development routes from this ecological point of view?
Dr. Hamme: Definitely not! There is still considerable development potential for these technologies which cannot be fully assessed at the current time. We are only talking about a review based on the current situation. What is more, we are only talking about an extract from the study, and the statements only refer to a mobile crane. The same process showed that significant benefits were possible for installing an electric motor in a mixer truck or a small wheel loader, for example.
Why is there such a difference if the same procedure is used?
Federle: That is because of the extremely different ways in which the machines are used. As far as the crane is concerned, it was important for us to compare machines with identical functions. In other words, the machine must be capable of completing the same work as a current crane. This also includes the flexibility to work autonomously. A mixer truck, on the other hand, returns to base every night were it can be charged. And whilst it is being loaded with concrete, it can also be charged with electricity as it would be possible to provide the appropriate charging infrastructure.
Dr. Hamme: In addition, the mixer truck travels very limited distances compared to the crane and has to deliver a comparatively low level of performance. The load cycle of a mixer truck cannot be compared to that of a crane. If you can reduce the volume of stored energy as a result these marginal conditions, the battery can be reduced in size, thus significantly reducing the emissions from the production process.
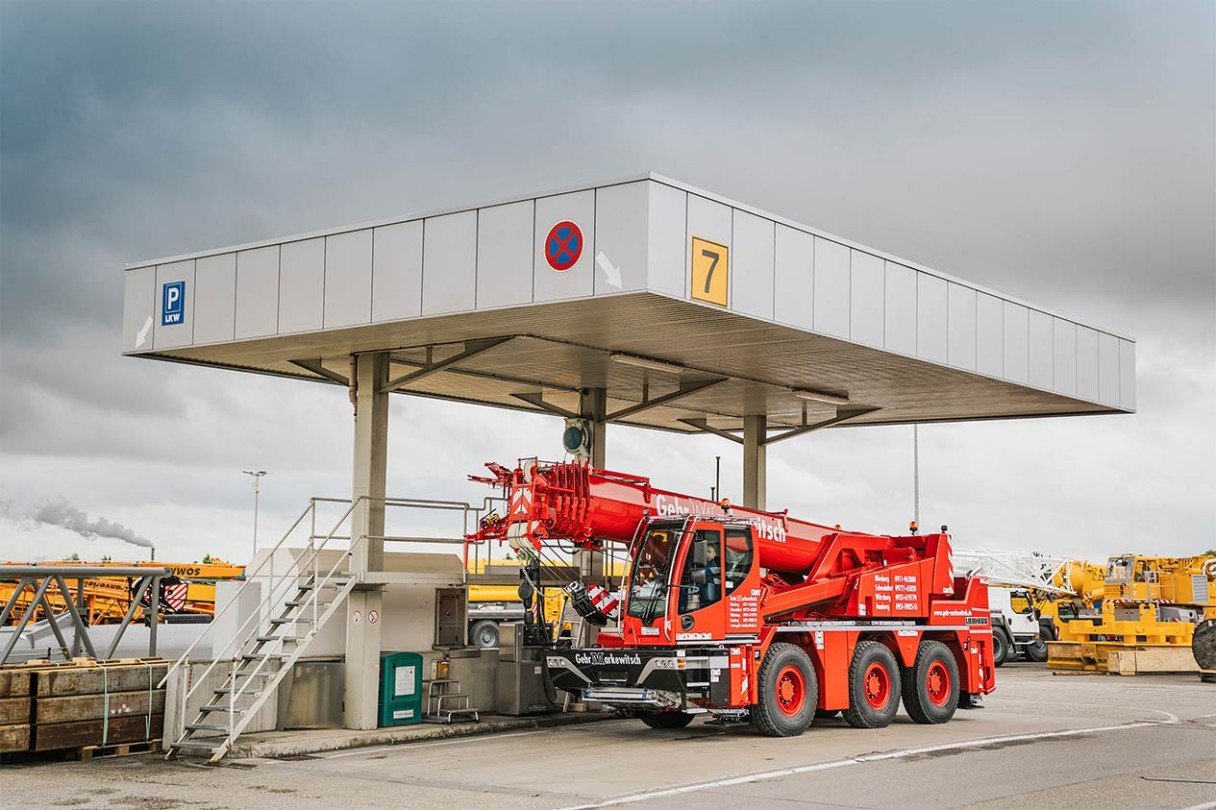
Hydrogenated vegetable oils: The filling station at the Liebherr Plant in Ehingen has been converted to HVO fuel.
