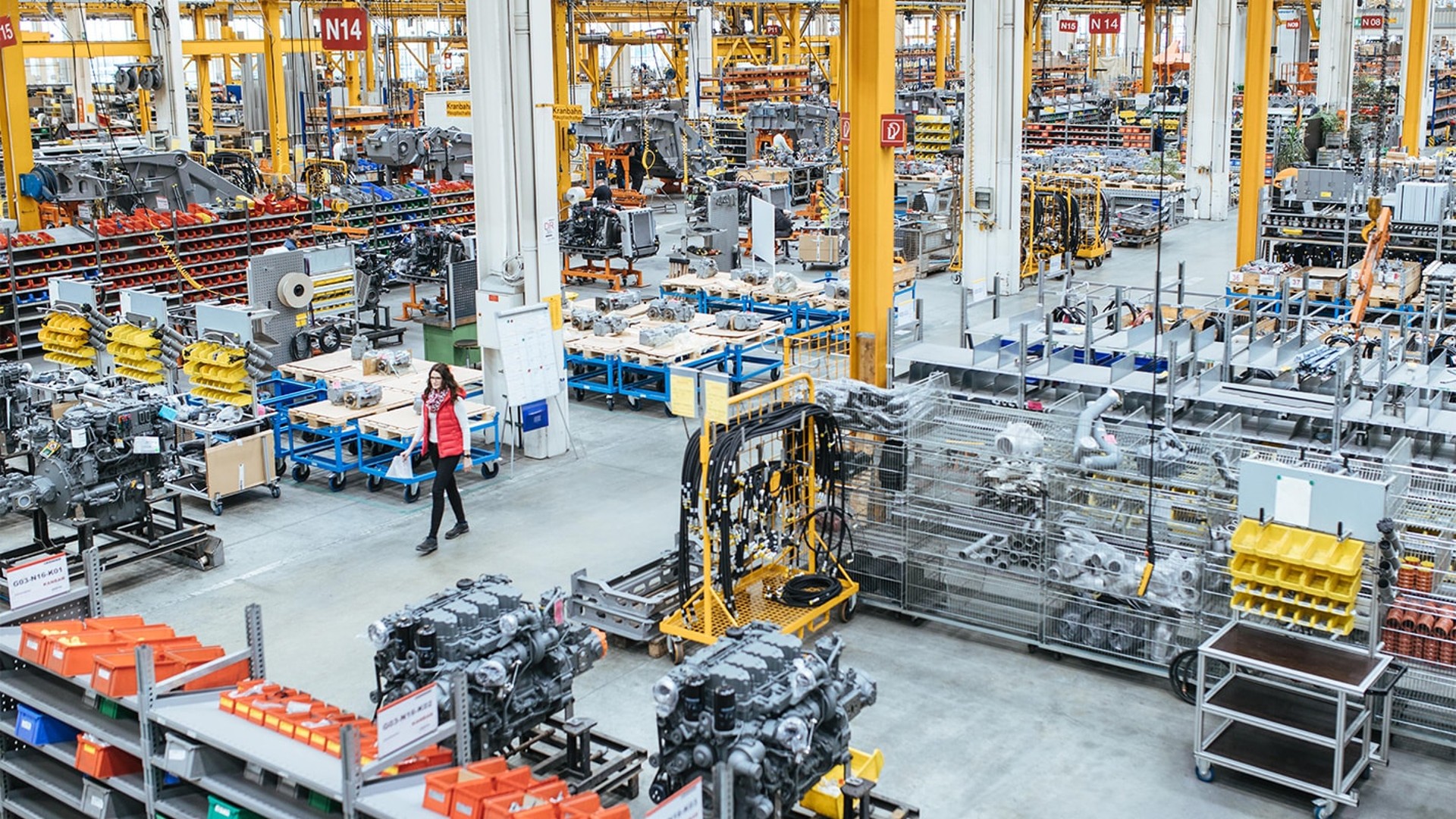
6 minutes reading time
Keeping the belt running
Configurations, sometimes even during ongoing assembly, are a service that customers appreciate in Liebherr mobile cranes. But who makes sure that the cranes are delivered as planned? A visit to Liebherr-Werk Ehingen, where Isabell Blaser and her team keep an eye on everything during the final assembly of the upper carriages.
