Maximum flexibility
- Larger work area
- NC counter column for long shafts
- Extended application possibilities of the cutter head
- FlexChamfer: the most flexible chamfering solution on the market
Maximized productivity
- Fast axis movements thanks to optimized drive design
- Powerful hob head for use with the latest tools and technologies
- Shortest set-up times thanks to Liebherr's clamping fixture quick change
Improved ergonomics
- Fold-out steps for easy access
- Optimum accessibility for maintenance work
- Ergonomic machine operation thanks to LHStation and LHMobile
Machine concept
Liebherr gear hobbing machines are optimally customized to the requirements of universal usability. Our high-performance gear hobbing machines are productive and machine in the highest quality.
- Gear hobbing head for larger and longer tools delivers greater productivity and flexibility
- Chamfering of workpieces of up to 500mm workpiece diameter during the machining process and a module of 7mm with ChamferCut and/or the new FlexChamfer technology
- Maximum flexibility thanks to larger work area
- Counter column with NC technology for maximum ease of setup
- Internal ringloader automation concept for workpieces up to 100kg
- Operating concept with LHStation & LHMobile and LHGearTec
- Improved chip removal thanks to optimized and redesigned machine bed
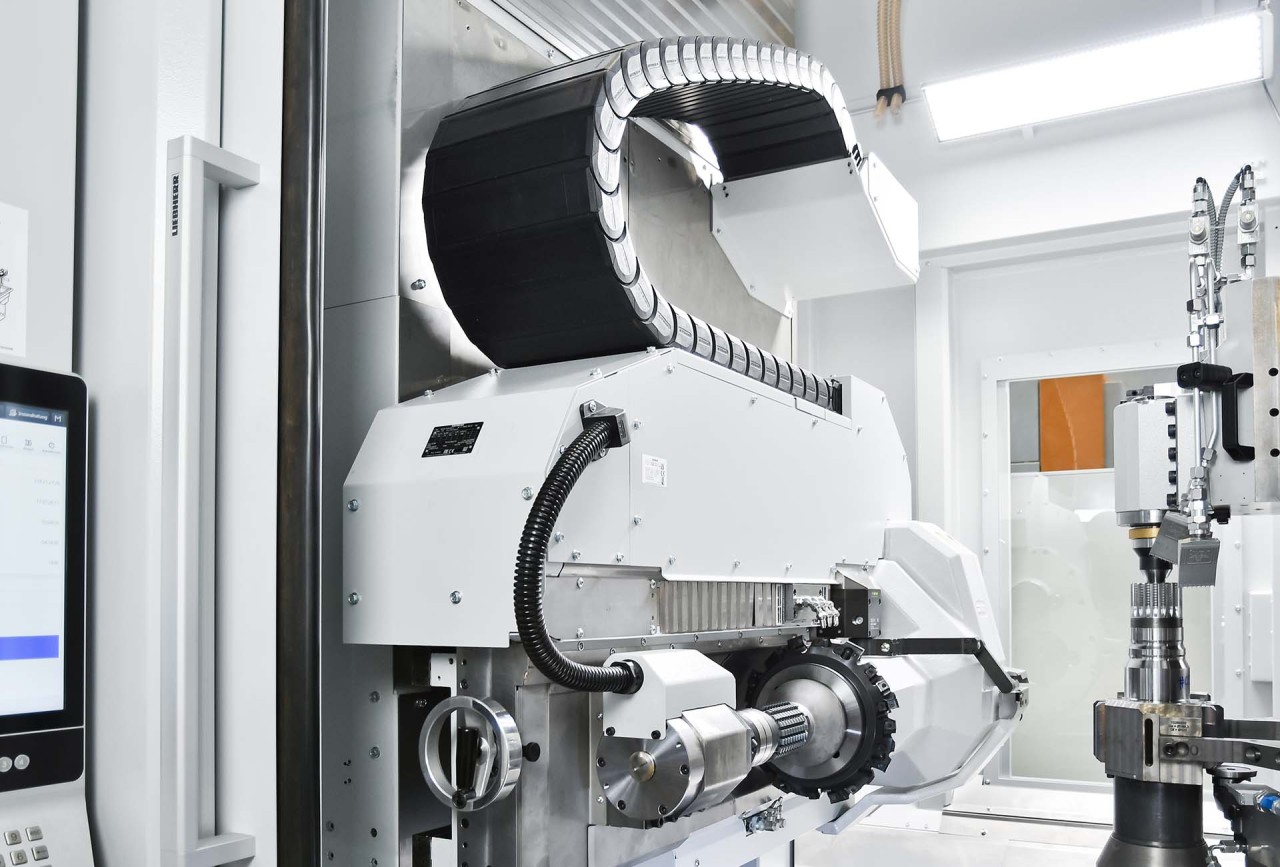
Powerful and uncompromising
The powerful HH 240 hob head enables workpieces up to a module of 12 mm to be machined. With different gear rations, up to 3000 RPM are possible. Due to the large travel range of the counter bearing, very long or, if necessary, relatively short tools can be used. As standard, even hobs with a maximum diameter of 240 mm can now be accommodated.
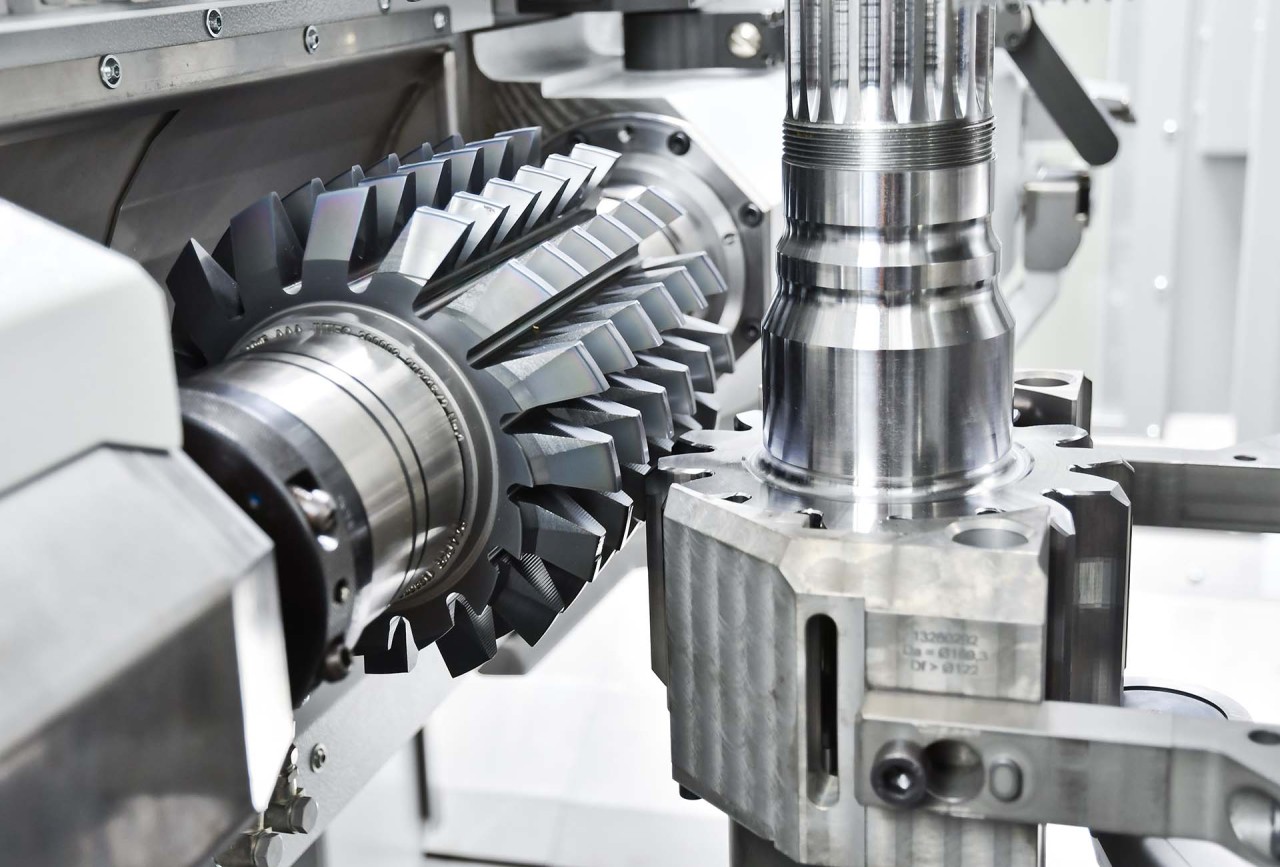
The hob head with a range-change gearbox is exceptionally well suited for particularly high torque requirements. Using different gear ratios, the optimum configuration for your requirements can be found.
Drive power (kw): 27
Max. module (mm): 12 / 12 / 9 / 3.5
Speed (rpm): 600 / 900 / 1500 / 3000
Gear ratios: 12 / 8 / 5 / 2,5
Optionally, the hob head can be equipped with a meshing/positioning device or a swiveling probe for gear check.
