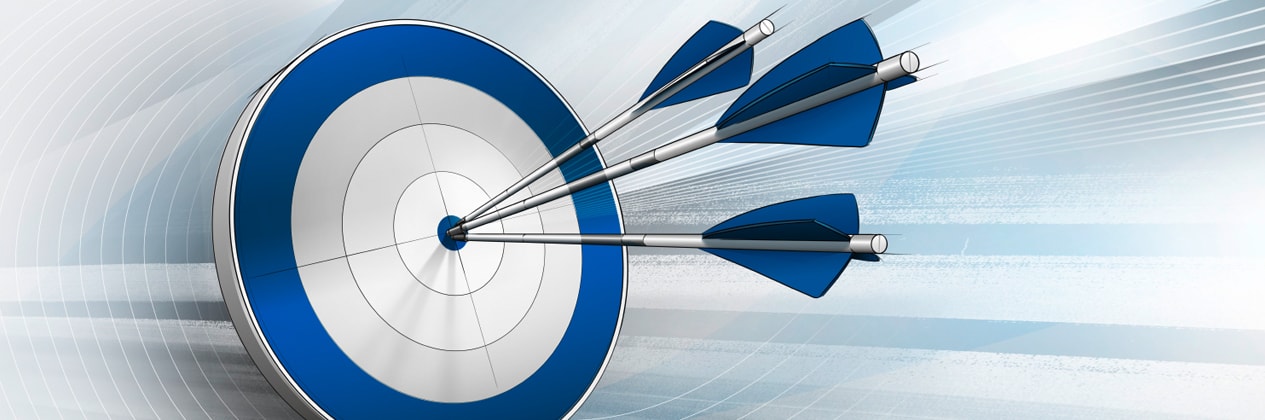
Magazine 2020
Magazine 2020
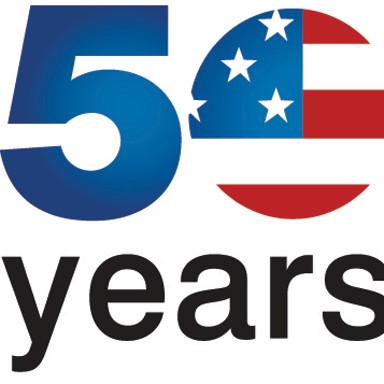
Liebherr in the United States is proud to celebrate five decades in North America and establish itself as a leading manufacturer. Liebherr has built its U.S. business on a foundation of trust, innovation and engagement with customers. Five decades later, Liebherr’s growth, diversity and stability are evidence of how the company is united by success with customers as they work on the challenges of tomorrow and focus on the future together.
Most read
01
In August 2019, trainees Fabian Altenried and Julia Fetzer participated in the Liebherr Summer Program at Liebherr Gear Technology Inc. / Liebherr Automation Systems Co. (LGT / LAU) in Saline, near Detroit. There, they ran the PLC programming course for pupils of the robotics course from the local high school, which was offered for the first time, and got to know the work routine at the Liebherr site. Fabian reports on his experience here:
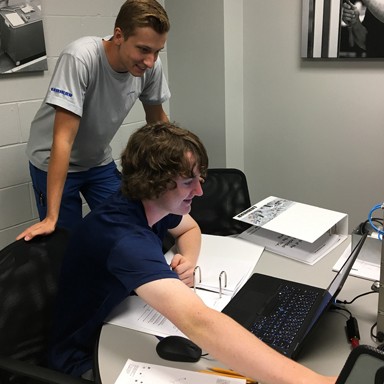
02
Liebherr presents the new series of generating and profile grinding machines for hard machining of external and internal gears on workpieces with diameters of up to 500 millimeters. The LGG series follows the successful Liebherr LCS 300 to 500 series. With an impressive range of added features, they offer more flexibility and grinding performance with a significantly reduced footprint.
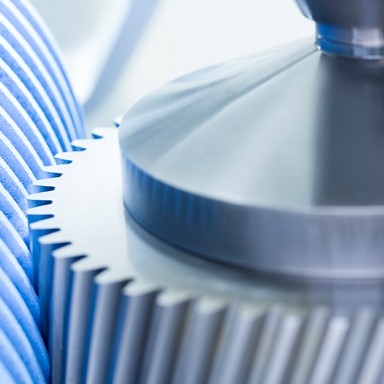
03
Gear skiving is over 100 years old and has recently been experiencing a renaissance as a flexible and economical alternative to other gear cutting methods. However, this complex process frequently presents great challenges to users. In addition to Skiving3, a “complete package” consisting of machine, tool and technology, Liebherr now also offers skiving tools for suppliers and contract gear manufacturers – and the appropriate consultation, if desired.
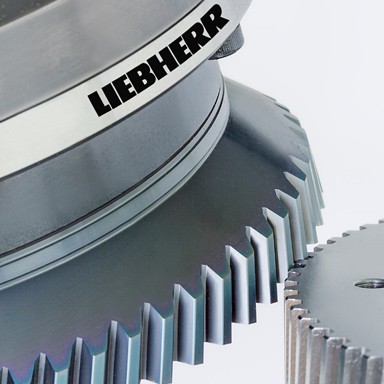
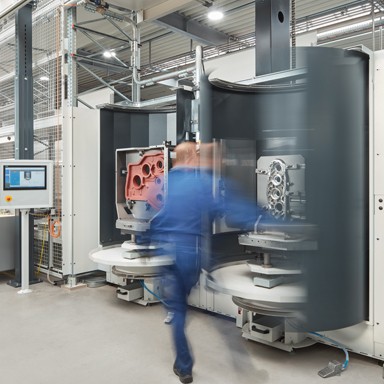
How can we ensure maximum manufacturing productivity? What is the best automation system for our wide variety of parts? Which partner can reliably put our plans and requirements into practice? These are the kinds of questions that every manufacturing company aiming to increase its productivity has to ask. Kordel Antriebstechnik GmbH, based in the Westphalian town of Dülmen, found the right solution for its gearbox production with a pallet handling system from Liebherr.
