The revised Liebherr gear shaping machine with new features
Robust and even more versatile: the LS 500 E
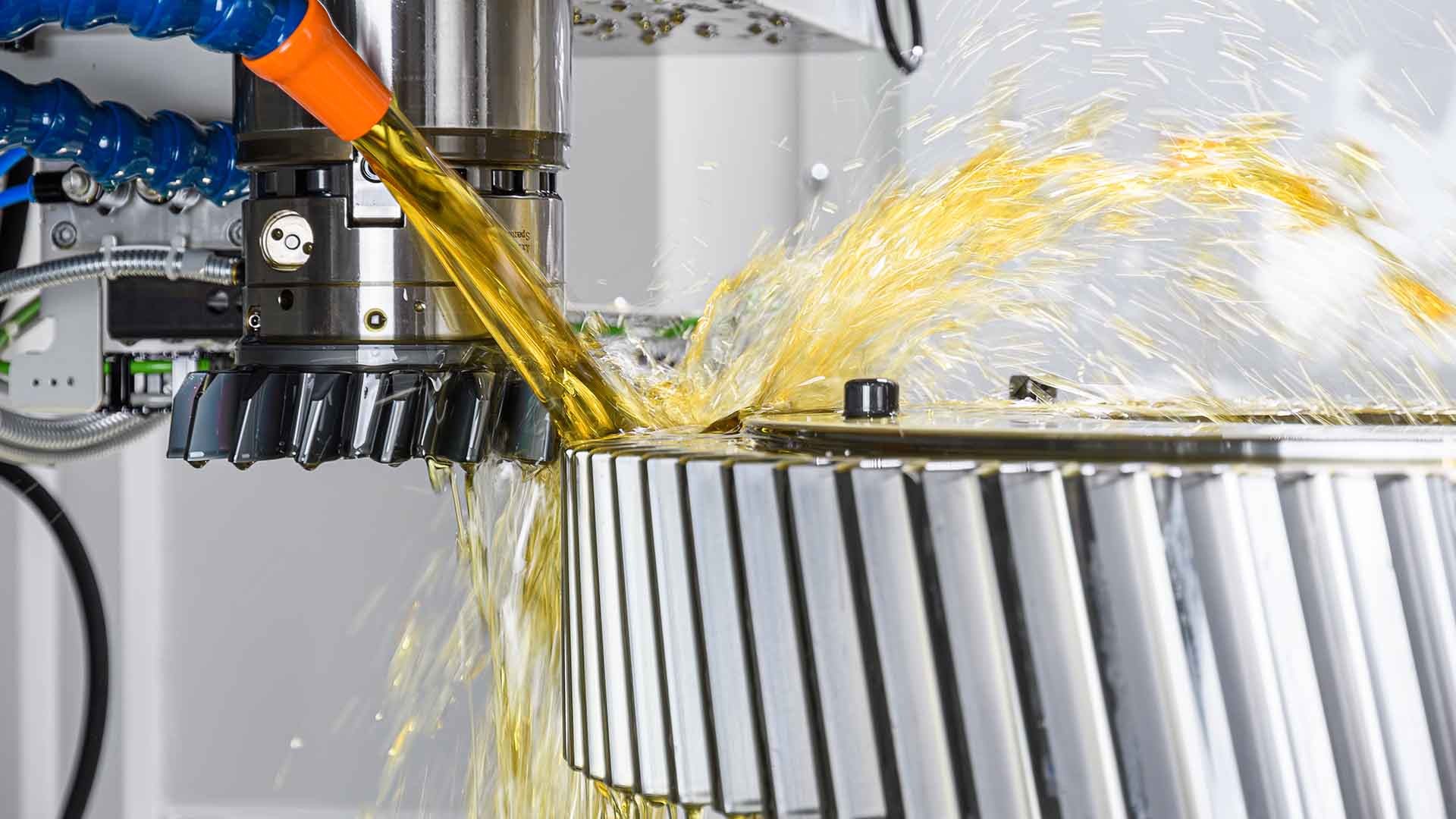
The revised Liebherr gear shaping machine with new features
Robust and even more versatile: the LS 500 E
The revised Liebherr gear shaping machine with new features
Robust and even more versatile: the LS 500 E
The revised Liebherr gear shaping machine with new features
Robust and even more versatile: the LS 500 E
Gear shaping is a robust and universal process for manufacturing gears – due to the geometries of some gears, no other machining methods are capable of producing the teeth. In order to offer even more versatility in this area, Liebherr-Verzahntechnik GmbH has fundamentally revised and developed its LS 500 E gear shaping machine. A shaping head featuring an electronic helical guide and an interface for an optional chamfering device are now included as standard.
If you are looking to produce gears on workpieces with interfering contours and with a low tool overrun, there is usually no other way than gear shaping. Although it is not necessarily the fastest process, it is the most flexible, versatile and robust gear cutting method. This method can also be used to machine components for which no other process, such as double-helical gears, clutch hubs or drive shafts, is suitable. Tools and clamping devices for gear shaping are cost-effective and can be used universally.
