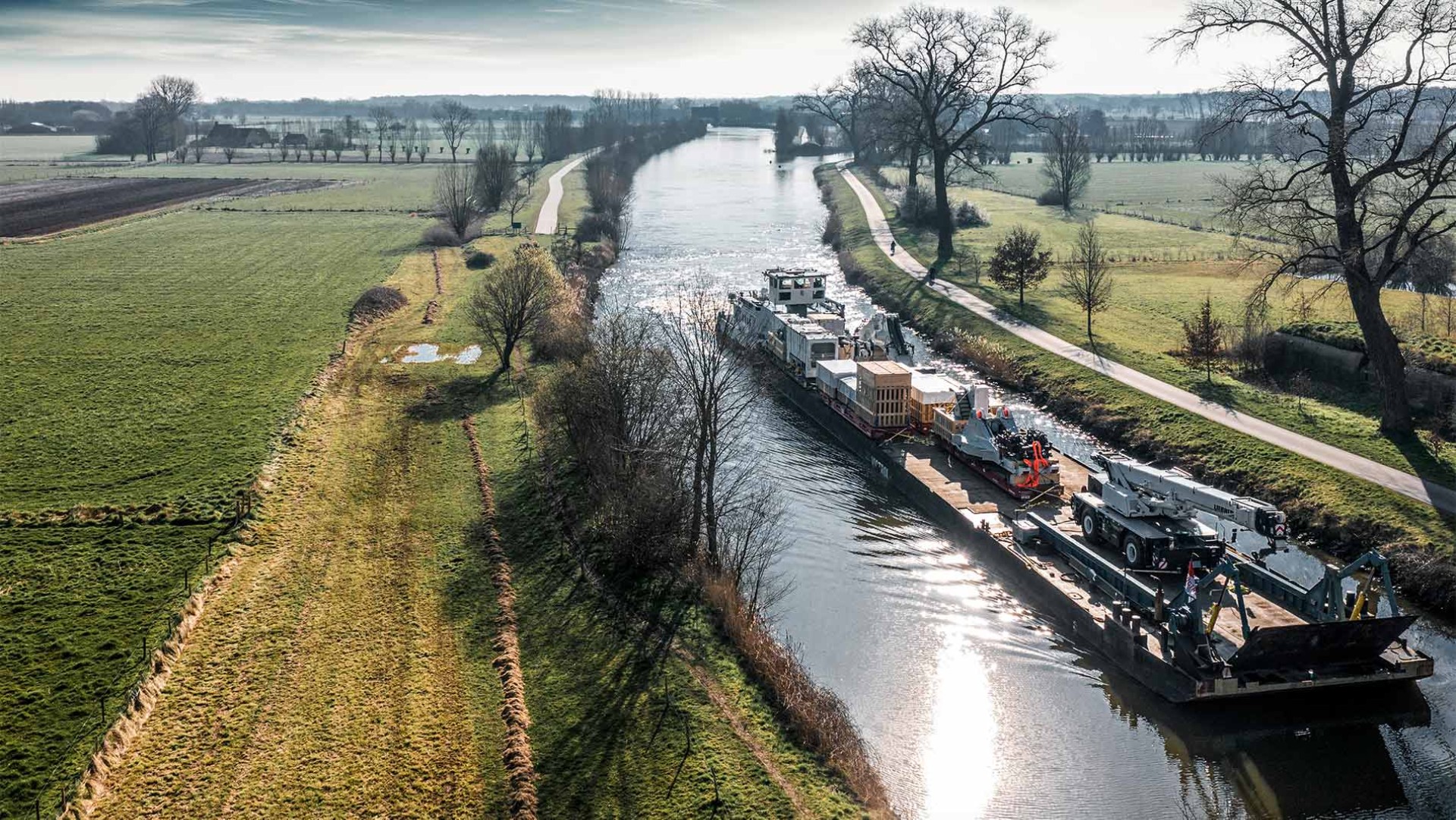
17 minutes | magazine 02/2022
Daring to go new ways
In this age of climate change, at Liebherr we are working on finding solutions to create sustainable production procedures and greener processes.
