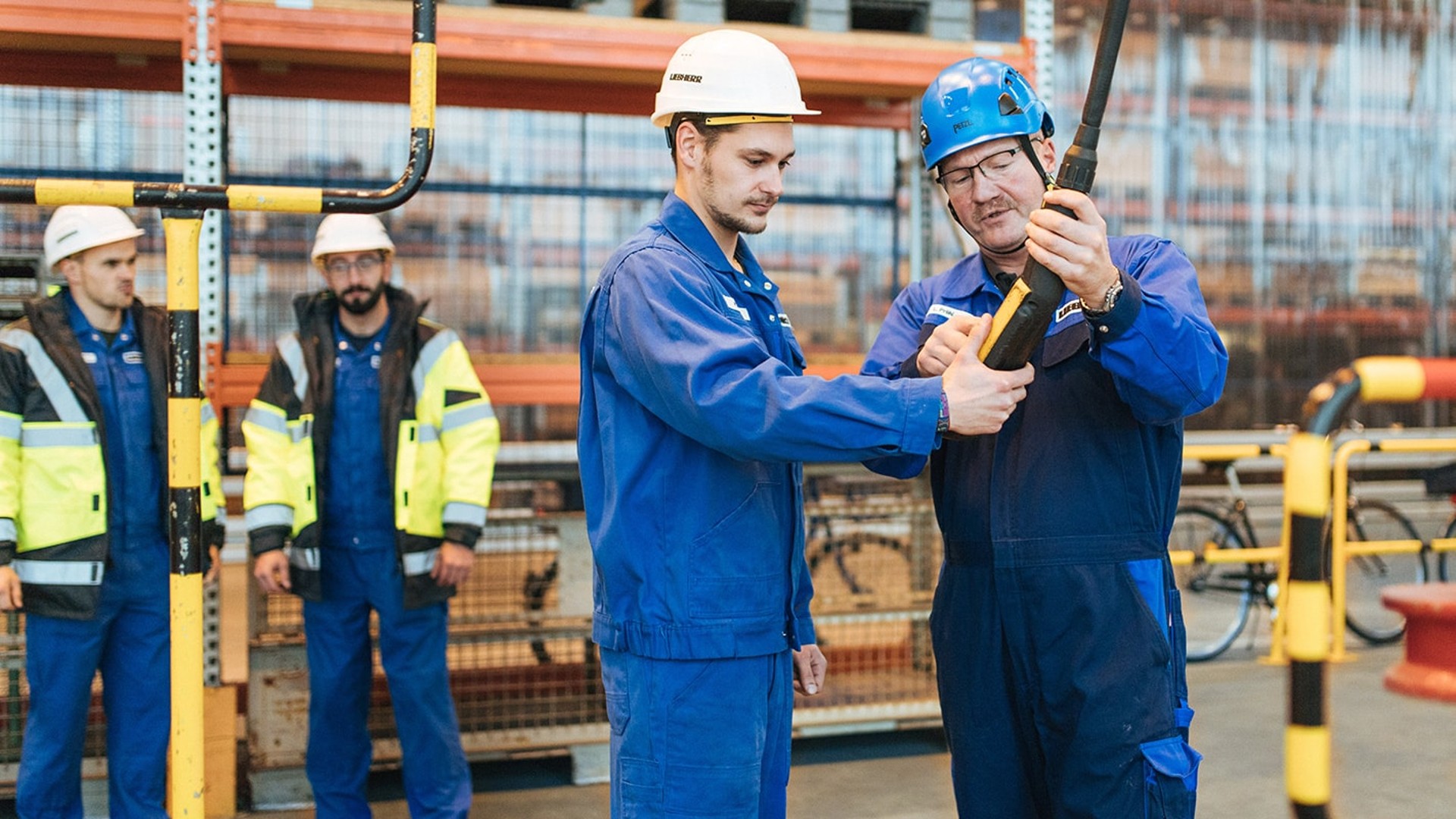
Skilled workers are made
Skilled workers and shortage – for many, these are two terms that invariably go hand in hand. At Liebherr, Lars Pröhl and his colleagues at the Liebherr Academy are already planning ahead.
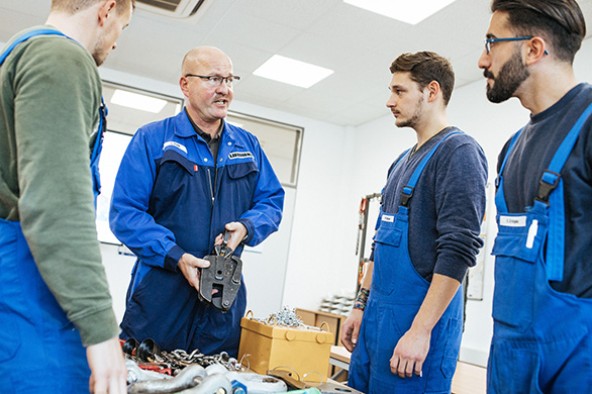
A daily routine that is different every time
Thursday morning in Rostock, Germany: three students are looking attentively at various items of lifting gear which are spread out in front of them on a classroom table. They are listening expectantly to their teacher. “Today, we will be learning about these crane parts,” explains Lars Pröhl with a firm, calm voice. This teaching unit with his apprentices is one with which the team coordinator is very familiar. Over the last 10 years he has taught 514, ranging from locals born and bred in Rostock to trainees from Romania, Spain or Afghanistan. “Every day is different, because every one of my trainees is different. As a result, the same lesson always turns out differently,” says the 56-year-old trainer. He has been at the Liebherr Academy, where 140 Liebherr trainees and around 30 apprentices from outside companies are currently learning about the technical and commercial aspects of mechanical engineering, since 2008. “Everyone can do something well. My job is to find out what that is for each individual trainee, using my professional knowledge and my understanding of people,” says Pröhl.
