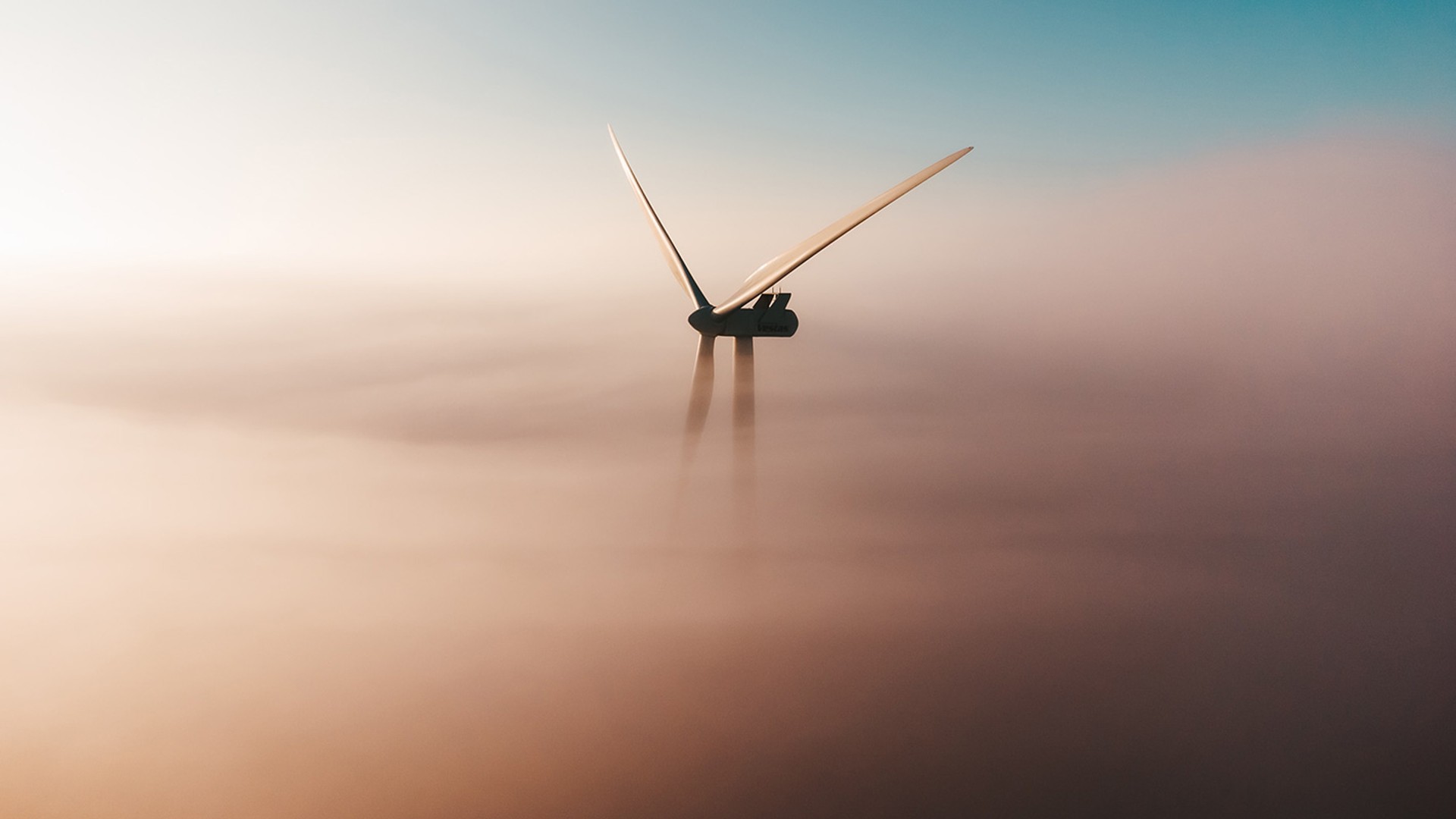
Cranes at work for wind energy
The wind energy sector is growing and growing – along with the size and efficiency of the wind turbines. For Global Wind Day, we’ll take a look behind the scenes, following two cranes as they help build wind farms on land and at sea.
