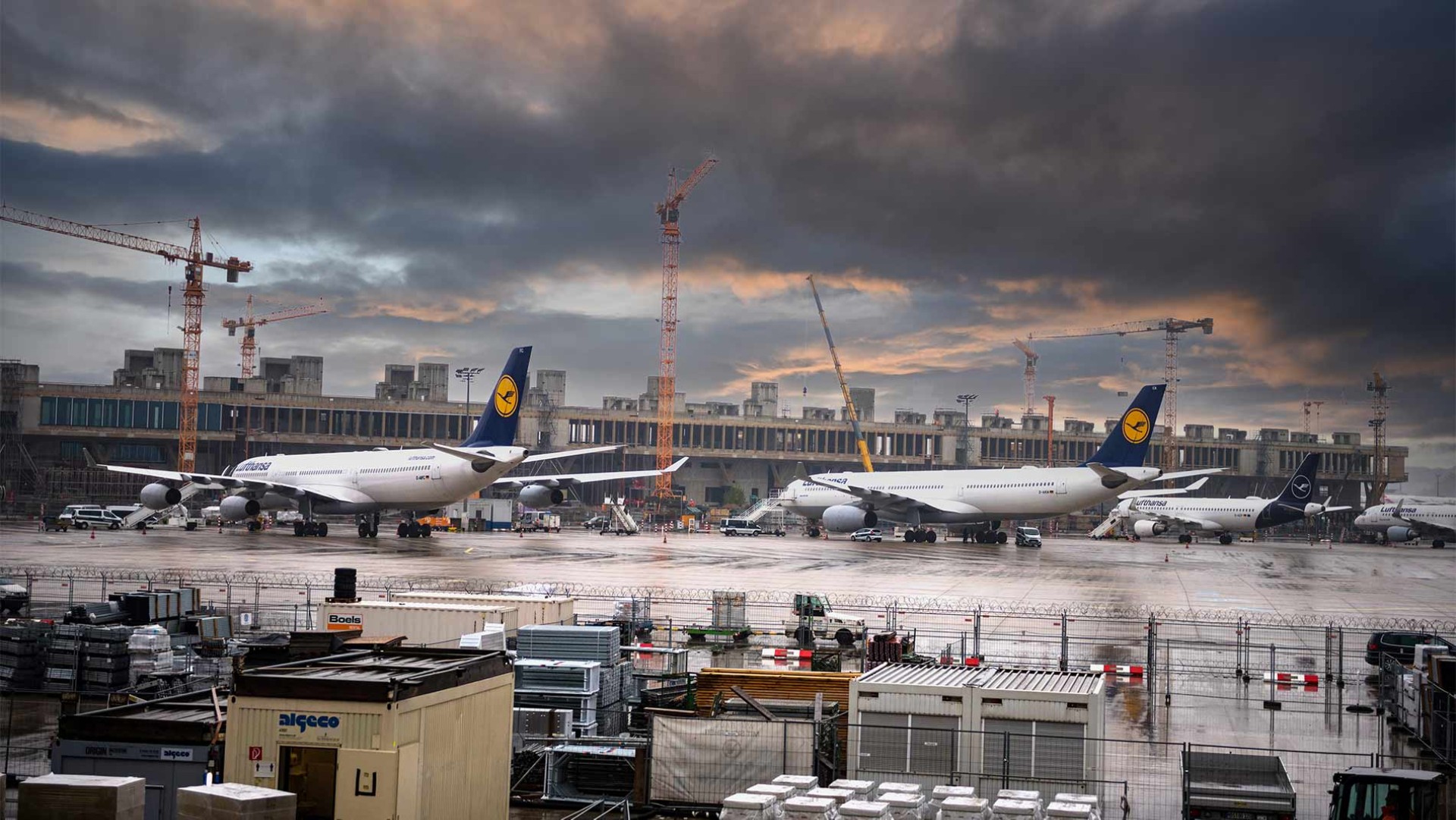
8 minutes | magazine 01/2022
Smart and stable with Y
It is the largest privately financed infrastructure project in Europe – the new Terminal 3 is currently being built at the southern side of Frankfurt Airport.
Into the future with Terminal 3
Airport operator Fraport is investing around 4 billion euros in the future of Frankfurt Airport. Also involved in the project are the Schick Group and its Liebherr mobile cranes – and 86 Y-shaped supports, which are delivering stability and elegance. Really chic.