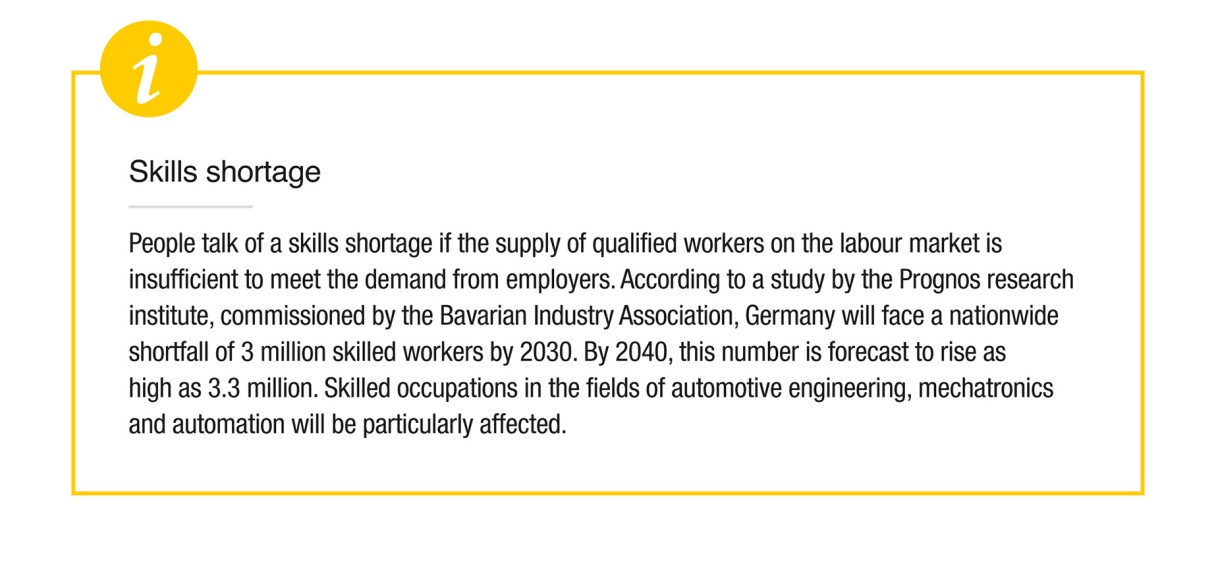
Chance or fate?
Pröhl’s own route to the Liebherr Academy was actually dictated more by chance than anything else. Through a former colleague in a refinery in southern Germany, he landed up working in mobile harbour crane production at the Liebherr plant in Nenzing (Austria) after he was no longer able to continue his work as a storekeeper in the offshore fisheries sector. Then, his responsibilities had included looking after all the technical equipment on board. During trips of up to 120 days at sea, he learned above all to cope with unexpected challenges and to work in close collaboration with the whole ship’s crew. This would also stand him in good stead later at Liebherr. “I was sceptical at first about whether this was going to be the right thing for me, always staying in the same place – never seeing any change. But I soon found that you can make things change here,” laughs the 56-year-old. He quickly recognised that skilled workers would be the most important but also the scarcest resource for companies of the future, including Liebherr. He was proved right. Today, Pröhl is not only responsible for coordinating three of the total of eleven training programs, but also carries out training himself in the specialist fields of hydraulics, crane engineering and materials handling technology.


Practice makes perfect
“Now be careful here…,” says the trainer, looking over Malte Hansen’s shoulder. The future mechatronics engineer is in the second year of his apprenticeship, and what he particularly likes about his training is the variety. Today, he is practising on a course containing various obstacles, learning how to transport loads in the production plant. With a look of concentration, Malte Hansen skilfully steers the crane hook past the obstacles – with Lars Pröhl constantly at his side. “Mr. Pröhl has supported us right from day one. He knows every crane here like the back of his hand – and us, too!” laughs Hansen. Pröhl then shows him how to attach a load to the crane hook and how to use the remote control to lift it evenly without the transport plate tilting. Since the first year of his apprenticeship, the 26-year-old trainee has been handling small projects in various disciplines such as electrical engineering or metalworking independently. As part of these, he has produced small crane models as well as actual tools and appliances for the Liebherr production plant.
Skilled workers don’t make themselves, skilled workers are made. If you want skilled workers, you have to train them.
