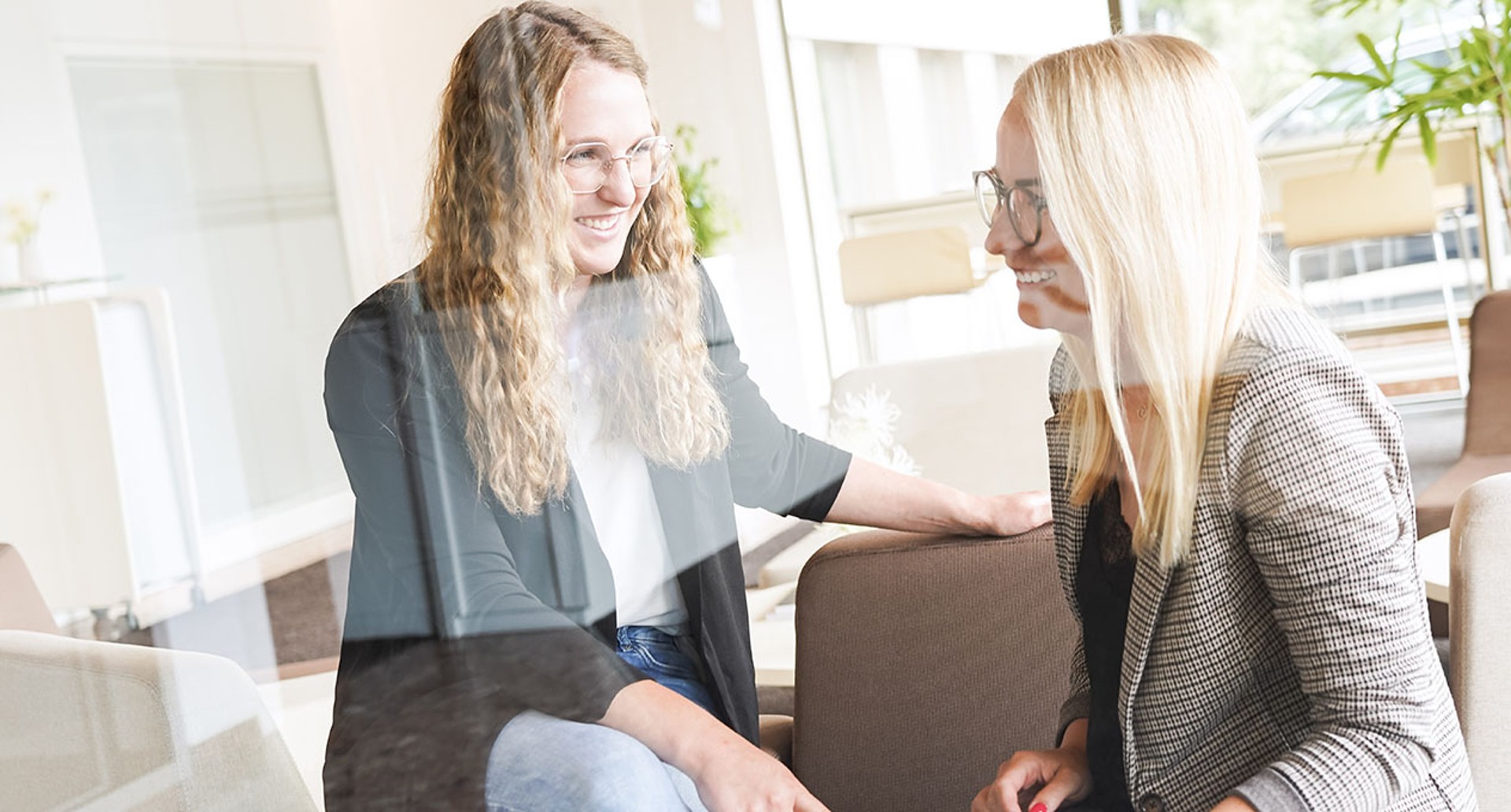
Women@Liebherr: A conversation with Anna-Lena Belm and Martina Waldmann, Project Engineers, Industrial Engineering
Anna-Lena and Martina have been dedicated engineers and loyal Liebherr employees ever since they first began their apprenticeships. After her apprenticeship, Anna-Lena continued her education by attaining a bachelors and masters degree in industrial engineering with an emphasis on mechanical engineering. Martina chose to qualify as a mechanical engineering technician and worked as a production engineer in automation systems. Now both work in industrial engineering.