Shipping cranes by barge – a trial for low emissions transport on waterways
For example, we want to make the planned extension of our crane factory carbonneutral in terms of construction, energy, production and energy sources. As far as our products are concerned, a new LTC compact crane with an additional electric motor for site operations marks the route to zero emission versions of our power units. And since we want to go as far as we possibly can in terms of sustainability, we are also opting to dare to go new ways into unchartered territory. One of these new ways is a pilot for transporting a Liebherr rough terrain crane destined for overseas export. A report on an extraordinary journey.
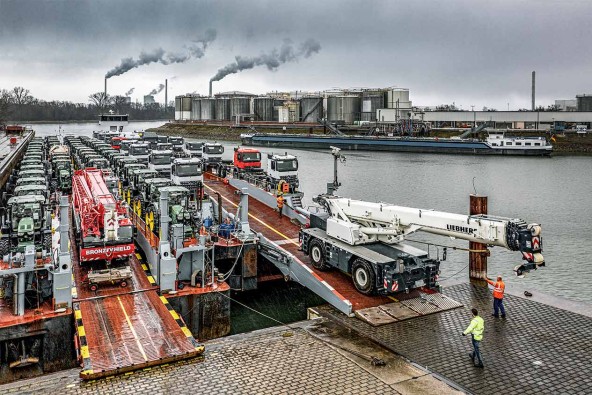
On it goes - At the Industrial Port of Mannheim, the LRT 1090-2.1 moves onto the giant Rhine ferry, which will transport the rough terrain crane to Antwerp. The journey ends at the Port of Rotterdam for the red mobile crane destined for Great Britain (pictured on the left).
The Liebherr plant in Ehingen is a genuine global player when it comes to mobile and crawler crane technology and also in terms of its sales figures. From here, our products are shipped all over the world. Every year, around 1,000 mobile and crawler cranes leave our factory to be loaded onto ocean-going vessels at major seaports – and this figure is on the rise. The terminals in Bremerhaven and Hamburg are the main export ports we use. Generally, our mobile cranes cover the routes to the ports under their own steam. Rough terrain cranes, crawler cranes, some prototypes and the components for our large cranes, on the other hand, must be transported to the ports using lots of heavy, high volume haulage trucks, which involves a great deal of logistics work. We conducted a trial recently to find out whether we could simplify this process, and above all, do so using fewer resources.
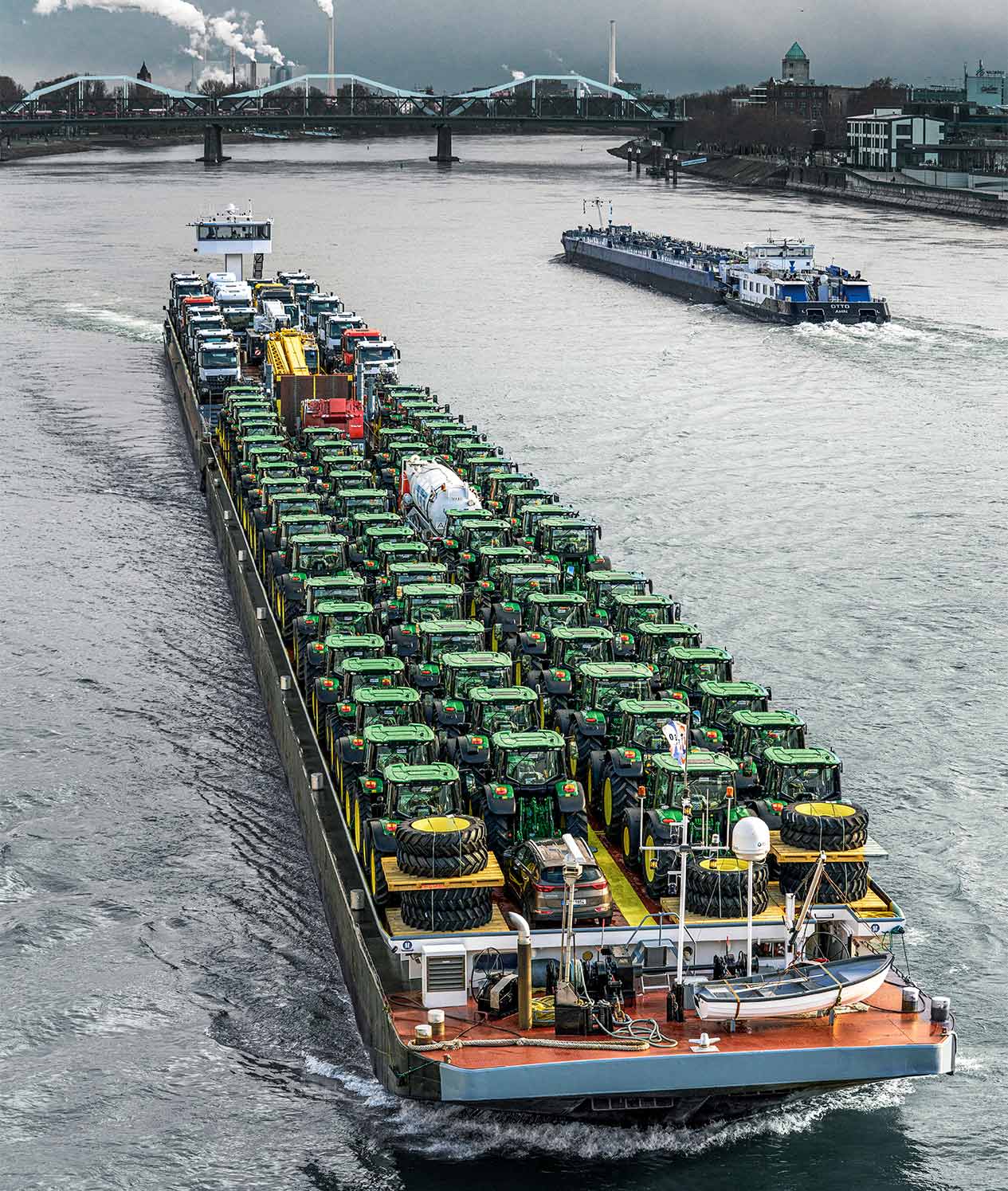
