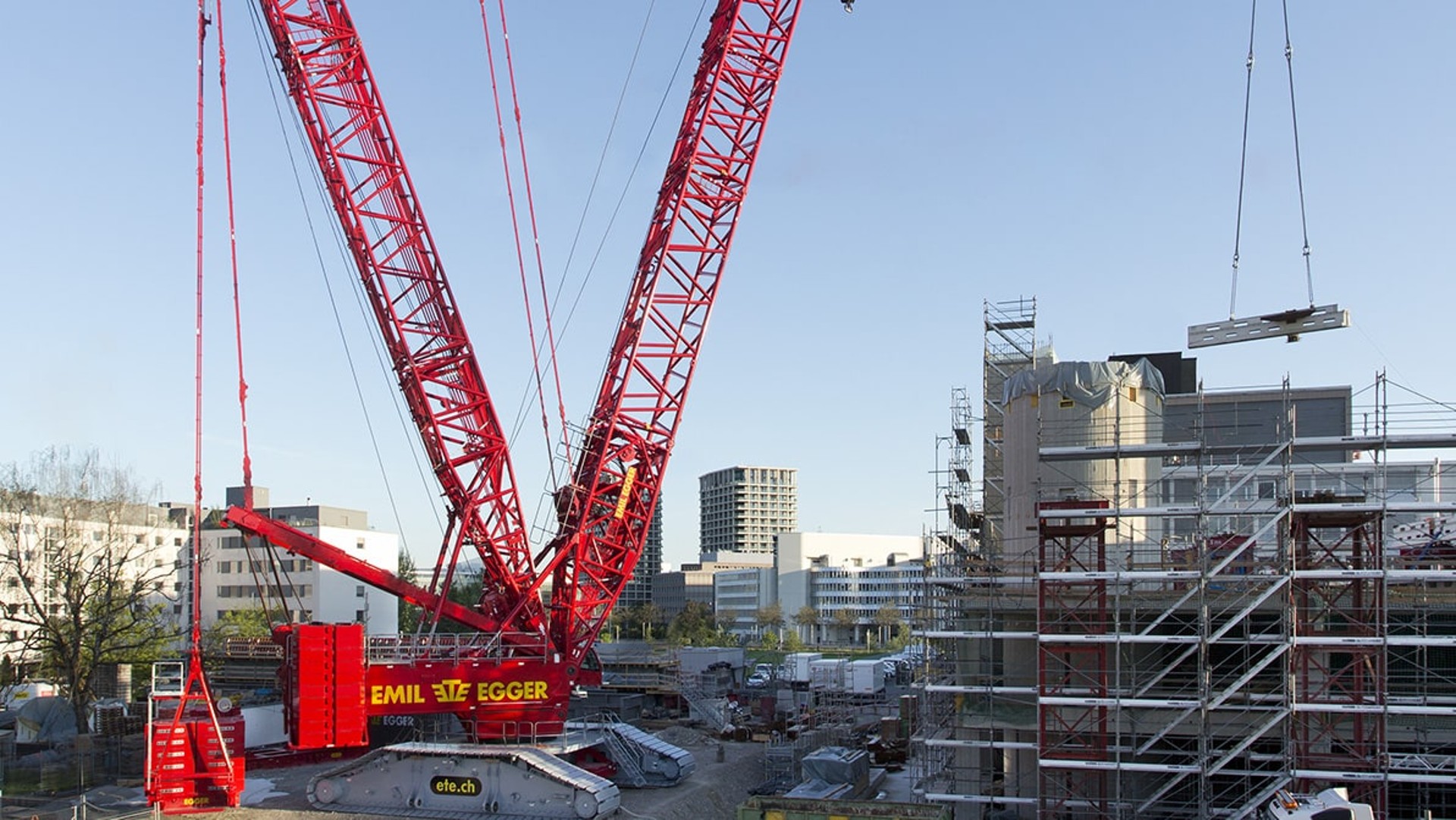
5 minutes | magazine 01/2018
Slow ballast? You've got to be joking
Unbolting rather than unstacking: The innovative VarioTray ballast system enables the central section of the suspended ballast to be simply unbolted. The result is a massive increase in flexibility and significantly less work on site.
