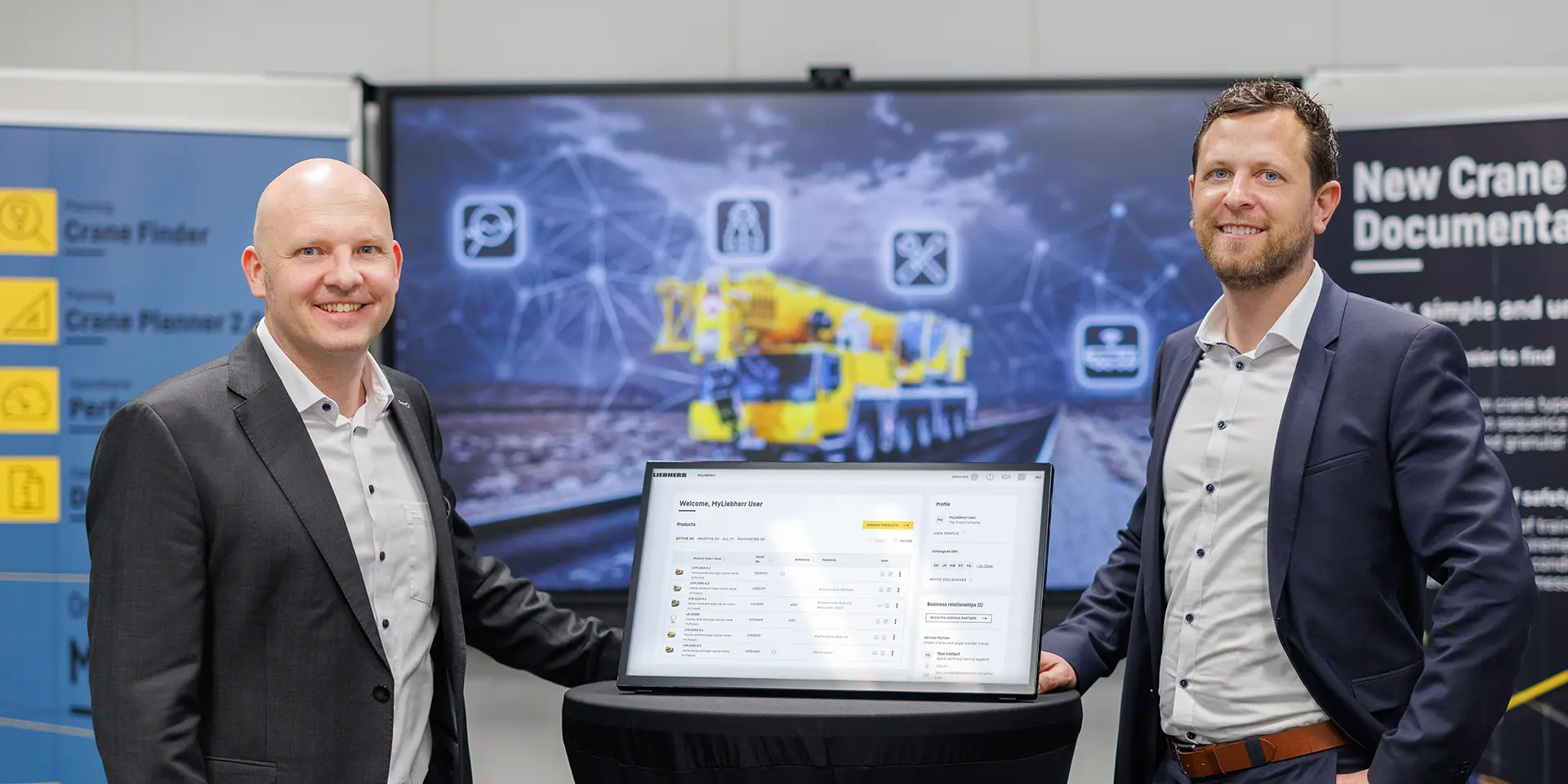
Game changer digitalisation: from ego to ecosystem
The worlds in which we live and work are continually transforming. Within this, digitalisation is a megatrend that Liebherr is using to create innovations – across multiple product segments. There is a particular focus on tailor-made, sustainable solutions with measurable added value for customers, for example with greater process efficiency or the conservation of precious resources.