Ship ahoy! - With its imposing length of 214 metres, the “Dynamica” starts its three-day journey in Mannheim on the River Rhine to Rotterdam and then on the Schelde-Rhine Canal to Antwerp in Belgium. In addition to several other Liebherr mobile cranes and truck tractor units, there are around 100 tractors on its upper and lower decks.
An LRT 1090-2.1 rough terrain crane destined for the North American market had to be delivered to Zeebrugge in Belgium for shipping. This powerful crane, suitable for use in open cast mines or large construction sites, with its enormous gross weight of around 55 tonnes is not licensed for driving on roads. Therefore, it is split into two packages for transport, namely the basic machine, including the superstructure and boom, in one parcel and accessories, such as the hook block and ballast slabs, in the other. However, instead of being driven on a low loader over the 800 kilometre trip to the Belgian coast, the journey actually covered just one third of the distance to Mannheim, around 80 kilometres south of Frankfurt am Main. At the Rhine port there, the crane was driven onto an enormous Rhine ferry, together with three other Liebherr mobile cranes destined for Great Britain, several new truck tractor units and around 100 tractors. The subsequent trip down the River Rhine on the 200 metre barge took around three days to Rotterdam and then on through the ScheldeRhine Canal to Antwerp, the largest breakbulk port in the world. On arrival, the LRT 1090-2.1 was parked up for around a week between thousands of cars and enormous storage areas for breakbulk, which is the specialist term for large piece goods.
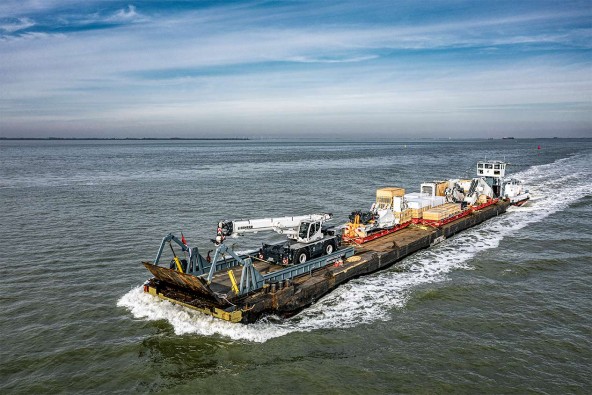
High seas? - You might think so. But actually, the heavyweight barge train is actually shown here travelling across the wide mouth of the River Schelde towards the North Sea before turning back into Belgium’s canal network.
