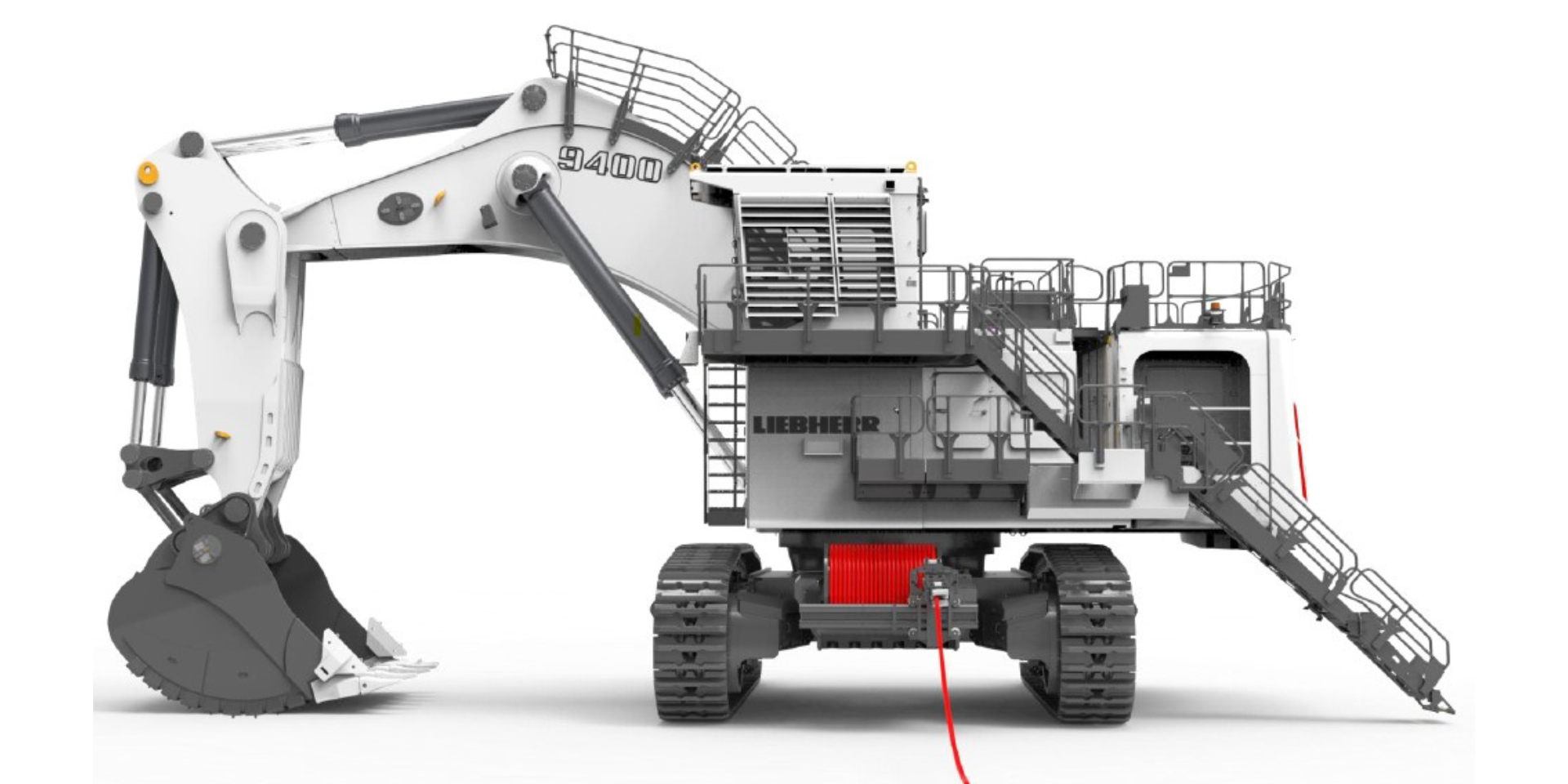
Technical spotlight: Cable reel for electric excavators
In 2020, Liebherr Mining released its cable reel system. This system provides up to 300 metres of autonomous cable reeling for Liebherr’s electric excavators, increasing the manoeuvrability of these machines and the safety of the onsite personnel that work with them.
Liebherr used its extensive expertise in developing, manufacturing, and maintaining electric excavators – honed over more than 40 years – to develop the cable reel. For electric excavators to provide optimal onsite productivity, they much be as mobile and as easy to use as possible while also staying connected to their power source.
How it works
The Liebherr cable reel system is a fully autonomous solution that consists of a drum, cable, winder, hydraulic motor, and several safety sensors.
Drum
The size of the drum – and therefore the length of cable within the system – depends on the size of the excavator. Specifically, it depends on the space available between the bottom of the uppercarriage and the top of the undercarriage, as the cable reel is installed onto the centre girder. There has to be adequate room between the drum and the ground to prevent any damage to the cable reel system. Because of this, a smaller drum is used on smaller excavators. However, this does not mean a reduction in reeling capability. The reel system is hydraulically driven, allowing for smaller component integration than an electrically driven system. Liebherr’s R&D team chose to power the cable reel with a hydraulic motor rather than an electric one as electric motors are highly sensitive to dust and to humid environments. As mine sites are often situated in dusty areas with extreme temperatures, this sensitivity would have been likely to cause performance issues on site. Furthermore, hydraulically driven systems are more reliable and more compact than their electric equivalents, while also being simpler and easier to maintain.
