The next generation of Liebherr’s high-performance GET for hydraulic excavators up to 400 tonnes
Introducing the Liebherr Z G3 System – an advanced evolution of our GET (Ground Engaging Tools) for hydraulic mining excavators up to 400 tonnes. Since the launch of the first generation more than a decade ago, we have been committed to continuous improvement, pushing the boundaries of innovation to set new industry standards and deliver the best plate lip system available on the market. Driven by cutting-edge research, direct feedback from on-site personnel and valuable customer insights, we have refined every aspect of our design to deliver unmatched durability, performance and efficiency.
Boosting your operation with real benefits
Want to find out more?
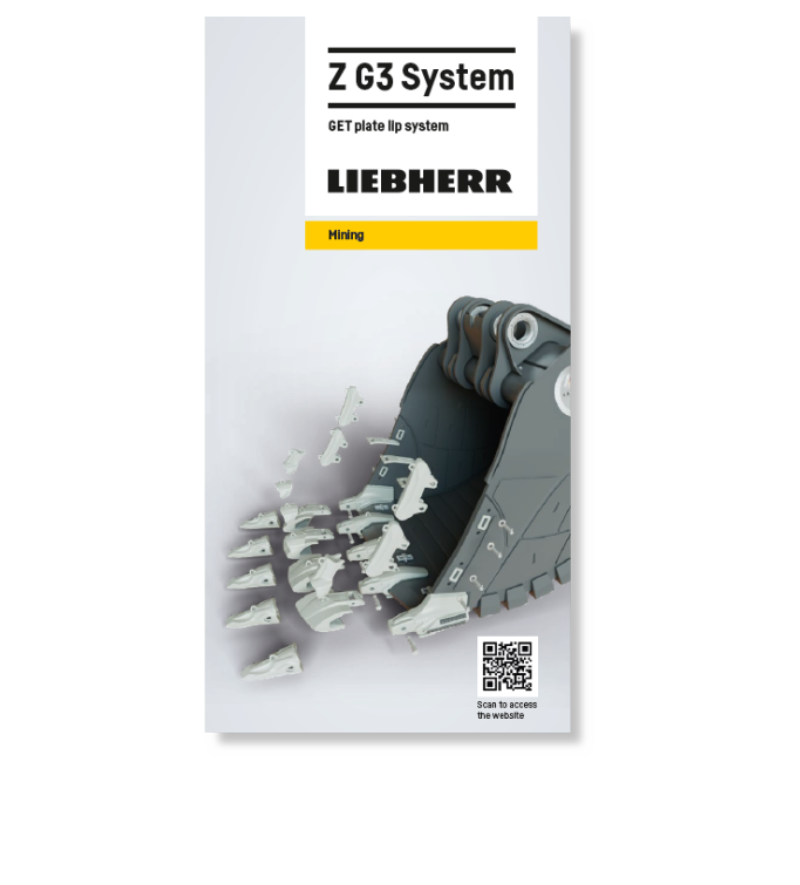