Travelling with a mining excavator
Our crane had to wait. In fact, it was waiting for an R 9400 excavator to arrive from the Liebherr Plant in Colmar (France). This enormous machine was also travelling to Antwerp by waterway. Together with the components of this mining machine, our rough terrain crane was due to travel the rest of the way on a barge train comprising tug and RoRo (Roll on Roll off) pontoon. The planned route was on the River Schelde, which partly passes through the Netherlands, towards the open sea and finally on Belgium’s internal waterways via Ghent and Bruges to the seaport of Zeebrugge. The Wallenius Wilhelmsen shipping company, whose enormous ocean-going vessels take care of the maritime transfer of Liebherr machines throughout the world, was responsible for this section of the journey.
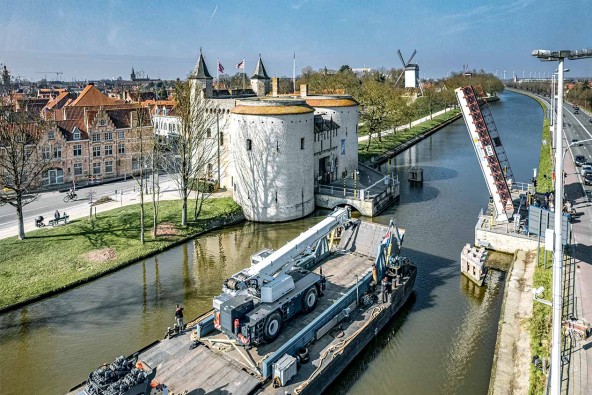
Sightseeing - On the Ringvaart Canal along the old town of Bruges in Belgium, our rough terrain crane on the front of the barge also passed several bascule bridges and windmills. The barge train is shown here passing the 600 year old former city gate known as “Kruispoort”.
220 Tons Liebherr technology on board
“The Liebherr Group is an important partner for us and has been our customer for many decades”, says Carsten Wendt from Wallenius Wilhelmsen. In his role as “Senior Manager High & Heavy and Breakbulk Sales Germany”, he looks after breakbulk transport for German customers and was therefore responsible for planning the entire trial for this trip through Belgium. “We have plenty of load space on this large barge for rough terrain cranes from Ehingen and for the mining excavator from Colmar”, adds the experienced logistics expert. “We loaded the excavator components and the accessories for the LRT 1090-2.1 on a total of seven standard roll trailers. They are placed on the pontoon and then in Zeebrugge they are moved onto the ocean-going vessels without us having to unpack the goods again. The rough terrain crane, on the other hand, drives itself onto the pontoon and later also onto the ship.” There is a simple reason why the LRT 1090-2.1 was unable to start its sea journey from Antwerp: “Because the Ehingen crane is going to North America, it can only be loaded onto one of our ships in Zeebrugge. From Antwerp, we go to different regions of the world.”
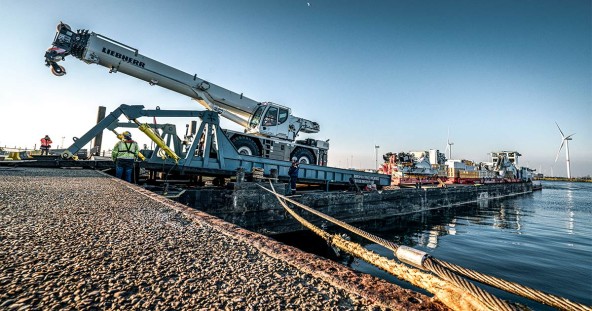
Arrival - At the Port of Zeebrugge, the rough terrain crane drives down the pontoon ramp onto dry land. The Wallenius Wilhelmsen shipping company has its own terminal where its ocean-going vessels are loaded before travelling to North America.
Wendt was also there when the crane was loaded onto the barge in Antwerp: “After a long period of planning, I wanted to know how well loading breakbulk onto the pontoon works here and whether we might have created any logistics traps which we hadn’t thought about.” However, after just two hours, all the material had been effortlessly moved onto the vessel and safely secured. The trial involving a total of 220 tonnes of Liebherr expertise could begin.
