The future of zero emission haulage
Based on Liebherr’s proven T 264 mining truck, the T 264 Battery Electric is leading the charge for decarbonising the 240-tonne class. This 240-tonne capacity haulage solution not only plays an important role in reducing operational greenhouse gas emissions but is also compatible with a range of charging options, both static and dynamic, for optimal onsite flexibility. And on top of all this, the T 264 Battery Electric can be used autonomously, with Liebherr’s Autonomous Haulage Solution, to further enhance safety, productivity and efficiency.
Payload class - 240.00 t
240.00 t
Gross vehicle weight (GVW) - 416.00 t
416.00 t
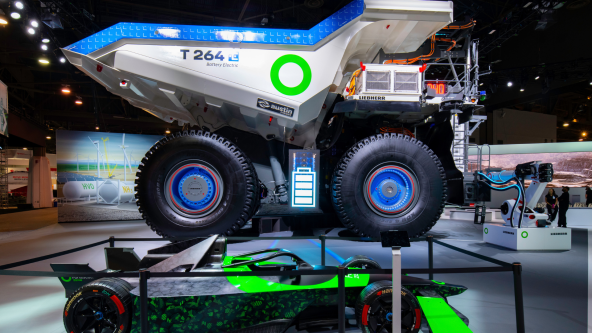
Making decarbonisation a reality!
Fortescue Zero is developing groundbreaking technology which push the boundaries of engineering, making industrial, enterprise decarbonisation a reality.
Liebherr and Fortescue Zero are working together to integrate the battery power systems developed in-house at Fortescue Zero, into Liebherr's mining trucks, to create zero emission haulage solutions for the mining industry.
Videos
This video is provided by Google*. When you load this video, your data, including your IP address, is transmitted to Google, and may be stored and processed by Google, also for its own purposes, outside the EU or the EEA and thus in a third country, in particular in the USA**. We have no influence on further data processing by Google.
By clicking on “ACCEPT”, you consent to the data transmission to Google for this video pursuant to Art. 6 para. 1 point a GDPR. If you do not want to consent to each YouTube video individually in the future and want to be able to load them without this blocker, you can also select “Always accept YouTube videos” and thus also consent to the respectively associated data transmissions to Google for all other YouTube videos that you will access on our website in the future.
You can withdraw given consents at any time with effect for the future and thus prevent the further transmission of your data by deselecting the respective service under “Miscellaneous services (optional)” in the settings (later also accessible via the “Privacy Settings” in the footer of our website).
For further information, please refer to our Data Protection Declaration and the Google Privacy Policy.*Google Ireland Limited, Gordon House, Barrow Street, Dublin 4, Ireland; parent company: Google LLC, 1600 Amphitheatre Parkway, Mountain View, CA 94043, USA** Note: The data transfer to the USA associated with the data transmission to Google takes place on the basis of the European Commission’s adequacy decision of 10 July 2023 (EU-U.S. Data Privacy Framework).Introducing our T 264 Battery Electric truck
Downloads
Technical data
Payload class | 240.00 t |
Gross vehicle weight (GVW) | 416.00 t |
Empty vehicle weight (EVW) | 176.00 t |
Drive system | Liebherr Litronic Plus AC drive system with IGBT technology |
Max speed | 55 km/h |
Machine gallery
Truck excavator match*
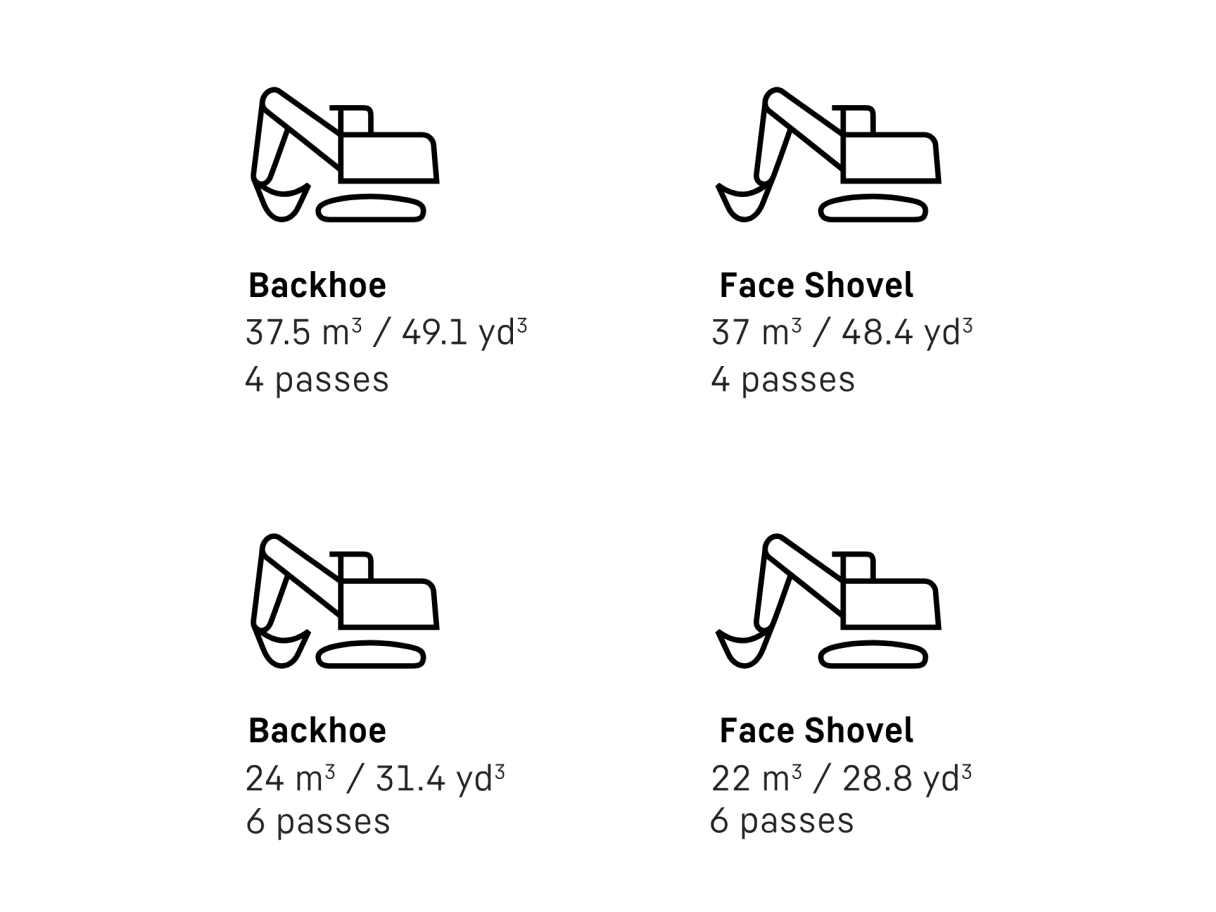
*Site-specific factors like loose material density, bucket size, fill factors, truck body size and payload capacity will influence pass match. Contact your local Liebherr sales and service company or sales partner for analysis of your site