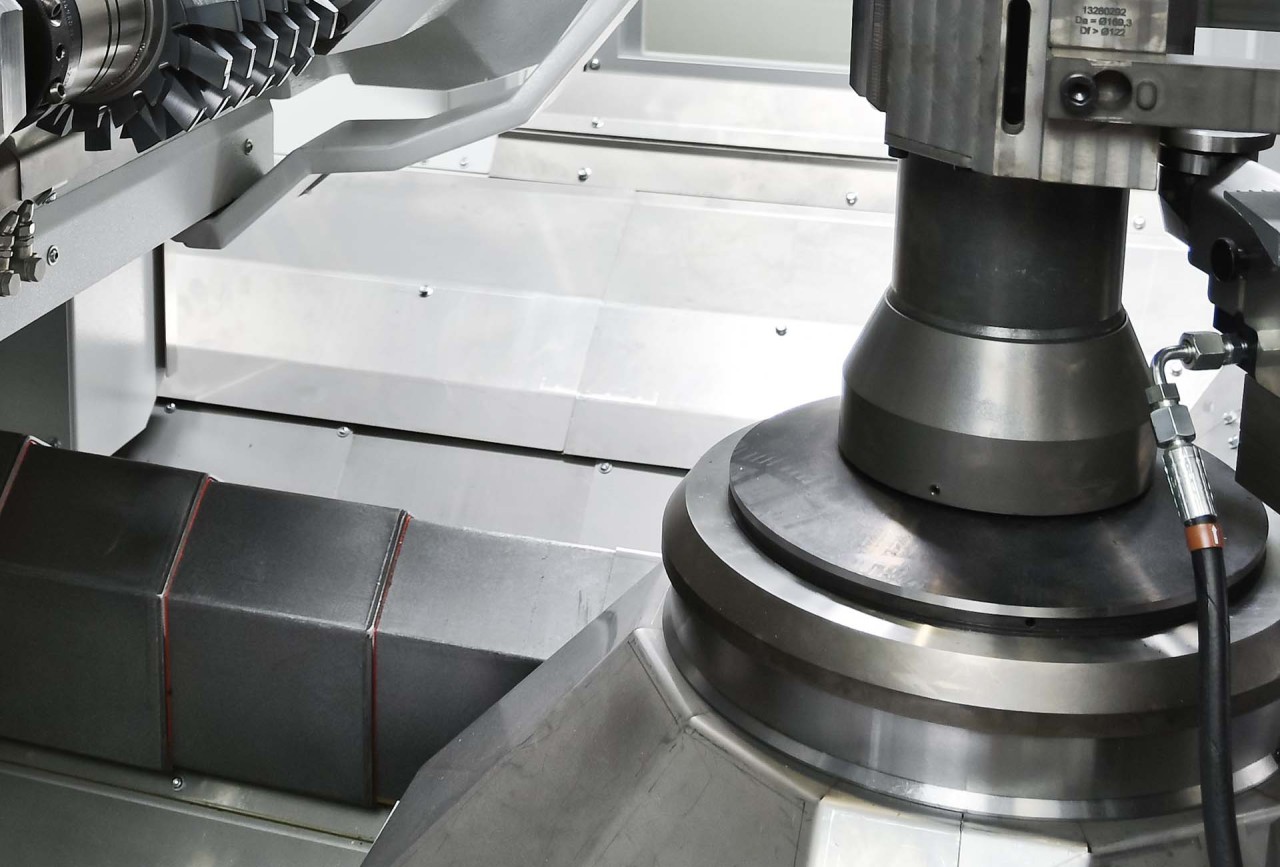
Machine table
For gear manufacturing, a workpiece drive with absolutely zero backlash is required. A table drive with preloaded zero-backlash spur gears and high torque is available for a broad range of applications. For high performance cutting (HPC), a highly-dynamic direct drive is available that fulfills all speed and precision requirements.
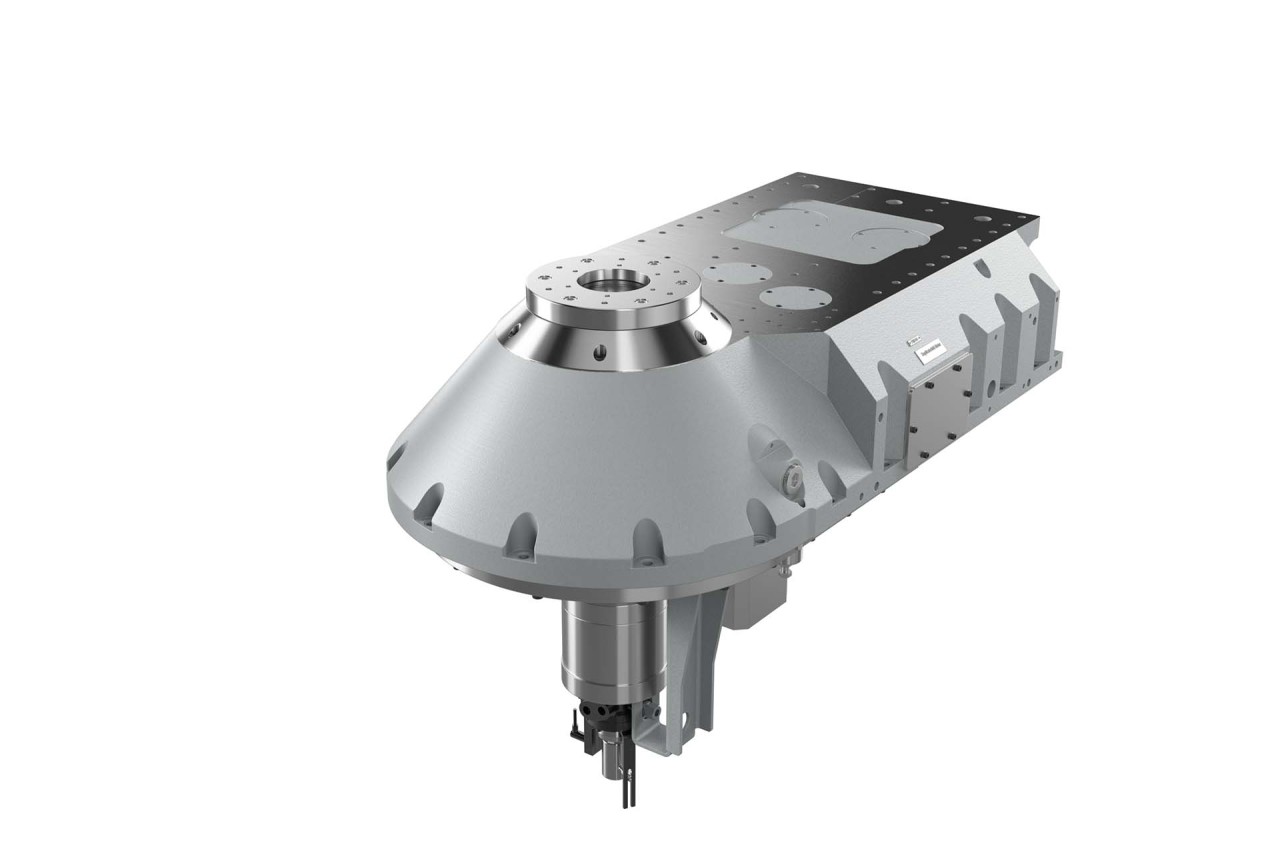
T 100 / T 170
Speed (rpm): 100 / 170
Max. table load (kN): 18
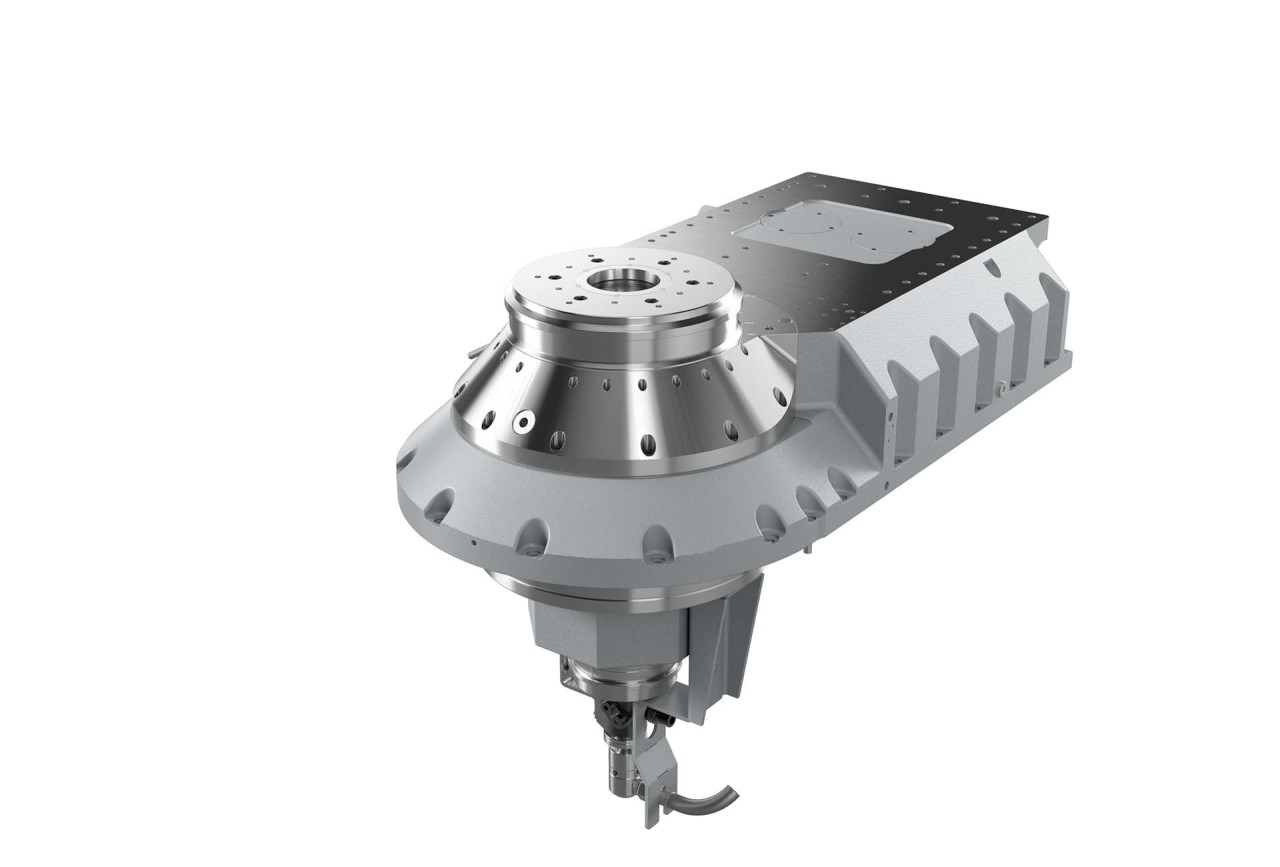
T 400 D
Speed (rpm): 400
Max. table load (kN): 16.5
Drive power (kW): 21.8
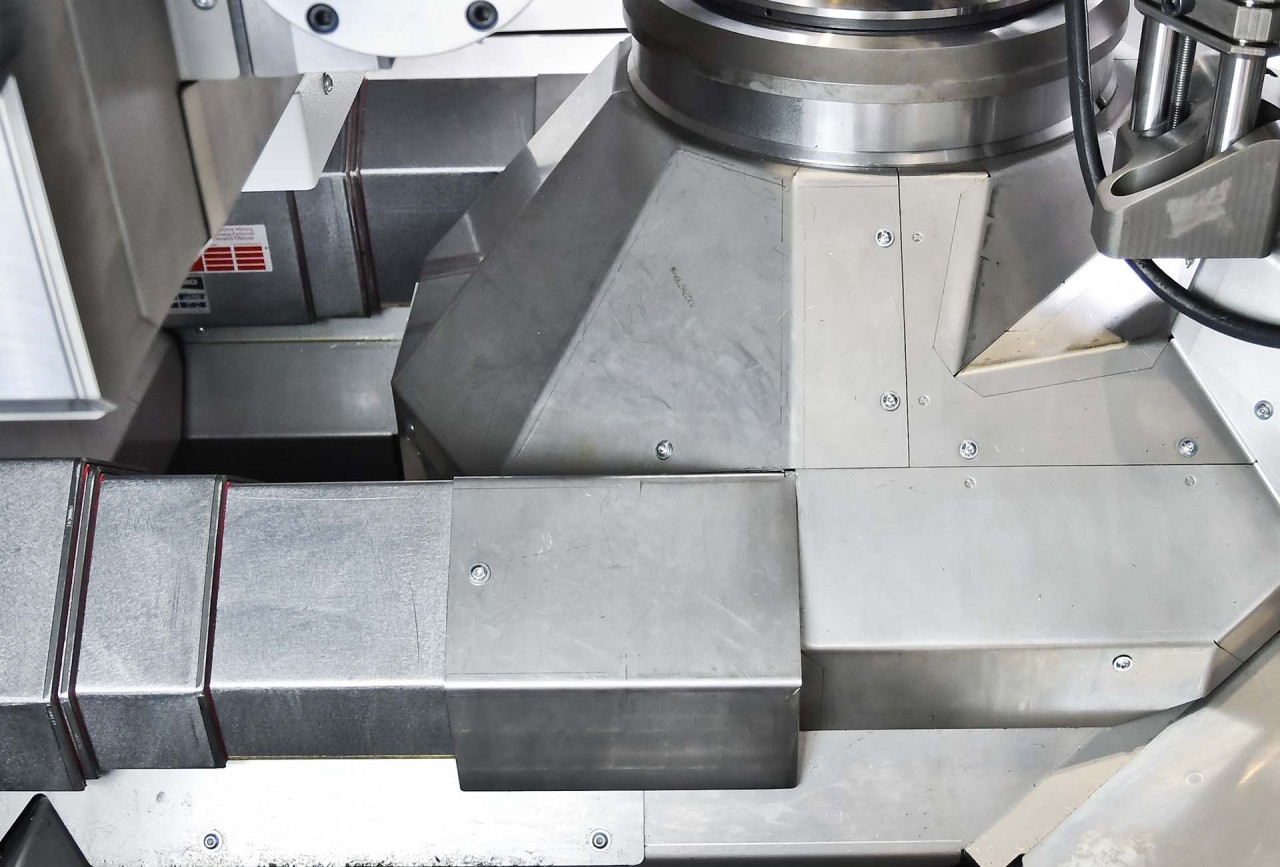
Dry machining in perfection
Special attention was paid to perfected dry machining during the development of the new machine generation. Thanks to the design-optimized machine bed, chips can be removed even better. In