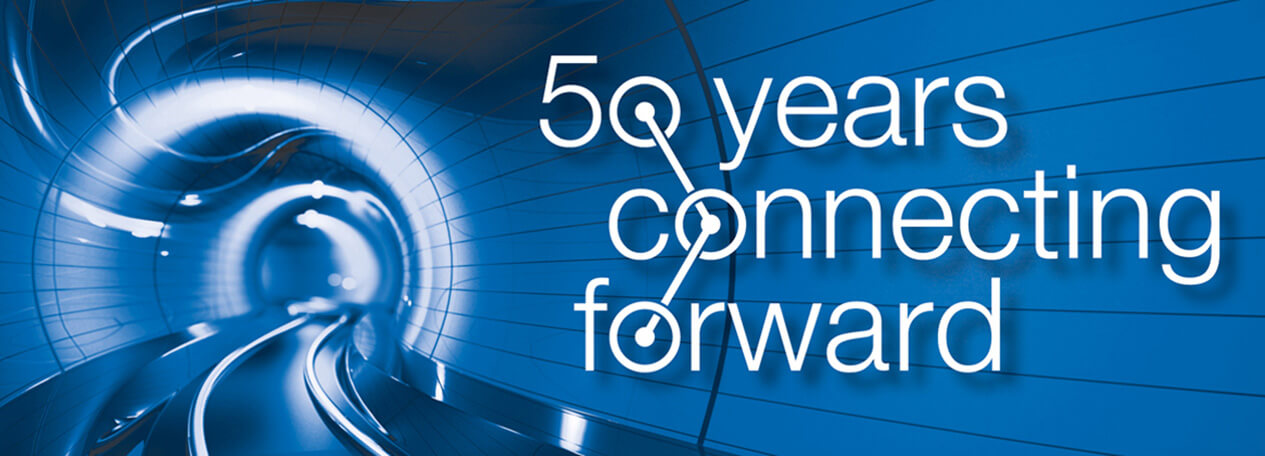
Magazine 2019
Magazine 2019
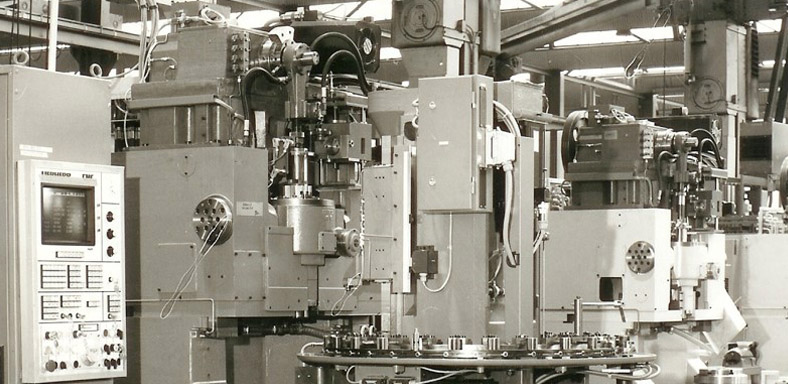
Half a century of Liebherr-Verzahntechnik GmbH means 50 years of commitment to the machinery and plant engineering industry. Gear technology originated in the technology of the revolving tower crane. Hans Liebherr wanted to buy a gear hobbing machine for gear manufacturing, but could not find what he wanted – so he simply built it himself. It’s a typical Liebherr story, since many sectors in the company group have emerged in this or in a similar way. Taking things into one’s own hands: an attitude that can still be found at Liebherr today.
Most read
01
Half a century of Liebherr-Verzahntechnik GmbH means 50 years of commitment to the machinery and plant engineering industry. Gear technology originated in the technology of the revolving tower crane. Hans Liebherr wanted to buy a gear hobbing machine for gear manufacturing, but could not find what he wanted – so he simply built it himself. It’s a typical Liebherr story, since many sectors in the company group have emerged in this or in a similar way. Taking things into one’s own hands: an attitude that can still be found at Liebherr today.
