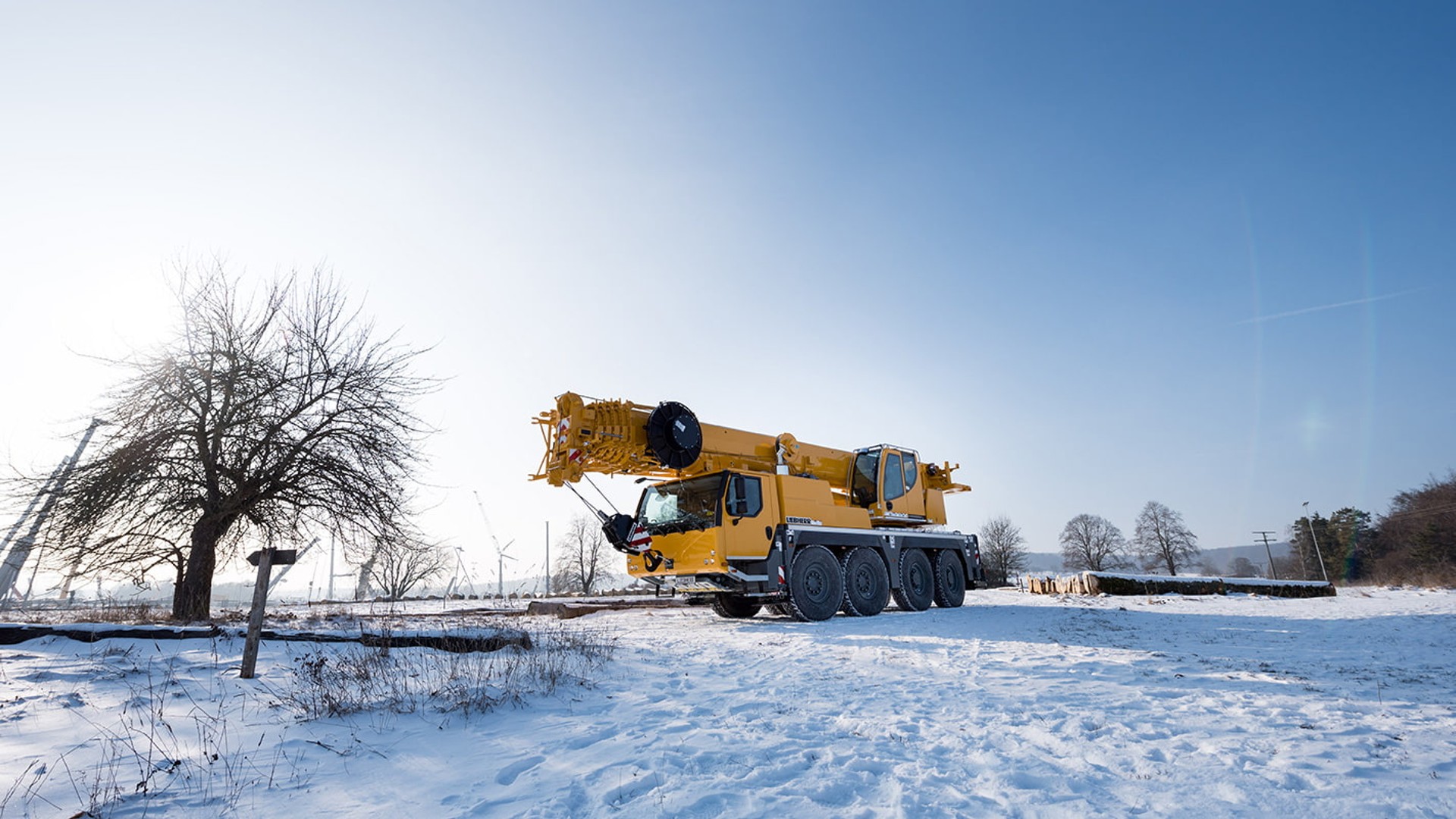
7 minutes | magazine 02/2018
Field test – the latest engine and emissions technology
Over the last few months, there has hardly been a news bulletin which has not mentioned “particulate pollution” or “diesel bans”. The topics of environmental protection and statutory regulations pose a daily challenge to Liebherr as well. Since mid 2017, crane rental contractor ESB based in Mittelbiberach has been testing an LTM 1070-4.2 with an engine which complies with emissions stage 5. We talked to Karl Engeser, owner of Kranverleih ESB, Karl Stöhr, Head of Product Management at Liebherr in Ehingen and Daniel Rössner, Test Engineer at Liebherr about the challenges and solutions in this field.
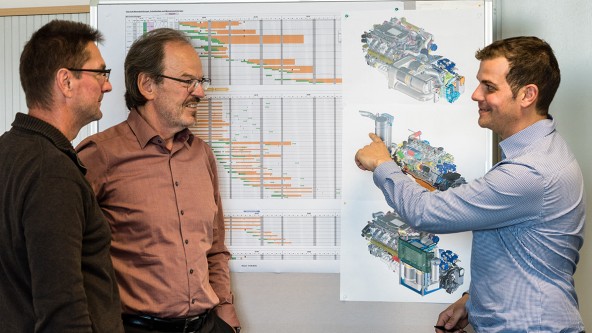
Karl Engeser, Karl Stöhr and Daniel Rössner
Why is Liebherr currently working on fitting new engines to mobile and crawler cranes?
Karl Stöhr: The main reason for this is essentially a statutory one. The European Union is pursuing the goal of reducing engine emissions further. The main aim of this is to use new filter technology to prevent particulates being emitted into the environment.
The new EU Regulation 2016/1628 will come into force on 1 January 2019 and will affect all the diesel engines fitted in our cranes. In all the countries of the EU as well as Norway and Switzerland, every engine built in 2019 or after will have to provide greater protection to the environment through its particulate filter.