addition, essential components such as the machine table, the machine bed, the machine column and the flat guides have been covered with stainless steel covers so hot chips have no influence on the temperature behavior. This guarantees constant temperature behavior and has a significant effect on gear quality and process stability.
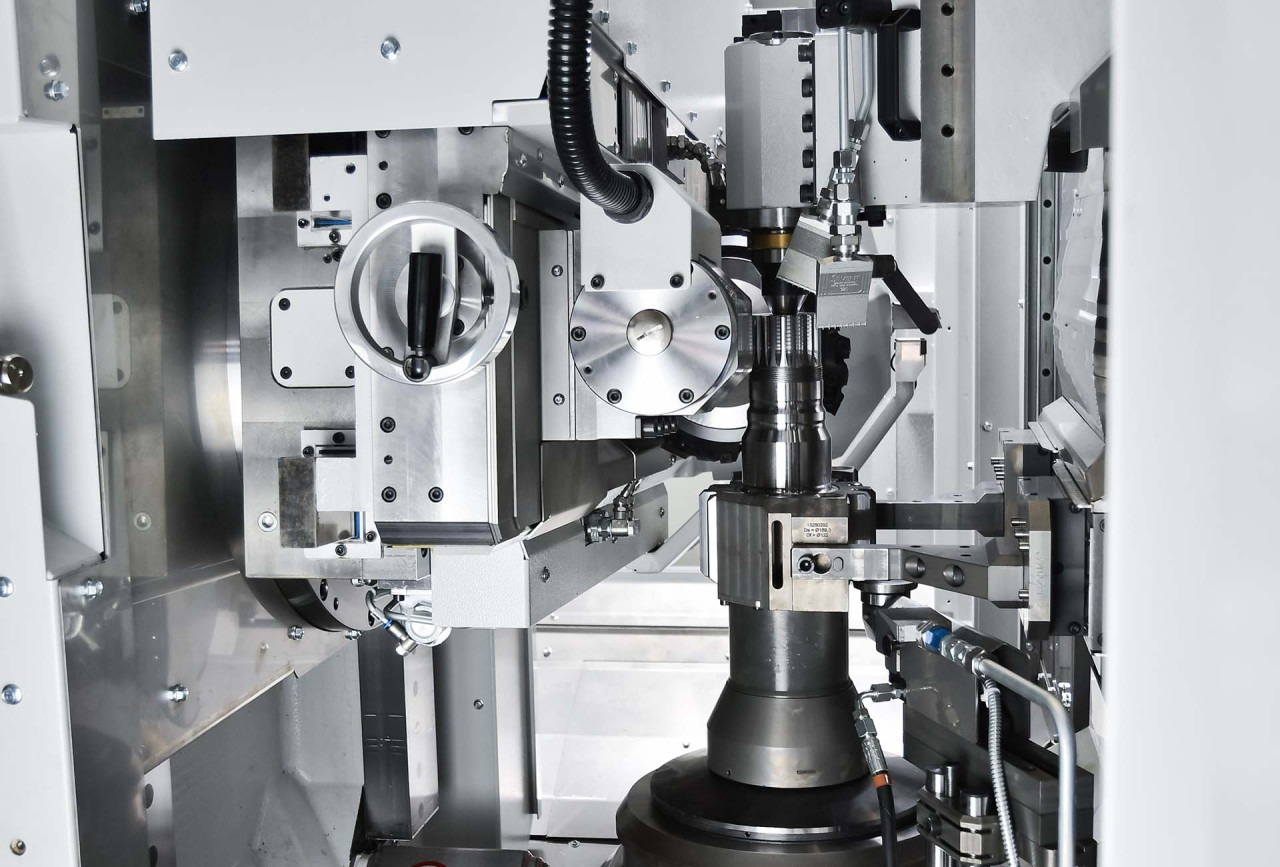
NC counter column and ringloader automation
The CNC-controlled counter column reduces setup time and ensures quick and easy settings via the HMI. Counter column travel of 750 mm for extremely long shafts and high clamping force of up to 13 kN. As standard, the machine is equipped with collision monitoring for downward movement.
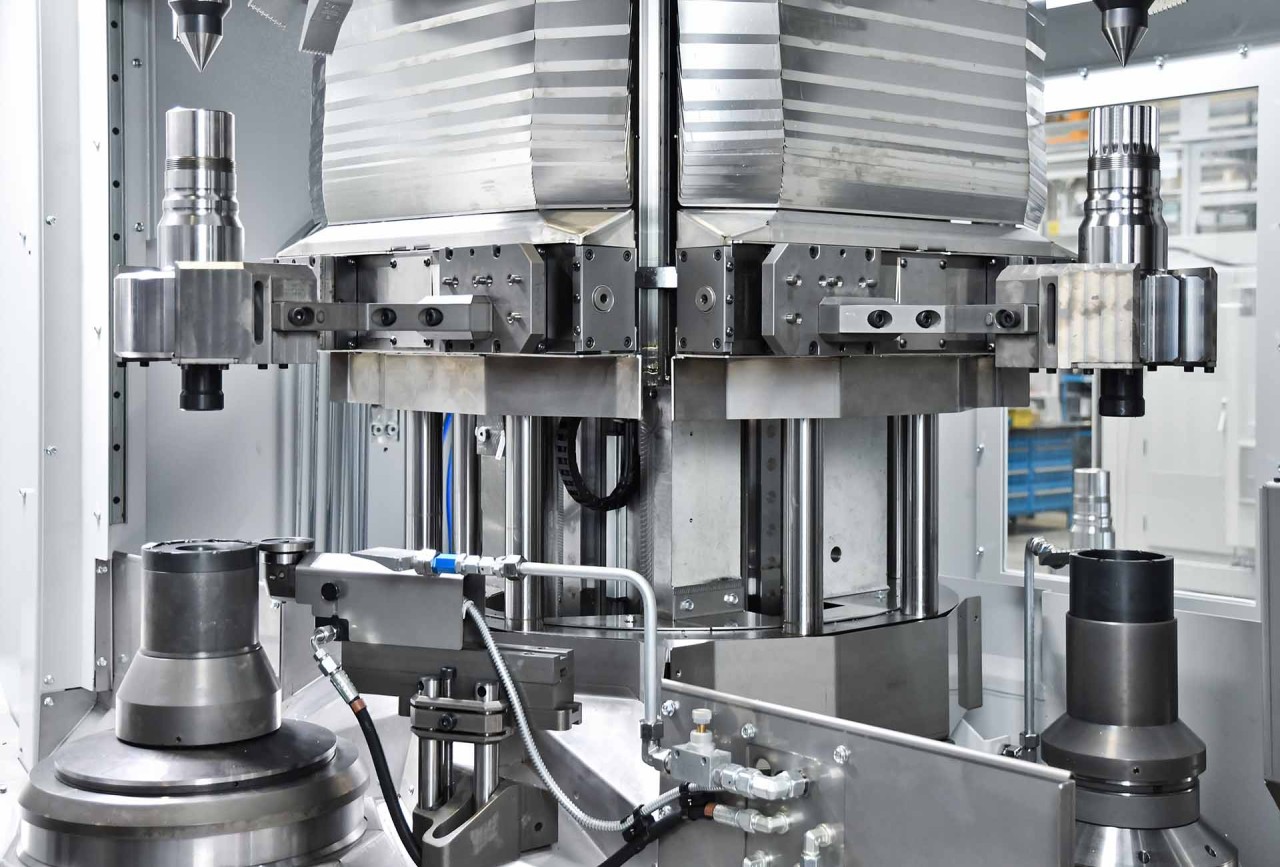
Internal workpiece automation with ringloader
The ringloader can automatically load workpieces up to a max. workpiece weight of 100 kg.