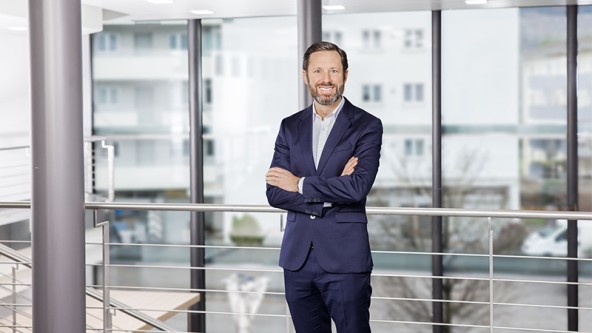
Stephen Albrecht is managing director at Liebherr-International AG
Aristotle once said that the whole is greater than the sum of its parts. In the age of digital transformation, this insight takes on a whole new dimension. ‘The focus is no longer just on the technological excellence of devices and machines. Today, we focus much more on the entire value chain for customers and users of Liebherr solutions. It’s all about concrete, measurable added value that comes from digitalisation’, explains Stephen Albrecht, managing director at Liebherr-International AG. Ever better opportunities for data capture and analysis would pave the way to this. ‘Augmented products with application scenarios that can be experienced and optimised digitally enable this added value to be seen in a different, much brighter light. And, not least, they can also contribute to decarbonisation.’
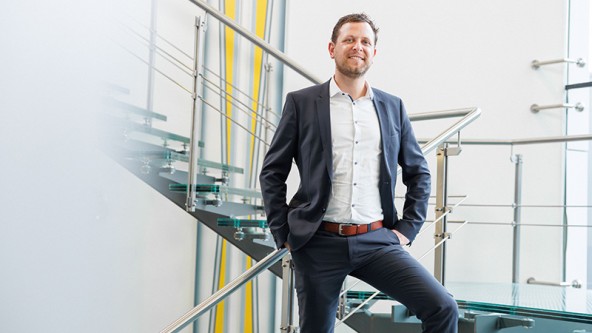
Marcel Flir is head of digital business and strategy at the Liebherr Group
Thinking about technology and measurable added value for customers from such a holistic perspective is second nature to Marcel Flir. The skilled environmental and process engineer with a qualification in industrial engineering spent several years building the digital business at the Liebherr site in Nenzing (Austria) and was also responsible for leading the product management for digital solutions there. He is now head of digital business and strategy for the Liebherr Group. The focus here is on identifying and exploiting synergies in Liebherr’s digital solutions, which extend across all 13 product segments and all parts of the customer journey. This includes, for example, operational planning, maintenance management, digital inventory management, smart home integration and organisational matters.
For Liebherr, digitalisation is not a new trend that is only just being discovered and inspiring innovation. Development engineers at Liebherr have been working on how to capture, record and transfer machine and process data since the mid-1990s in order to use this data for greater product optimisation and emissions reductions. ‘Back then, the time of user-friendly data management hadn’t arrived yet – with 56k modems, the stream of data first had to be painstakingly threaded through a digital eye of a needle’, says Marcel Flir. At the same time, remote maintenance and remote access to controls and components were quickly gaining importance for Liebherr devices, which are exported all over the world, and there was demand for relevant solutions.
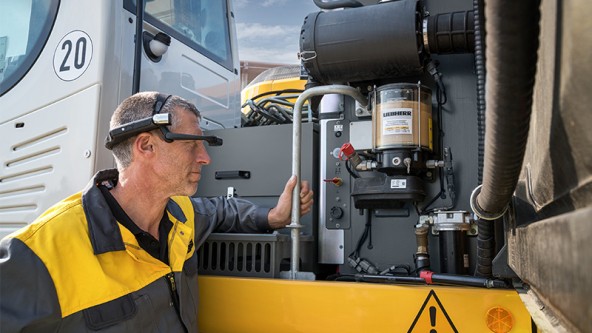
The Remote Service tool includes comprehensive digital services that provide support in service and maintenance cases
Today, specialists at Liebherr work on digital innovations across all product segments – and on connecting the constantly evolving options, machines, refrigerators or components to the associated systems. ‘We have several hundred digital solutions in the field, from APIs to IoT solutions and training simulators – and more are on the way of course’, says Stephen Albrecht. The development departments in the Liebherr product segments shouldn’t need to completely rework the relevant digital basis every time. ‘We seek out and utilise synergies wherever they make sense. To do this, we call on proven standards and system interfaces – with data security, data governance and cybersecurity in general playing a central role, along with the use of established modules. Overall, we drastically reduce the time to market, while also offering our customers ISO 27001-certified digital solutions and services’, explains Marcel Flir.
