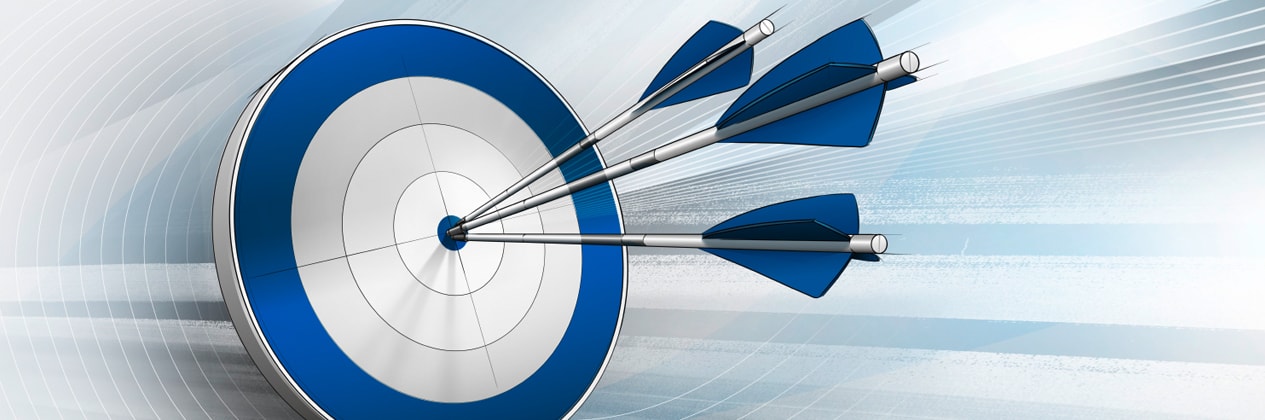
Magazine 2020
Magazine 2020
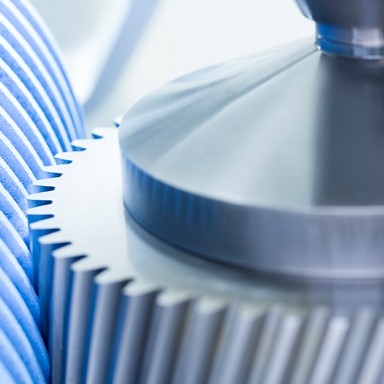
Liebherr presents the new series of generating and profile grinding machines for hard machining of external and internal gears on workpieces with diameters of up to 500 millimeters. The LGG series follows the successful Liebherr LCS 300 to 500 series. With an impressive range of added features, they offer more flexibility and grinding performance with a significantly reduced footprint.
Most read
01
In August 2019, trainees Fabian Altenried and Julia Fetzer participated in the Liebherr Summer Program at Liebherr Gear Technology Inc. / Liebherr Automation Systems Co. (LGT / LAU) in Saline, near Detroit. There, they ran the PLC programming course for pupils of the robotics course from the local high school, which was offered for the first time, and got to know the work routine at the Liebherr site. Fabian reports on his experience here:
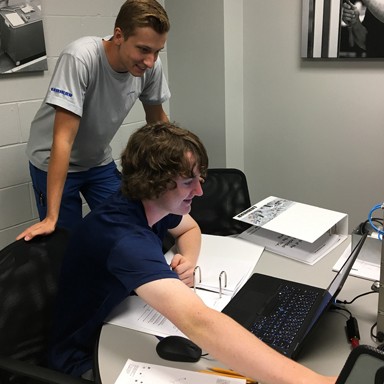
02
Liebherr presents the new series of generating and profile grinding machines for hard machining of external and internal gears on workpieces with diameters of up to 500 millimeters. The LGG series follows the successful Liebherr LCS 300 to 500 series. With an impressive range of added features, they offer more flexibility and grinding performance with a significantly reduced footprint.
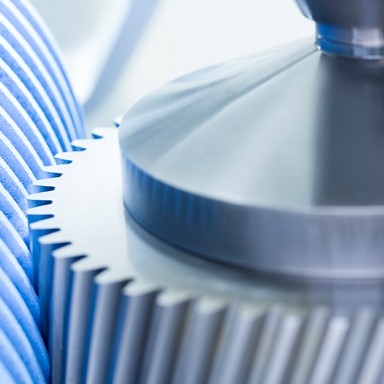
03
Gear skiving is over 100 years old and has recently been experiencing a renaissance as a flexible and economical alternative to other gear cutting methods. However, this complex process frequently presents great challenges to users. In addition to Skiving3, a “complete package” consisting of machine, tool and technology, Liebherr now also offers skiving tools for suppliers and contract gear manufacturers – and the appropriate consultation, if desired.