From Ehingen to Zeebrugge with just one stop
To put it bluntly, Wendt’s plan ran like clockwork. Around two days and 150 kilometres of waterway later, the powerful pusher tug had manoeuvred its pontoon through the Belgian inland waterways and arrived at the shipping company’s terminal in Zeebrugge with its heavyweight cargo. Waiting for vessels going in the opposite direction, at locks and bascule bridges reduced the speed of the barge train slightly. However, Jens Bachmann, Team Leader Crane Shipment at the Liebherr Plant in Ehingen, puts the time required for the journey by waterway compared to road transport into perspective: “The steady increase in traffic, ever longer diversions due to ramshackle motorway bridges and the complicated licensing processes for heavy haulage transport all mean that we regard the option using the ferry and barge as a genuine alternative.” Shipment Manager Benjamin Buchmüller continues: “The Wallenius Wilhelmsen solution using the RoRo barge enables us to reach the ports of Antwerp and Zeebrugge with a single stop and we can deliver even more cargo on green inland waterway vessels.”
The summary from the shipping company was very similar: “The detailed planning and preparations paid dividends, everything went perfectly”, said a delighted Carsten Wendt, after the rough terrain crane and roll trailer had been unloaded in a very short time using the pontoon ramp at the Zeebrugge terminal. The shipping company regards the successful trial as motivation and a general opportunity for the more ecological shipping method which generates lower emissions of carbon dioxide. In future, the move from road to inland waterways could be used not only for containers but also for piece goods. “Actually, the Belgian government is very interested in moving traffic off its highly congested roads, and what’s more, the availability of truck capacity is a massive problem at the moment.”
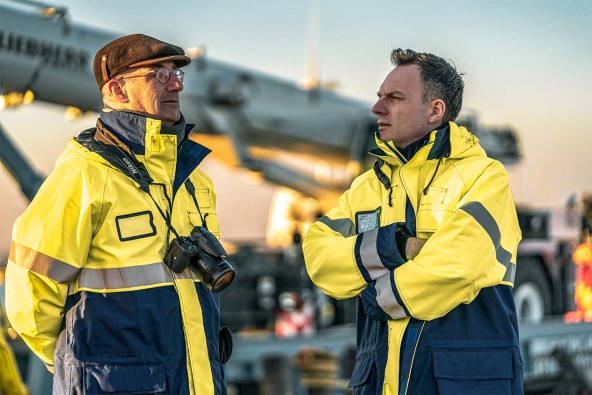
Chewing the fat - Carsten Wendt, Senior Manager High & Heavy and Breakbulk Sales Germany, on the right of the photograph, and Werner van Dessel, Manager Sales Development EMEA (both from Wallenius Wilhelmsen), are both positive about the trial after the carefully planned trip on the water went like clockwork. According to van Dessel, ten to twelve road transport vehicles would have been required to move the entire cargo.
50 percent lower CO₂ emissions between Antwerp and Zeebrugge
At Liebherr, we are now conducting a thorough analysis of the pilot. But already we have discovered that the trial was positive from both an ecological and a financial point of view. “This method of transport is definitely an option for us”, confirms Jens Bachmann. “We already ship around 160 cranes a year through the port of Mannheim. Ferries travel to Rotterdam and Antwerp twice a week. Now we can even ship machines to Zeebrugge waterway.” The pontoon on the barge train through Belgium actually has enough space for up to nine cranes.
We’ve saved the best for last – Wallenius Wilhelmsen has now calculated the potential reductions in carbon dioxide for the route between Antwerp and Zeebrugge. Carsten Wendt continues: “On a positive note, we have found that this method using inland waterways halves the CO2 emissions compared to the conventional solution using trucks.”
