From little things, big things are created: Liebherr components for mining
Mining machines are massive. Our biggest, the R 9800 excavator, weighs 800 tonnes and stands almost 12 metres tall. Each machine has networks of components – made by the Liebherr’s own components product segment – that keep them running.
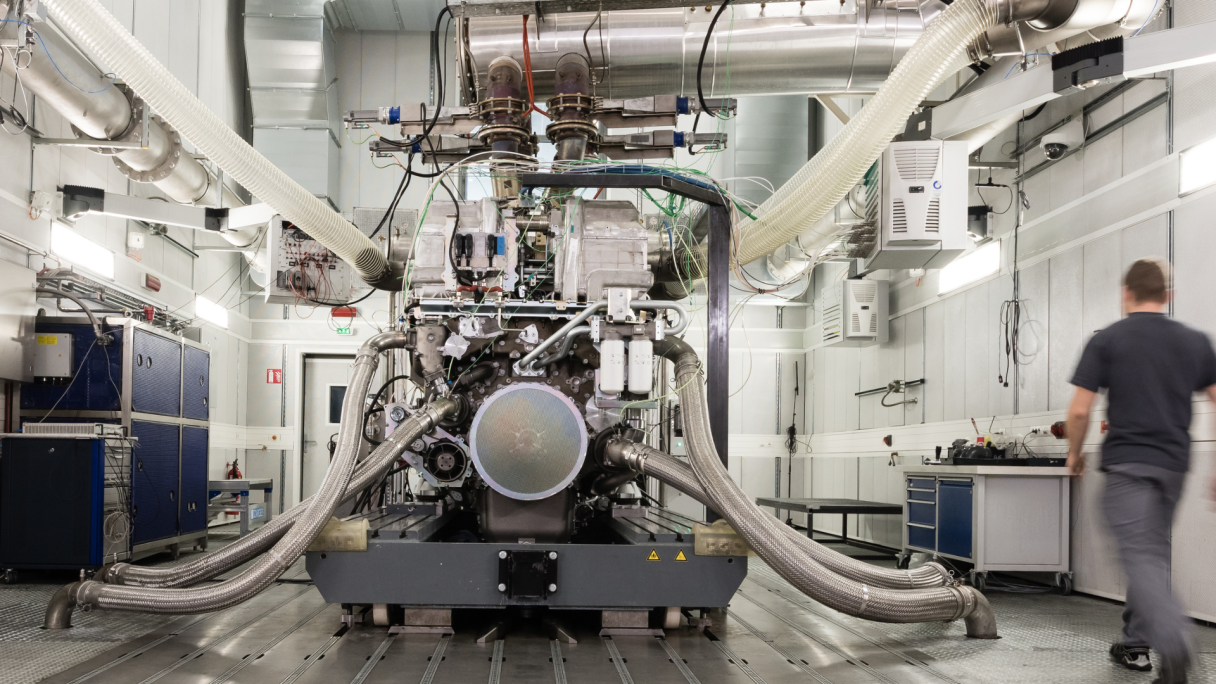
Every Liebherr component is designed and manufactured to meet the unique challenges of the environments they’ll be used in.
All of our mining equipment includes a number of components that have been designed and manufactured by Liebherr: from huge components like combustion engines, slewing bearings and hydraulic cylinders, to smaller
ones like travel, slewing and wheel drives; hydraulic pumps and motors of different types; suspensions and fuel injection solutions for combustion engines.
‘Using Liebherr components in Liebherr equipment has a range of advantages, the biggest of which is quality. Every Liebherr component is designed and manufactured to meet the unique challenges of the environments they’ll be used in,’ says Roman Maurer, design engineer, drive component development, Liebherr-Components Biberach GmbH. ‘To survive on a mine site, our components need to be reliable and rugged enough to withstand the extreme conditions seen in the pit, while also meeting our strict quality standards.’
As Liebherr is responsible for the components and the machines that house them, customers need only make one phone call should their Liebherr equipment require attention. Getting everything from a single source, like machine servicing, spare parts and components, saves time and money – two of the most precious resources on a mine site. Plus, servicing is also much more straightforward for Liebherr technicians when we use our components for our machines. Take the powertrain of a Liebherr mining excavator, for example. The powertrain contains numerous Liebherr components: a combustion engine with an internally developed fuel injection system, gearboxes (including travel and slewing drives), hydraulic motors, hydraulic cylinders and a splitter box with hydraulic pumps – depending on whether it’s a diesel-hydraulic or an electric-hydraulic powertrain. Liebherr’s in-depth technical expertise for upstream and downstream technologies and processes helps technicians to better understand what’s happening within the powertrain, therefore reducing servicing time to get the excavator up and running again much sooner.