Swivel-type grippers or parallel grippers are available. Both systems can be combined with a quick-change system.
Maximized operator friendliness
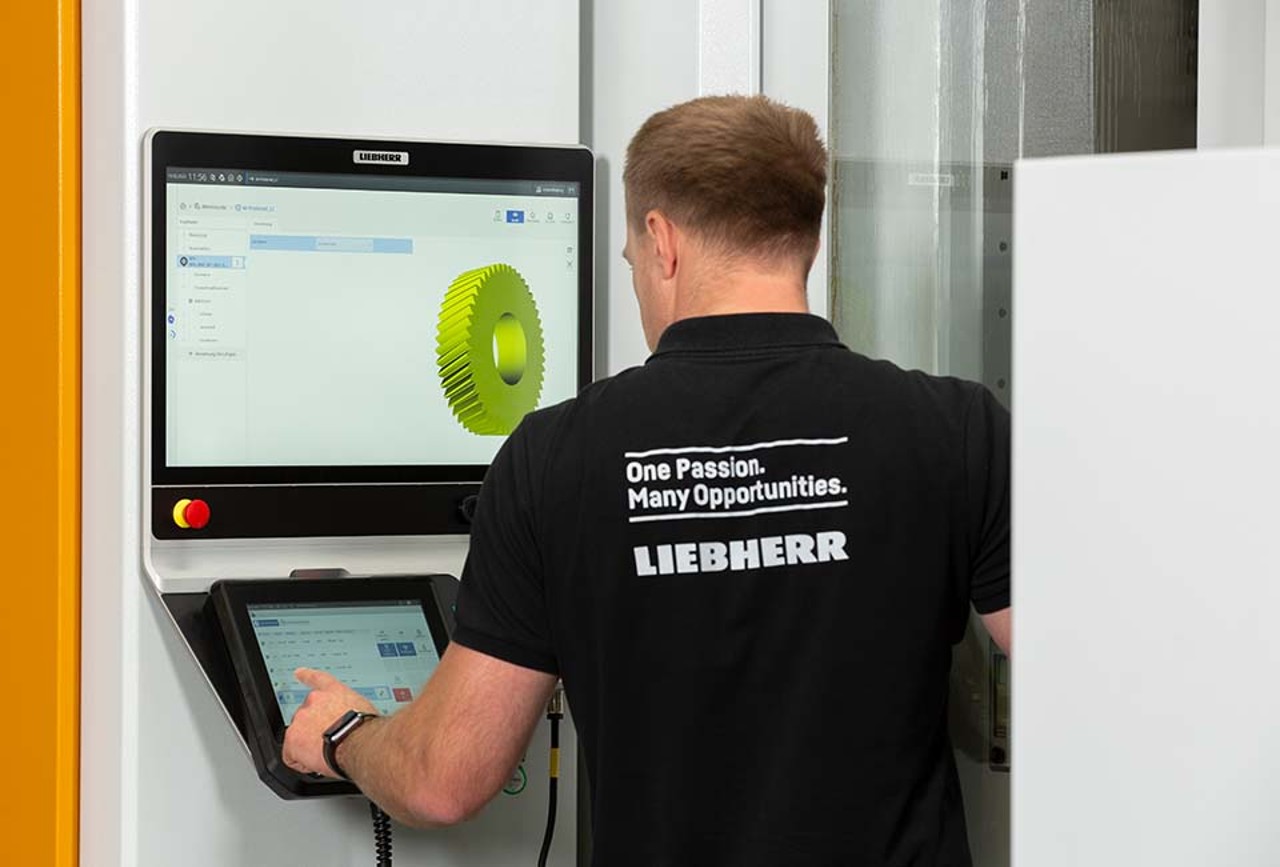
The new optimized control panel, LHStation & LHMobile
With the control panel, Liebherr is intelligently dividing the programming and operation of the machine between two system parts: The large, fixed monitor unit LHStation for data input and process monitoring and the standardized, mobile handheld terminal LHMobile with context-sensitive user guidance during set-up. Both units have a multi-touch surface as well as tactile elements for optimum operating speed and operating safety.
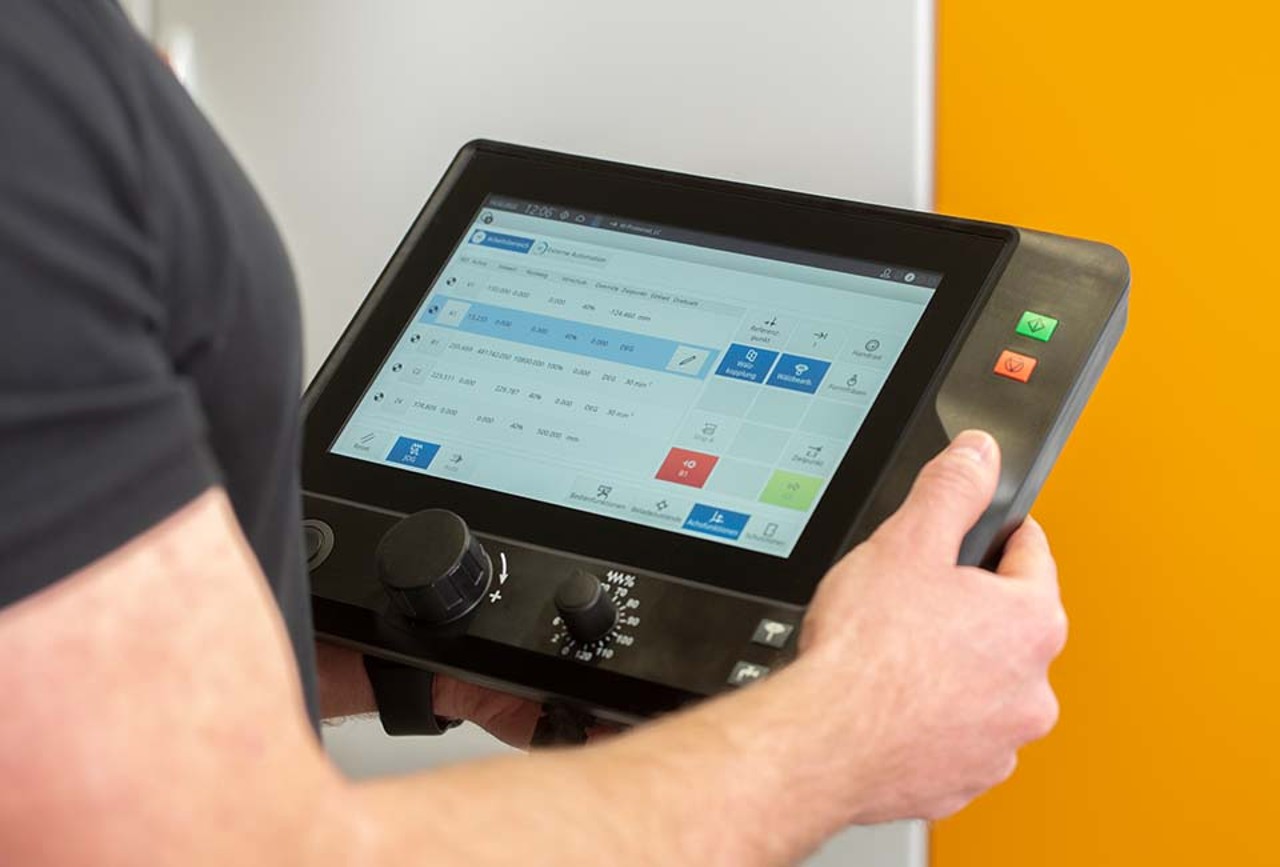
Mobile handheld unit LHMobile
- 10-inch multi-touch as standard
- Context-sensitive views such as PLC/NC keys and program statuses
- Wired signal transmission for maximum safety
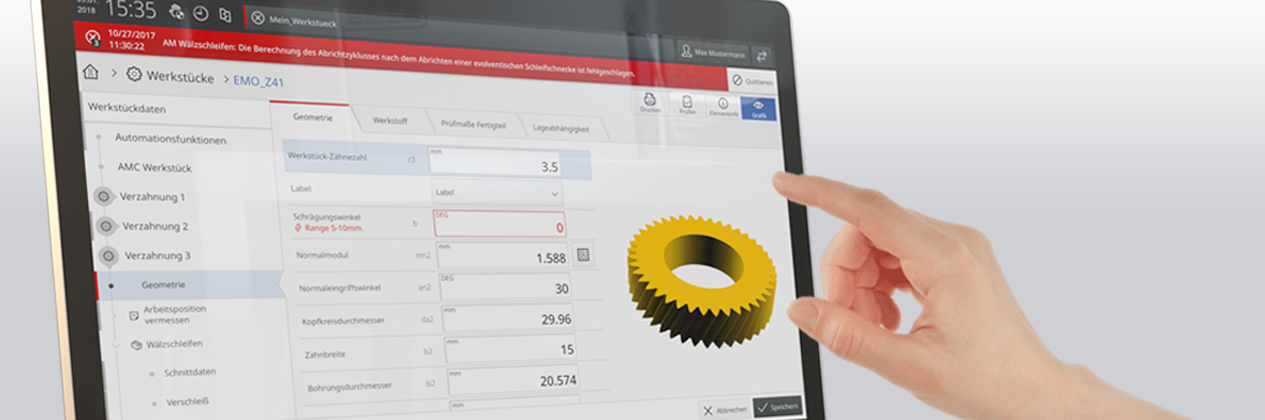
The programming system by Liebherr: 25% faster set-up time
With the LHGearTec software, the system constantly guides users when entering workpiece and tool data, as well as during workpiece correction and process monitoring. The user guidance was redefined in intensive cooperation with designers and users.
