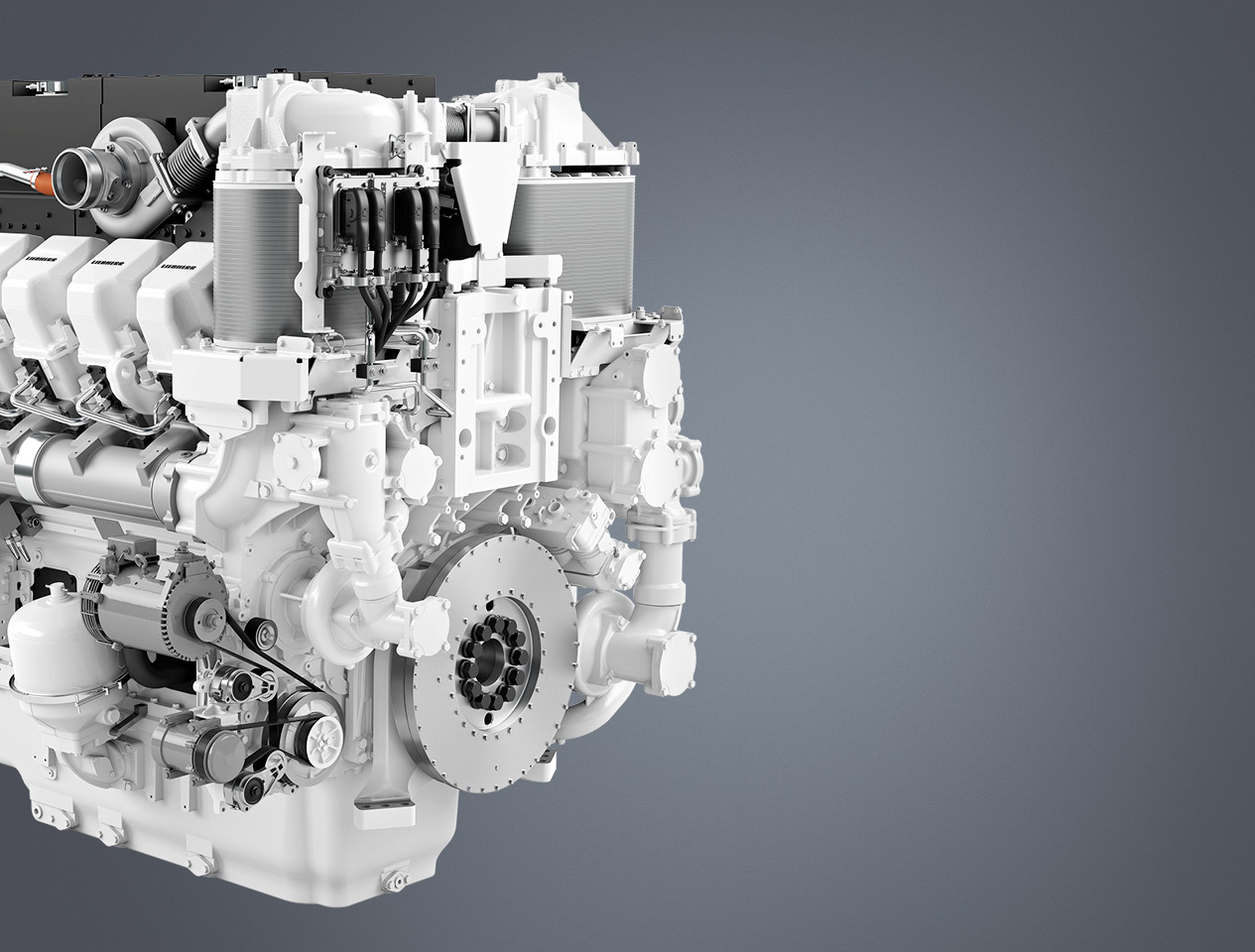
3D printed brackets
3D printed brackets
Metal FFF and 3D printing for the creation of prototype parts
Liebherr-Components attaches great importance to innovation and new technologies. We are proving this once again with a collaboration between our diesel engine production site in Colmar (France) and BASF Forward AM in Heidelberg, a company specialising in 3D printing solutions.
The story began with the additive manufacturing team at Liebherr Components, which is dedicated to the research and development of additive manufacturing solutions. In autumn 2019, they contacted BASF Forward AM to start a project and clarify the question: Is Metal Fused Filament Fabrication (MFFF) technology a reliable and competitive way to produce prototype parts for engine development?
The origin of the project/question
During prototyping phases, we do not have tooling for all components. As a result, they are often produced in very small quantities, with processes that are not representative of the series, which means high costs. We therefore wanted to carry out a feasibility assessment and draw conclusions on the benefits that could be obtained with this new process.