From container to Academy
Pröhl is convinced that “skilled workers don’t make themselves, skilled workers are made. If you want skilled workers, you have to train them.” That is why, as long ago as 2005, he suggested setting up an in-house training facility that would provide training in precisely those occupations that were urgently in demand. It began in a small steel container with seven trainees – today the Liebherr Academy has training areas covering more than 10,500 square metres and provides training in eleven occupations. These range from mechanical design or cutting machine engineer to industrial electrical engineer or metal technology specialist.
The Academy has special practice areas for welding and is one of twelve recognised centres of competence for control and automation engineering and for CNC machining in Germany. This certification is awarded by Festo Didactic, a world-leading service provider in the area of technical education and skills development, to companies with particularly comprehensive technical facilities and experienced trainers. This is complemented by a 4,500-square-metre training area, which is integrated in the Liebherr-MCCtec Rostock production plant. Here, the trainees work directly on customer projects from the second year of their apprenticeship onwards and rotate through all the Maritime Cranes production areas.
The Liebherr Academy at a glance
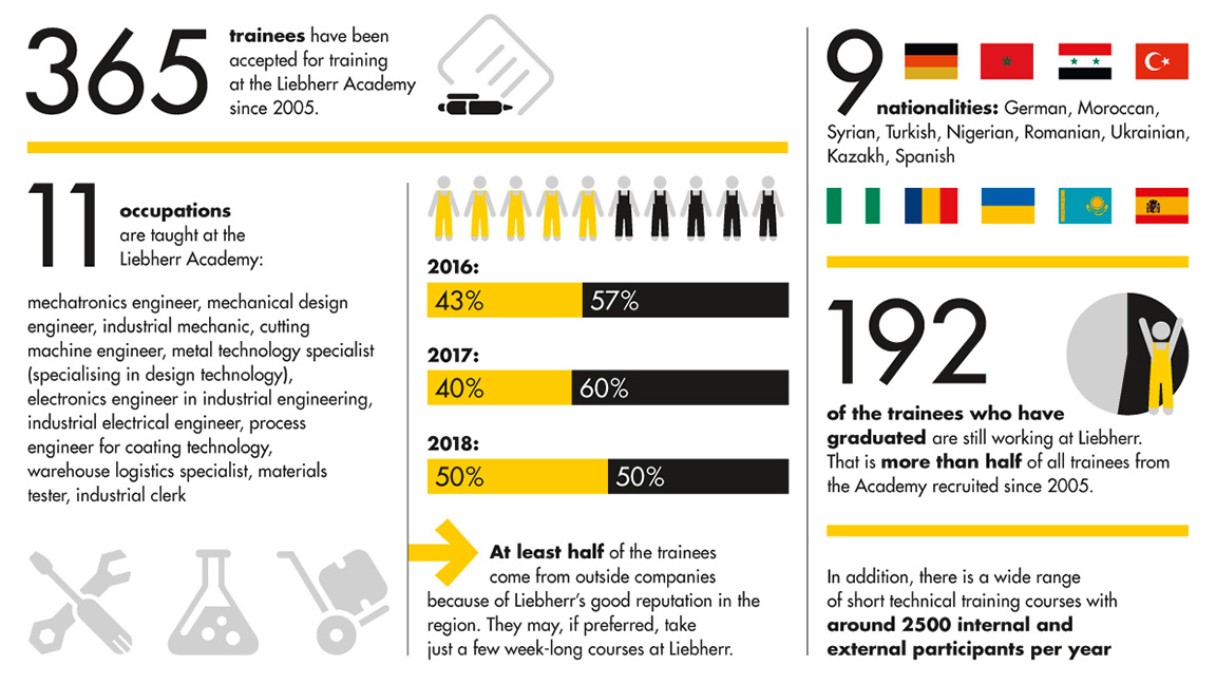
The skilled workers of tomorrow must be able to think and act flexibly and unconventionally. No machine will ever be able to take that away from us.
Looking forward
Increasing digitalisation and automation will bring new requirements for mechatronics engineers, mechanical design engineers, electronics engineers and many other occupations. These developments will impact on job profiles as well as on the relevant training. “Planning ahead is therefore vital. Our trainees will learn precisely those skills that they will need later in the company,” explains Ralf Harder, head of the Liebherr Academy. For him, this means in particular that trainees at Liebherr need to work even more intensively with machines. According to Harder, the latter will at some point largely take over assembly line work, while employees will have to depend primarily on their problem-solving skills and creativity. “The skilled workers of tomorrow must be able to think and act flexibly and unconventionally – for no machine will ever be able to take that away from us,” he says. To prepare apprentices for this as well as possible, the Academy is planning a pilot project, in collaboration with vocational schools, which will enable more flexible training through distance learning and project-based work. This development is welcomed by team coordinator Lars Pröhl: “I may not be building machines any more, but here, every day I am building the future of many young people – the skilled workers of tomorrow.”
* In order to guarantee better readability we only use the male form, with latter being representative of a gender-neutral designation. When doing so, we always address all gender identities (m/f/d).