In our interview, Anna-Lena and Martina talk about their daily work as project engineers at Liebherr and how they develop their ideas and their projects. They also provide insights into their most exciting projects and their personal development.
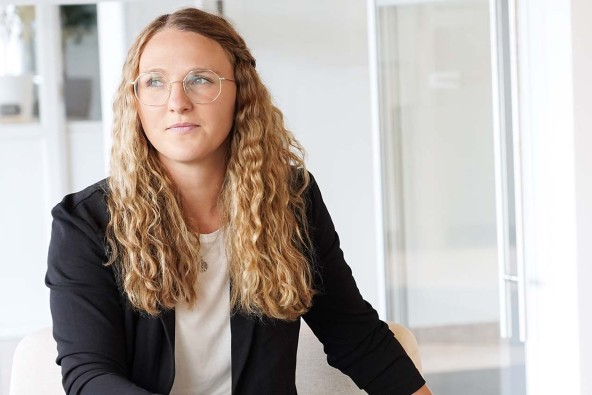
Martina Waldmann, Production Engineer, Industrial Engineering
Give us an idea of your day-to-day work and tasks as project engineers.
Martina: As project engineers at Liebherr, we're versatile and flexible in terms of the tasks we can be assigned to. All projects start with an idea, usually about how to optimize operating procedures. The impetus can come from us, but also directly from the departments. We then consider whether the task can be achieved, how to approach it and how we can help. The answers to these questions form the basis of a project profile, which clearly defines the requirements and goals.
In the next step, we examine the situation on-site. Either we work for a few days directly with the processes themselves or we watch them in action so that we can gain precise insights into the procedures and get to know the employees involved. That helps us to better understand the problem and find the right approach to solving it.
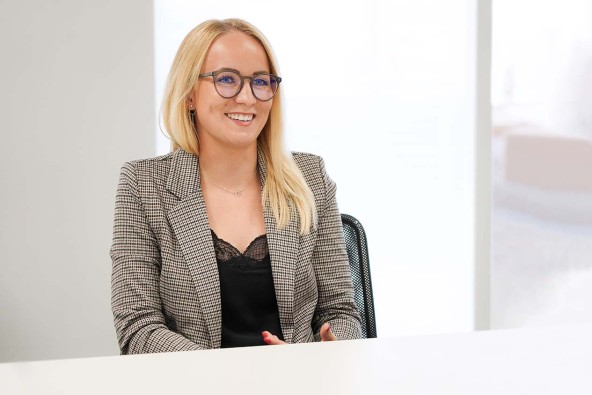
Anna-Lena Belm, Project Engineer, Industrial Engineering
Anna-Lena: That's right, when it comes to implementing a project, we often have an outsiders view and can discover operational blind spots. This allows us to introduce optimizations and achieve improvements that may have eluded employees.
Based on our observations and analyses, we create a schedule and plan milestones for the project. We discuss these plans with our head of department, the employees and the foremen so that we can be sure that everyone involved is informed and working toward a common goal.
Why did you decide to become project engineers? What sparked your interest in technology?
Anna-Lena: Technical projects in school, for example, can point you in the right direction, but a passion for technology is either a part of you or it isnt. I've personally always loved creating things and experimenting. That sort of interest in technical subjects and innovative solutions as well as the desire to help develop processes and optimize procedures were the things that ultimately inspired me to pursue a career in project engineering.
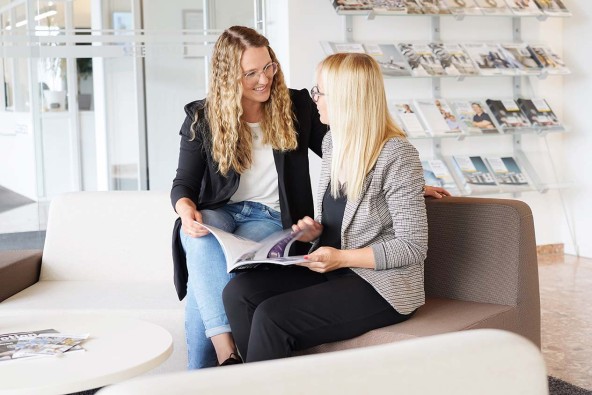
How did you come to choose Liebherr as an employer?