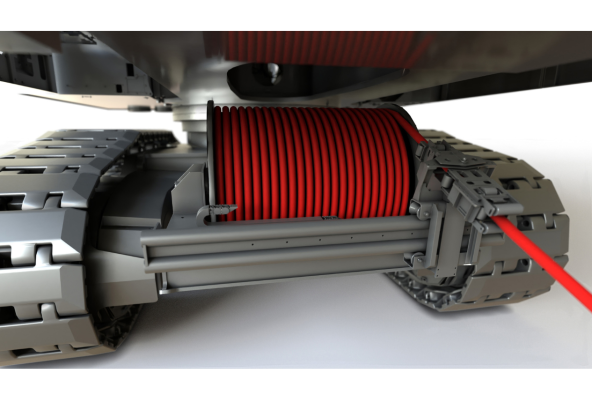
Cable
The cable in the reel system is different to the one used for a standard trailing application. The trailing cable is specially designed to withstand the friction caused by the stress of continuous contact with the ground as the excavator pulls the cable. On the other hand, the cable in the reel system is designed to be coiled and so offers much more flexibility than the trailing cable. Additionally, the cable in the reel system is larger than the trailing cable to prevent the power cable from overheating.
Sensors
The safety sensors within the reel system help to ensure that the cable always remains at an optimal tension. When the excavator reaches the maximum length of its cable, these sensors let the system know that the machine can no longer move forward. The reel system is equipped with a number of limit switches that alert the operator to how much cable is on the drum. Once activated, these switches trigger an audible chime and warning lights within the cabin so the operator knows the excavator must change direction.
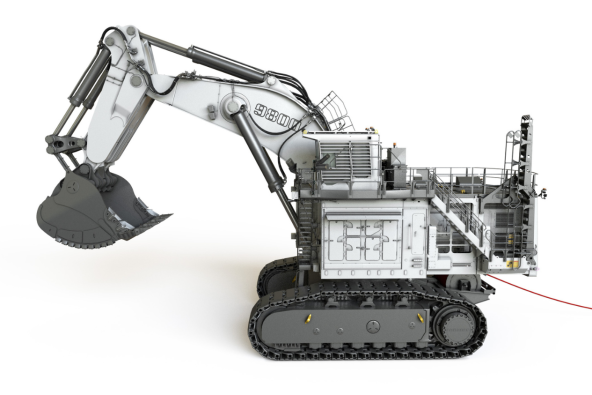
How it helps
Electric excavators that use Liebherr’s cable reel system benefit from better machine mobility and optimised safety. In fact, the cable reel system provides the best possible solution for managing the cables of electric excavators in backhoe configuration – particular those that need to be repositioned multiple times. Because the cable can be retracted automatically while the machine is reversing, there is no need for an operator to manually handle the cable. This not only speeds up the excavator relocation process, but also improves the safety of the operator as they do not have to get too close to an active machine.
The robust design of the cable reel is also an advantage on site. The cable reel is protected by thick steel plates that keep the structure off the ground and prevent the cable reel from being damaged should it come into contact with the terrain of the mine.
How to get started
Liebherr’s cable reel system has been designed to be straightforward to install, while also preserving easy access to the travel drive circuit for routine maintenance. Customers using the cable reel for their electric excavators can use the same infrastructure to connect to their site’s electric grid as they would when using the trailing cable. Further, Liebherr’s electric excavators have been designed so the reel system can be easily integrated into them. The machines’ frames are reinforced so that they can easily accept the additional weight of the cable reel once bolted to the centre girder. Plus, there is enough room underneath Liebherr’s electric excavators to accommodate the reel system without reducing the amount of ground clearance.
Liebherr’s cable reel system can be installed at first fit or can be retrofitted and is available for the majority of Liebherr’s electric excavators.
Check out this video to learn how our cable reel can be used on site!
By clicking on “ACCEPT”, you consent to the data transmission to Google for this video pursuant to Art. 6 para. 1 point a GDPR. If you do not want to consent to each YouTube video individually in the future and want to be able to load them without this blocker, you can also select “Always accept YouTube videos” and thus also consent to the respectively associated data transmissions to Google for all other YouTube videos that you will access on our website in the future.
You can withdraw given consents at any time with effect for the future and thus prevent the further transmission of your data by deselecting the respective service under “Miscellaneous services (optional)” in the settings (later also accessible via the “Privacy Settings” in the footer of our website).
For further information, please refer to our Data Protection Declaration and the Google Privacy Policy.*Google Ireland Limited, Gordon House, Barrow Street, Dublin 4, Ireland; parent company: Google LLC, 1600 Amphitheatre Parkway, Mountain View, CA 94043, USA** Note: The data transfer to the USA associated with the data transmission to Google takes place on the basis of the European Commission’s adequacy decision of 10 July 2023 (EU-U.S. Data Privacy Framework).