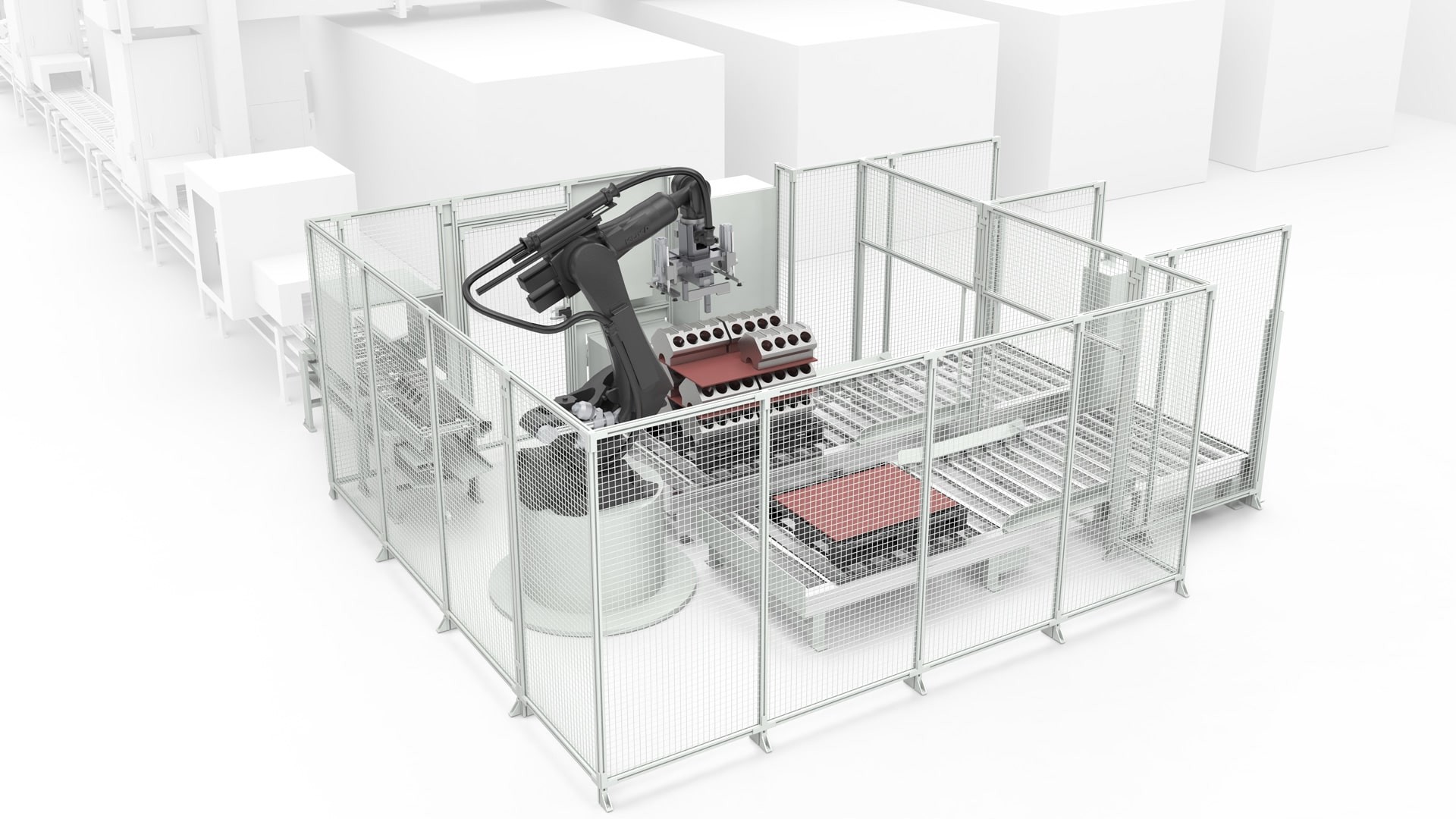
Automated line inputs and outputs
Due to the electrification of automotive fleets, there is no doubt among experts that growth in combustion technology will come to a halt. This will result in increased cost pressure on the current production capacities. A simple retrofitting solution by Liebherr for automated raw part input and finished part removal helps to make full use of productivity reserves.
The manufacturing lines for components of combustion engines, such as engine block, cylinder head and gearbox housing, are usually fully automated. However, a number of manufacturers worldwide continue to load and unload material or parts manually. For the operators, this is monotonous and heavy work.
Efficient pick-and-place solution by Liebherr
Particularly in high-wage countries, automation in this area would quickly pay off, but automated machine loading is also an interesting option in low-wage countries. In the inexpensive and space-saving Pick-and-Place solution by Liebherr, components are added to the line in blisters or on pallets. A robot then grips the parts and feeds them into the line. At the end of line, the process takes place in the opposite order. In the case of simple applications – for example, for pre-sorted workpieces in blisters or frameworks – such a solution can be designed with process reliability without the use of vision systems.
Liebherr solves more complex depalletization tasks in which, for example, the orientation of the workpiece varies due to tilting, using 2D or 3D robot vision systems. To evaluate 3D images, the proven Liebherr software LHRobotics.Vision is used in a reduced variant (more information here).
Easy retrofitting for lines by other manufacturers as well
This means that highly-qualified employees can be used for value-creating tasks, while unproductive process idle times are eliminated and lightly-manned manufacturing can be expanded. Further-reaching solutions, right up to completely unmanned manufacturing (“lights-out production”) are also possible. The use of transverse shuttles to optimize the loading cycle or the connection of an automated guided vehicle (AGV) are also conceivable. Since the robot cells are a closed unit, Liebherr’s solution can also be applied to manufacturing lines by other manufacturers.
Concept also suitable for e-mobility parts
The concept can also be applied to manufacturing lines for e-mobility. Particularly in battery pack assembly, large, heavy workpieces such as battery trays or modules are processed. Viktor Bayrhof, Market Sales and Product Management for automation systems at Liebherr, sees future application potential here: “„In existing production facilities, space is usually very limited. Liebherr has developed a simple, inexpensive, custom-fit retrofitting solution which is also suitable for further automation in e-mobility.”