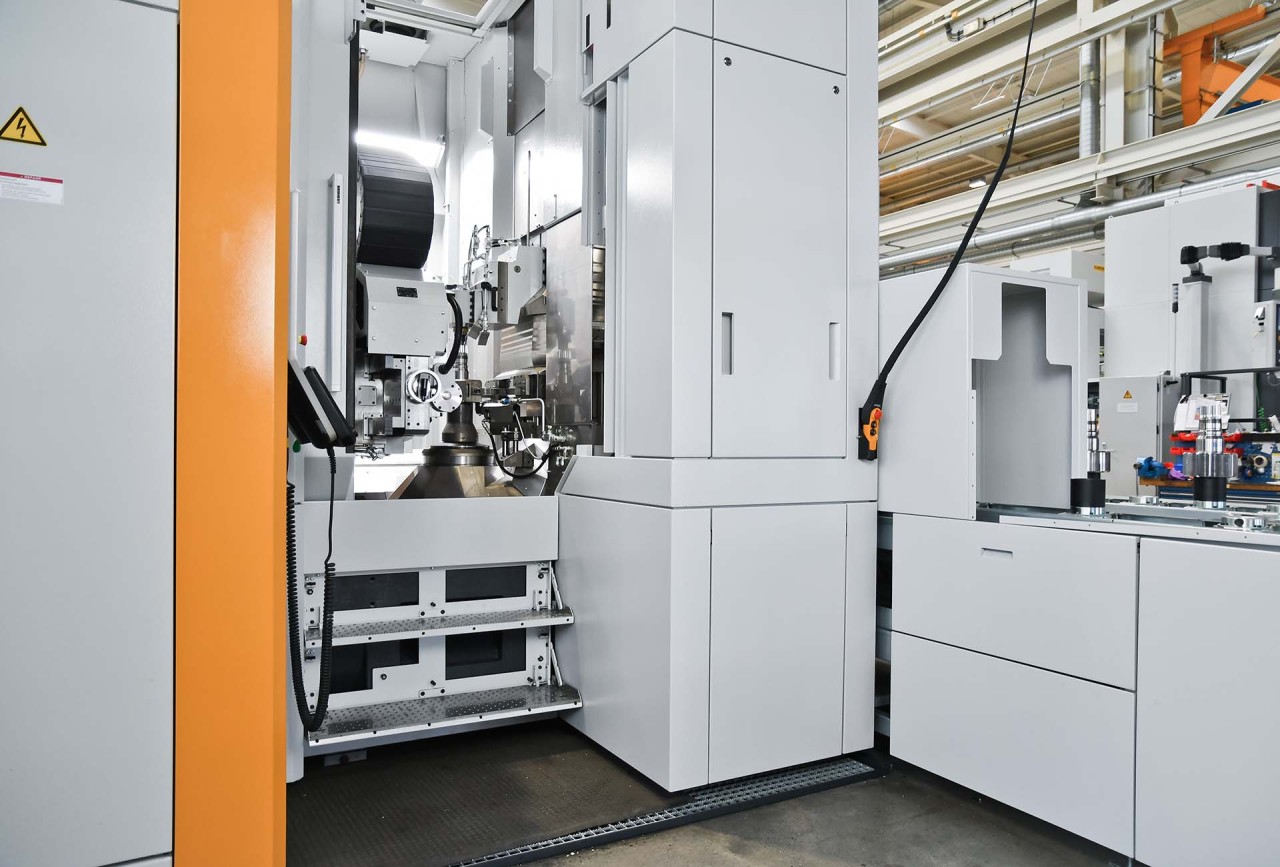
Unrestricted accessibility for setup to both machining processes is also part of the numerous further developments. In addition, there are ergonomic fold-out steps as standard, which further improve accessibility.
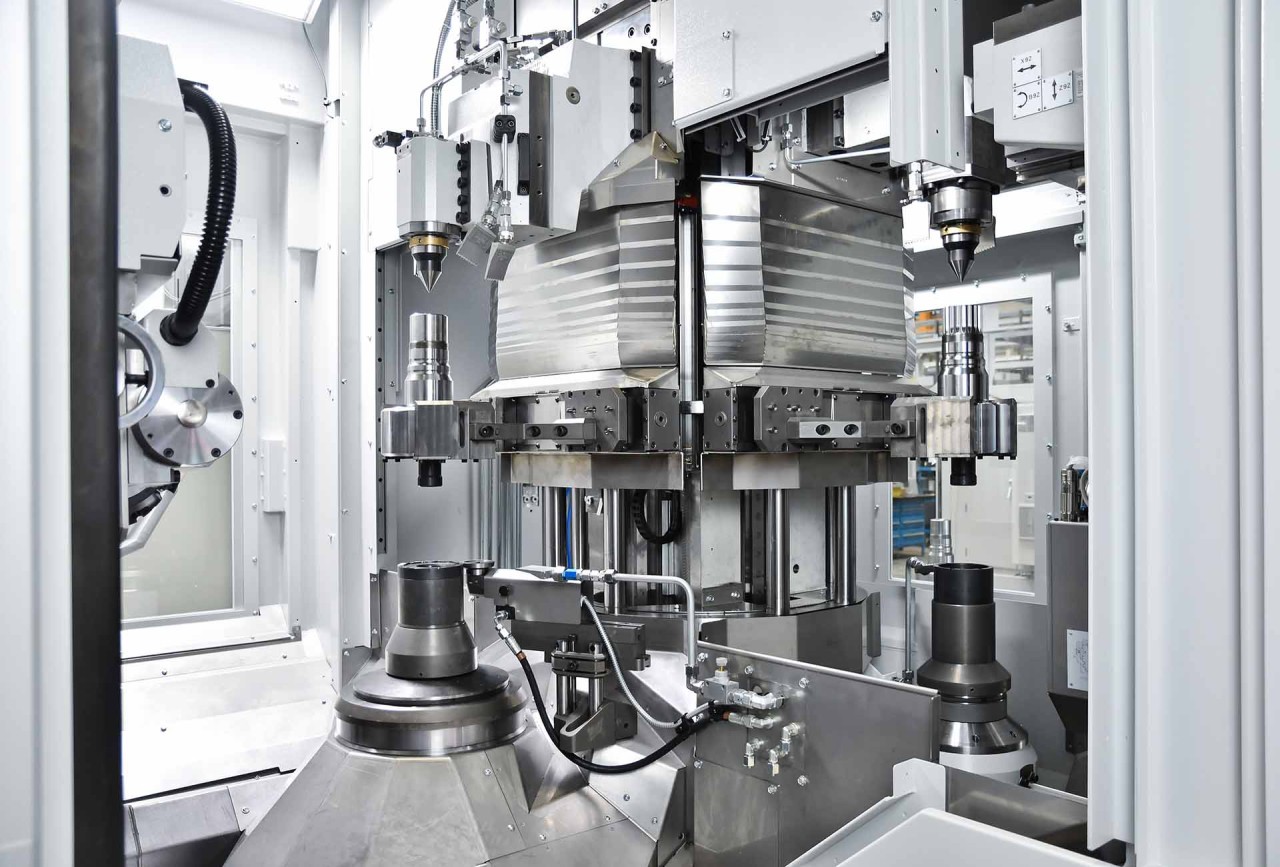
Unrestricted accessibility for setup to both machining processes is also part of the numerous further developments. In addition, there are ergonomic fold-out steps as standard, which further improve accessibility.
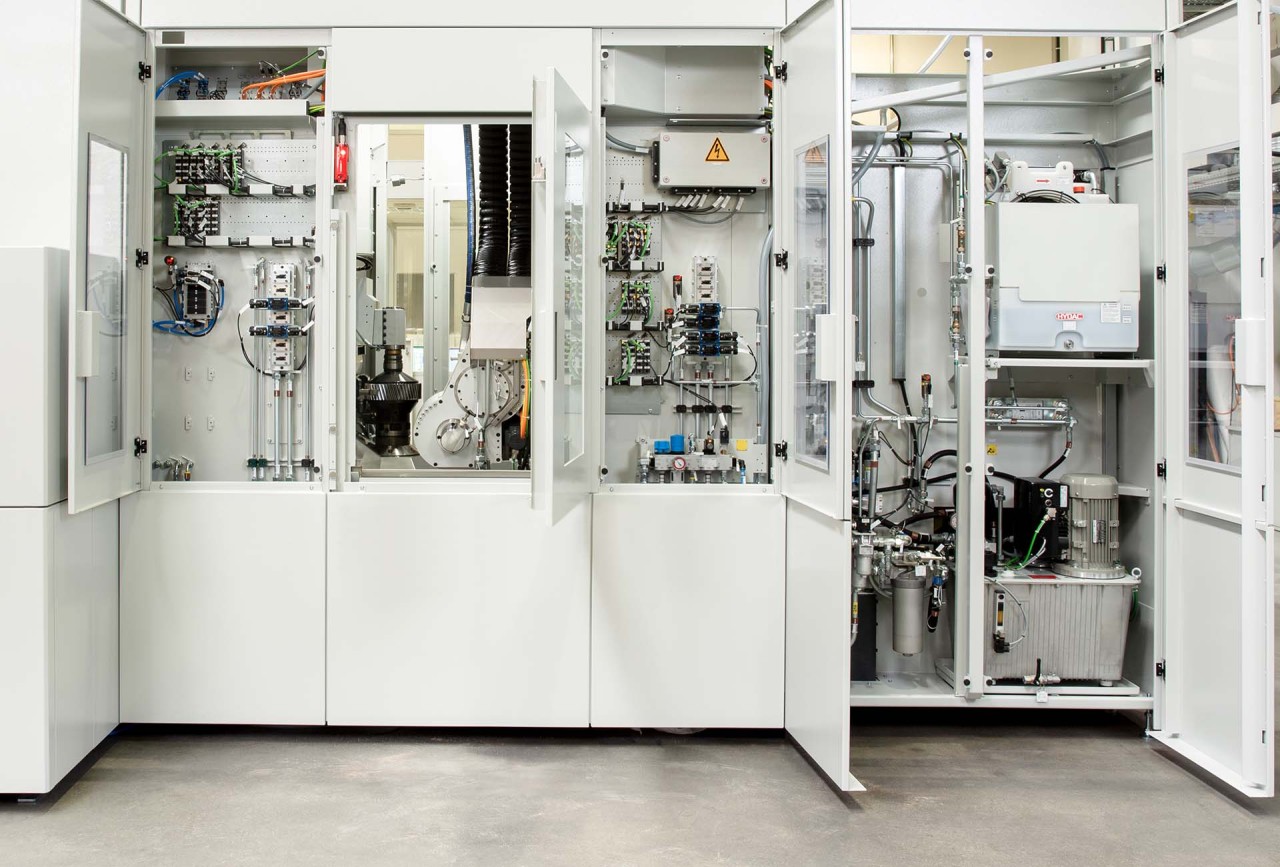
Easy to maintain
Optimum machine accessibility during maintenance work is a prerequisite for ensuring productivity. For this purpose, all necessary maintenance access points are equipped with doors. Moreover, to enable quick and easy additional monitoring of specific statuses, window panes are inserted into the maintenance doors. This means the machine operator or maintenance personnel can read the signals from outside in very little time. An enclosure for the hydraulics has also been integrated into the new machine design. This ensures sustainable reductions to hydraulic power unit noise.
