More than mining: Liebherr’s special application machines
Liebherr’s mining excavators are impressive for a number of reasons. They’re reliable, fast, efficient and can withstand some of the toughest conditions imaginable: scorching heat, bitter cold and soaring altitudes. But thanks to Liebherr’s Special Applications projects, these incredible machines can also be used in projects outside of the pit.
Transforming one of Liebherr’s excavators into a special application machine is a highly collaborative process that requires input from Liebherr, the customer and – sometimes – a third-party specialist. The first thing that needs to happen is that Special Applications has to be told exactly why the customer needs a specialised machine: what type of work it will be doing and which capabilities it needs to have. Once Special Applications has this information, they will know if Liebherr Mining is able to supply the entire machine on its own or whether a trusted third-party supplier needs to be brought in.
‘We do a lot of things well as an OEM [original equipment manufacturer], but in order to give our customers the best possible solutions, sometimes we need to look outside the box and involve external expertise,’ explains Zack Sims. ‘For example, if a customer needed an excavator with a reach of more than 25 metres with the weight of a mining-sized machine, we would work with a third-party supplier that specialises in these kinds of attachments.’
Zack Sims is a national account manager for Liebherr USA, Co. (Liebherr USA) focused on large machine specialty markets. Sims worked in heavy equipment sales for a decade before joining the Liebherr USA team in 2019. His previous experience, coupled with his expanding knowledge of Liebherr’s product range, allowed Sims to see how Liebherr’s mining excavators could be used to meet a variety of customer needs. Because Liebherr’s special application machines can be so highly customised, they can be used in a wide range of job sites, allowing Liebherr Mining to provide more solutions to more customers.
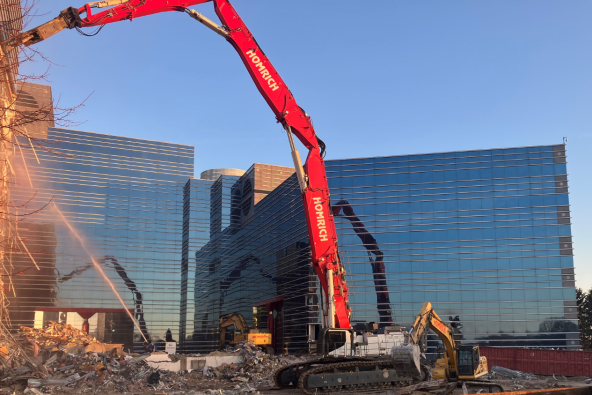
Homrich
Homrich
Homrich is a third-generation family owned and operated demolition company. The company has been based in Detroit, Michigan, since 1964 and has grown to become a leader among demolition contractors in the United States. Homrich is recognised as one of the premier environmental and demolition contractors in the industry.
Machine model
Liebherr R 9150 XHD (modified by Kocurek)
Machine specs
– 272 tonnes (600,000 lbs)
– Extended tracks and widened track frame
– Ability to reach over 50 m (165 ft)
Year machine went to work
2021
The machine’s job on site
The R 9150 XHD is the primary machine used for larger demolition projects. It brings high structures down to the ground so the support equipment can process the materials.
A word from Homrich
‘While conceptualising the custom retrofit, our fabricator said the Liebherr R 9150 XHD was the only option for a base carrier. Now, after experiencing the quality, stability and hydraulic precision and power, they were clearly correct! Our operators cannot speak highly enough about the power, speed and precision of the hydraulic system and our mechanics appreciate the serviceability of the machine.’
Choosing the right machine
While Liebherr’s excavators can be used in a range of specialised applications, they can usually be found in dredging or demolition operations. Customers prefer to use Liebherr excavators for these types of projects due to their fuel economy, extensive engineering, robust builds and the company’s willingness to work with customers and to partner with potential third parties. But in order to find the right machine for the customer’s project, there’s some fundamental information Special Applications needs first.
‘At a very basic level, we need to know how high a demolition machine needs to reach and how low a dredging machine needs to go. For dredging, we also need to know the capacity of the bucket,’ says Sims. ‘Once we have that info, we can start the planning process.’
As much as there can be standard machines in such a highly specialised field, Liebherr has two special application ‘models’ that customers can choose from as a starting point: the R 9150 XHD and the R 9150 EW-SL. Which of these machines a customer chooses all depends on the final design specifications. Liebherr can use other excavators within its product range as the basis for a special application machine, not just the R 9150. However, the R 9150 has been approved for these projects; other models would need to go through extensive vetting processes conducted by the engineering team at the excavator factory in Colmar, France, to ensure they would be a good fit for applications outside of digging in mines.
The R 9150 XHD has the uppercarriage of a standard R 9150 but has the undercarriage of an R 9200. This configuration was first seen in 2017, when Liebherr partnered with a construction company in Switzerland to build Europe’s largest demolition excavator (at that time). The design of the machine was so successful – thanks in large part to the additional 22.7 tonnes of weight acting as a counterweight for the elongated attachment –that it inspired the R 9150 XHD used today.
Liebherr creates the large footprint of the R 9150 EW-SL by lengthening the tracks of an R 9150 and cutting out its X-frame and widening it. The wider undercarriage of the R 9150 EW-SL helps to keep the machine stable as its attachment moves up and down.
