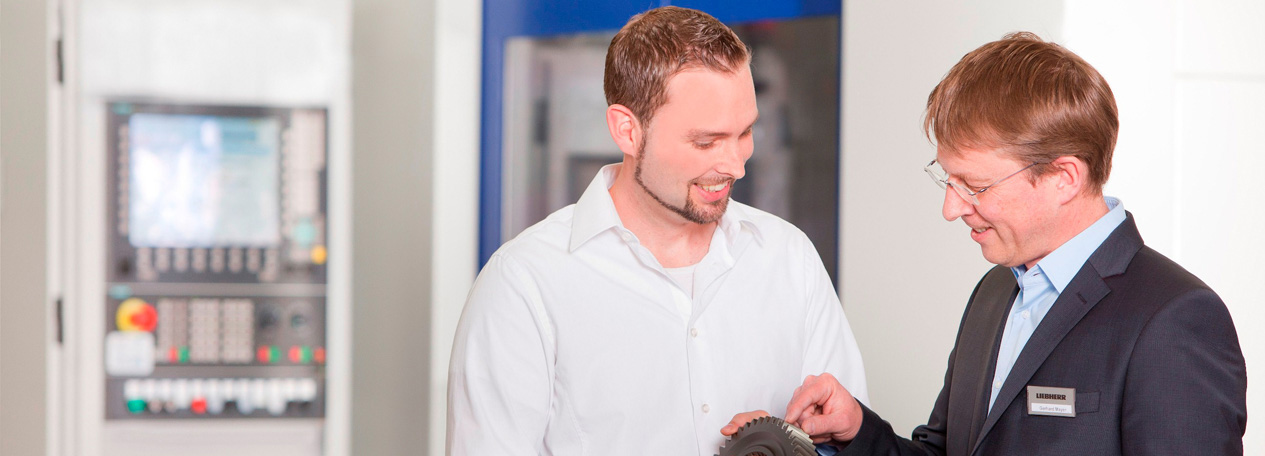
Only the best
Quality management has a special place at Liebherr, it protects the core of the brand. The following is an overview of the processes necessary for quality assurance provided by Christof Porsche.
The proverbial Liebherr quality is not a matter of chance. Christof Porsche is the custodian of this topic on account of him being responsible for quality management (QM), machine approvals, certifications and complaints handling. He has been with Liebherr-Verzahntechnik GmbH for 30 years, holding various posts such as Head of Machine Production and has been Head of the QM Department for seven years.
Focused on fault avoidance
With his team of 30 co-workers, he is responsible for two areas: the products themselves and the processes for their manufacture. “Fault avoidance is always at the forefront for us, checking the quality is just another aspect”, he explains the fundamental concept of his approach. Nevertheless, the inspection of products takes up a large part of the work of his department as no machine gets past his staff: every Liebherr machine, without exception, runs through an approval process orientated in part strictly around the requirements of the customer. “We employ a complete final check during which each machine processes at least one workpiece. Usually, though, a small series of items are produced in which the dimensions of all individual workpieces are evaluated according to statistical criteria in order to safeguard the accuracy of the machine for series production. No product leaves the building unless it has been approved by me.”
Only experienced workers with extensive knowledge are employed in his area. They become involved as early as the development phase of a new machine and accompany the entire process of creation. “We pursue our quality aims consistently up to and beyond the entire production creation process. We have the complete support of the company management when doing this because quality has a very high priority in the corporate values.” To Christof Porsche, ongoing improvement is important because quality, too, is a process. “Checking and if in doubt discarding cannot be our aim. Mistakes need to be noticed and dealt with right from the outset.”
We pursue our quality aims consistently up to and beyond the entire production creation process.

Christof Porsche, Head of the QM Department
Advisors to specialist departments
In the event of complaints, these are also handled by the QM staff. After all, it is especially important to learn from the respective fault: Where did the problem lie? How can it be ruled out in future? Are suppliers affected? Which specialist departments need to be informed? “We consider ourselves to be advisors more than controllers. We become aware of important aspects for design, procurement and production that can improve the processes there significantly.”
Ultimately, the purpose of quality management is always customer satisfaction. Christof Porsche: “The expectations of the quality of Liebherr machines and automation are high. Our aim is not just to meet them but also, where possible, to surpass them.”