Martina: Our first contact with Liebherr was the MuT Girls and Technology project. Our girls school had a partnership with Liebherr, and we studied various technical modules with a tutor from Liebherr in the afternoons at school but also on site in the training workshop. That was a really exciting experience we built mechanical assemblies, designed and controlled electrical circuits as well as doing programming exercises.
Anna-Lena: From that point on, Liebherr became known as a "cool" company, and a lot of us applied to work there. I also got to know Liebherr better and quickly realized I wanted to work there. During the apprenticeship and in all the steps that followed like university and technical school that initial positive impression we had was always borne out by reality, so we stayed on.
Martina: It was actually an interesting journey from the girls school to a men's profession (laughs).
Our colleagues are always there for us either with a word of advice or a helping hand, and that's one aspect of the company that's truly invaluable when you need to get a project over the line.
And what do you like most about Liebherr?
Martina: We were just talking about that recently what we like most about Liebherr and we agreed its the variety. When I was 15, it was just construction cranes and excavators that came to mind when I thought about Liebherr, not gear cutting machines and automation systems.
Anna-Lena: Exactly, the products in the Gear Technology and Automation divisions are truly fascinating. In Automation, we work with new technologies like robots, while in Gear Technology, they do ultra-fine work thats precise down to the micrometer. This combination between the various divisions as well as their contrasts makes working at Liebherr especially exciting.
Besides the products, the team spirit also can't be overlooked. I often say we're a little Liebherr family. Our apprenticeships gave us the opportunity to work with and get to know nearly every department, and we've built up a small network. Kempten isn't very big; we often see each other outside of work, whether planned or by chance.
Martina: Yes, that collaborative spirit is wonderful. Whenever we have a problem, we always know who we can call, and in every department, theres someone we know who can help us out. Our colleagues are always there for us either with a word of advice or a helping hand, and that's one aspect of the company that's truly invaluable when you need to get a project over the line.
We have to get the team excited and keep people motivated, so that everyone identifies with the project and takes ownership.
Which traits are particularly important for a project engineer to have?
Anna-Lena: Perseverance. You have to fight for your project and truly believe in it, even in the face of obstacles and challenges. Of course technical know-how is also important, but you dont have to be an expert in every field. For that, we have specialists who we can always rely on. And yet you should still have an interdepartmental view of things and an understanding of the interactions between the different departments.
Martina: Teamwork is also super important. As project engineers, we have to get everyone in the team involved and motivated by emphasizing a cooperative spirit and a common goal. When people in a team are motivated, the project basically completes itself.
Anna-Lena: Exactly, the project team is the key. We have to get the team excited and keep people motivated, so that everyone identifies with the project and takes ownership. We clearly define the responsibilities from the outset and make the project our common baby.
Martina: Not too long ago, I was at a training seminar for two weeks. The entire time, I was super worried about how I was going to restart my current project when I got back as well as all the things that hadn't been dealt with while I was away. But when I got back, the team showed me all the things they'd done in my absence. It was cool to see how the team had advanced the project with so much enthusiasm and understanding.
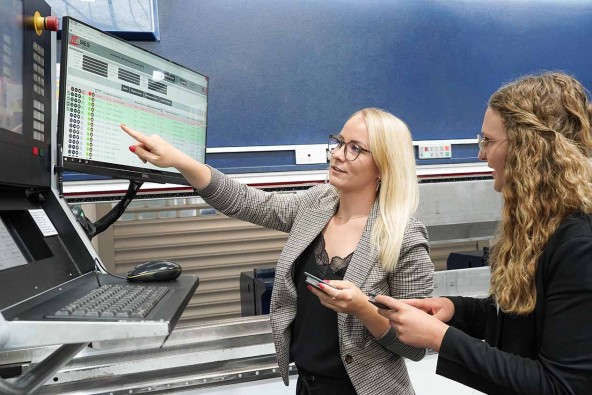
What was your biggest achievement at Liebherr to date?