Finding the best solution together
Digitalisation is not an end in itself for Liebherr – it needs to be internalised, accepted and practised in day-to-day work. ‘We don’t need to be the first with a solution in the field – instead, we discuss the opportunities and risks associated with digitalisation in-depth with our employees, stakeholders, customers and partners and talk about how we can reach the best and most sustainable solutions together. This is an interdisciplinary approach that listens to every voice that is actively involved in the solution process’, says Marcel Flir, describing the Liebherr route to digitalisation.
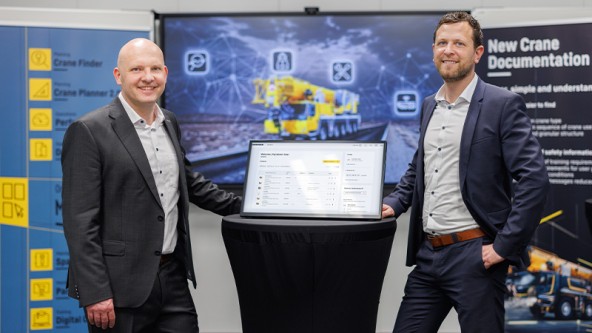
The cooperation in the technology and digitalisation work ensures that innovation will continue to be at the heart of Liebherr’s activities. Marcel Flir and Stephan Schrade, head of digital products and services at Liebherr-Werk Ehingen GmbH, during a joint conference.
‘It depends greatly on how we handle data ourselves’, says Stephen Albrecht. He describes how the focus is always on ‘improving the customers’ processes and the efficiency of how they use their products’. This includes, for example, preparing ways to integrate partner data into the digital ecosystem or to deal with different legal frameworks around the world in the context of digitalisation. ‘It would be wonderful for data to already be interoperable and useable across manufacturers’, says Flir. This demands a certain mindset.
‘Going it alone is a thing of the past. Customers, manufacturers, associations and providers of solutions are all in the same boat when it comes to adding value and achieving the decarbonisation targets that are now needed. We are bringing a real paradigm shift to the table: out with the egosystem, in with the ecosystem’, sums up Marcel Flir. ‘So things that belong together grow together.’
MyLiebherr – one customer portal for all
One example of this holistic perspective is the MyLiebherr customer portal. ‘It is the main gateway to Liebherr’s digital world’, says Marcel Flir. ‘MyLiebherr started out as a spare parts portal. We then gradually expanded the application fields in an iterative process and so created a hub that now has over 125,000 active users and over 60,000 customers.’ Users can now book online training for professionals or buy licences or spare parts. It also offers applications for planning crane lifts, site monitoring and integrated functionalities for machine and maintenance information. In other words, MyLiebherr enables users to access the entire digital world of Liebherr with just a few clicks.
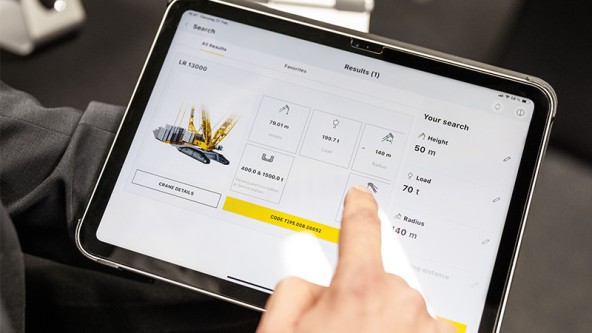
The MyLiebherr customer portal has long since become much more than a spare parts portal. It is the central gateway to Liebherr’s digital world.
The customer portal not only offers comprehensive services, but is also a building block for enhancing Liebherr products and services with further functionalities as part of end-to-end digitalisation. Stephen Albrecht explains: ‘Because in technology development we have everything on our plan – from the idea, production and service through to discontinuation and recycling – and this creates many opportunities for us. For example, the data that a technician records at one site when reconditioning used components can be made available to development engineers at another site. Digitalisation can therefore help us to make our products even more robust and efficient right from the development stage.’