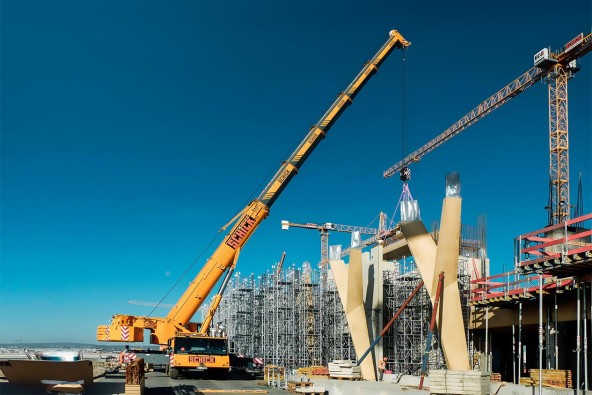
“When we started the construction work in 2018, this was all green fields,” says Carina Wehner. The 27 year old construction engineer is the Project Manager for Prefabricated Concrete Components at Anton Schick GmbH + Co. KG. Together with two other project managers, Aileen Kempf and Michael Metz, she is responsible for the complete process from planning and production, to transport and installation on site. Michael Metz has been with Schick for 20 years: “The airport expansion is the largest construction project in the history of our group.”
The Schick Group is building the new tower with an impressive height of 70 meters and the two main passenger gates for the new Terminal 3. Pier J, with its three levels, a length of 600 meters and an area of 27,000 m² will provide space for 14 aircraft positions. There will be 12 positions at Pier H, which has two levels, a length of 400 meters and an area of 16,000 m². Thousands of heavy prefabricated concrete components are required for the structures. The vast majority of them are manufactured at one of the Schick Group’s own prefabricated concrete plants in Bad Kissingen around 150 kilometers away.
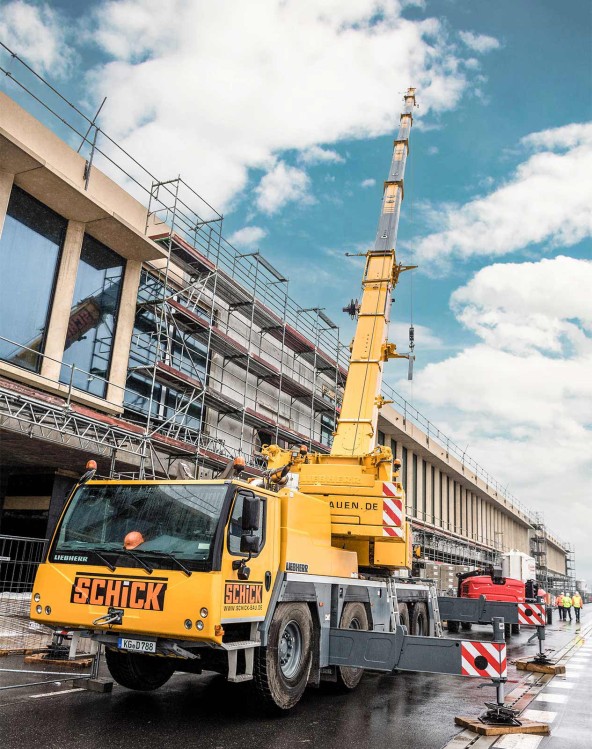
An LTM 1090-4.2 installs coloured concrete façade elements on Pier H.
Y-shaped supports deliver stability and flair
Many of the concrete components will be visible once the piers have been completed. So they therefore have to be designed and produced accordingly. Almost all the prefabricated concrete components have been manufactured using a specially coloured granulate. The 86 Y-shaped supports, which fit on both sides along Pier J, are particularly striking. “The Y-shaped supports have both a load-bearing and architectural purpose. In load-bearing terms they dissipate the load of the projecting floor above them through level E02 into the ground. Their architectural feature is their unique geometry. They only have sharp edges which run at angles to each other,” says Wehner, explaining their twin function. “For our customer, they are essentially important and must comply with the architects’ plans exactly,” adds Metz.