Development of the LS 500 E
The LS 500 E gear shaping machine from Liebherr-Verzahntechnik GmbH, together with its slightly smaller sister – the LS 300 E – and the manually loadable LS 700 EM, all offer a versatile, high-quality and forward-thinking platform. These machines are incredibly useful in job shops, but can also be used across the industrial, commercial vehicle, and aerospace sectors. In recent years, Liebherr has further developed and optimized its platform for all gear cutting machines for machining workpieces up to 500 millimeters in diameter. The LS 500 E was also given a facelift, and was fundamentally revised as part of this process.
Shaping head variants
SH 120 E | SH 240 E | |
Drive power kW | 35 | 54.5 |
Max. stroke speed DH / min | 1,200 | 1,000 |
Max. stroke length mm | 120 | 240 |
Max. module mm | 8 | 12 |
Tilt angle adjustment ° | + ⁄ - 0.4 | + ⁄ - 0.4 |
Max. helix angle ° | 45 | 45 |
Max. tool diameter mm | 275 | 275 |
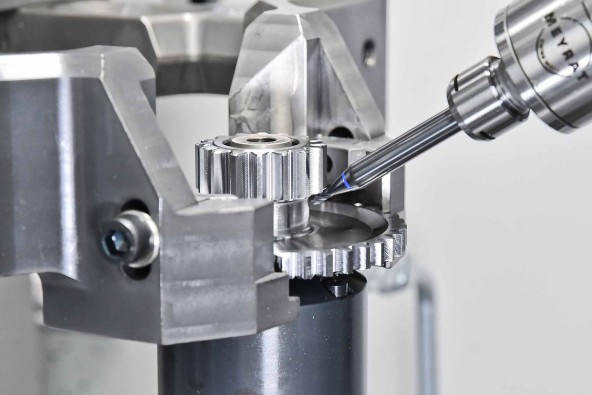
FlexChamfering during the machining process on the chamfering device
Optimized structure with tried-and-tested components
The new platform includes a powerful electronic shaping head guide, and an interface for an optional machining unit for chamfering and deburring during the machining process. Thanks to its thermodynamic design, the LS 500 E is a powerful, high-precision machine with high rigidity, which is also suitable for processing more demanding materials. Furthermore, the machine technology has been revised and developed beneath its modern monolith housing design.
The machine table with wear-free, high-precision hydrostatic bearings is now driven directly, while the shaping head for the SH 120/240 E variants is NC-controlled with an electronic guide. “Even asymmetrical tooth trace modifications for special gearbox requirements can be shaped,” points out Thomas Breith, Head of Product Management Gear Technology at Liebherr-Verzahntechnik GmbH.
New features for greater versatility
Arguably the most important new feature is the interface in the machine table for a 90-degree machining unit, on which additional operations such as deburring, chamfering using ChamferCut or FlexChamfer (also for internal gears) or even pointing can be carried out during the machining process. “FlexChamfering in particular – chamfering with end mills – is an interesting option for job shops when cycle times play less of a role,” adds Thomas Breith.
For the production of position-dependent gears, such as double-helical gears, a newly developed, an optional measuring probe directly on the tool spindle offers the possibility of precise correction measurement with a measuring accuracy of a few micrometers. “This improves positioning accuracy and leads to a considerable increase in process reliability,” says Dr. Andreas Mehr, expert for gear shaping at Liebherr-Verzahntechnik GmbH, summarizing the newly developed design. The control panel with the LHGearTec software enables intuitive operation and programming. For particularly large workpieces, the LS 500 E is also available with a workspace extension, which increases the travel range of the z-axis by a further 200 millimeters.
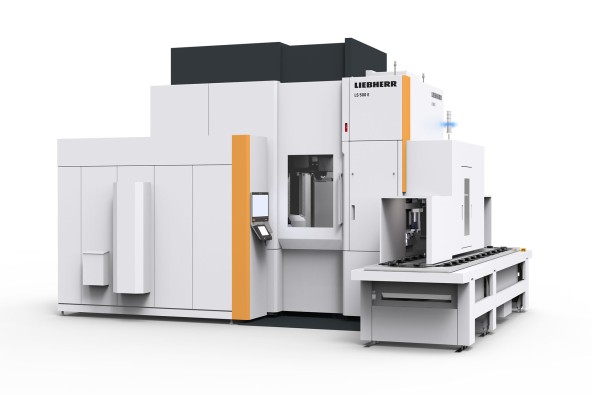
The new LS 500 E
The manually loadable LS 700 EM is also of interest for contract gear manufacturing, which can be easily automated later with robot loading if required. “A high degree of versatility is absolutely essential – particularly in areas with differing batch sizes or when producing very large or very small, complex and collision-prone parts,” explains Thomas Breith.