… followed up
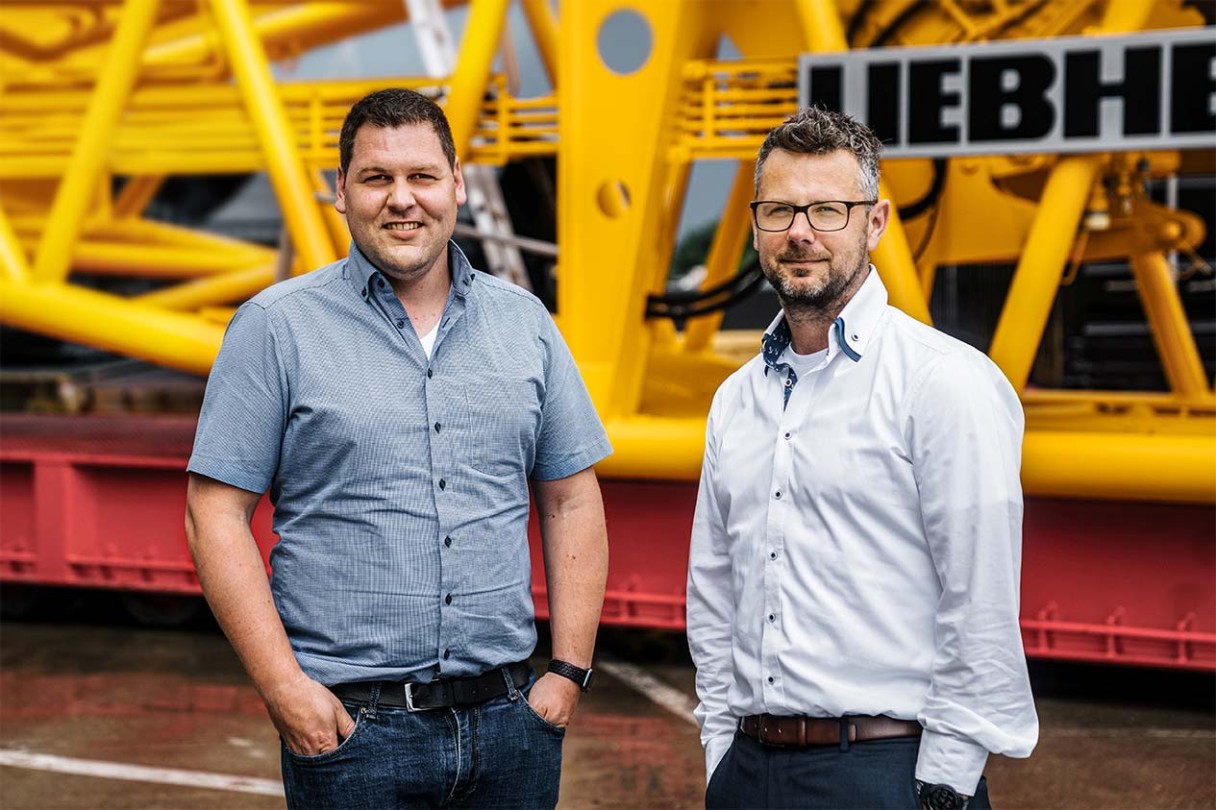
Benjamin Buchmüller, Head of the Shipment Department at Liebherr in Ehingen (right) and his colleague Jens Bachmann, Team Leader Crane Shipment, give us a little more information about the alternatives for transporting cranes and equipment by waterway.
Why were you looking for a new means of transport as an alternative to the road?
Benjamin Buchmüller: Essentially, the search for new or better transport routes in financial and ecological terms is one of the main challenges facing the Shipment Department. In this specific case, the main idea was to find an alternative to the export ports we generally use in Bremerhaven and Hamburg, which we would be able to reach by waterway. Fortunately, the subject of sustainability is becoming more important in the transport sector as in every aspect of our lives. Furthermore, the route from Ehingen to Bremerhaven and Hamburg by road is becoming ever longer and more difficult. Infrastructure problems, particularly ramshackle, restricted bridges, mean that the routes approved by the authorities for transporting our products are becoming ever longer and the transport conditions are becoming more and more difficult.
What do you mean by restricted bridges?
Jens Bachmann: In order to protect older bridges or those that already show initial damage, the maximum vehicle weight is limited. Mobile cranes and heavy haulage trucks then have to take alternative routes. The direct route from our plant in Ehingen to Bremerhaven is actually around 800 kilometres, but the route approved for transporting our products is currently up to 1,190 kilometres depending on the crane model. That is the opposite of sustainable.