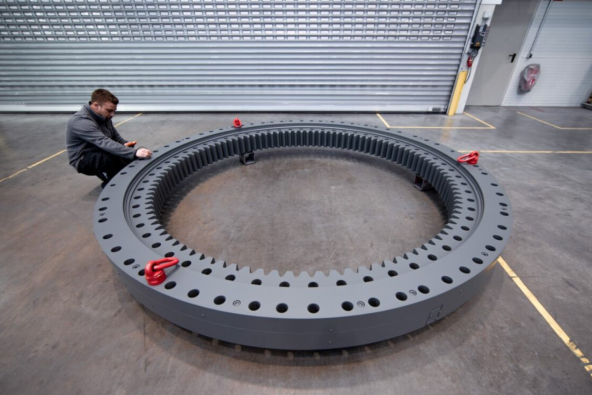
Making components work for mining
Conditions on mine sites are unique in their intensity. Mines are often in remote locations in regions that experience extreme temperatures and, sometimes, are even located at extreme altitudes. Day-to-day mining activities involve a lot of dust and dirt, not to mention the vibrations of the mining equipment itself. Any component used in such conditions must be tough enough to withstand them, while also offering the efficiency and reliability customers need to achieve their production targets – which is no small feat. Liebherr components are designed to be robust enough to meet all of these challenges, and also to be sustainable in nature. The majority of Liebherr components can be remanufactured, which increases the service life of these components, while also minimising resources used, reducing waste and saving both energy and costs. This contributes to customers’ satisfaction with our components and also demonstrates Liebherr’s commitment to building exceptional products across all of the product segments.
But before our components even catch a glimpse of a Liebherr mining machine, they go through an intensive validation process.
‘Our validation process is both theoretical and practical. The theoretical phase uses dynamic simulations and the finite element method to assess a component’s ability to work within the conditions of a mine site. Once the component passes this phase, the product moves on to practical validation, where it is subjected to tests designed to find weaknesses, so these can be addressed before field testing,’ explains Maurer.
Field testing is where we really see what our components can do. The process for testing our components differs depending on the component being assessed, but there are some similarities between the processes. Components are tested in the field for a specific period of time – for example, Liebherr’s suspension systems are put to work in the pit for up to 9,000 hours. Once the field test comes to an end, the component is then disassembled into its smallest parts and each one is analysed to understand what happened to the product during operation. The results are then collated and compared with the needs of the end customer. All of the data gathered by Liebherr engineers during this process helps Liebherr-Component Technologies AG (Liebherr-Components) to perfect its designs before they officially become part of Liebherr equipment around the world. However, integrating a Liebherr component into a Liebherr machine is not the end of the component’s journey.
‘Continuous improvement is a huge priority for Liebherr and so our products are never completely “finished”. When we get feedback that can be used to optimise machine performance, it’s collected, analysed and then implemented into our product improvement processes. This feedback can come from our customers, technicians, engineers or anyone else who works with our components,’ says Romain Botzkowitz, sales engineer, mining, Liebherr-Components Colmar SAS.
Production centres for components
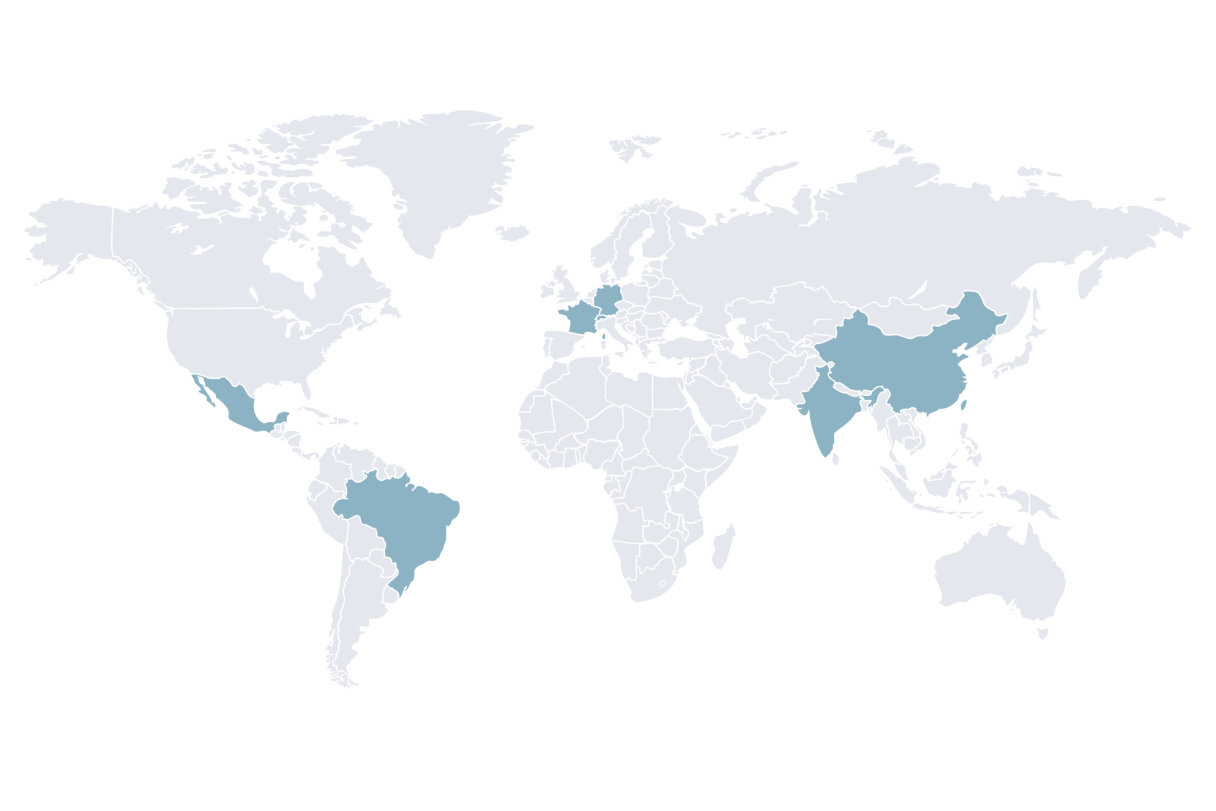
Who makes what?
Mexico
Slewing bearings of up to 3,500 mm and gear rings for the American market