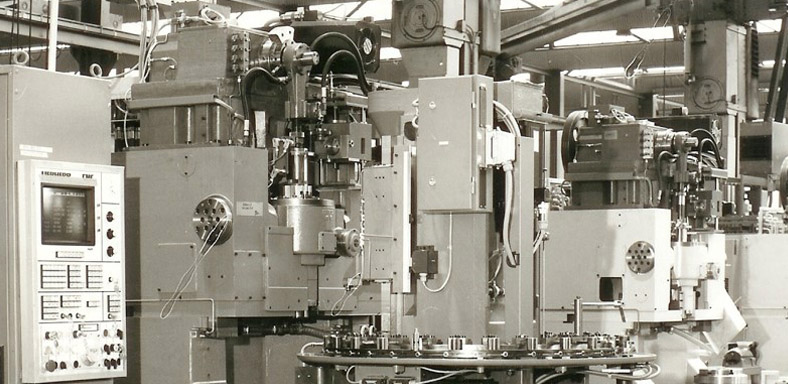
02
Bauer Gear Motor operates two new LC 180 gear hobbing machines at its facility in Slovakia, producing gearing for all facilities. These machines are characterised by their operational versatility, given that they are used to produce around 180 different components in a very wide range of different sizes.
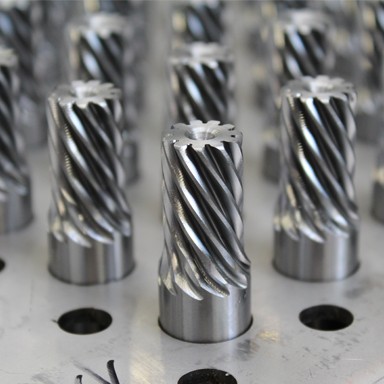
03
“The fire pump is the heart of every fire truck”, explains Michael Schöftner, Head of Mechanical Production at Rosenbauer International AG, the global leader for fire service equipment. The equipment has to withstand enormous loads in cases of operation. Rosenbauer relies on an automation solution for pump manufacturing from Liebherr. The rotary loading system RLS 800 from the Kempten-based automation experts has been deployed in Leonding near Linz for around two years now.
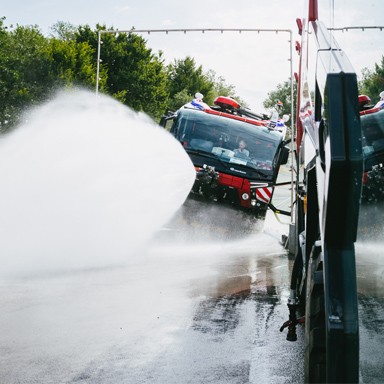
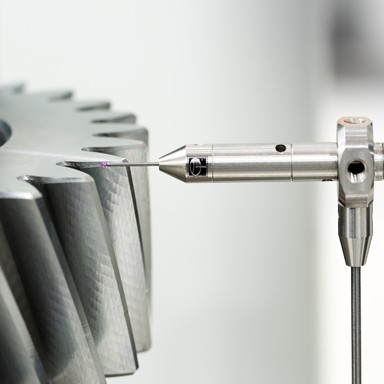
Wenzel GearTec GmbH, a successful manufacturer of gear inspection machines, has been part of Liebherr-Verzahntechnik GmbH since May 2019. The Karlsruhe-based company has specialised in the measurement of gears, gear cutting tools and other rotationally symmetrical workpieces since 2004 and has an innovative product range that perfectly complements Liebherr's own.
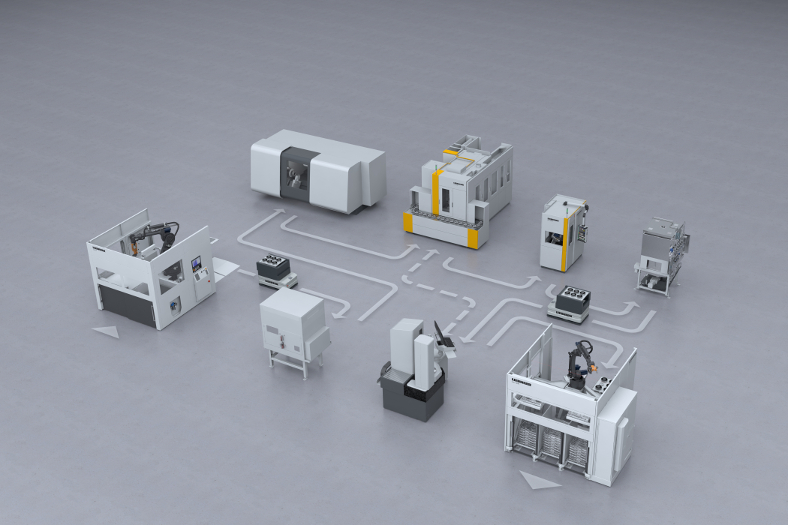
While we still have some way to go to achieve autonomous driving on the road, factories are miles ahead: AGVs (automatic guided vehicles) are already being used in the area of production.