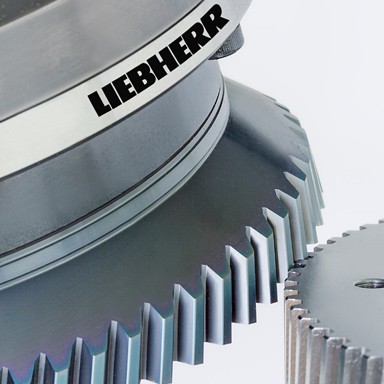
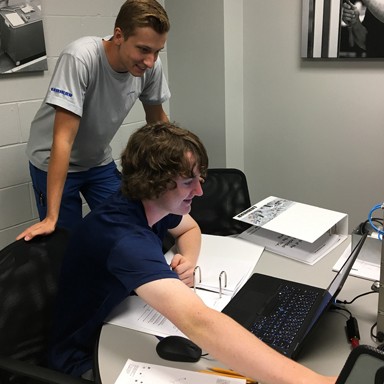
In August 2019, trainees Fabian Altenried and Julia Fetzer participated in the Liebherr Summer Program at Liebherr Gear Technology Inc. / Liebherr Automation Systems Co. (LGT / LAU) in Saline, near Detroit. There, they ran the PLC programming course for pupils of the robotics course from the local high school, which was offered for the first time, and got to know the work routine at the Liebherr site. Fabian reports on his experience here:
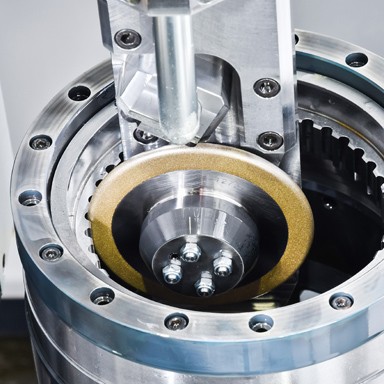
x
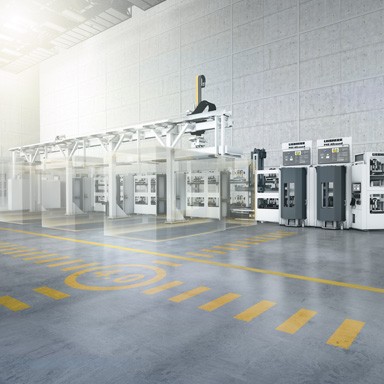
Liebherr presents the latest member in the PHS Allround family, the PHS 800 Allround. It has a narrower design than the PHS 1500 Allround, which makes it ideal for automated loading of smaller machine tools while retaining the basic principle of modular design and universal applicability and expandability.
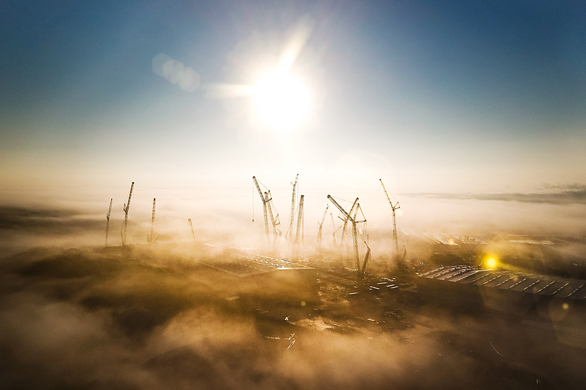
Insights into the highlights of the group
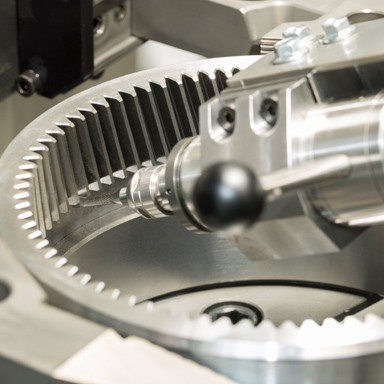
Anyone who manufactures small batch sizes of complex components wants to perform as many work steps as possible with a single machine. This not only saves time and equipment costs but also increases the quality, provided that the clamping fixture does not have to be changed. Liebherr-Verzahntechnik GmbH offers a comprehensive solution for complete machining by integrating a tool changing system and a chamfering device while using the turning, drilling and gear cutting functions of the latest generation of Siemens controls.
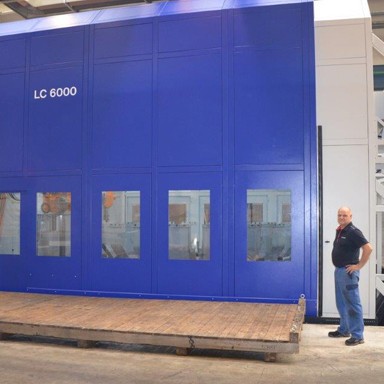
Karl-Heinz Klöble is responsible for putting large gear cutting machines into service in China. We spoke to him about his experiences there and what fascinates and motivates him in his unusual job – and why he’s too busy to retire yet.
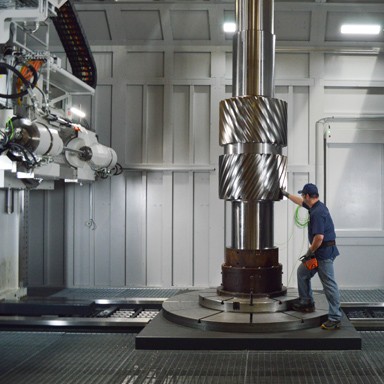
A visit to the HMC Gears plant in Indiana kicked off an extensive project which resulted in the creation of a unique solution for exceptional demands: With the LC 4000, Liebherr forges new paths in large-scale gear cutting production and unites diverse machining methods in one highly efficient machine for the American gear specialist.
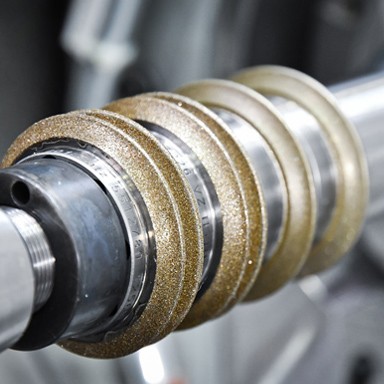
The machining of gears with interfering contours for the aerospace industry places the highest demands on the grinding tool and often cannot be carried out with standard grinding heads due to the small tool diameters. Liebherr has developed an auxiliary spindle for these applications which can be retrofitted. This enables the production of challenging aerospace components on existing LGG gear grinding machines.