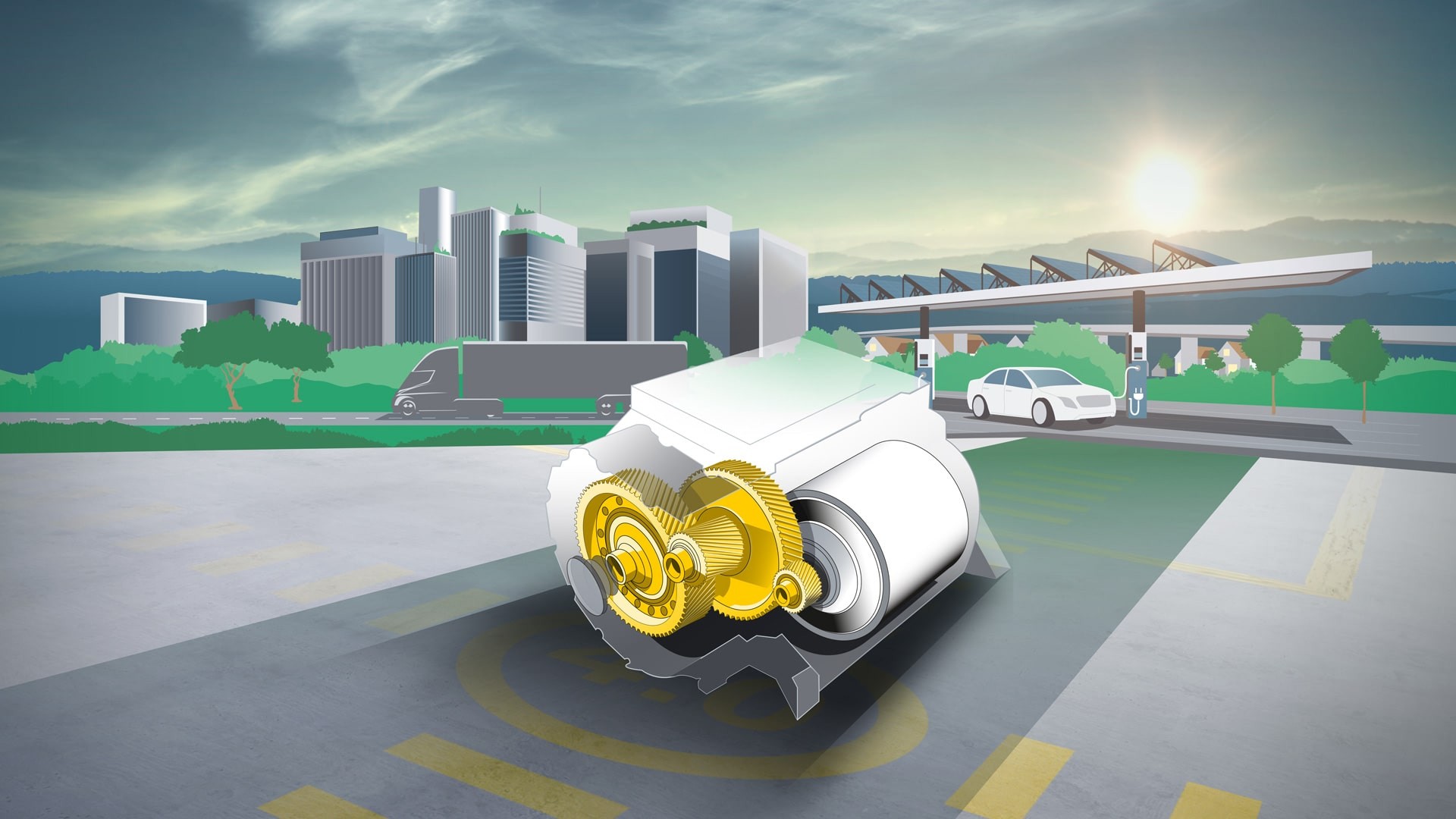
Gear solutions for e-mobility
New drive technologies in electric mobility are changing the requirements for gears and therefore also for the quality of the tooth flank surfaces. Manufacturers of gears have to adapt their manufacturing process accordingly. It’s good to be able to rely on a technology partner with expertise covering the entire range of production processes and technologies, which enables them to find suitable solutions even for special challenges.