There is a total of five different types of Y-shaped support, depending on their structural role. There are also double Y-shaped supports, which provide extra stability at the two ends of the piers. Most of the supports weigh 22.5 tonnes, the heaviest weighs in at 44 tonnes. Metz explains the special installation procedure: “They are installed using two mobile cranes, an LTM 1230-5.1 and, depending on their availability, an LTM 1090-4.2 or 1160-5.2. The 230 tonne crane hoists the support and holds it in the right position for installation. The smaller crane provides hoisting support until the required angle has been reached by turning the component in the air. After the component has been installed, it then installs the angled supports which the Y-shaped supports require from the front to fill and harden the sleeve foundations.”
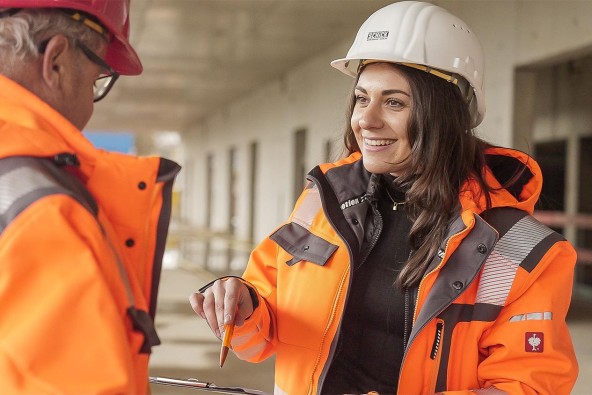
Aileen Kempf discusses the next crane jobs for installing concrete façade elements on site.
Wehner continues: “The installation work is particularly challenging because the angle of seven degrees to the front must be maintained precisely. Because this is difficult to check, surveying technicians check with specially manufactured gauges whether the position of the Y-shaped support is within tolerance.”
All from a single source
The process, consisting of planning, production, transport, installation on site and embedding in the carcase structure is supported and completed in full by the Schick Group. It has its own vehicles, its own mobile cranes, its own personnel, planning and site managers – everything from a single source. Aileen Kempf, who has been with the Schick Group for almost ten years, believes that this delivers great benefits: “We have very good communication between each other, which enables us to react flexibly and quickly. As soon as the crane is available, it is used for other work.”
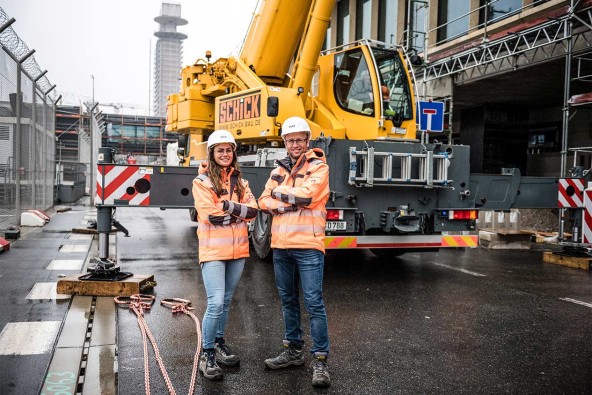
Experts for the complete prefabricated component process – Carina Wehner and Michael Metz. In the background you can also see the new tower for Terminal 3, which has also been built by the Schick Group.
Michael Metz appreciates the fact that he can talk direct to the crane operators: “We planned the crane jobs at the office using the Liebherr LICCON work planner. That enables us to check which crane model is required for a specific job. We then define the crane configuration and the location. And sometimes that is a real challenge because the area for the crane and for setting up the crane is limited. We then discuss our plans on site with the crane operators because they have the practical experience. Their feedback is very valuable. We simulate particularly complex jobs on the actual site.”
“We often have to take projecting edges into account. There is also the fact that the maximum crane height at Fraport is limited to 60 meters because of flight activity. If the slewing range of a mobile crane projects into that of a construction crane, the latter has to be turned off. Industrial safety is absolutely paramount here on the site,” adds Kempf.