Global Wind Day
This worldwide event on 15 June is a day for learning about the importance of wind energy and its possibilities for reshaping our energy systems. The wind energy sector is currently on a strong growth path and 2020 was a record year. According to the Global Wind Energy Council, new wind energy installations totalling 93 gigawatts were built across the globe, some 53 percent more than in the previous year.
As a partner for the wind energy sector, the Liebherr Group offers solutions specially adapted for the energy of the future: individual components for wind turbines, foundation manufacture with concrete mixing plants and truck mixers, the spectacular task of installing wind turbines using Liebherr cranes… and many things in between.
It’s not just the number of wind turbines that is increasing year by year. Their efficiency is also increasing – along with their size! And if the turbines are following the slogan “Higher, faster, further!”, then the cranes need to keep up. After all, building wind turbines is truly a feat of strength. Let’s take a closer look!
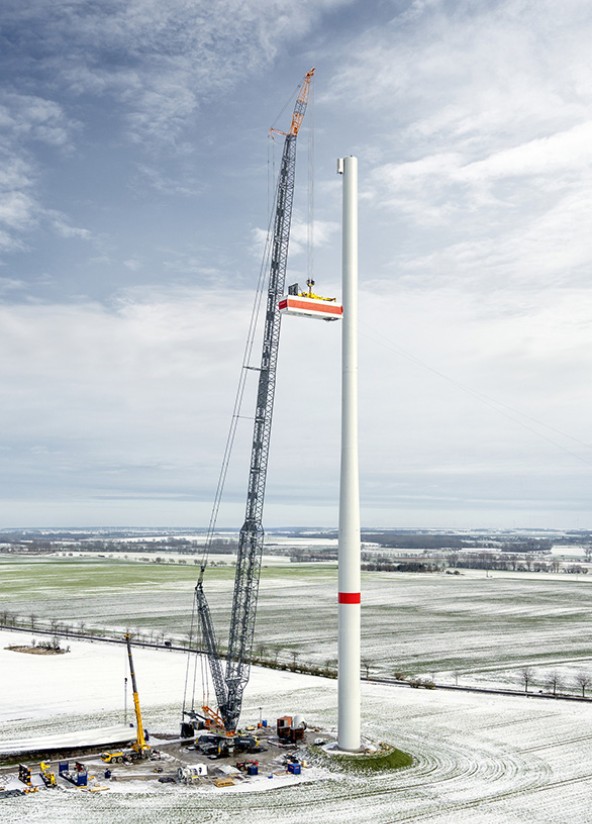
On land...
When it comes to installing wind turbines on land, mobile cranes and crawler cranes are the go-to machines. For example, our lattice boom mobile crane LG 1750 was used in north-east Germany to install two turbines with hob heights of 170 metres and unusually heavy tower components up to 120 tonnes.
The first step in installing a wind turbine is to choose the right crane. The crane needs to have the right lifting capacity, of course, but that’s not all: it is also important that it can be transported quickly and efficiently to where it will be used – and some wind farms are in remote locations. Once the crane has reached the site, lifting the tower elements into place is a routine task for an experienced crane operator. One after another, the individual tower elements are set in place on the foundation and connected up. Finally, the machine house, which in this project weighed in at a hefty 112 tonnes, is lifted into place.
In any lifting operation, the wind speed at the location can affect the process significantly. Of course, wind is essential for the work of the wind turbines once they are operating, but it can create real difficulties for our cranes. To meet this challenge, the LG 1750 has a reinforced lattice boom that enables it to be used safely in wind forces up to 10 metres per second – in fact, sometimes as much as 11.2 m/s. Nonetheless, intense concentration is essential for the final stages, when the individual rotor blades are lifted onto the turbine and secured to the hub. By their very nature, these present the biggest targets for the wind. The crane operator and crew cannot afford to let their attention lapse for a moment.
…and at sea.