E-mobility is changing the entire drivetrain in cars, which also changes the demands made of gear components. One of the most important topics is the reduction of noise emissions from the drivetrain while driving. In order to minimize installation space, many parts of the gearbox are manufactured using a lightweight or compact design. At the same time, gear components must become increasingly robust and long-lasting in order to withstand the considerable stress caused by the higher engine RPM.
We apply our expertise both in the process depth and in the range of technologies. This means that we can advise and assist customers comprehensively in order to find the optimal solution for them and their application.
Process and technology expertise from Liebherr
This results in high quality demands on the tooth flank surfaces, which in turn brings about growing demands on the gear cutting process. Liebherr-Verzahntechnik GmbH has addressed this issue and refined and optimized various technological solutions for e-gearboxes. “We know about the challenges that manufacturers and suppliers must master in terms of quality and process reliability”, explains Dr. Andreas Mehr, who is responsible for the technology applications of gear grinding and shaping. “We apply our expertise both in the process depth and in the range of technologies. This means that we can advise and assist customers comprehensively in order to find the optimal solution for them and their application.”
Processes and methods
On the process side, generating grinding with dressing-free CBN grinding worms, for example, ensures a high degree of process reliability. During the hard gear finishing, the gears can be precision-ground and polished, which further improves the surface roughness. Tools with small outside diameters machine collision-critical gears with limited tool overrun.
Methods for tooth lead modification are available for the tooth flank topology. For example, topologically error-free grinding with targeted end relief (GER) optimizes the load-bearing capacity. In order to reduce noise emissions, a targeted waviness can be applied to the tooth flank (Noise Excitation Optimization), or the diagonal amount during finishing can be increased in order to distribute the ghost line structure stochastically (Silent Shift Grinding).
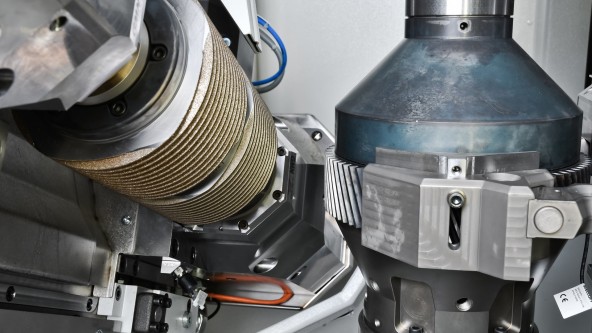
Example of use: Generating grinding of a drive gear for an e-drive with dressing-free CBN
Tool material: CBN grinding worms
The more topological modifications are necessary, the more it pays off to think about the tool material: CBN tools can be an economical alternative here. For many applications, grinding with corundum grinding worms is a good solution which, however, reaches its limits when grinding with high topological demands because of the dressing effort required. Dressing-free CBN grinding worms from Liebherr’s own production offer a number of advantages: high process reliability due to the long tool life, the avoidance of error sources during dressing, easy tool handling, and considerably reduced measurement and testing effort. For a topology with GER modification, for example, CBN grinding performs much better than corundum grinding with regard to the unit costs. Extremely fine surfaces with an Rz roughness factor of under three micrometers can also be achieved in this way.
Clamping solutions for small components
The challenge when producing gear parts for e-bikes is often in the intricate measurements and small modules. To manufacture these components in a high quality, the grinding process and clamping technology must be fast and extremely precise. Special clamping solutions ensure that even small and collision-critical components, such as drive shafts with a module of 0.6 in a gear quality of DIN 1-4, can be machined without difficulty.
Machine concept: economic efficiency and reproducibility
The exclusive Liebherr machine concept provides optimal concentricity and the highest possible reproducibility with a one-table solution – for the controlled and continual manufacturing of parts with quality requirements in the micrometer range, this is a technologically indispensable advantage. Particularly for smaller and medium batch sizes, which frequently occur in manufacturing for e-mobility, this concept is also particularly economical, since the short setup times enable a fast production start.
