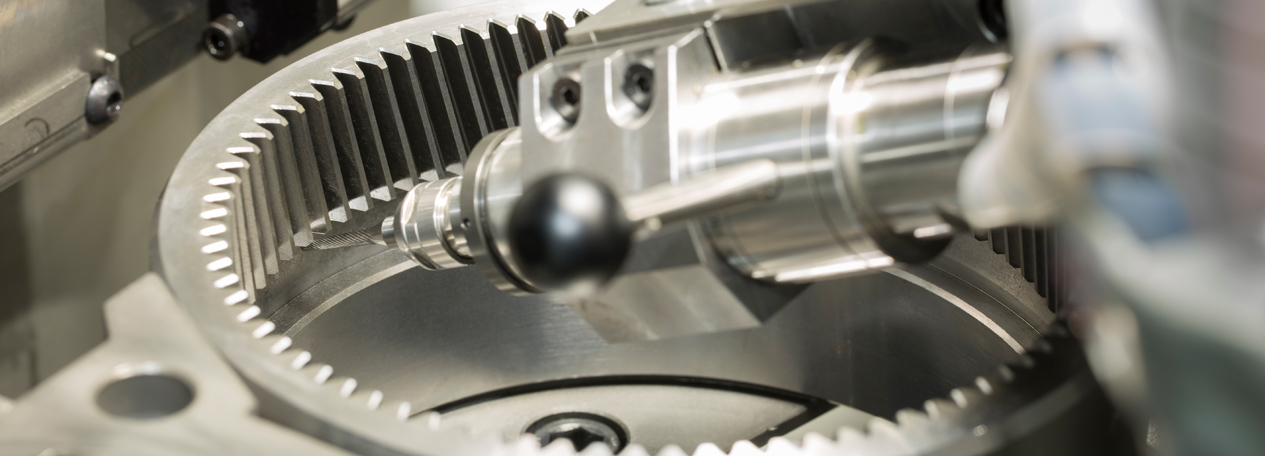
One tool for everything: flexible machining from A to Z
Anyone who manufactures small batch sizes of complex components wants to perform as many work steps as possible with a single machine. This not only saves time and equipment costs but also increases the quality, provided that the clamping fixture does not have to be changed. Liebherr-Verzahntechnik GmbH offers a comprehensive solution for complete machining by integrating a tool changing system and a chamfering device while using the turning, drilling and gear cutting functions of the latest generation of Siemens controls.
Machining a workpiece completely with a gear cutting machine necessitates four key elements:
- Flexible programming which enables a combination of gear cutting processes with turning, drilling or hobbing operations
- A tool changing system which accelerates the workflow over various sub-processes
- A utomated tool check and workflow correction
- A n intelligent distribution of primary and secondary processes
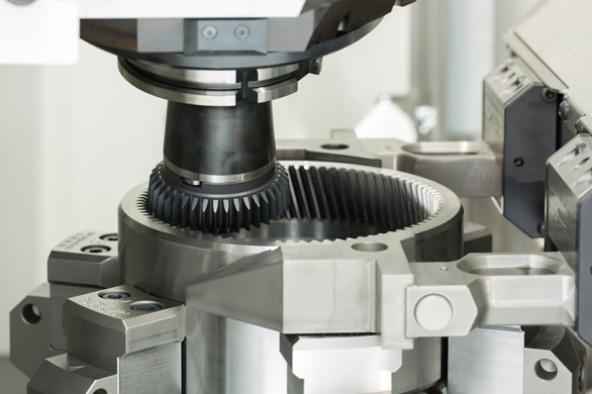
The system can accommodate twelve tools
Flexible programming with LHGearTec and programGUIDE
With the programming system LHGearTec and the new control panel LHStation, Liebherr offers a comprehensive operating concept to define gears with optimum efficiency and precision. When combined with the Siemens programming system programGUIDE, further contours can be programmed. Bores, slots, levelings, engravings and threads become a standard.