Anna-Lena: By far my biggest achievement at Liebherr so far was my work on paperless production. I wrote my bachelor's thesis on the topic. Until then, the shop floor papers and drawings had always been printed out and transferred by hand. So the goal was to digitize them. This allowed processes to be tracked in real time and provided the employees with access to all necessary data like CAD models and drawings directly at their workplaces. This transition is a long-term project, but its very near and dear to my heart as it really increases our efficiency.
That the employees accept it is the decisive factor for me. They bring valuable ideas and suggestions to the table. The paperless production system didn't turn out exactly how I was thinking it would when I first set out. Thanks to the constant feedback from employees, it's grown and thats the way it should be. In the end, they are the ones who work with it every day.
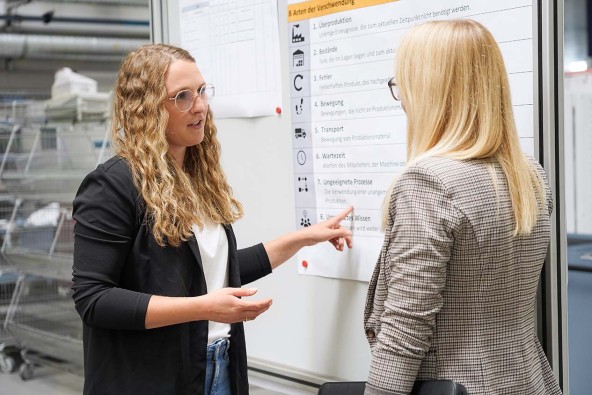
Martina: I'm currently working on a project to integrate lean management within the company. We've already tested out some approaches and have optimized the flow line assembly. It's fun to see how quickly you can improve things with relatively simple means. We've introduced eight types of waste that employees can use to critically evaluate their work steps. It's amazing how the employees have already internalized lean principles.
We want to implement lean philosophy at all levels of manufacturing and assembly, and it's exciting to see how visible the effects already are. We're proceeding one step at a time and making sure that we have the approval of the workforce for each step. If the motivation isn't there, the whole idea is pointless. To bring the employees on board and ensure the success of the project, it's essential that the managers support lean principles and are able to lead by example.
Whats next for you? How would you like to evolve in the coming years?
Anna-Lena: We've already attended various seminars, like project management and lateral leadership. No one is born with leadership qualities, but our tasks guiding our students and working in project teams, for example, require that we take responsibility, lead teams and are able to motivate people.
Martina: We want to remain at the cutting edge and don't want to stagnate, which makes feedback an important source of personal growth. When we are told what we do well and where we need to do better, we can reflect on our own behavior and improve. It's especially in difficult situations that we learn the most. Now we know how to deal with these situations and to seek support if needed.
Our boss brings a lot of experience to the table and is always there for us when we need good advice. Hes home-grown Liebherr, knows the company very well and can communicate with anyone on equal terms.
Anna-Lena: We're able to learn an incredible amount from managers and colleagues across the whole company. There are several quite young executives whose development we're following closely and who we find quite inspiring. But the old hands are also always open to our suggestions. Further education and continuous training have their place of course, but the experience and practical knowledge that our colleagues share with us are priceless.
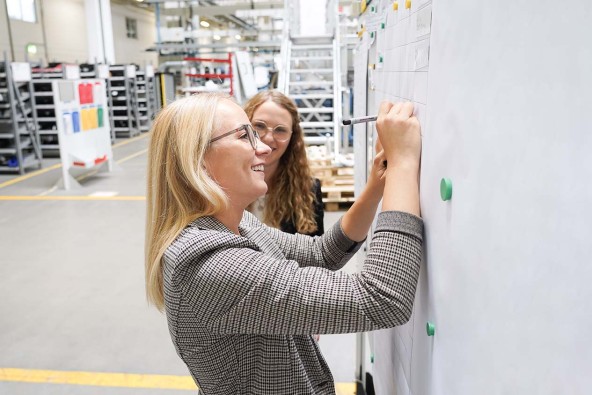
What advice would you give women who would like to pursue a career in technical fields or who are already working in these areas?
Martina: My advice is to approach your work with commitment and joy. That will provide you with the most opportunities for growth. Be open, and everything else will follow.
Anna-Lena: Absolutely, I completely agree. Having fun, enjoying your daily work is the key to success. The only way you'll find the endurance to successfully complete a project is by approaching it with enthusiasm and joy.