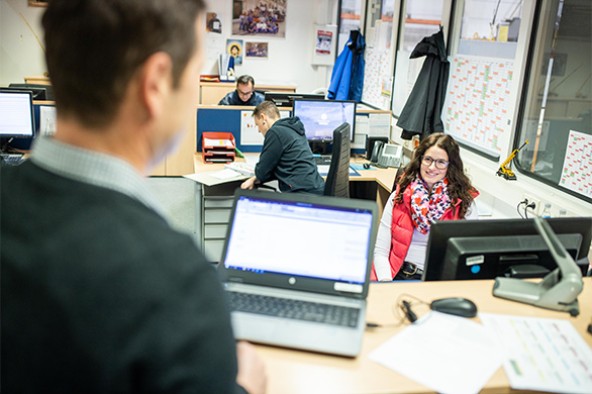
A morning on Belt N
It’s 7 a.m.: Andreas Osswald, the department head of the mobile crane final assembly and completion for upper carriages has gathered his team of nine team leaders. They meet every Monday and Tuesday, check whether all is on order and talk about the tasks and possible changes. It is them who make sure that up to eight complete mobile cranes can roll off the belt and to their new owners every day.
This means that everybody in the control station always speaks openly - in the local German dialect that many at Liebherr speak: Swabian. They know and like each other. On the shelf behind their desks, skiing trophies are lined up. A faded advent calendar shows the young Diego Maradonna with a halo. None of the doors has ever been opened. Typical men, you might think. If it wasn't for Isabell Blaser. The 27-year-old controls belt N with 25 employees in the pre-assembly of the upper carriages. This is where hoist gears, hydraulic components, motors, pump distributor gears, oil tanks, fuel tanks, storage boxes and battery boxes are assembled. Everything is going according to plan," she reports to the crew, “Two people have called in sick with the flu so we’re working with stand-ins.”
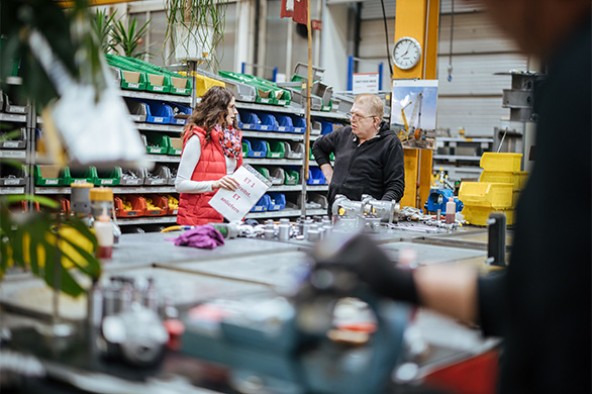
Between palms and spare parts
As the team leader, Isabell has extensive organizational and personnel management tasks and also acts as the interface to sales. “We regularly have ad-hoc customer configurations coming in,” she says. “The most common additional orders are hoist gear II, supplement oil coolers and folding jibs.” For Isabell, such short-notice modifications, even while a machine is already in assembly, are nothing unusual. But when they do come in, they mean work. Do the customer's changes mean that an already completed hoist has to be reconfigured again? And can this be done in a few hours including the order for spare parts? "Of course we have to make sure that the crane is delivered as requested."
While she speaks, the first email of the day arrives. It’s from the logistics department. An incorrect filter type was delivered because of a number twister. Isabelle's team has to pre-assemble exactly this filter so that the belt can then build it into the upper carriage. “I have to be quick now. The belt cannot stop.” But where is the filter? In the computer system, Isabell searches for the delivery and picking number, writes the numbers out and goes on a search. She is lucky, the filter has not yet been assembled and is lying on a picking cart. Isabell removes it directly from circulation and orders the replacement via the system.