See you later, time wasters
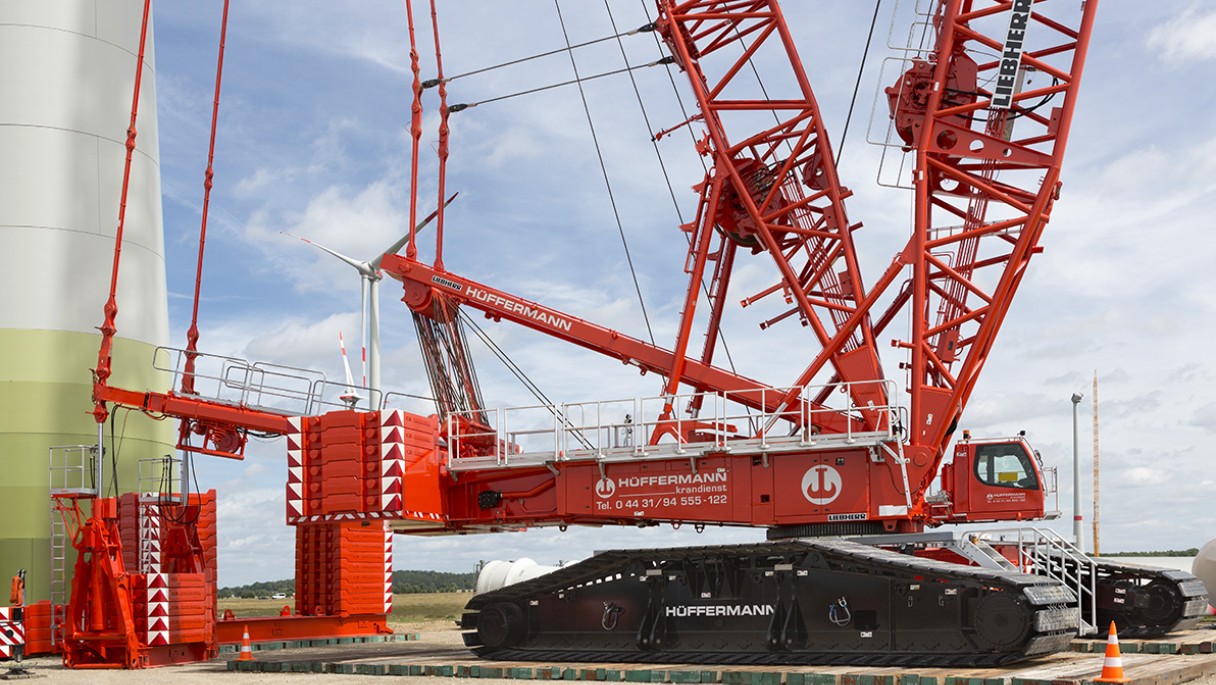
An idea becomes reality, progress is here and the future is now. Everything comes together. Ideas are often whispered to us from the market. We heard "The suspended ballast is too inflexible". An example: A long boom is required to erect wind turbines with heights of 160 metres being far from rare. The boom is assembled on the ground and then raised. Everything stands and falls with the laws of physics: The law of leverage explains why we need a high counterweight to get this long boom into the air.
Once the boom is upright, the suspended ballast sinks to the ground. The crane is fixed in position and cannot be moved. However, that is rather impractical for follow-up hoists. The ballast slabs then have to be unstacked individually until the correct counterweight has been reached. The hoist can take place, the wind turbine in our example can be erected. And then? We restack the ballast slabs so that we can lower the long boom correctly and safely. But all that takes time. And time is money.
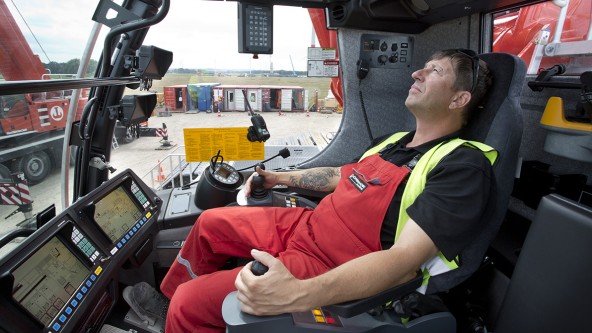
Sven Jacobs, crane driver at Hüffermann
Our solution: VarioTray
We have an elegant solution for these cases. VarioTray. A short name for a smart concept. A smaller ballast pallet is docked on the centre of the large ballast pallet. After the boom has been raised the small pallet is unbolted. The large, heavy part remains in place whilst the smaller part is still suspended on the derrick boom. This makes it easy to work with. And the ballast can be bolted back into place to lower the boom. Hüffermann Krandienst has already tested the system on its LR 1750/2 crawler crane. Crane driver Sven Jakobs says: "Without VarioTray it would definitely have taken us three to four hours longer to erect the wind turbine. What a great idea!"
Only four bolts and a cable plug have to be released to disconnect the ballast pallet. That can be done really quickly.