Pooled digital expertise
In all of this, the Liebherr Digital Development Center, based in Ulm (Germany), takes on the role of an enabler. It has been working continually on technology and digitalisation since 2020, based on the needs of the customers. ‘With the Digital Development Center, we have created the basis for digital solutions that we roll out to the market in our product segments. As an internal service partner, it covers the entire digital chain – contributing extensive knowledge in the areas of IoT, cloud solutions, data science and mobile applications and sharing this with the product segments. This speeds up our development and helps us to standardise digital technologies Liebherr-wide’, explains Stephen Albrecht.
The Liebherr Digital Development Center in profile
The Liebherr Digital Development Center was founded in 2020 to provide all product segments within the Liebherr Group with digital products based on cloud and IoT connectivity, as well as data and AI integration. This creates digital solutions for the future, which in turn improve efficiency, value and customer service for Liebherr products.
The Digital Development Center focuses on three core objectives in particular:
1) Improving the speed and efficiency of digital development within the Group
2) Supporting the standardisation of digital technologies within Liebherr
3) Attracting and retaining talent for digital development
The team
At the Science Park in Ulm (Germany), a diverse team of software engineers, data science specialists, cybersecurity experts and AI enthusiasts works on digital development for the whole group of companies. There are around 85 employees (correct as of March 2024) from a range of sectors, some with up to 25 years of experience.
The methods
Agile work, fail-fast approach, rapid prototyping, data-driven decisions to improve production processes.
Customer-specific solutions in focus
Supporting customers as a partner in digital transformation and therefore also creating prospects with a view to sustainable development, is also useful in the development of drivetrains, for example.
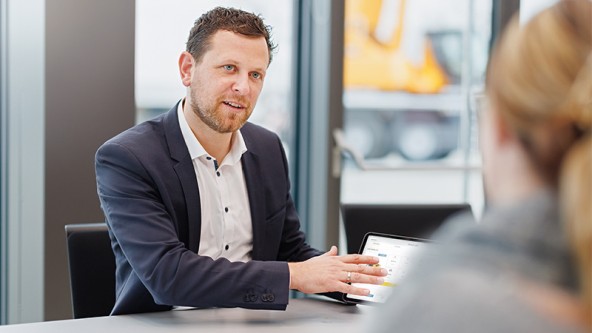
User-specific data is important for decarbonisation. Marcel Flir tells a customer how real operating data can be used.
‘Electrification is not about transferring the performance capability of a diesel unit to an electric drive one-to-one’, says Stephen Albrecht. He believes it is much more important to find out what the customer is actually using their machine for in day-to-day operations. ‘As we are able to capture real operating data and transmit it from our telematics units, we can now optimise the design of the battery and electric powertrain to meet customer requirements. And we don’t always need to stick 100 % to the performance parameters that were originally applied to a conventional drive.’ Another advantage: by incorporating such user-specific data, the Liebherr digital experts and the development engineers are also helping to accelerate the introduction of CO2-optimised machines.
‘Liebherr has the skills, the determination and the vision to achieve great things, because we cover the entire digital chain and aim to create complete ecosystems of our applications with our digital solutions’, adds Stephen Albrecht. ‘We haven’t reached the finish line yet in these transformative times, but we are on a very, very good path.’
1. In which German city is the Liebherr Digital Development Center based?
a. Ulm
b. Kirchdorf an der Iller
c. Stuttgart
2. Which digital tool creates the ideal conditions for exact positioning and execution of Liebherr drilling and piling rigs?
a. LIPS
b. LIPOS
c. Liebherr POSI
3. Machine learning is …
a. … a new type of school where students are allowed to take their mobile phones into lessons.
b. … a branch of artificial intelligence with a focus on training computers to learn from data and experiences and to continuously improve, without having to be specifically programmed to do so.
c. … a sub-discipline of bulimic learning, where students cram in as much content as possible in the shortest possible time to then forget it again as quickly as possible.