Why is Liebherr in Ehingen not currently pursuing battery-electric power units? Has this technology any potential for mobile and crawler cranes in the medium term? We read about developments which can significantly increase the capacity of batteries and drastically reduce charging times.
Dr. Hamme: Battery-electric power units are not a realistic power option today for any mobile cranes, both all-terrain and lattice boom types, due to a large number of aspects which cannot be realised with any sort of priority. In terms of climate protection and economy, this technology is not the first choice for our type of machines, quite apart from the fact that technically mature, sustainable solutions are not currently available for our cranes.
Federle: The amount of energy in lithium-ion batteries is very low relative to their size and weight. To deliver the familiar flexibility and performance of a mobile crane using a battery-electric power unit, for example, around 20 tonnes of batteries with a volume of more than 15 cubic meters would have to be fitted on the 5-axle LTM 1160-5.2 crane studied by Frontier Economics. That is completely unrealistic and shows that the current technology has no potential for universal installation in a fully electric mobile or crawler crane.
External battery packs for cable power supply as an alternative to mains power are also conceivable for use on small mobile cranes. It may be possible to meet the demand for “local zero emissions” on larger cranes using buffer battery storage devices.
Dr. Hamme: Other conditions such as safety, thermal stability, charging speed, charging logistics, service life and ultimately also economy will not make it any easier to use battery-electric power units in mobile cranes. There are no signs of any revolutionary developments of this technology which could vastly improve the above criteria.
The continued development of battery power units is focusing more on their mass use in cars and is subject to totally different requirements than those for using them in large, heavy cranes.
We are naturally monitoring the development of batteryelectric power units very closely by adopting an “openness to technology” approach. We have bundled the technological competence for this within the Liebherr Group at a “Battery Competence Centre”. This will ensure that we stay on the ball and do not miss any developments.
Mobile construction cranes in the MK series can be operated with site power as an alternative to an internal combustion engine. Could the technology behind this also be a reasonable alternative for telescopic mobile cranes?
Federle: It is, of course, conceivable that this technology could be an alternative power unit for small mobile cranes as well. But as I say, that is an alternative. In other words, in addition to the HVO diesel engine for road travel and crane operation, it would require an additional electric motor to be installed for the superstructure. That would involve a great deal of volume, weight and money.
Dr. Hamme: The answers to a series of technical, application-related and economic questions must be sought for every single application and every crane model. It should be possible to operate a telescopic mobile crane supplied with site power in the same way as a crane with an internal combustion engine. The electric power unit must be designed so that site power can deliver almost the full performance of the crane, as well as the speeds of crane movements and the dynamic of a crane. That becomes more difficult, of course, as the crane gets bigger. The strength of the external power source, for example site power from a mains supply, is also limited. An approach of this type is certainly conceivable for individual small telescopic mobile crane models for which “local zero emissions” play a role because they are frequently operated within enclosed areas.
Liebherr has developed a battery-electric 250 tonne crawler crane at Nenzing. Can this technology also be used in smaller crawler cranes from Ehingen?
Dr. Hamme: The “smaller” crawler cranes in Ehingen start with a nominal lifting capacity of 500 tonnes and are designed to act purely as heavy duty assembly cranes. In other words, they are at least twice as powerful and twice as heavy as the electric 250 tonne machine from Nenzing. The battery-electric approach cannot be scaled up on a linear basis for these crane sizes.
The approach taken by our colleagues at Nenzing of building a crawler crane which is also a mobile crane with only an electric power unit is very courageous and an exciting development. The universal range of uses, the way in which the crane is used, the flexibility and the performance of the electric crane compared to a conventional crane with a diesel engine are all subject to change.