Brazil
Slewing bearings of up to 4,500 mm
France
Large combustion engines
Switzerland
Combustion engines, hydraulic pumps and motors
Germany
All types of drives, slewing bearings and main bearings of all diameters, fuel injection systems, single- and double-acting hydraulic cylinders, piston accumulators, composites, suspensions, electric-drive technology, electronics and control technology. Components are also remanufactured here!
India
Drives and gearboxes for the wind industry
China
Gearboxes for the wind industry, earthmoving machinery and other industries; slewing bearings and main bearings with diameters of up to 6,000 mm for the wind industry and hydraulic cylinders for construction machinery
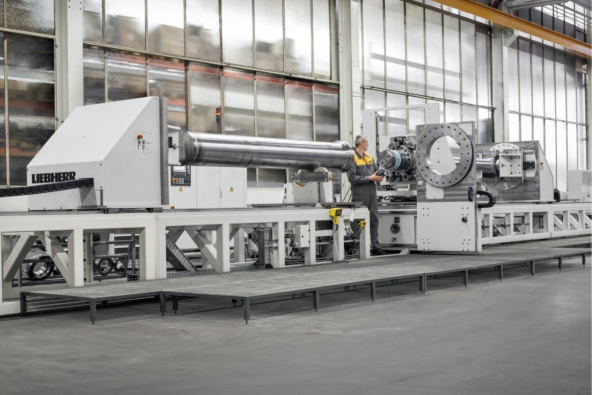
Preparing for the technology of tomorrow, today
Most of the Liebherr components used in our mining machines – such as our slewing bearings, combustion engines and fuel injection systems, hydraulic pumps and some types of drives – are equipped with sensors and are ready to be used in smart components monitoring systems. Using a combination of sensors, data analytics and autonomous technology, these systems allow mine operators to continuously monitor the performance and health of individual components within a massive mining machine. This can help onsite personnel to anticipate maintenance needs, which not only reduces unscheduled downtime, but also lowers maintenance costs and helps to keep maintenance personnel safe.
We wish to help our customers get the very best out of their Liebherr products. By ensuring that our components can easily be integrated into smart monitoring systems, we can help customers optimise their operations through data they may not have had before.
Let’s take, for example, Liebherr-Components’ own smart components monitoring systems like LiDIA for combustion engines or BCM for bearing clearance monitoring. Both systems offer a complete overview of the status of their respective components, which can help technicians to detect potential issues, optimise performance and even avoid breakdowns.
‘We wish to help our customers get the very best out of their Liebherr products. By ensuring that our components can easily be integrated into smart monitoring systems, we can help customers optimise their operations through data they may not have had before,’ says Andreas Palmer, managing director, slewing bearings technology and development, Liebherr-Components Biberach GmbH.
Working together
However, Liebherr-Components doesn’t just make components for Liebherr mining machines. To best support our customers, Liebherr-Components also develops, manufactures and distributes aftermarket slewing bearings, hydraulic cylinders, travel drives and wheel drives for a range of thirdparty OEMs (original equipment manufacturers).
‘It’s our goal to provide components that genuinely benefit our customers and their dayto- day operations. We aim to build long-term partnerships with our customers, in order to support their fleets the best we can – even if they aren’t all Liebherr machines,’ says Andreas Stark, senior global business development manager, aftermarket, Liebherr-Components Biberach GmbH.