Gear cutting and chamfering parallel to machining
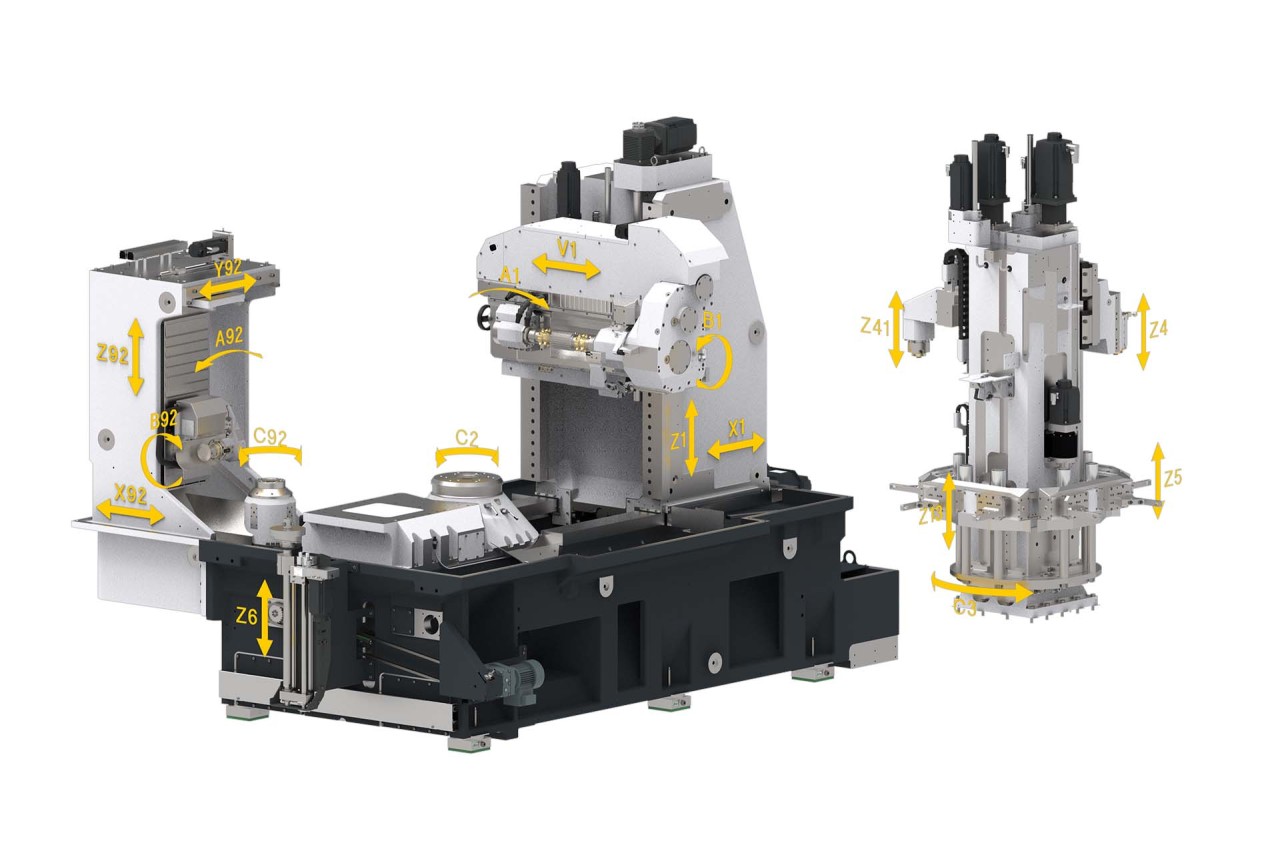
LC 300 / 500 DC with integrated ChamferCut device
With the LC 300/500 DC, the ChamferCut device is integrated on the operator side. This device has been enhanced in terms of user-friendliness. As such, the machine operator has unobstructed accessibility to both machining positions. Chip removal has also been significantly improved. Using the proven Liebherr ringloader concept, the workpiece can be transferred quickly and efficiently between the gear hobbing and chamfering machining positions. Chamfering by ChamferCut or FlexChamfer therefore takes place parallel to gear hobbing. The special feature of the chamfering unit is that it is controlled using 6 CNC axes as standard. Set-up or corrections and adjustments for varying flank corrections can be executed quickly and easily using the user-friendly software.
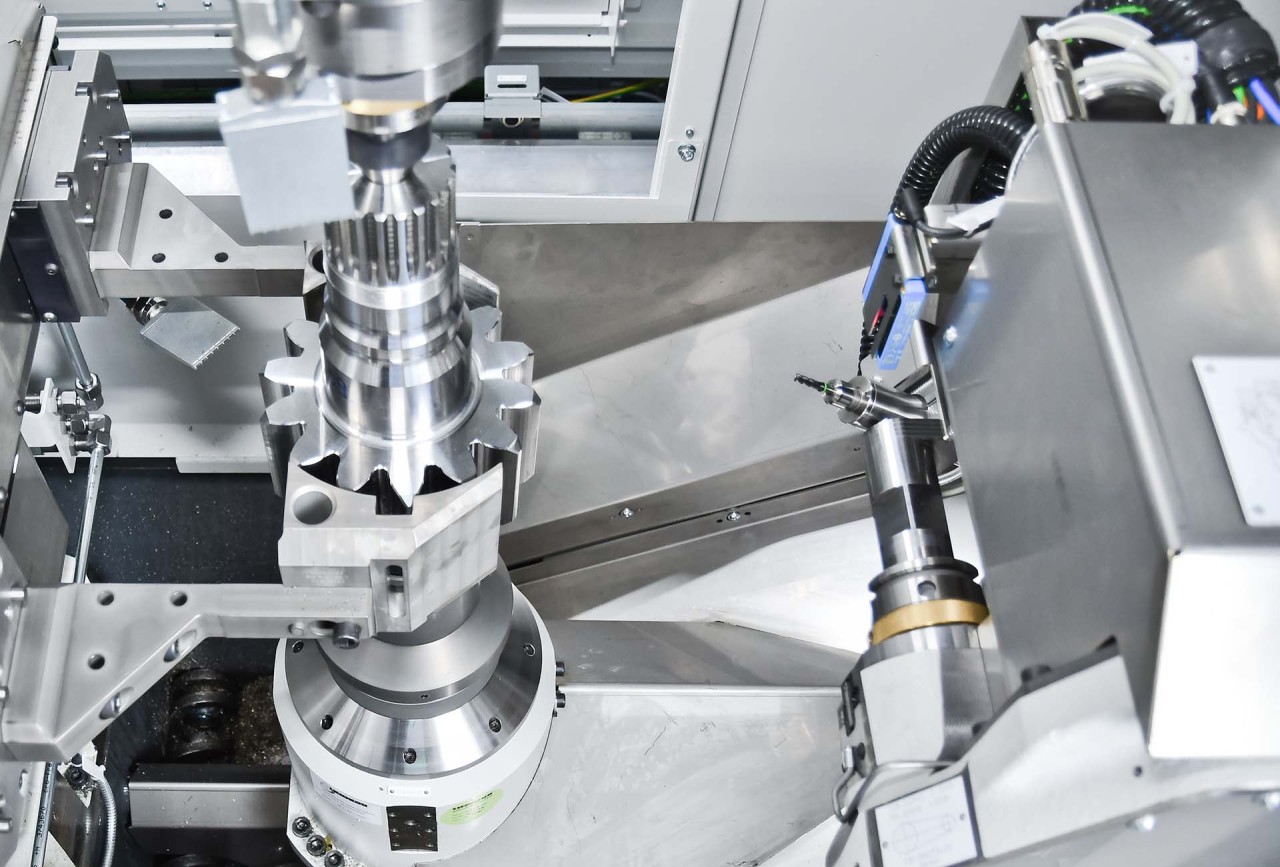
The chamfering parallel to machining has once again been improved in the overhauled machine series for gear hobbing. Perfect chip removal is now provided and chip deposits can be virtually eliminated.