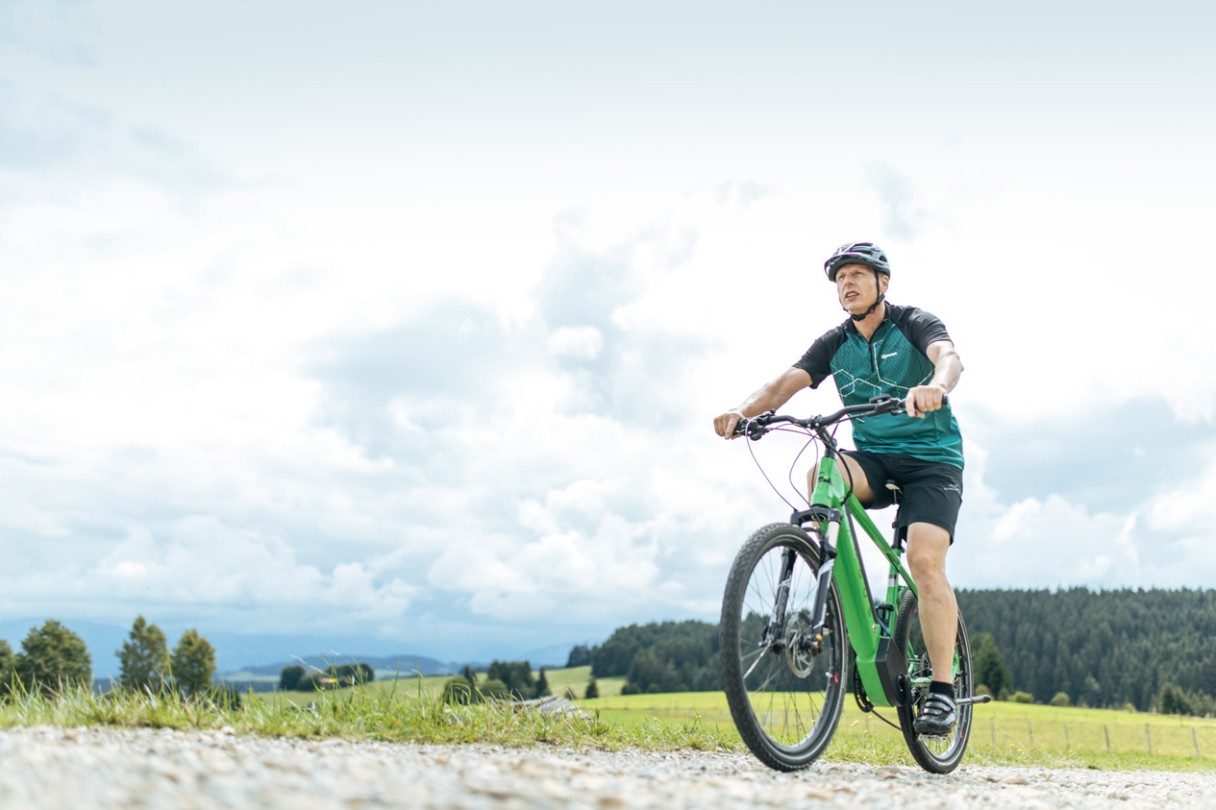
We see ourselves not only as product providers but as partners and solution providers.
At eye level with the customer
“We see ourselves not only as product providers but as partners and solution providers”, Dr. Andreas Mehr emphasizes. “We take the customer with us on the journey by offering advice and pointing out plausible alternatives so that he can finally make the decision that is best for him.” For this purpose, Liebherr has a number of test machines on which all the process parameters for the production of specific parts can be tested and designed, including the tool, the design or measuring software, grinding methods or process parameters, tooth flank modifications or other settings.
The only limits are those set by physics
For example, in one customer’s gearbox, noise was emitted despite adherence to the required specifications. Liebherr addressed this issue in an intensive discussion with the customer under strict time pressure. On the test machines, a number of variants for the corresponding component were ground and tested. It was revealed that the cause lay in further parameters outside the grinding process and that the gearbox had to be designed differently. On the basis of these results, the customer was able to optimize its processes accordingly. Noise emissions were significantly reduced, achieving a satisfactory solution within the limits of what is physically possible.
“It was possible to maintain the narrow timeframe because Liebherr has bundled the complete technology and expertise”, recalls Dr. Andreas Mehr, who explains further: “Often, there is no ‘right or wrong’. Rather, the choice of the optimal process depends on the specific requirements and parameters. At this point, we want to support our customers by honestly weighing up the pros and cons of one method or another.”