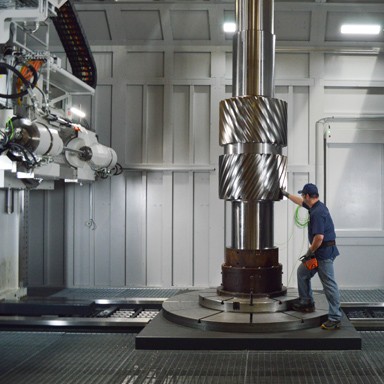
A visit to the HMC Gears plant in Indiana kicked off an extensive project which resulted in the creation of a unique solution for exceptional demands: With the LC 4000, Liebherr forges new paths in large-scale gear cutting production and unites diverse machining methods in one highly efficient machine for the American gear specialist.
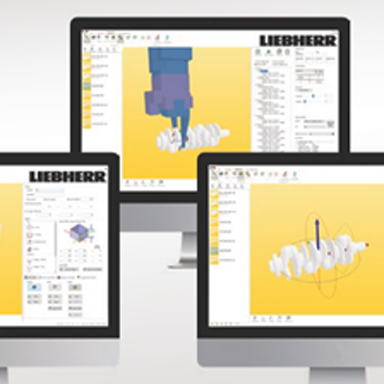
Until now, Liebherr has provided Bin Picking solutions with software supplied by a partner. Now the company offers its exclusive software package with new features that can also be integrated into systems from other manufacturers. Liebherr’s combined expertise in software development and industrial application also makes LHRobotics an interesting product for integrators.
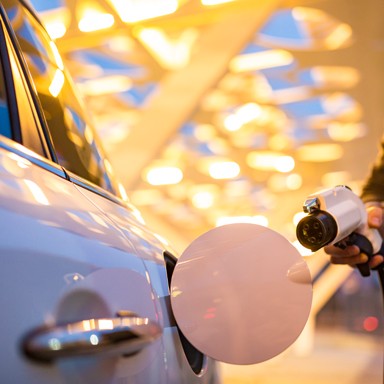
Liebherr is embracing technological change towards alternative drives and has developed a modular automation system solution for the assembly of battery packs for electric cars – from small batch manufacturing to fully automated mass production. Advantages: Liebherr automation is system-compatible and offers process reliability, fast cycle times and flexibility.
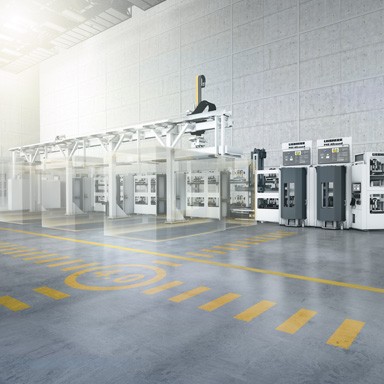
Liebherr presents the latest member in the PHS Allround family, the PHS 800 Allround. It has a narrower design than the PHS 1500 Allround, which makes it ideal for automated loading of smaller machine tools while retaining the basic principle of modular design and universal applicability and expandability.
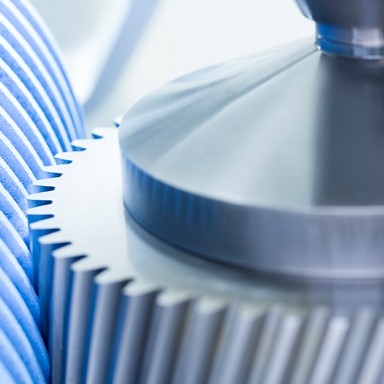
Liebherr presents the new series of generating and profile grinding machines for hard machining of external and internal gears on workpieces with diameters of up to 500 millimeters. The LGG series follows the successful Liebherr LCS 300 to 500 series. With an impressive range of added features, they offer more flexibility and grinding performance with a significantly reduced footprint.
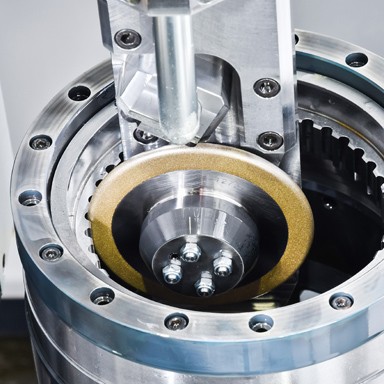
x
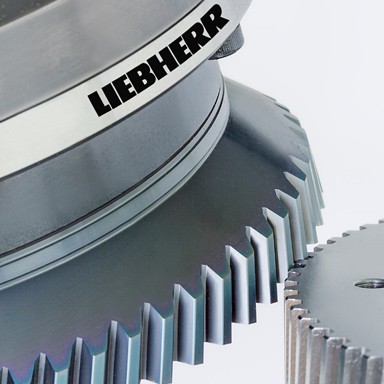
Gear skiving is over 100 years old and has recently been experiencing a renaissance as a flexible and economical alternative to other gear cutting methods. However, this complex process frequently presents great challenges to users. In addition to Skiving3, a “complete package” consisting of machine, tool and technology, Liebherr now also offers skiving tools for suppliers and contract gear manufacturers – and the appropriate consultation, if desired.