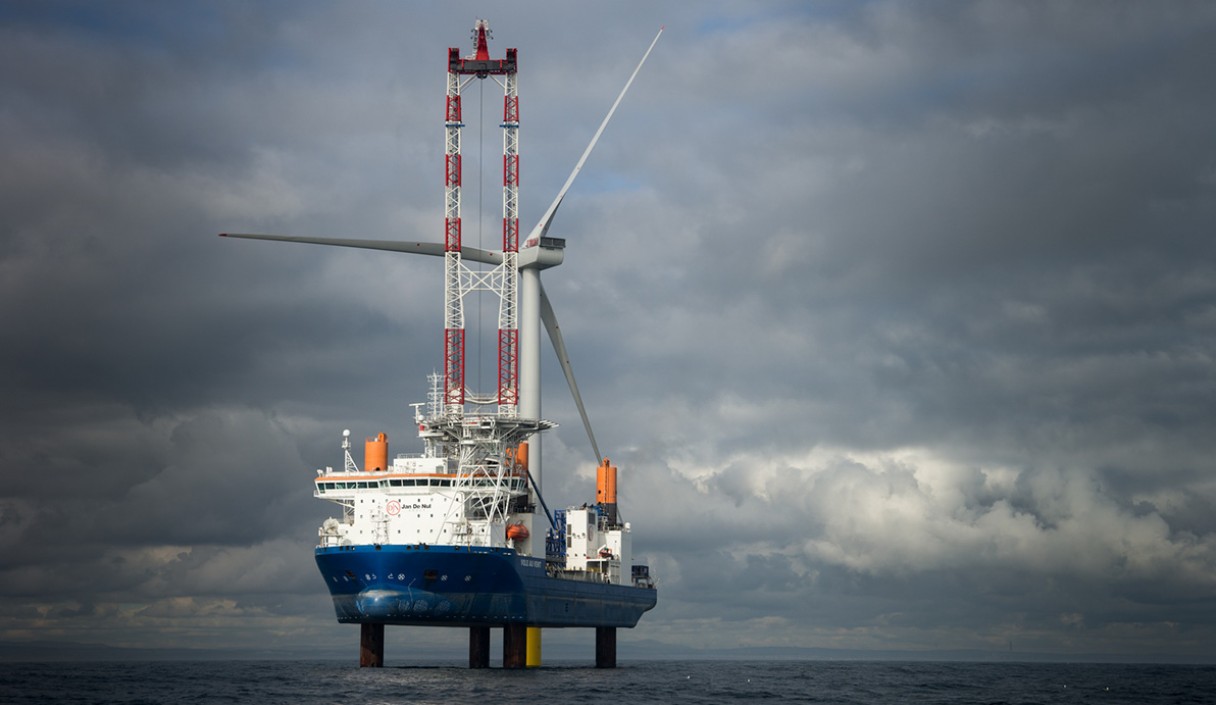
Constant sea breezes mean offshore locations are perfect for wind farms. However, working at sea brings other challenges: the unpredictable and changeable weather, waves and swell. Offshore wind farms are often built using jack-up vessels. The Vole au Vent, shown in this picture working off the coast of Taiwan, is one such vessel. And on board the Vole au Vent is a Liebherr heavy-lift offshore crane, the CAL 45000.
Jack-up vessels need to be able to work independently of the ocean swell, so they have lifting equipment that holds the vessel a few metres out of the water. The crane itself is designed such that its huge bulk can be positioned compactly on the vessel – the CAL 45000 here is a “crane around the leg”. The ship and crane work together as a single unit and are designed to match from the shipbuilding stage.
In port, the wind turbine elements are loaded onto the vessel using mobile harbour cranes (learn more). The jack-up vessel then transports the turbine elements to their offshore destination. Even when working offshore, the first stage of building the wind turbine is to create a foundation. These are often made of monopiles – steel piles that the crane drives into the sea floor to depths of up to 60 metres. An intermediate element is then lifted onto the foundation and the tower elements are set on top of this. Finally, the machine house and rotor blades are lifted into place and secured. The CAL 45000 lifts up to 1,200 tonnes during these jobs; its big brother in the offshore crane series, the CAL 64000, can lift as much as 1,500 tonnes. But these numbers pale in the face of Liebherr’s new HLC series of offshore cranes, which will be able to lift loads up to an astonishing 5,000 tonnes.