What are the special challenges for Liebherr as a manufacturer of mobile and crawler cranes?
Karl Stöhr: Converting our entire crane range to engines which comply with emissions stage 5 is a massive task in itself. More than 30 different engine installations have had to be redesigned. But in addition to this, the same basic machine not only has to be suitable for the new EU engine with a particulate filter, but also the stage 4 (Tier 4) engine which is primarily aimed at the USA and the stage 3a engine for countries with lesser regulations. That is a massive challenge both for our design team and for our logistics people.
The correct and prompt provision of prototype units featuring the new filter technology and above all, early testing by our test department is another important job.
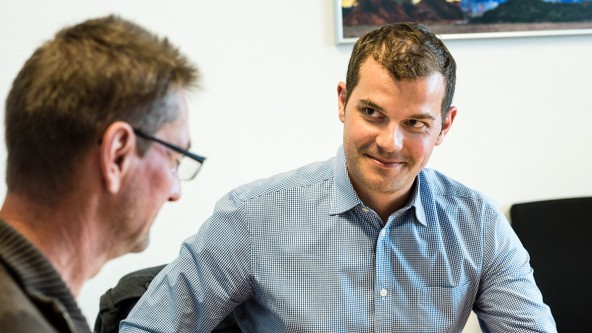
Karl Engeser and Daniel Rössner
What technical solution do Liebherr engines feature to enable them to comply with the stage 5 limit values?
Daniel Rössner: In addition to the SCR technology we already have, our cranes feature a sealed particulate filter system. This filters almost all the soot particles out of the exhaust gas. You will notice it in the future by the clean exhaust tailpipes – as you can see on the LTM 1070-4.2 test machine.
Karl Engeser: I can only confirm that. You can put your hand into the exhaust – and it’s really clean!
Daniel Rössner: In principle, the introduction of a particulate filter in an existing machine concept is very demanding from a technical point of view. The use of our diesel engines for cranes cannot be compared to applications such as those involved in long range trucking. Furthermore, the load collective of the units, depending on the type of operation, is extremely diverse. For example, in undercarriage mode, the engine operates for long periods at full power, whilst in superstructure mode, high load requirements are more temporary in nature.
One of the big challenges is the recurring regeneration of the particulate filter. Our system is designed in such a way that the regeneration takes place continuously whilst the vehicle is being driven. That enables us to minimise downtimes. If the filter does fill up eventually, it is of course possible to regenerate the filter by active means whilst it is in the machine without it having to be removed.
We made the procedure required for this as customer-friendly as possible together with the Control, Product Management and Testing Departments and the Liebherr engine plant in Bulle (Switzerland) without overburdening the operator with displays.
What are the testing procedures and what role do field tests play?
Daniel Rössner: In general, each prototype goes through a range of acceptance procedures in undercarriage and superstructure tests. The machines are subjected to standardised tests. This is necessary to ensure that the systems achieve an appropriate level of maturity before being released for field tests by customers. A field test can only be started when we are certain that the customer can expect not to have any restrictions in crane operations involving the machine or the new system.
The test should therefore not be guarded as a substitute but actually as a supplement for the testing phase. It is enormously important for us to observe new systems, such as the diesel particulate filter, operating in real conditions for customers. In addition to improving the components, these measurements from the field tests can also deliver important findings for new developments.
Mr Engeser, you have been operating probably the cleanest mobile crane in the world since April 2017. What made you help Liebherr with the field tests?
Karl Engeser: When you consider that the new emissions stage 5 in Europe exceeds all other limit values, there is no doubt that we have been operating the cleanest crane in the world for the last 18 months. And it was actually our consideration for the environment that played a major role in our decision to get involved. In addition, I’ve always been interested in new technology. The field test seemed an obvious choice as a result of how close we are to the Liebherr mobile crane plant in Ehingen. We are just 30 km away, very close indeed.
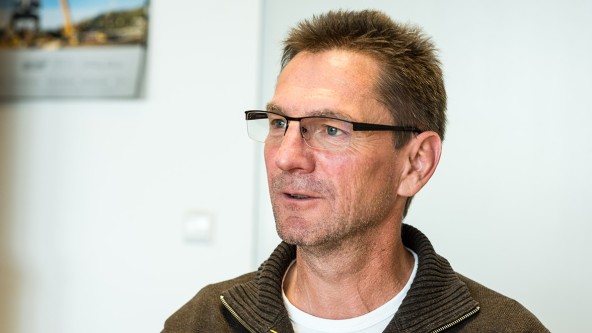
Karl Engeser
What experiences have you had with the new engine and its emissions technology?
Karl Engeser: They have all been positive! The crane has not let us down at all over the entire period. The vehicle remained operational throughout. High availability is a major criterion. We owe that to our customers. We clarified any minor faults we experienced direct with Liebherr’s Test Department. There was one breakdown where I phoned Mr Rössner direct. The problem was dealt with straight away. Again, the crane did not suffer any downtime.
Daniel Rössner laughs: I was expecting the phone call. The replacement part had already been ordered. The measurement data records showed that the failure was about to happen. We had direct access to the engine data using the telemetry.
Karl Engeser: My crane drivers had reservations at the beginning because nobody wants to look silly in a customer’s eyes due to technical problems. But that is absolutely not an issue any more. In fact, everybody wants to drive the new crane. What’s more, the drivers are absolutely delighted with the engine performance. The new emissions technology has not resulted in any loss of power. The consumption of both fuel and of AdBlue is unchanged.
Daniel Rössner: Emissions stage 5 does not adversely affect fuel consumption. Previous experience from practical tests has also been very positive for Liebherr. We now have other cranes with other engine types undergoing field tests.
This article was published in the UpLoad magazine 02 | 2018.