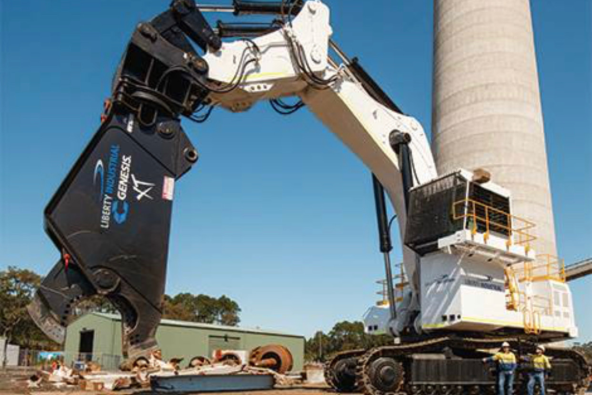
Liberty Industrial
Liberty Industrial
Liberty Industrial is an award-winning provider of specialist decommissioning, demolition, deconstruction and remediation services around the world. The company is based in Australia and has received both local and international recognition for the delivery of some of Australia’s most recognised industrial demolition and remediation projects.
Machine model
Refurbished R 994
Machine specs
The machine weighs in at 230 tonnes and is equipped with an Embrey Heavy-Duty Grapple or a Genesis GXT2555R Shear attachment – capable of cutting a 1.2 metre steel I-beam in a single bite.
Year machine went to work
The machine has been working since 2011.
The machine’s job on site
This machine has been deployed on the largest industrial demolition projects across Australia. It has processed large structural steel members on projects including power stations, refineries and mining Infrastructure.
A word from Liberty Industrial
‘The Liebherr R 994 and shear combination was a game changer. It allowed us to demolish substantially bigger and heavier structures without needing to pre-weaken them. This mitigated the risk involved in using traditional demolition methods and removed personnel from the demolition work face.’
Supporting the machines
Regardless of whether a special application machine is built solely by Liebherr or in collaboration with a third party, customers can be assured that their machine is still covered under warranty – the cover might just look a little different than it would for a standard Liebherr excavator.
‘Liebherr still handles the warranty for all Liebherr parts of the machine. That doesn’t change,’ explains Sims. ‘What’s different is that, if a third party was involved in the build, they will cover the warranty for their parts.’
Liebherr is also responsible for facilitating the maintenance and repair for all of its special application machines, even if a third party was involved in their manufacture. Liebherr trains onsite personnel so that they can work on these machine themselves. The company also relies on its network of dealers to assist with equipment support requirements to keep downtime to a minimum, as these dealers can often get to a customer faster than someone from the local Liebherr branch. And if a special application machine is experiencing an issue the local team can’t fix, Liebherr sends in one of its specialist technicians from the region or even possibly from the excavator factory.
Spare parts – more often than not – also fall within Liebherr’s purview given that Liebherr spare parts are usually a customer’s first choice for their machine.
‘What we’ve found, across the numerous special application machines we’ve completed over the years, is that both customers and the third parties we work with prefer our spare parts installed on the majority of the machine. Using Liebherr spare parts makes it easier for end users to order what they need – they can just pick up the phone and call us, rather than having to call different places for different things,’ says Sims.
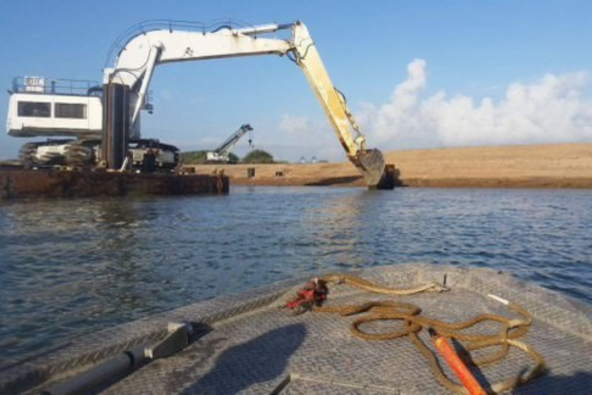
Luhr Bros., inc.
Luhr Bros., Inc.
Luhr Bros., Inc. is one of the largest and most well-respected marine contractors in the United States. Founded in 1939 by brothers Alois and Eugene Luhr, the company offers services for the delivery, unloading and placement of stone at multiple locations on the Mississippi River. Luhr Bros., Inc. also owns a rock quarry In Ste. Genevieve, Missouri, that produces over five million tonnes of stone per year.
Machine models
6 R 994, 1 R 9200 FS
Machine specs
These are all dredging machines that have anywhere from 19 to 32 m (65 ft. to 105 ft.) of reach capacity.
Year machine went to work
First machine was in 1987.
Latest machine was in 2020.
The machines’ jobs on site
Luhr Bros. use Liebherr machines on both land and water. The R 994s in the dredging application are used to dredge and place stone up and down the Mississippi River and connecting waterways. The R 9200 is used to mine stone at the quarry and is then sent to the barges for the rock placement division.
A word from Luhr Bros.
‘The Liebherr excavators have been reliable in the quarry and dredging projects. When we purchased the first Liebherr mining excavator in the 1980s, we were told the life expectancy would be 25,000 hours. We have already exceeded 70,000 hours on these units.’
Looking forward
Since Sims began leading these Special Applications projects back in 2021, the number of enquiries he receives about these machines has increased considerably.
‘Year on year, we’re seeing more and more customers reach out to us and ask whether our special application machines will work for them,’ Sims explains. ‘And as the number of Special Applications projects we’re involved in grows, our service department evolves right alongside us to support this growing demand.’
One of Special Applications’ current projects is to deliver two pontoon P 9150 XHDs to one of the largest dredging providers in the USA in Q3 of this year. This machine will be used to build rock pedestals for wind farms being placed at sea.