Off to new shores
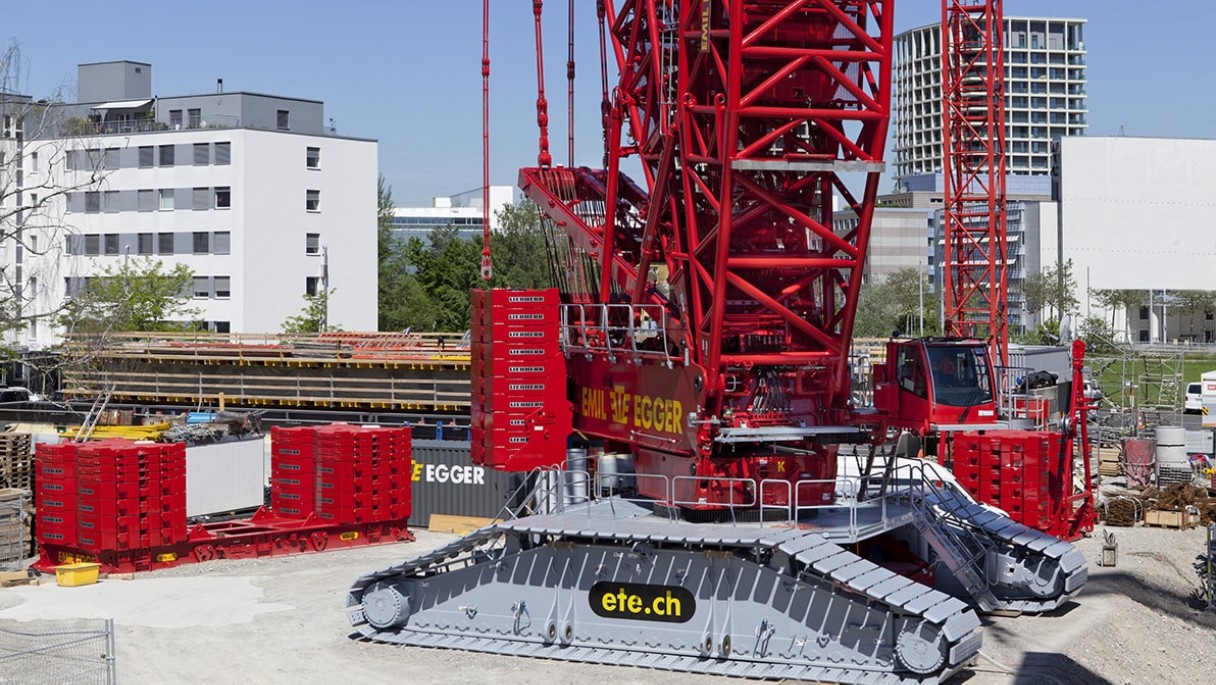
Michael Egger knows all about mobile cranes. He and his brother Markus are the third generation to manage the Swiss company Emil Egger AG, which specialises in cranes and heavy haulage. Until summer 2017, the company's fleet did not feature any crawler cranes at all. And then everything changed. Egger invested – and did so properly. The new LR 11000 is now the most powerful crawler crane in Switzerland. "We are really proud of our new flagship! It is the most modern crane in this class and is incredibly flexible. VarioTray® just adds to that." You can see the enthusiasm on Egger's face as he talks.
And we know that we can rely on Liebherr's great service.
The first job for the new 1000-tonne crane was a large newbuild in Zurich. For six months the crawler crane assembled reinforced concrete girders and heavy façade parts with various weights between 25 and 58 tonnes and radii ranging from very small to very large. VarioTray was absolutely ideal for this job. A set-up crane would have been hard-pressed to find any space on the constricted site. And the alternative of a ballast trailer would have significantly increased the ground pressure – which would have meant making a special concrete slab. Edgar recalls: "VarioTray really paid dividends on this job. We did not have to stack and unstack the individual ballast slabs for the various hoists. That saved us lots of time and lots of money."
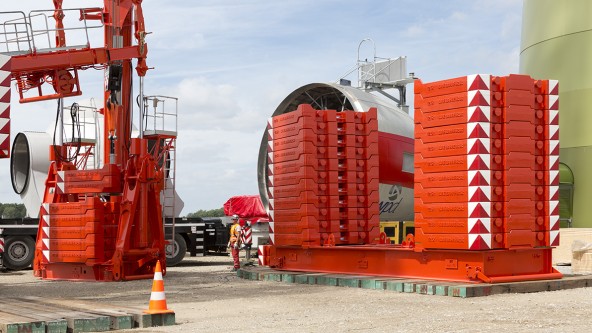
Easy work
The small ballast pallet is simply unbolted. The large part, which is only required to raise and lower the boom, remains on the ground.
This article was published in the UpLoad magazine 01 | 2018.