The battery capacity installed in the LR 1250.1 unplugged must be combined with a cable connection to manage an average working day and the site must also provide a charging facility for the crane’s batteries. The approach for the 250 tonne crawler crane cannot be reasonably be used for the large heavy duty crawler cranes we make in Ehingen taking into account all the relevant aspects – and there are many of them.
Federle: Operating our cranes with the very latest emissions treatment technology which complies with Stage 5 and the use of synthetic fuels is a much more practical method and is already available on a widespread basis. This is also shown by the results of the Frontier Economics study we discussed earlier. Naturally, this “clean” crane still has some residual exhaust emissions.

Volume requirement and weight of medium including tank for various type of power unit using the LTM 1160-5.2 as an example
Liebherr has already stated that there will be an electrically powered version of a compact Liebherr mobile crane at the next Bauma. Can you tell us any more about this?
Dr. Hamme: We have plans to launch the LTC 1050-3.1, our 3-axle, single cab compact crane in the 50 tonne class, with an additional, optional electric power unit for all crane functions before the end of the year. In other words, the crane will be fitted with the conventional diesel engine fuelled with HVO for road driving and crane operations, but as an alternative will also be able to carry out crane operations with an electric motor so that it complies with the “local zero emissions” requirement. That means that all the familiar usage properties of the crane will be retained, regardless of whether it is operated using its zero emissions power unit or its internal combustion engine.
The power for the electric motor will come from the local power supply using a cable connection. A heavy current 125 ampere connection is required to be able to use the crane’s full performance. The maximum working speeds may be reduced with a 63 ampere connection.
With this approach we ensure that the hybrid LTC 1050-3.1 can continue to be used economically as a flexible “global crane” at all sites. Customer benefits, everyday practice and economy go hand-in-hand with global and local environmental protection.
The future therefore has lots of interesting things in store on the theme of sustainable power units to reduce CO2. But let’s look at the present. What is Liebherr actually putting in place in Ehingen?
Federle: Since September 2021, we have been fuelling our mobile and crawler cranes at the Liebherr plant in Ehingen exclusively with pure HVO. This is used for the crane trial procedure and test drives as well as the first tank of fuel before delivery. Over the last few months, we have been working on preparing the entire range of mobile and crawler cranes for use with HVO. The diesel engines were first checked, certified and approved by the manufacturers for this purpose. The cranes have also undergone extensive testing and trials with pure HVO by customers and in our own trial department.
Dr. Hamme: We have analysed all the vehicles that drive around our plant at our Ehingen site. With a very few exceptions, they can also be fuelled using HVO. As a result, we will be able to save 2.5 million liters of fossil diesel per year by switching to HVO fuel. This will result in an annual reduction of around 6,500 tonnes of CO2 at our plant.
And another thing – we have been exclusively purchasing green electricity for our Ehingen plant since 1 January 2022. So we are supplying the complete plant with certified electricity from European wind power sources. That is just another milestone towards CO2 neutrality.
What do you think about power units, alternatives and climate protection? We look forward to reading your views. Please send you mails to [email protected]. Perhaps we can use your question or view in one of our articles in our next magazine. Let’s get talking!
3 Questions to: Matt Waddingham - Managing Director, Cadman Cranes Ltd, UK
As one of the first crane rental companies worldwide, you’ve announced in July to adopt using HVO for your mobile crane fleet. Why did you take this step?
Waddingham: We have monitored our environmental impact for several years now and we were very aware that our consumption of fossil fuels was unsustainable in the long term. Though our crane replacement strategy has certainly made a difference with some great advances in crane technology and efficiency over the last few years we are still a mobile crane hire company and we need to move hundreds of tonnes of metal many thousands of kilometers every year. We knew battery power was not going to be an option for a long time so we started looking at the fuel itself. We were alerted to HVO early this year and the environmental gains did look incredible. After several months of discussions with crane and engine manufacturers and a series of trials we could not find a valid reason not make the switch.