This enables us to achieve maximum flexibility at the same time as maximum precision, because the reference surfaces remain the same through all the machining steps.
Tool changing system with standard hollow shank taper
The Liebherr tool changing system can be used in various ways. Firstly, it makes the process more flexible and more efficient. This is because it can incorporate different gear cutting tools, even those specifically intended for roughing and finishing processes. This means that more expensive tools are only used where they are really necessary, thus saving money and extending tool life. Secondly, sister tools can also be accommodated to increase productivity. The remaining magazine stations accommodate up to twelve tools, allowing additional operations such as drilling, hobbing or turning in the same clamping fixture used for gear cutting processes. “This enables us to achieve maximum flexibility at the same time as maximum precision, because the reference surfaces remain the same through all the machining steps,” summarizes Dr. Peter Pruschek, Head of Electrical Design and Machine Control Development. “For specific application cases, this removes the need for an upstream turning machine or a downstream machining center.”
Deburring at the additional machining station
Flexible chamfering is a major topic, particularly for precision gears for e-mobility. However, comprehensive technological solutions enabling flexible chamfering are increasingly in demand for gears with interfering contours such as in the aerospace industry, as well. “Deburring gears is now pretty much the norm,” says Dr. Gerd Kotthoff, Head of Technology Gear Cutting. “However, many customers are now also demanding pre-defined chamfers on the front sides. That’s why, with ChamferCut and FlexChamfer, we offer the option of integrated chamfering units which deburr a second workpiece during the machining process, so that no time is lost.” Like the tool changing system, the chamfering device reduces the intralogistics to other machining processes and saves setup time. In the case of the new FlexChamfer unit, simple shank milling tools can be used here as well, replacing special deburring tools. “This enables us to obtain stable processes with optimum accuracy and minimal tool costs.”
Measuring and correcting inside and outside the machine
For extremely precise manufacturing, continuous quality control is indispensable. At Liebherr, the customer can select a number of different methods for this. While the gear cutting machines themselves perform a gear check on the basis of a measuring probe, complete measurement can also be carried out on a separate gear inspection machine. This is connected to the control system by the network. If errors should occur, the overall system can optimally support the user and can also activate corrections itself, depending on the configuration. “Until now, we have always spoken of a ‘closed loop’,” Peter Pruschek explains. “However, with the LHOpenConnect service portfolio, we can go beyond the closed loop to connect both our own products and measuring systems and control station solutions by other manufacturers via open interfaces. Measuring data only constitute a small part of the process data which we connect and use to optimize the entire process.” The services bundled within LHOpenConnect, as well as the associated Industry 4.0 software products summarized by the term LHWebPlatform, are presented in detail in this article.
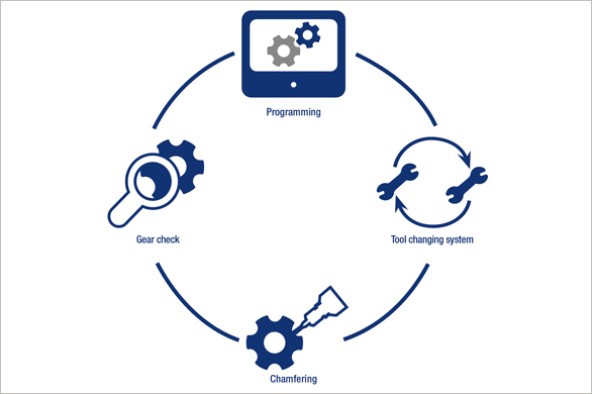
Flexible and accurate: An overview
Gear cutting in combination with chamfering, additional machining options and tool changing system in a closed quality loop
- LHGearTec with Siemens programGUIDE: Flexible programming of complete machining processes
- Tool changing system: Roughing and finishing, sister tools for longer tool life and unsupervised manufacturing, and additional machining such as turning, drilling or hobbing using a hollow shank taper
- FlexChamfer and ChamferCut:Very high quality deburring and chamfering during the machining process
- Gear check: Measuring during the machining process with the possibility of correction