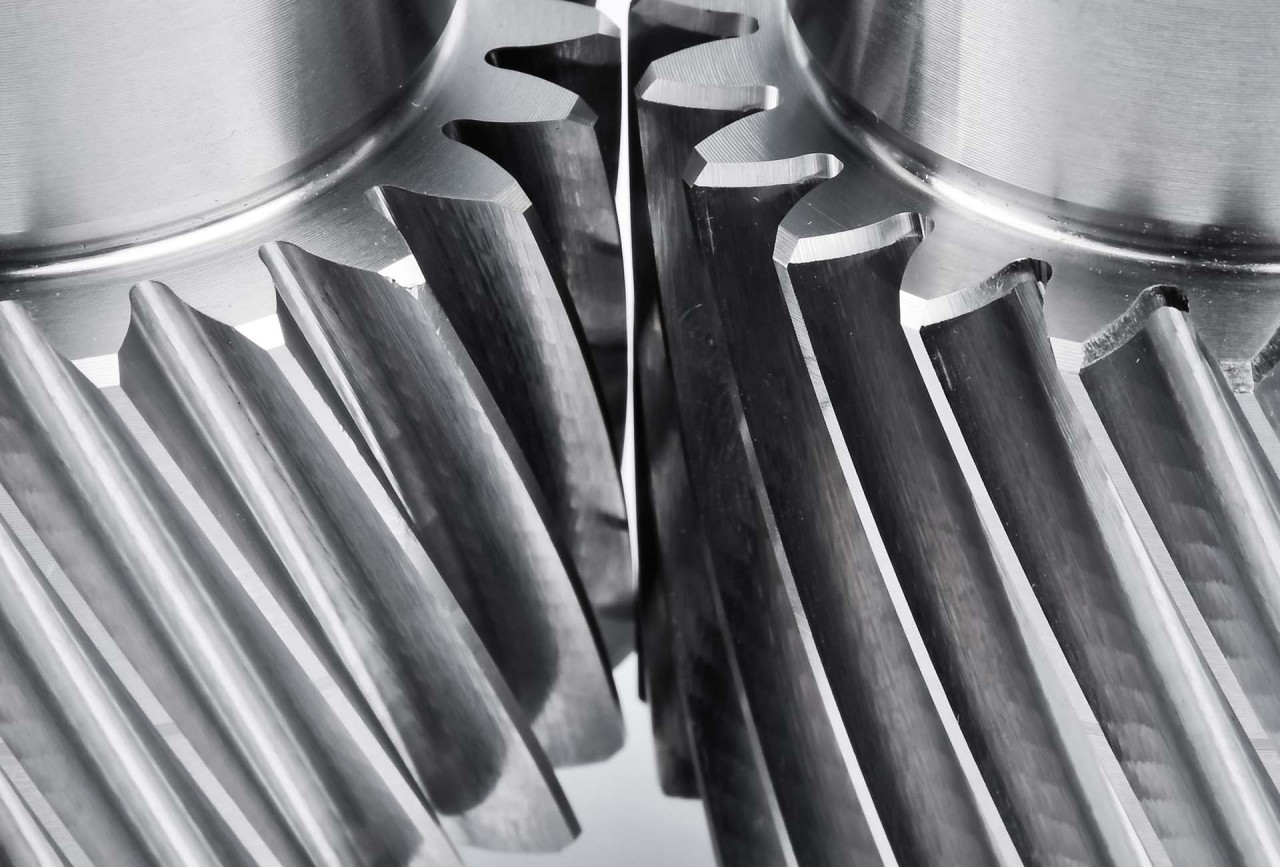
ChamferCut & FlexChamfer
The chamfering technology used can be either the familiar ChamferCut and/or the newly developed FlexChamfer process. A particularly notable feature is that workpieces with a diameter of up to 500 mm can now also be chamfered during the machining process. In addition, both processes can be used. This means that the finger milling unit can be mounted quickly and easily. This allows the customer to chamfer large workpiece lot sizes with the economical and fast ChamferCut process. However, if the workpiece lot sizes are very small, the FlexChamfer process can be used and the workpieces can be chamfered very quickly and flexibly. This is unique to this gear hobbing machine.
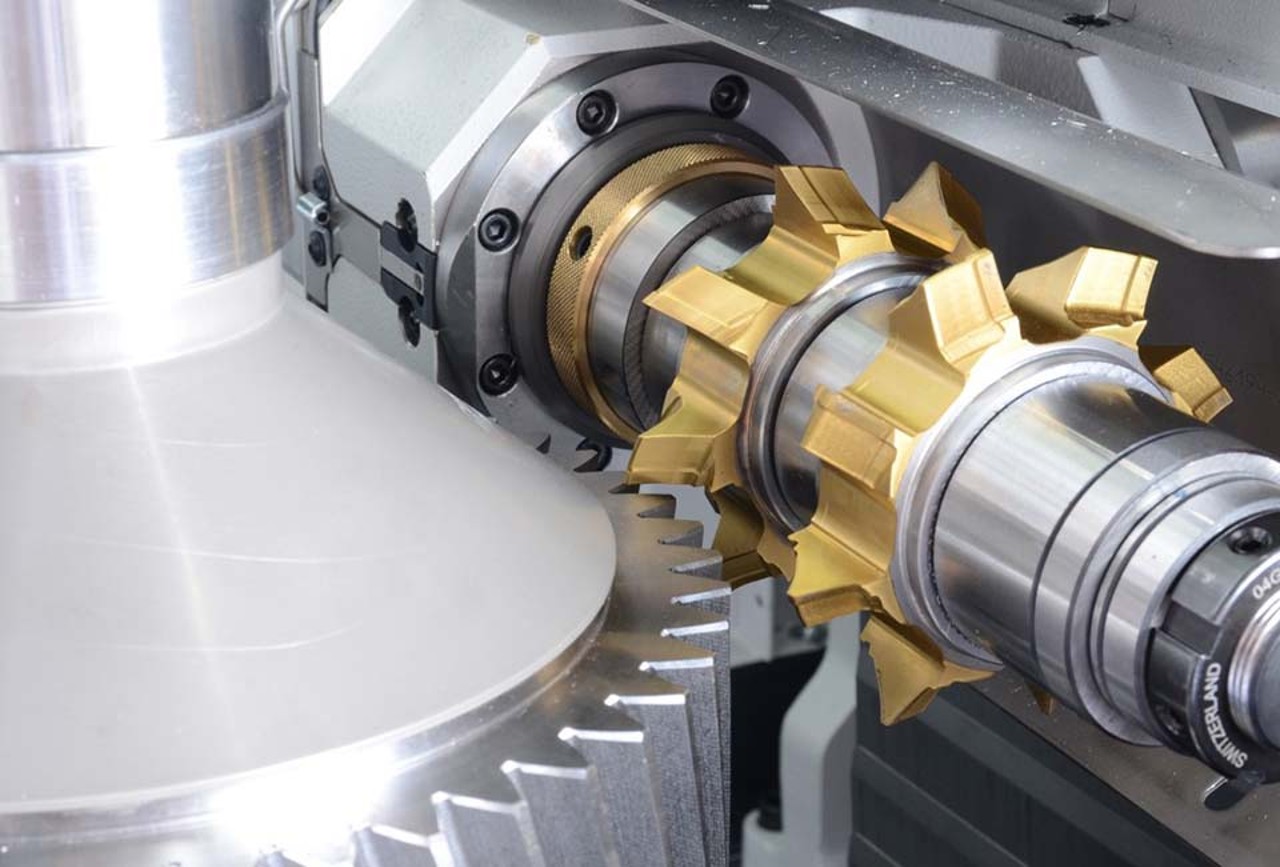
ChamferCut - Fast. Economic. Precise.
This is the chamfering process
After chamfering with the patented ChamferCut technology, no additional machining is necessary. The second hobbing cut, which is typically necessary when press deburring, is not necessary. The exact chamfer shape is generated by removing chips. In contrast to reshaping processes, there is no effect on the material structure. An optimal starting point is created for the subsequent finishing of hardened gears, particularly gear honing. This process is perfectly suited for very large batch sizes and quantities in mass production.