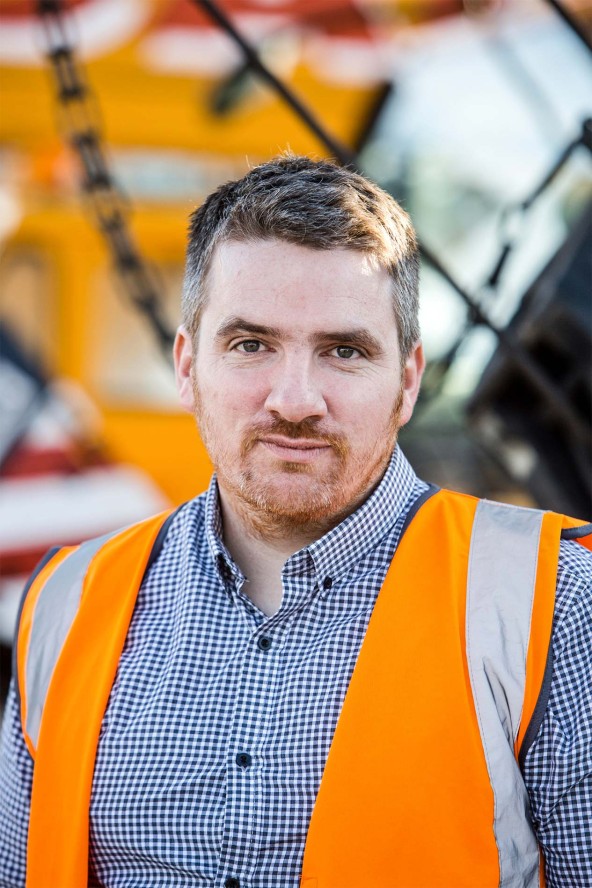
Matt Waddingham - Managing Director, Cadman Cranes Ltd, UK
We know there are some risks being the first to do this and we know that there will be some who are monitoring our progress before making any decisions. But we want to lead the way and we hope that our actions may be a catalyst for the rest of the industry. But it is not wholly altruistic, we know there are customers, projects and industries that will be fully supportive of more sustainable crane movements and we also know that, as an industry, big changes are coming – by choice or by regulation – and we think being in the lead is the best place to tackle these challenges.
Having HVO in use now for roughly half a year, what are you experiences with it, how do your customers react on it?
Waddingham: Our experiences have been wholly positive so far. We have seen no negative effects on the cranes itself and our customers have been very supportive and keen to understand it better. It is more expensive but we feel the gains are worth the extra costs. My only concern is the resilience of supply, we have had no problem getting it so far, even through the recent fuel supply dramas in the UK but we are aware that we don’t have the infrastructure in this country to produce it yet. It will be interesting to see what happens should there be a substantial uptake in its use. Now we have made this move we certainly don’t want to be going back.
Cadman Cranes Ltd.
Cadman Cranes Ltd. is one of the leading crane rental companies in East Anglia, United Kingdom, with over 50 years of history in the crane rental business. Since the beginning the company has made its great importance to being more than just another crane rental company. Quality, reliability and safety are the core values of Cadman Cranes, which are always geared towards customers and employees. Full-service solutions are offered that go well beyond crane rental. Matt Waddingham has been appointed Managing Director of Cadman Cranes Ltd. in 2019.
With this step, it’s a first move on the path towards net zero carbon. What else do you have in mind or already started with to take on this journey?
Waddingham: We are looking at everything and have a strong understanding of every aspect of our impact. But 70% of our carbon output is the crane movement and operation so this is where we have concentrated our efforts so far. We are part of the Milbank Group – a diverse group of companies with interests in agriculture, construction, manufacturing, information technology and retail – and our chairman is committed to nurturing successful businesses that make a positive impact on our communities. Soon we will have Sustainability Manager on board and we are looking forward to working with an industry expert to really shake things up and help plot our route to net zero carbon. But we understand it doesn’t end with us, or a small handful of companies, our customers and supply chain are just as important so it is great to see Liebherr’s commitment as well. It’s obviously going to be a challenging few years ahead but it is also exciting to see what innovation and ingenuity our industry can contribute.
This article was published in the UpLoad magazine 01 | 2022.