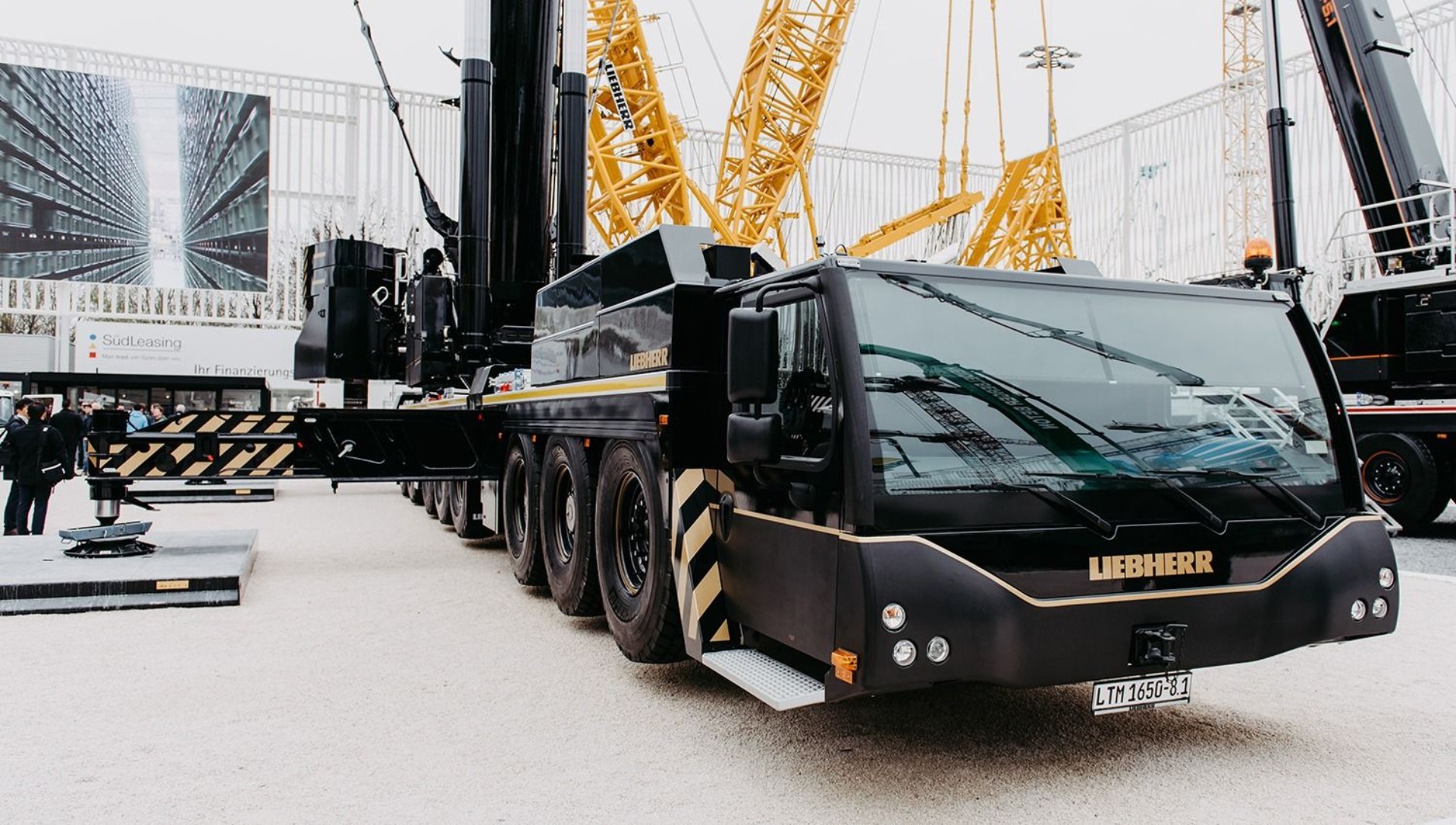
2 minutes | magazine 01/2019
More and more powerful cranes. How is this possible?
The laws of physics never change, but for decades cranes have been becoming more and more powerful. How is this possible?
The LTM 1500-8.1 dominated the market for large telescopic cranes for two decades. Its successor, the new 8-axle LTM 1650-8.1, is significantly more powerful although it is based on the same crane concept and has approximately the same crane weight. That enables it to break into the lifting capacity range which was previously the domain of 9-axle cranes. We asked Bernd Boos, Telescopic Crane Design Manager, how this is possible.
“Both cranes do indeed have around the same weight in terms of their crane structures. However, a good deal of technical work has been done in the twenty years between the design phase for the LTM 1500-8.1 and the one for the LTM 1650-8.1. For example, we now have fine-grain structural steel types which are much more efficient. In fact, the telescopic boom on the LTM 1500-8.1 is made of S 960 with a yield point of 960 N / mm². On the LTM 1650-8.1, on the other hand, we use S 1300 steel with a yield point of 1300 N / mm². That means that steel of the same weight has a 35 percent greater load capacity. Even better coordination of the boom profiles with the improved guying equipment has enabled us to increase lifting capacities even further.
Experience plays a major role in this development. We are always learning. For example, over the last few years we have collected a great deal of experience with thin-walled boom profiles and have managed to improve our calculation models using the finite element method.
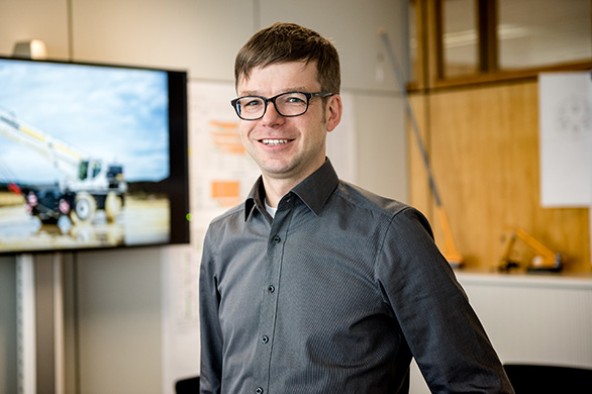
Bernd Boos, Telescopic Crane Design Manager
Furthermore, we have new manufacturing methods available today. It is now possible to manufacture longer metal sheets for the boom profiles which means that fewer welds are required. That also means less warpage in the material.
Two innovative Liebherr developments have also made a significant difference – the single-engine concept and VarioBallast®. We also made a conscious decision to use the single-engine concept for the LTM 1650-8.1 because the weight reduction caused by not having a superstructure engine can be used for the load-bearing components. VarioBallast® can improve performance since the increased ballast radius results in an increase in the moment of the counterweight and also relieves the strain on the vehicle’s chassis by reducing torsion. And the small ballast radius is perfect for constricted operating conditions.
These continuous improvements show that we are systematically working on pushing the bounds of physics.”
This article was published in the UpLoad magazine 01|2019.