Benjamin Buchmüller: When we deliver cranes using their own engines or transporting them on a low loader, this is known as large volume and heavy haulage and we have to obtain an official road permit for these trips. Without them, our machines cannot leave our yard. The road permit contains details of the route and this route must be followed precisely. For example, it states exactly when the journey may take place and when it must not, whether a second driver is required, the speed and distance that must be maintained on bridges and whether another vehicle or the police must escort the truck.
Jens Bachmann: The worse the infrastructure to the ports becomes, as is increasingly the case, the more diversions we have to include in the route, which in addition to increasing the distance also means higher costs for fuel, personnel and escort vehicles. What’s more, it is becoming more and more difficult to obtain trucks in the time available and in the quantity we require.
So what are the alternatives?
Benjamin Buchmüller: One of them is transport by waterway. The nearest port to us is in Mannheim, around 200 kilometres away. From there, a ferry travels twice a week carrying tractors and trucks from local factories to the ports of Rotterdam and Antwerp, and it can also carry our basic machines easily, loading them using a ramp. Compared to transporting them to Bremerhaven, this saves the journey via Mannheim of around 560 kilometres, which our cranes would otherwise have to cover themselves or on a low loader. We have been using the Rhine ferry from Mannheim to Rotterdam and Antwerp for years. Last year alone, we transported over 160 cranes on this route, saving a lot of transport costs and CO2.
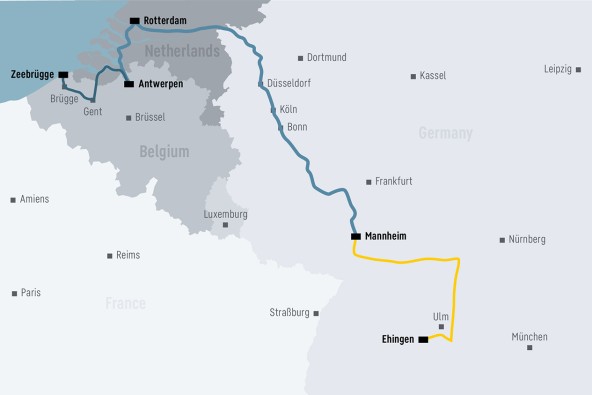
Yellow: Route by road - blue: waterways
You describe transporting the LRT rough terrain crane to the sea port of Zeebrugge as a pilot project. What is new about it?
Jens Bachmann: The challenge was that the Rhine ferry from Mannheim did not travel to Zeebrugge because firstly it is not suitable for travel on the high seas and secondly it is too large for Belgian canals and their locks. However, the Western ports are the only adequate alternative for the global export of our machines if we can reach both Antwerp and Zeebrugge. We wanted to make sure that this was possible.
Benjamin Buchmüller: Our sister company, Liebherr-Mining Equipment Colmar SAS, has been almost exclusively using barges from Neuf-Brisach to transport its machines for some considerable time. Just like the RoRo ferry from Mannheim, however, the trip to Zeebrugge is not possible from there. When we talked to our shipping company, Wallenius Wilhelmsen Ocean AS, therefore, we had the idea of linking the ports of Antwerp and Zeebrugge using a RoRo barge. Wallenius Wilhelmsen also saw that this would be an opportunity to generate additional Liebherr cargo for its loading operation in Zeebrugge and in addition Liebherr-Mining Equipment Colmar SAS was also very much in favour of the idea straight away.
And what is your conclusion?
Jens Bachmann: The trial was extremely successful. The collaboration with our partners was excellent. Naturally, there are one or two points that have to be ironed out.
Benjamin Buchmüller: Transporting the LRT 1090-2.1 on a low loader from our plant to Mannheim, from there on a barge to Antwerp and then using the RoRo barge to Zeebrugge was more than 30 percent cheaper than by low loader from Ehingen straight to Zeebrugge, and we were also able to reduce our greenhouse gas emissions by around 28 percent. That is sustainable and is definitely a step in the right direction.
Transporting machines by waterway to the port of Zeebrugge is a good alternative transport solution for delivering them to customers overseas. The example of the LRT is clearly transferable to other mobile cranes and is a solution to the urgent need to move transport vehicles from the road to the water.
This article was published in the UpLoad magazine 02 | 2022.