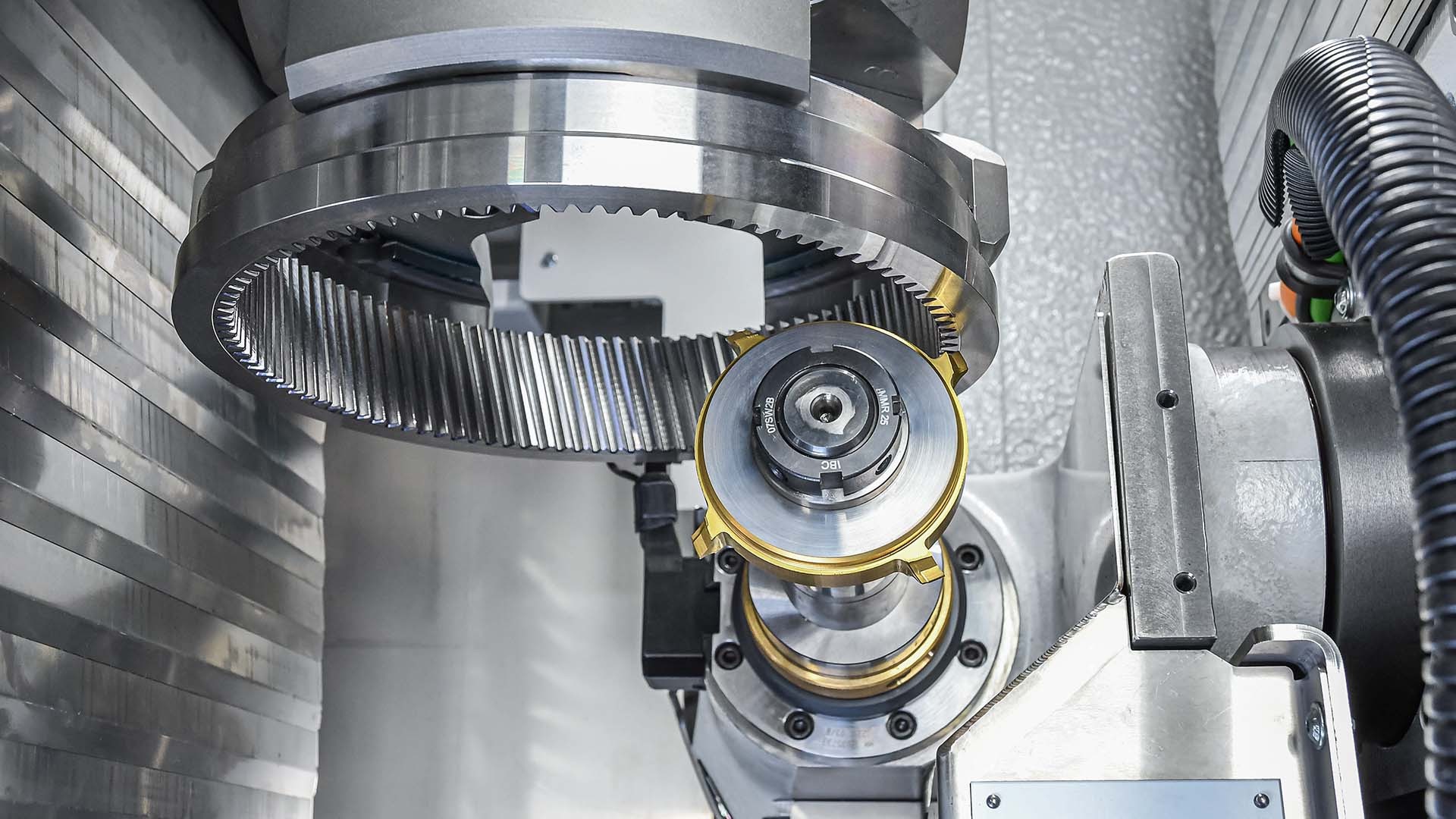
ChamferCut IG: Nothing is impossible
On the new LK 280 DC gear skiving machine from Liebherr-Verzahntechnik GmbH, internal gears can not only be produced efficiently, but also chamfered during the machining process thanks to an integrated ChamferCut device. This opens new opportunities for the industry to manufacture gearboxes with higher power density, giving them a competitive edge in the market for modernized or alternative drive technologies.
New drive designs require gearboxes with greater power densities, and not just for the electromobility sector. Planetary gears are therefore being used more and more frequently, which deliver a higher transmission ratio at a smaller volume. However, the possibilities for chamfering the internal gears required for this have been limited up to now.
“There was a desire in the industry for economical and high-quality chamfering solutions for internal gears. But up until now these seemed almost impossible to put into practical use,” says Dr. Oliver Winkel, Head of Application Technology at Liebherr-Verzahntechnik GmbH, describing the situation at the get-go. Now the company has become the first to present a machine which does exactly that: by making use of an exciting new cutting method to make a defined, exact chamfer on an internal gear – and to do just that during the machining process and with high precision to boot. In this way, previously formed burrs are removed and, at the same time, the leading edges are broken, which creates the best conditions for assembly, application behavior or any subsequent hard gear finishing.
Modular machine design with pick-up spindle
This is made possible by Liebherr’s modular machine design, which allows the ChamferCut device to be integrated into the machine. The chamfering device is at a right angle to the main machining and is fed by a ringloader. For the particular requirements of chamfering internal gears, Liebherr has developed a new type of pick-up spindle that lifts the workpiece and thus makes the burred underside of the internal gears accessible for the ChamferCut tool. “That’s where our strength lies; in developing innovative solutions and new machine designs for new component requirements. The know-how was there, and the first customer inquiry got the ball rolling. We were offered the opportunity to make a machine just for this purpose,” explains Winkel. The gear skiving machine with integrated chamfering device is already in use at a well-known gear manufacturer.
Tried and true ChamferCut tools from LMT Fette
“The tool manufacturer LMT Fette, which exclusively supplies us with ChamferCut tools, had the tools for chamfering internal gears (ChamferCut IG: Internal Gear) in its product range. We then developed and built the machine for this, so to speak,” Winkel continues. “The customer approached us because they had good experience with our gear skiving tools in the past and trusted us to provide the solution for the new requirements.” Another new feature of the machine was that it also allows clean and environmentally friendly dry machining during gear skiving and chamfering. With this, Liebherr offers a machine for economical and series production of internal gears with a defined chamfer.
With our machine design, we have succeeded in developing an innovative solution for the component requirements of current and future planetary gears.
Versatile: One machine, two technologies
But the machine is also suitable for changing between large and small batch sizes with a higher part variance. The changeover to the FlexChamfer process, in which the chamfer is generated by CNC-control with standard shank cutters, is easily realized with a simple switchover of the control system and opens up the greatest possible versatility in the application. “You only have to retool the machining head and switch between software programs. So you practically get one machine with two technologies and can produce large series, but also prototypes and small series economically and efficiently,” states Martin Schwarzmann, Product Manager for Gear Technology.
ChamferCut IG as a stand-alone solution
ChamferCut technology for chamfering internal gears can also be integrated into existing production processes as a stand-alone solution. The chamfer machines in the LD series are designed for either dry or wet machining and can be combined with various automation options. Winkel sums up, “With our machine design, we have succeeded in developing an innovative solution for the component requirements of current and future planetary gears.”