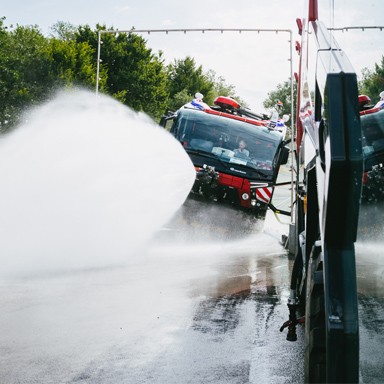
“The fire pump is the heart of every fire truck”, explains Michael Schöftner, Head of Mechanical Production at Rosenbauer International AG, the global leader for fire service equipment. The equipment has to withstand enormous loads in cases of operation. Rosenbauer relies on an automation solution for pump manufacturing from Liebherr. The rotary loading system RLS 800 from the Kempten-based automation experts has been deployed in Leonding near Linz for around two years now.
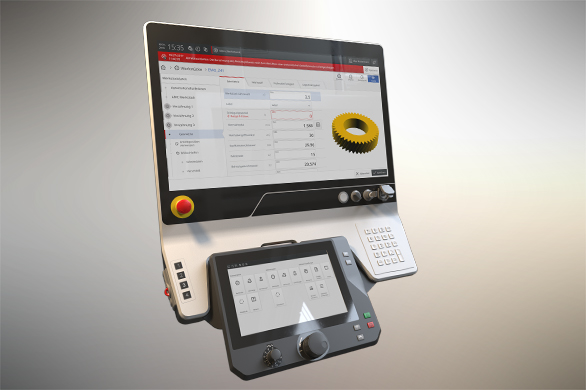
When Peter Pruschek, Head of Electronic and Control System Development at Liebherr-Verzahntechnik GmbH, presents the new LHGearTec control system, he first highlights the striking new features: “We are entering the market with a 24 inch touchscreen monitor – an above-average size for machine tools.
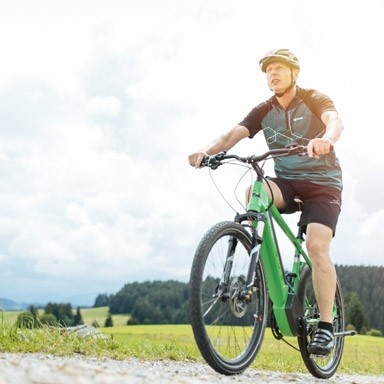
For the mobility of the future, we need solutions today. Sometimes this means starting from scratch. With a new production line, new processes and new machines.
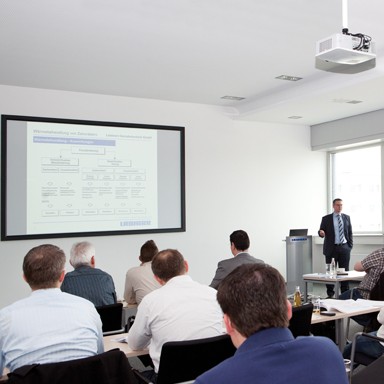
How do you get closer to the customer? For Liebherr the answer is simple: by increasing presence locally.
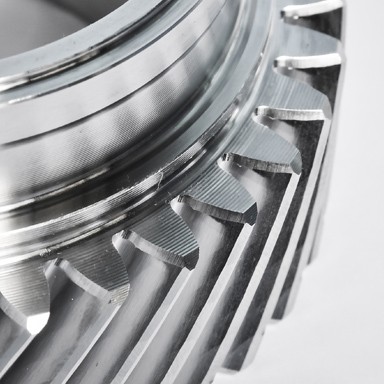
As before, ChamferCut is a technology with a great deal of development potential. A new upgrade is now pushing the limits of the impossible.
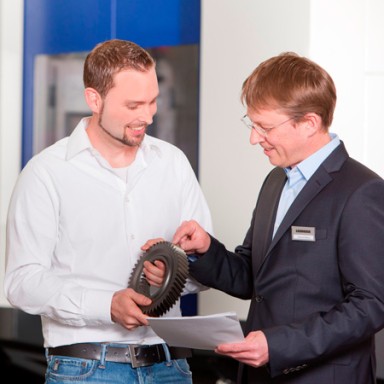
Quality management has a special place at Liebherr, it protects the core of the brand. The following is an overview of the processes necessary for quality assurance provided by Christof Porsche.