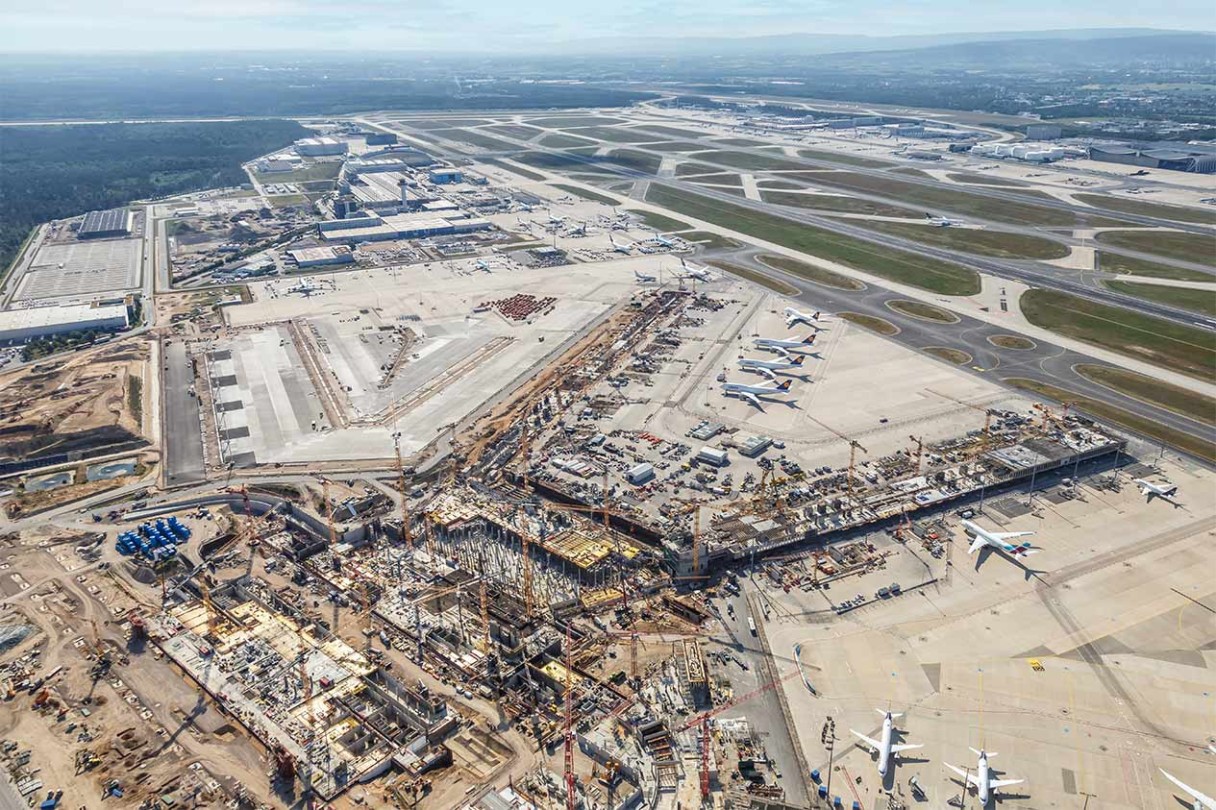
Frankfurt Airport
– Terminal 1 opened in 1972
– Terminal 2 opened in 1994
– 70 million passengers in 2019
– 81,000 employees from 88 nations
– Daily (2019):
190,000 passengers
1,400 take-offs and landings
6,000 tonnes of cargo
With up to five mobile cranes moving around the site at any one time, the quality of the cranes and service work for them must be absolutely perfect. As far as Metz is concerned, this is the case: “We have a direct line to the Liebherr service team. The Liebherr customer service people complete maintenance work on Fridays and Saturdays so that the cranes are available again during the week. We have also suffered very few crane failures. There was one, however, that I remember very well. We had a problem in the afternoon. The Liebherr fitter arrived at five the next morning and by seven the crane was up and running again. That really impressed me.”
Terminal 3
– Scheduled to open in 2026
– Construction work started in 2015
– Investment volume €4 billion
– 176,000 m² of floor space, corresponding to 25 football pitches
– 403,000 m² total area on all storeys
– 112,000 tonnes of steel, the amount required to build 15 Eiffel Towers
– 19 million passengers, when fully complete up to 25 million passengers
Terminal 3 is scheduled to start operating in 2026. It will enable an additional 19 million passengers a year to pass through the airport. The final extension will actually allow for 25 million passengers per year. The Schick Group is scheduled to complete its site work in 2022. In addition to the production and installation of the structural components of the external façade in prefabricated concrete, elements of the interior are also included. For example benches made of super-smooth, coloured concrete. Really chic.
This article was published in the UpLoad magazine 01 | 2022.