4. Which system helps with the operation of tower cranes and the use of their assistance systems?
a. Electronic Help System (EHS)
b. Electronic Assistant System (EAS)
c. Electronic Monitoring System (EMS)
5. What was the name of the computing machine designed in 1837 that is considered the forerunner to the modern universally programmable computer?
a. Analytical engine
b. Analytical machine
c. Numerical machine
Answers: ɐ :5 ؛ɔ :4 ؛q :3 ؛q :2 ؛ɐ :1
1. In which German city is the Liebherr Digital Development Center based?
a. Ulm
b. Kirchdorf an der Iller
c. Stuttgart
2. Which digital tool creates the ideal conditions for exact positioning and execution of Liebherr drilling and piling rigs?
a. LIPS
b. LIPOS
c. Liebherr POSI
3. Machine learning is …
a. … a new type of school where students are allowed to take their mobile phones into lessons.
b. … a branch of artificial intelligence with a focus on training computers to learn from data and experiences and to continuously improve, without having to be specifically programmed to do so.
c. … a sub-discipline of bulimic learning, where students cram in as much content as possible in the shortest possible time to then forget it again as quickly as possible.
4. Which system helps with the operation of tower cranes and the use of their assistance systems?
a. Electronic Help System (EHS)
b. Electronic Assistant System (EAS)
c. Electronic Monitoring System (EMS)
5. What was the name of the computing machine designed in 1837 that is considered the forerunner to the modern universally programmable computer?
a. Analytical engine
b. Analytical machine
c. Numerical machine
Answers: ɐ :5 ؛ɔ :4 ؛q :3 ؛q :2 ؛ɐ :1
‘Liebherr has the skills, the determination and the vision to achieve great things, because we cover the entire digital chain and aim to create complete ecosystems of our applications with our digital solutions’, adds Stephen Albrecht. ‘We haven’t reached the finish line yet in these transformative times, but we are on a very, very good path.’
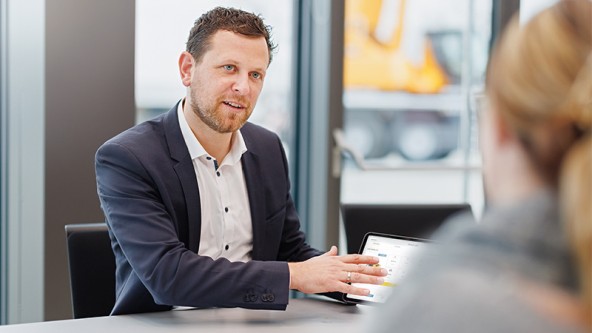
User-specific data is important for decarbonisation. Marcel Flir tells a customer how real operating data can be used.
‘Electrification is not about transferring the performance capability of a diesel unit to an electric drive one-to-one’, says Stephen Albrecht. He believes it is much more important to find out what the customer is actually using their machine for in day-to-day operations. ‘As we are able to capture real operating data and transmit it from our telematics units, we can now optimise the design of the battery and electric powertrain to meet customer requirements. And we don’t always need to stick 100 % to the performance parameters that were originally applied to a conventional drive.’ Another advantage: by incorporating such user-specific data, the Liebherr digital experts and the development engineers are also helping to accelerate the introduction of CO2-optimised machines.
Customer-specific solutions in focus
Supporting customers as a partner in digital transformation and therefore also creating prospects with a view to sustainable development, is also useful in the development of drivetrains, for example.
The Liebherr Digital Development Center in profile
The Liebherr Digital Development Center was founded in 2020 to provide all product segments within the Liebherr Group with digital products based on cloud and IoT connectivity, as well as data and AI integration. This creates digital solutions for the future, which in turn improve efficiency, value and customer service for Liebherr products.
The Digital Development Center focuses on three core objectives in particular:
1) Improving the speed and efficiency of digital development within the Group
2) Supporting the standardisation of digital technologies within Liebherr
3) Attracting and retaining talent for digital development
The team
At the Science Park in Ulm (Germany), a diverse team of software engineers, data science specialists, cybersecurity experts and AI enthusiasts works on digital development for the whole group of companies. There are around 85 employees (correct as of March 2024) from a range of sectors, some with up to 25 years of experience.
The methods
Agile work, fail-fast approach, rapid prototyping, data-driven decisions to improve production processes.
Pooled digital expertise
In all of this, the Liebherr Digital Development Center, based in Ulm (Germany), takes on the role of an enabler. It has been working continually on technology and digitalisation since 2020, based on the needs of the customers. ‘With the Digital Development Center, we have created the basis for digital solutions that we roll out to the market in our product segments. As an internal service partner, it covers the entire digital chain – contributing extensive knowledge in the areas of IoT, cloud solutions, data science and mobile applications and sharing this with the product segments. This speeds up our development and helps us to standardise digital technologies Liebherr-wide’, explains Stephen Albrecht.