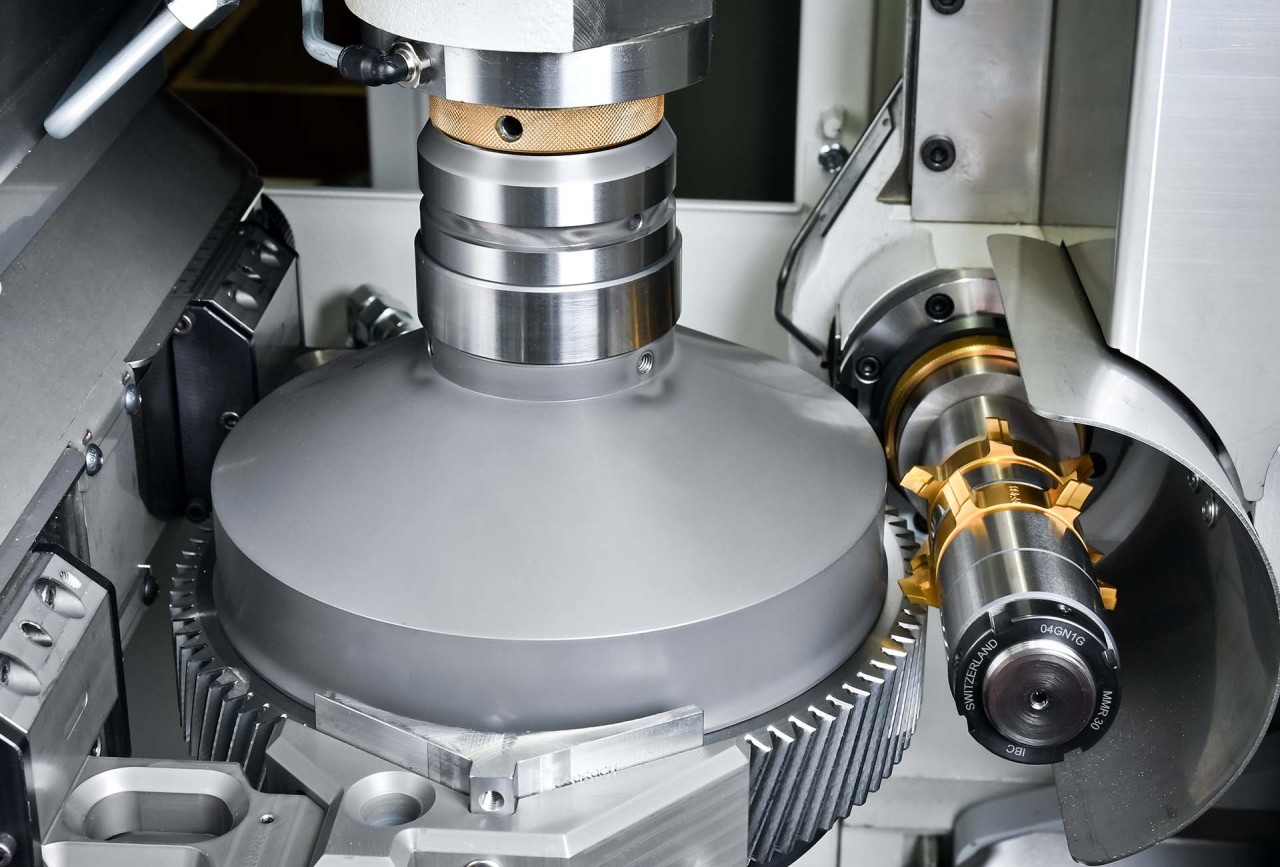
ChamferCut advantages
- Very precise chamfer geometry
- Premium chamfer quality and reproducibility
- No bulging or material deformation
- Tooth root chamfering as standard
- Established process in gear production
- Very long tool life
- ChamferCut tools can be easily and cost-effectively reground 15 - 20 times
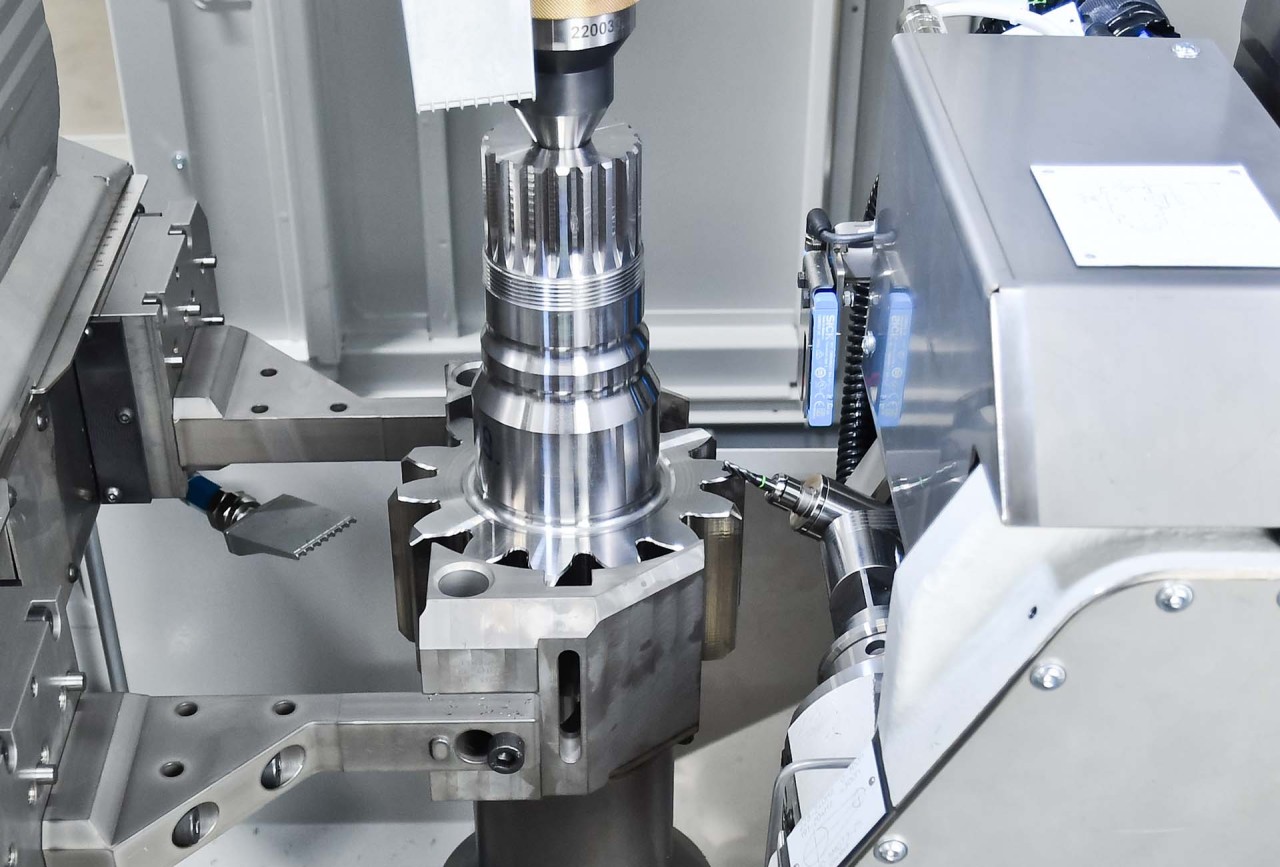
FlexChamfer - Efficient. Flexible. Precise.
In addition, we offer the new FlexChamfer technology. The gears can be chamfered quickly and efficiently using a standard shank hob. The movements of the tool are also fully NC-controlled, ensuring high repeatability and chamfer quality. This process is ideal for workpieces with interfering contours or when there is a very large part variance and small batch sizes.
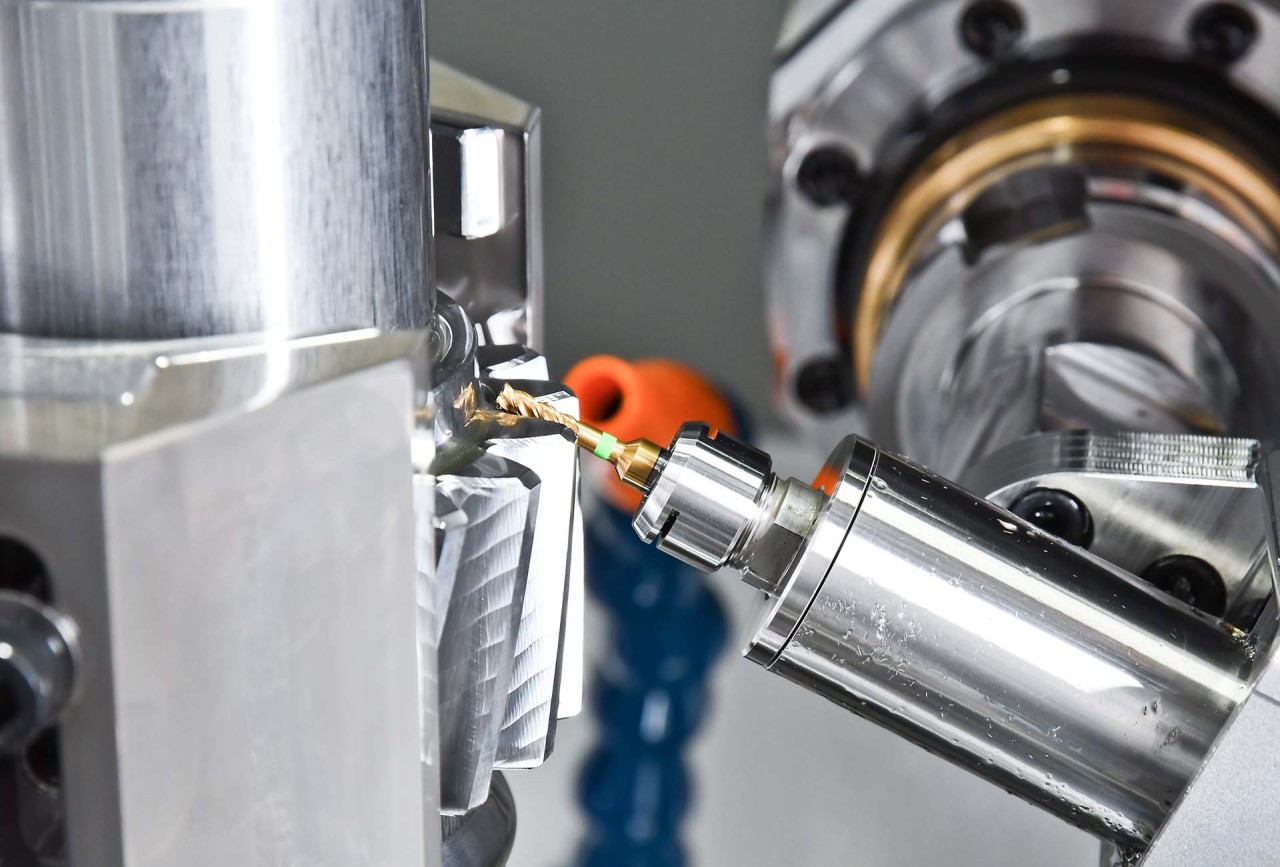
Advantages FlexChamfer
- Flexible and universally applicable
- Easy programming in the control software LHGearTec
- Ideally suited for workpieces with interfering contours
- Precision chamfering geometries
- Highest reproductive accuracy
- Easy NC corrections possible
- Use of standard tools (available extremely quickly)
Technical data
Variants | LC 300 | LC 300 DC | LC 500 | LC 500 DC |
---|
Automation & Features
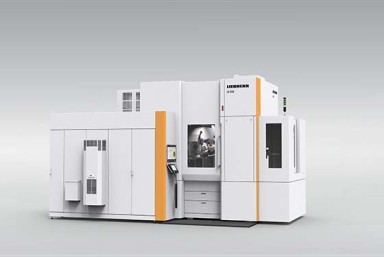
Manual or robot loading
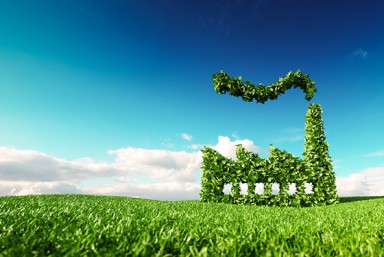
Energy and resource efficiency
- Regenerative drive technology
- Use of efficient control cabinet coolers
- LED technology lighting
- Coolant supply and
- preparation with speed-controlled pumps