But why would customers choose to use Liebherr components in another OEM’s machine? Stark says it’s the quality, performance and reliability of our products that put us over the top.
‘We have a reputation for providing top-of-the line products to our customers. This is in no small part due to our stringent quality standards for all components at Liebherr. Our constant drive to be better than the day before has led us to finding technical improvements for our components that can extend the service life and the reliability of equipment.’
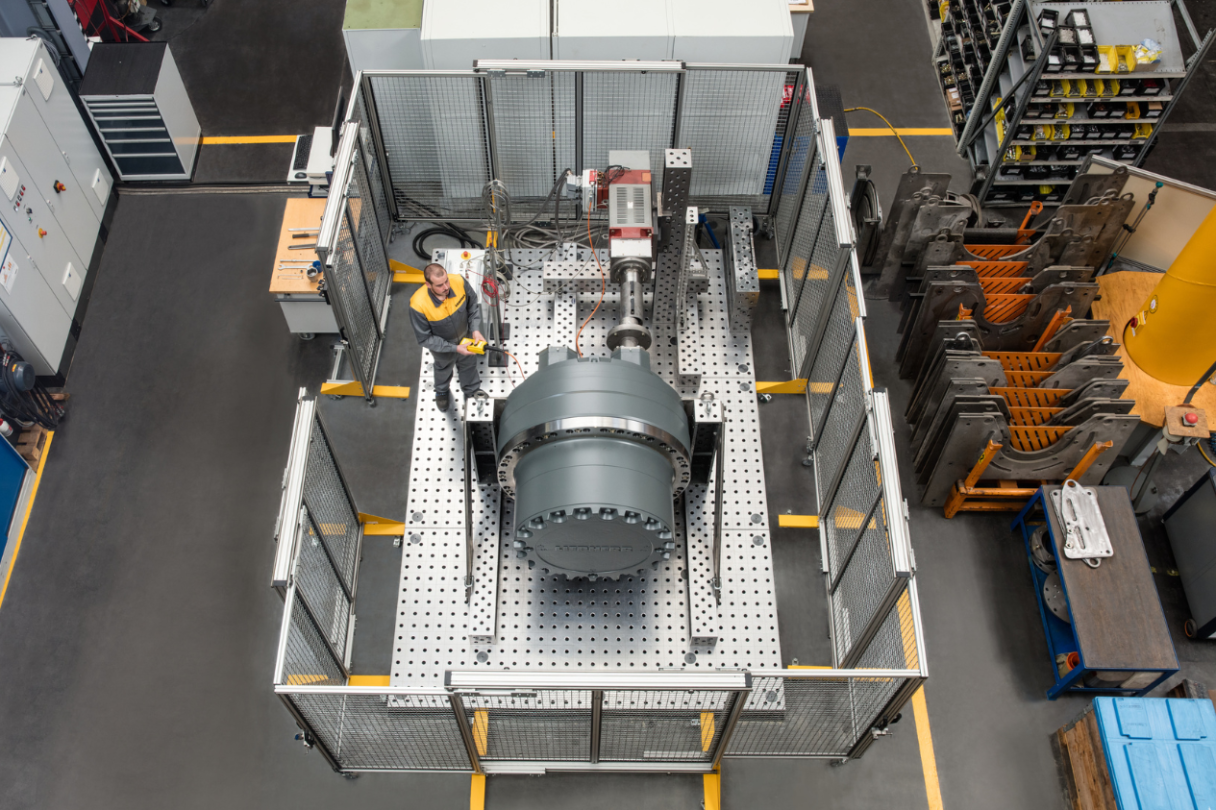
Liebherr-Components at a glance
– Liebherr has been producing components since the 1950s.
– Liebherr-Components’ parent company, Liebherr-Component Technologies AG, is based
in Bulle, Switzerland.
– There are eleven manufacturing facilities in seven different countries.
– Each of the nine Liebherr-Components sales companies is in a different country.
– The product segment has 5,700 employees worldwide.
Liebherr components are available all over the world, with eleven manufacturing facilities in seven countries, as well as nine sales companies. With such a global reach, Liebherr can get crucial components to customers quickly, saving precious time on site. Plus, using Liebherr components has the potential to provide cost of ownership benefits, as customers buy directly from the manufacturer, rather than from a dealer that receives the components from their supplier. Liebherr’s reputation for excellent aftermarket components is not limited to mining equipment. In fact, Liebherr components are also used in cranes, earthmoving machinery, wind turbines, automotive engineering and aviation and transport technology.
‘We are exceptionally proud of the work we do in the components product segment and are excited to see more customers in more industries experiencing the positive impact Liebherr components can have on their everyday activities,’ enthuses Palmer.