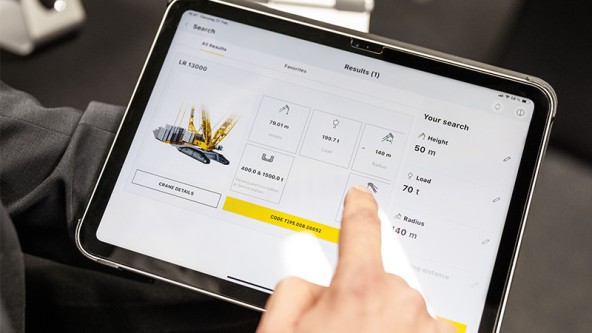
The MyLiebherr customer portal has long since become much more than a spare parts portal. It is the central gateway to Liebherr’s digital world.
The customer portal not only offers comprehensive services, but is also a building block for enhancing Liebherr products and services with further functionalities as part of end-to-end digitalisation. Stephen Albrecht explains: ‘Because in technology development we have everything on our plan – from the idea, production and service through to discontinuation and recycling – and this creates many opportunities for us. For example, the data that a technician records at one site when reconditioning used components can be made available to development engineers at another site. Digitalisation can therefore help us to make our products even more robust and efficient right from the development stage.’
MyLiebherr – one customer portal for all
One example of this holistic perspective is the MyLiebherr customer portal. ‘It is the main gateway to Liebherr’s digital world’, says Marcel Flir. ‘MyLiebherr started out as a spare parts portal. We then gradually expanded the application fields in an iterative process and so created a hub that now has over 125,000 active users and over 60,000 customers.’ Users can now book online training for professionals or buy licences or spare parts. It also offers applications for planning crane lifts, site monitoring and integrated functionalities for machine and maintenance information. In other words, MyLiebherr enables users to access the entire digital world of Liebherr with just a few clicks.
‘Going it alone is a thing of the past. Customers, manufacturers, associations and providers of solutions are all in the same boat when it comes to adding value and achieving the decarbonisation targets that are now needed. We are bringing a real paradigm shift to the table: out with the egosystem, in with the ecosystem’, sums up Marcel Flir. ‘So things that belong together grow together.’
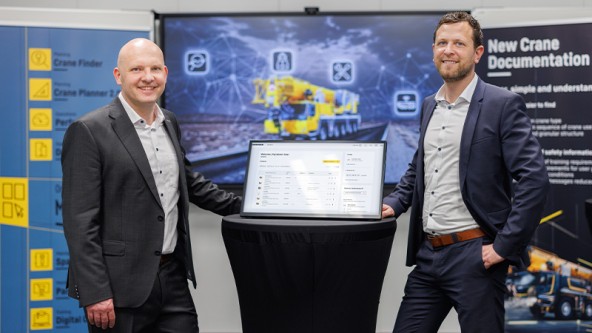
The cooperation in the technology and digitalisation work ensures that innovation will continue to be at the heart of Liebherr’s activities. Marcel Flir and Stephan Schrade, head of digital products and services at Liebherr-Werk Ehingen GmbH, during a joint conference.
‘It depends greatly on how we handle data ourselves’, says Stephen Albrecht. He describes how the focus is always on ‘improving the customers’ processes and the efficiency of how they use their products’. This includes, for example, preparing ways to integrate partner data into the digital ecosystem or to deal with different legal frameworks around the world in the context of digitalisation. ‘It would be wonderful for data to already be interoperable and useable across manufacturers’, says Flir. This demands a certain mindset.
Finding the best solution together
Digitalisation is not an end in itself for Liebherr – it needs to be internalised, accepted and practised in day-to-day work. ‘We don’t need to be the first with a solution in the field – instead, we discuss the opportunities and risks associated with digitalisation in-depth with our employees, stakeholders, customers and partners and talk about how we can reach the best and most sustainable solutions together. This is an interdisciplinary approach that listens to every voice that is actively involved in the solution process’, says Marcel Flir, describing the Liebherr route to digitalisation.
