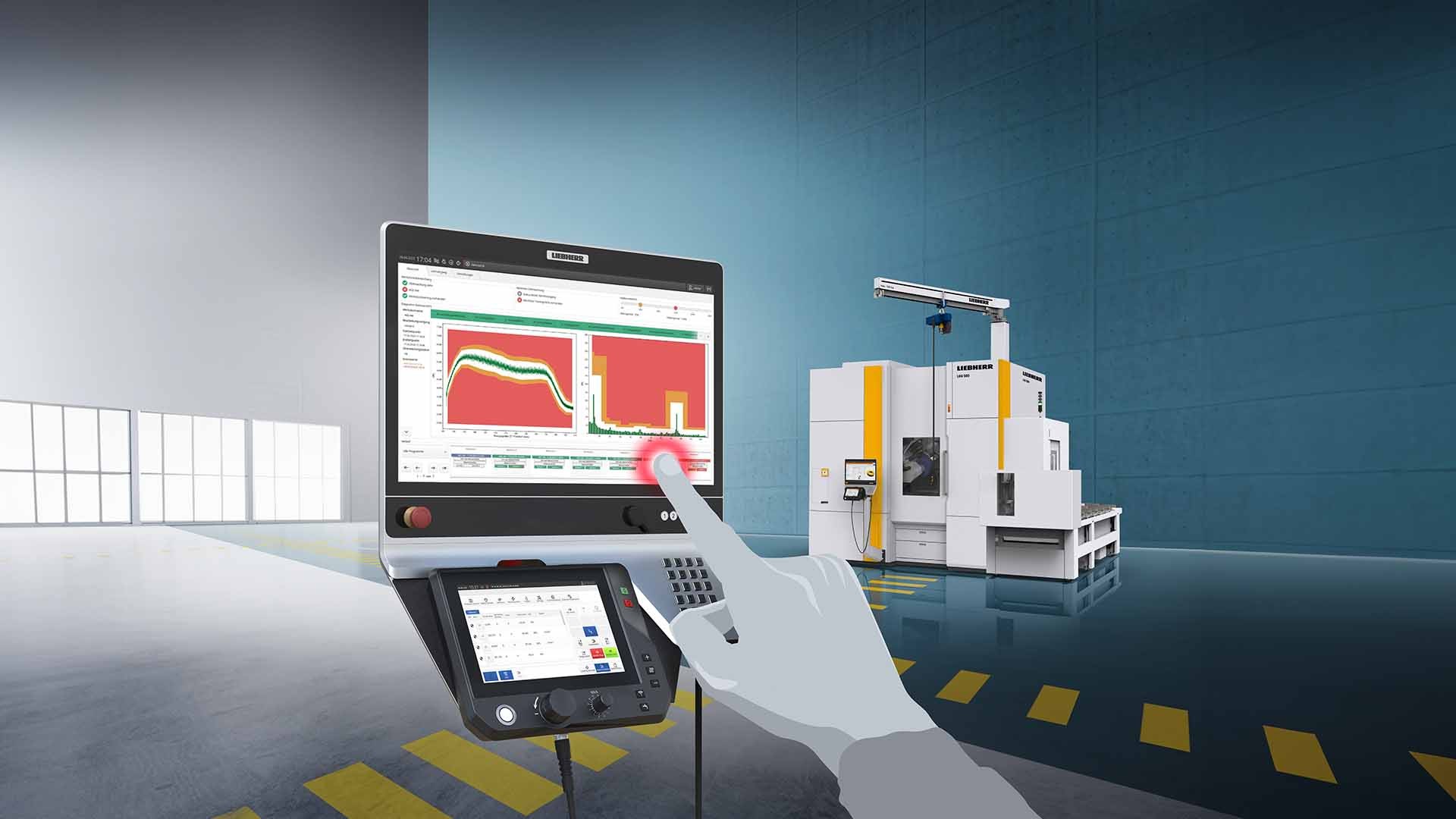
Inline process monitoring with LHProcessMonitoring
In electric vehicles, the meshing of the gears can cause disruptive gearbox noise excitations. It is therefore becoming increasingly important for automotive manufacturers and suppliers of electric motors to identify and eliminate the causes of unwanted noise at an early stage. With the LHProcessMonitoring software, Liebherr-Verzahntechnik GmbH has developed a tool that detects deviations during gear production. This saves costs and reduces rejects – and is therefore also of interest to manufacturers of conventional gearboxes.
The NVH (noise-vibration-harshness) behavior of a vehicle is significantly affected by the quality of the gears used. This makes it all the more important to detect anomalies in the micro-geometry of the tooth flanks at an early stage – and manufacturers are increasingly emphasizing this too. If noise abnormalities are only detected at the end-of-line (EoL) test bench, it is usually too late, and can be very costly to rectify. Ideally, deviations should be detected when the gears are being produced.
Digital tool for e-mobility
The LHProcessMonitoring software from Liebherr-Verzahntechnik GmbH for inline process monitoring visualizes the manufacturing process and uses the data obtained to determine limit values in the form of envelope curves, which are used to check the manufacturing process. These can then help identify any deviations that could lead to noise anomalies. The software is optionally available as part of the LHGearTec operating and programming interface, and is therefore “the logical continuation and expansion of our product portfolio of digitalization modules with a focus on e-mobility,” says Florian Schuon, Head of Digital Solutions at Liebherr-Verzahntechnik GmbH.
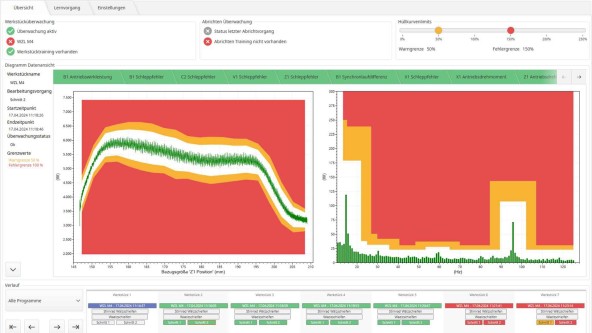
Clear visualization of parameters, warnings and limit violations
Detecting deviations at an early stage
Thanks to continuous recording and transparent evaluation, the software enables the operator to optimize and stabilize the manufacturing process. Limit violations are automatically detected, and do not enter the value chain. LHProcessMonitoring ensures the consistent quality of each individual gear and can replace a downstream full inspection that uses a single flank gear testing system or master gear, which in turn saves investment and set-up costs – all at a comparatively low investment. At the same time, a significantly higher degree of accuracy is achieved. “It's often only at the end of the supply chain that you realize something is wrong. Our software improves the traceability of parts at an early stage, not just during the EoL inspection. Manufacturers of conventional gearboxes also benefit from the improved gear quality,” says Schuon, explaining the advantages of the software.
Dynamic envelope curve analysis
Like the LHGearTec, the LHProcessMonitoring software also has an intuitive graphical user interface. It evaluates the parameters of the drive motors, and limit values can be easily set using a slider. Dynamic envelope curves indicate warnings or stops in the event of limit value violations, while signals from individual parameters such asmotor position, power and torque allow direct conclusions to be drawn about the source of the fault. The machine is “trained” using reference parts and immediately informs the operator of any deviations or anomalies, so that faulty parts don’t make it to the EoL test stage. The software is initially available for grinding and can also be used for dressing. In the future, it will also be extended to other gear cutting methods.