Then she's off to the assembly station for which the filter was intended. It resembles a small jungle in the midst of steel struts and screws, which the Belt N employees look after with dedication. Between yucca palms and a monstera, Isabell and her employee Matthias Zinke discuss the next steps. Will waiting for the right filter affect the workflow? No, he assures her, everything will run smoothly.
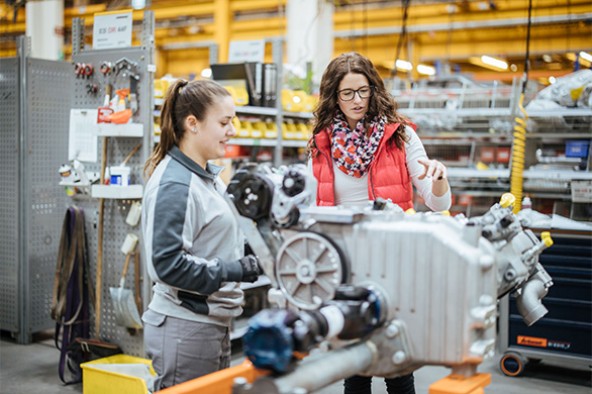
At home in production
Isabell knows that she can always rely on her employees and their experience in pre-assembly. Like them, she worked in the adjacent completion department in the final assembly. “Big machines and technology have always fascinated me,” she says. After finishing secondary school, she started an apprenticeship as a mechatronics engineer at Liebherr-Werk Ehingen. She never minded that she was the only woman in her year. “In my line of work, you need to be able to rely on your colleagues – it doesn’t matter if your male or female.” In 2014, one year after graduating, Isabell registered for a part-time training course to become a state-certified technician. For four years, she went to school three times a week alongside her job. Saturdays too. “When I told my supervisor it triggered an all-around positive echo. I got all the support I needed to make the transition from the workbench to team leader.”
Today, she passes on her knowledge and enthusiasm for production to her team. Also to Carina Glanz, the latest addition to the team. Under the watchful eye of her instructor, the young woman is working with great concentration on a pump distributor gear. She thinks it's great that the boss takes the time to talk to her and give her tips.
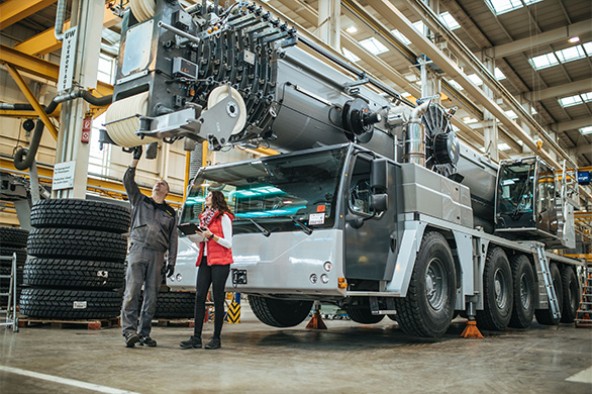
Quality down to the smallest hex nut
The belt is running and her team is happy. The first upper carriages float on large cranes through the factory hall. They are on their way to the marriage with their undercarriages. Now, Isabell has time for her next task. Every two weeks, in addition to the constantly running quality checks, a fully assembled mobile crane is randomly selected in the final assembly department and checked for quality. The team leaders take turns. Together with skilled worker Andreas Seifert, Isabell gets down to work. They inspect every cable, every screw, and every hydraulic hose. Is everything in place? Has everything been installed according to regulations? Does anything need to be reworked? Isabell takes down all her findings in a checklist, which is reminiscent of the ones airplane pilots use before take-off. The voluntary self-check takes almost an hour. Then comes her thumbs-up. The mobile crane is ready for its first trip out of the production hall on to the vehicle safety test, then the paint shop and eventually to its owner somewhere in the world.
“That’s my personal highlight. When our customers are happy with their mobile crane,” says Isabell. “We do it so well because we are a well-rehearsed team, well-positioned and very flexible.” And this is what makes every one of Isabell’s days special.