When we had to choose a possible part to test, our choice went to 4 brackets that hold the protective gird on the front of our diesel engines. On the one hand it was a low risk/high price part compatible with the process and on the other hand, it was important for us to have this pragmatic approach, balanced between R&D/integration of new processes and solution cost effectiveness.
Process
The first months were spent on project definition, feasibility studies and simulations, to start manufacturing the first parts during Q2-2020. These parts were tested and optimised through a number of test phases, including assembly tests. The brackets were finally analysed by an experimental modal and microstructure analysis at the end of 2020. Since the beginning of 2021, we have started implementing the new brackets on diesel engines prototypes for test runs.
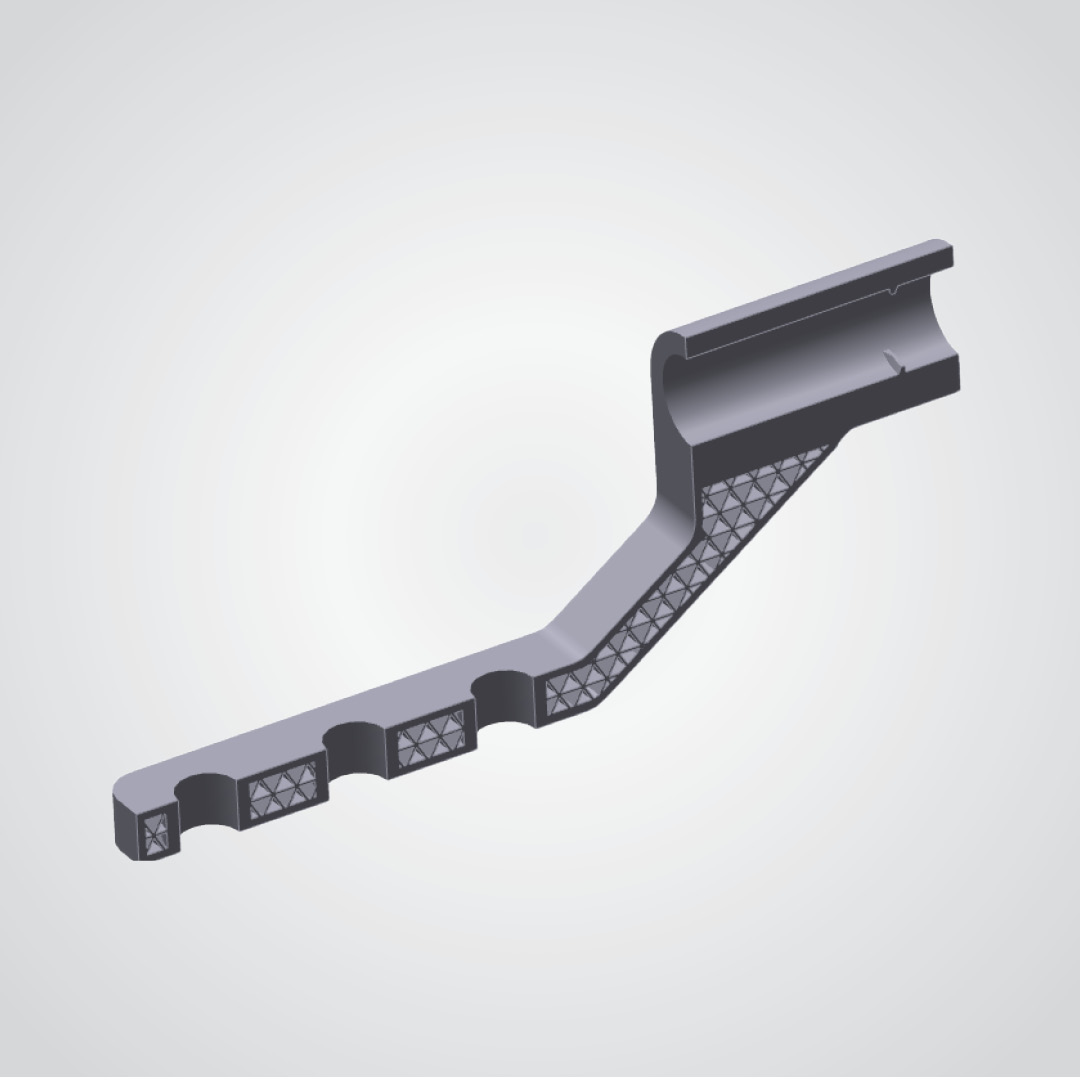
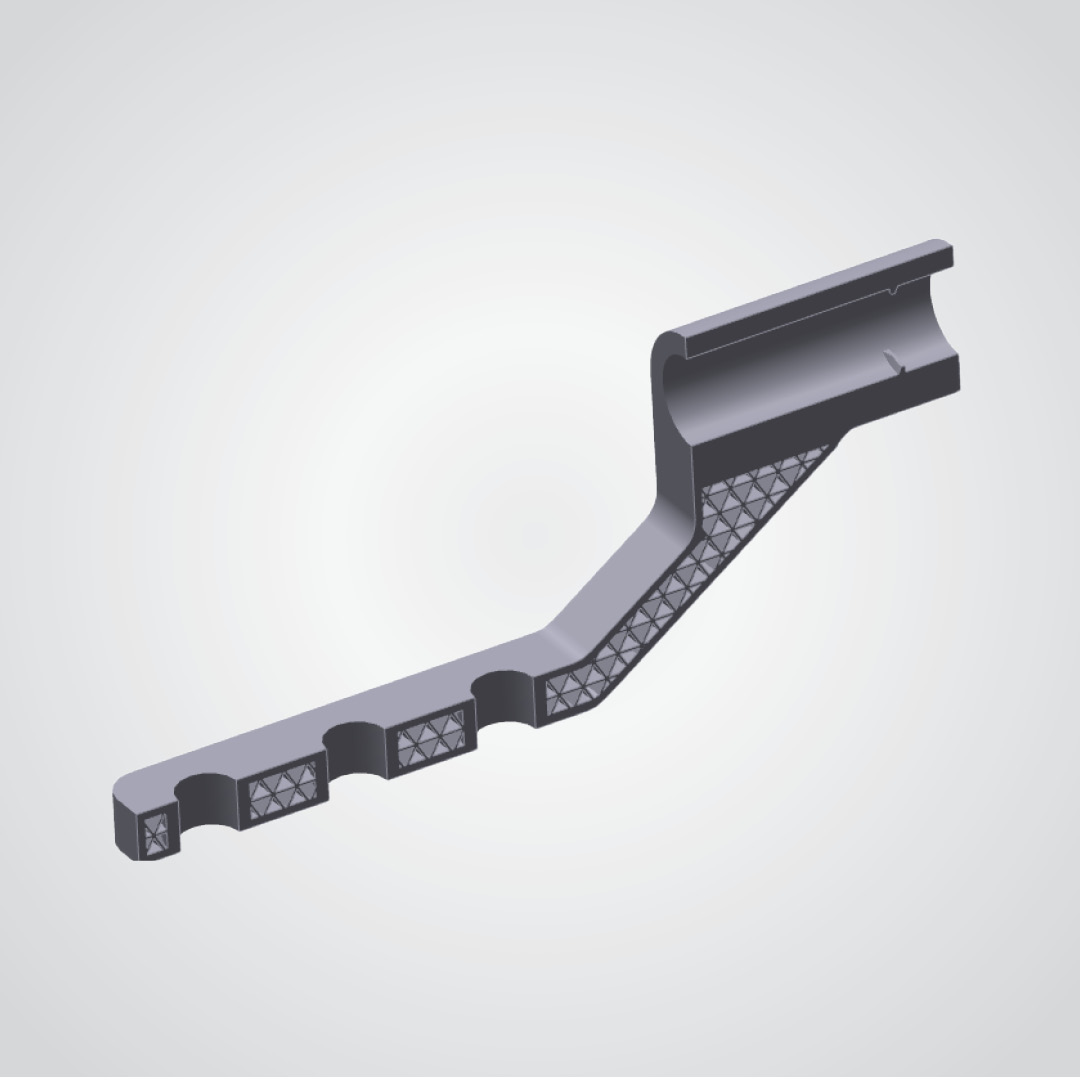
Internal structure of the part
Additive manufacturing enables variable density
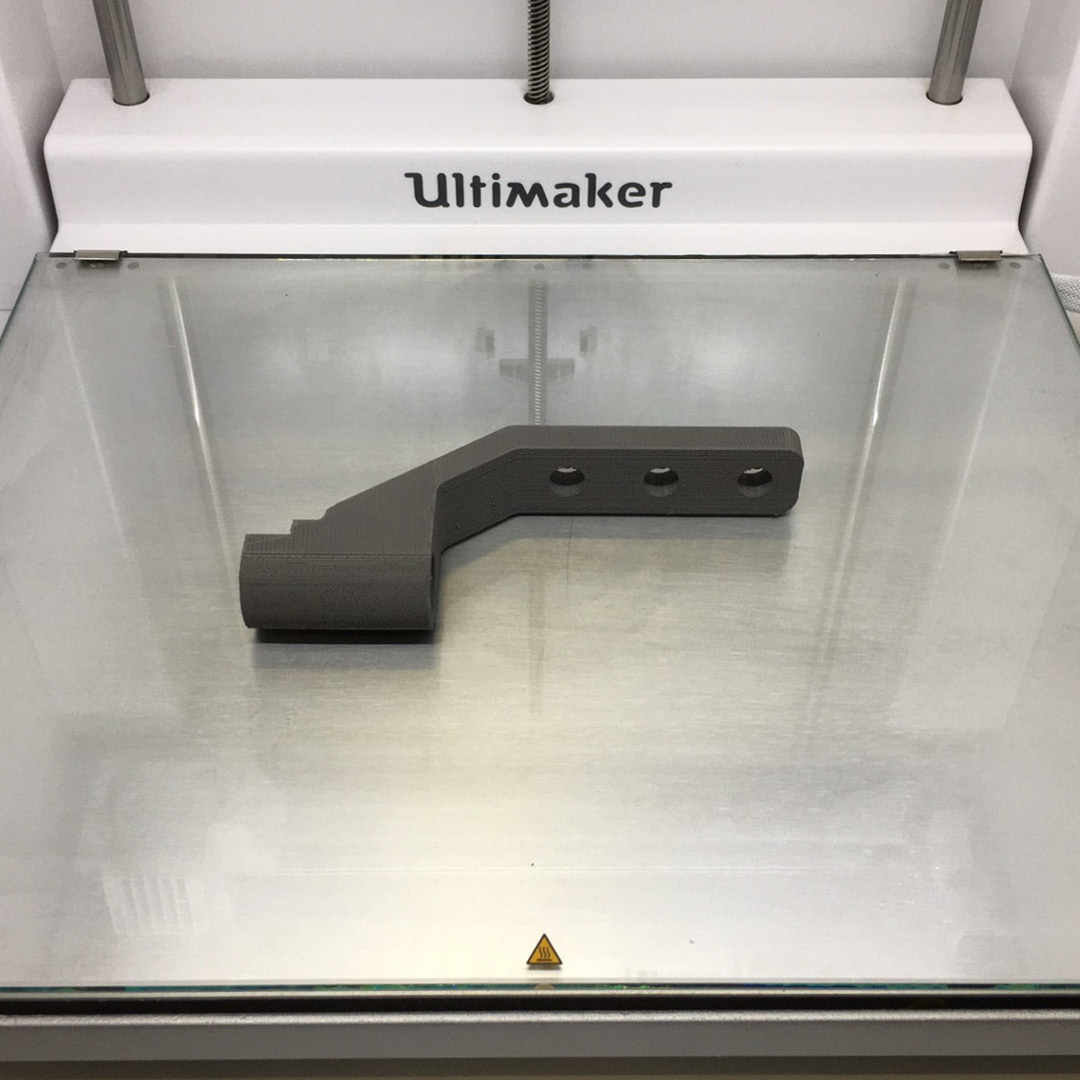
Printing of the part at Liebherr Components
The part will be sintered to get its final properties
Topology optimization process
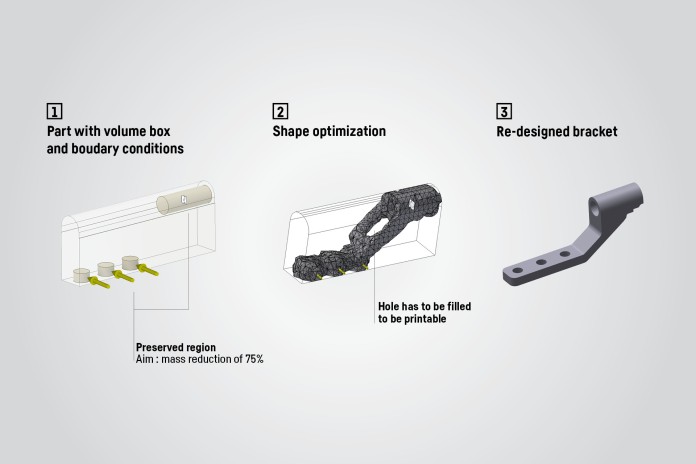
Results… and more?
The results are very satisfying:
- we reduced the mass of original brackets by nearly 60%
- we developed a new design that withstands current load cases (simulation)
- manufactured parts have been mounted on the engine
- we have fully integrated this use case in our supply chain
- our target is to match manufacturing costs of a machined version
We have answered our question: it is possible to use MFFF metal and 3D printing for prototype parts, as it enables on demand production while shortening the supply chain.
However, that is not all, in view of the potential of this technology, we have today redefined a new objective: to fully integrate the component on engine prototypes during endurance tests on test benches.
If you want more information about this subject, please contact Hugues Winkelmuller.