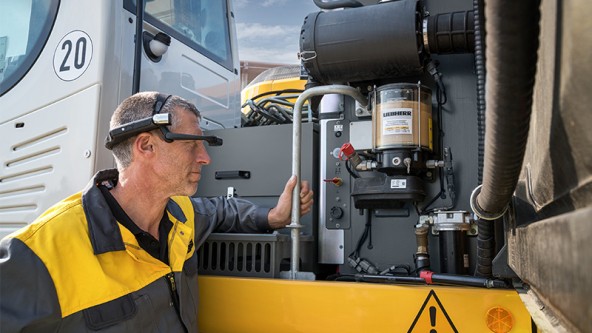
The Remote Service tool includes comprehensive digital services that provide support in service and maintenance cases
Today, specialists at Liebherr work on digital innovations across all product segments – and on connecting the constantly evolving options, machines, refrigerators or components to the associated systems. ‘We have several hundred digital solutions in the field, from APIs to IoT solutions and training simulators – and more are on the way of course’, says Stephen Albrecht. The development departments in the Liebherr product segments shouldn’t need to completely rework the relevant digital basis every time. ‘We seek out and utilise synergies wherever they make sense. To do this, we call on proven standards and system interfaces – with data security, data governance and cybersecurity in general playing a central role, along with the use of established modules. Overall, we drastically reduce the time to market, while also offering our customers ISO 27001-certified digital solutions and services’, explains Marcel Flir.
For Liebherr, digitalisation is not a new trend that is only just being discovered and inspiring innovation. Development engineers at Liebherr have been working on how to capture, record and transfer machine and process data since the mid-1990s in order to use this data for greater product optimisation and emissions reductions. ‘Back then, the time of user-friendly data management hadn’t arrived yet – with 56k modems, the stream of data first had to be painstakingly threaded through a digital eye of a needle’, says Marcel Flir. At the same time, remote maintenance and remote access to controls and components were quickly gaining importance for Liebherr devices, which are exported all over the world, and there was demand for relevant solutions.
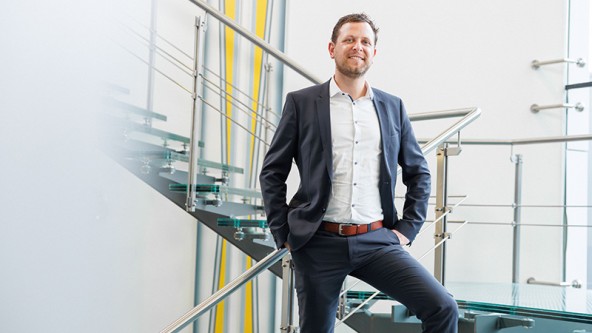
Marcel Flir is head of digital business and strategy at the Liebherr Group
Thinking about technology and measurable added value for customers from such a holistic perspective is second nature to Marcel Flir. The skilled environmental and process engineer with a qualification in industrial engineering spent several years building the digital business at the Liebherr site in Nenzing (Austria) and was also responsible for leading the product management for digital solutions there. He is now head of digital business and strategy for the Liebherr Group. The focus here is on identifying and exploiting synergies in Liebherr’s digital solutions, which extend across all 13 product segments and all parts of the customer journey. This includes, for example, operational planning, maintenance management, digital inventory management, smart home integration and organisational matters.
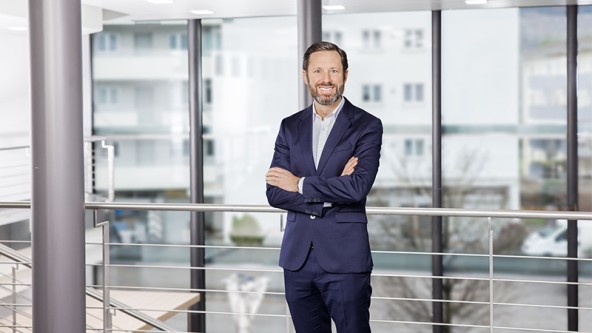
Stephen Albrecht is managing director at Liebherr-International AG
Aristotle once said that the whole is greater than the sum of its parts. In the age of digital transformation, this insight takes on a whole new dimension. ‘The focus is no longer just on the technological excellence of devices and machines. Today, we focus much more on the entire value chain for customers and users of Liebherr solutions. It’s all about concrete, measurable added value that comes from digitalisation’, explains Stephen Albrecht, managing director at Liebherr-International AG. Ever better opportunities for data capture and analysis would pave the way to this. ‘Augmented products with application scenarios that can be experienced and optimised digitally enable this added value to be seen in a different, much brighter light. And, not least, they can also contribute to decarbonisation.’