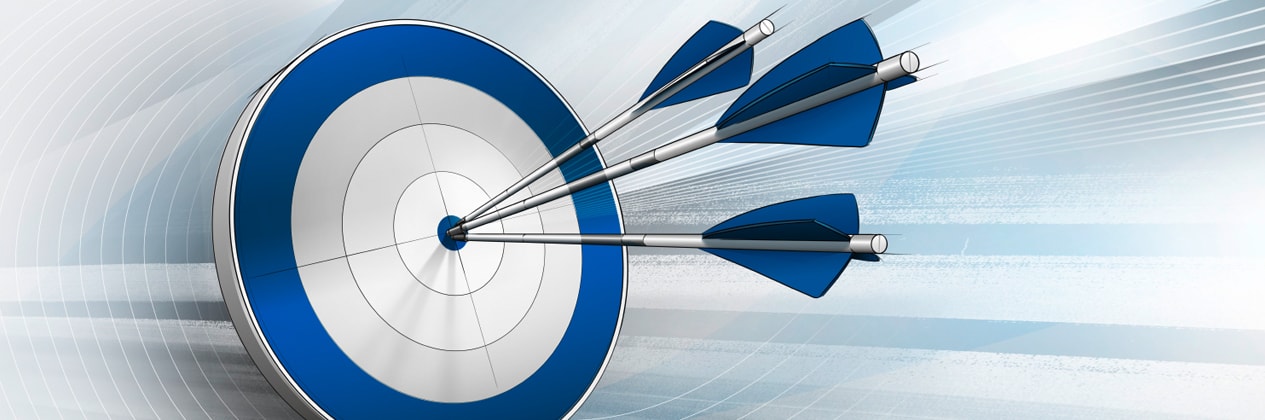
Magazine 2020
Magazine 2020
Most read
01
In August 2019, trainees Fabian Altenried and Julia Fetzer participated in the Liebherr Summer Program at Liebherr Gear Technology Inc. / Liebherr Automation Systems Co. (LGT / LAU) in Saline, near Detroit. There, they ran the PLC programming course for pupils of the robotics course from the local high school, which was offered for the first time, and got to know the work routine at the Liebherr site. Fabian reports on his experience here:
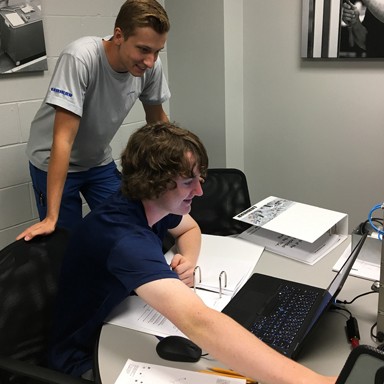
02
Liebherr presents the new series of generating and profile grinding machines for hard machining of external and internal gears on workpieces with diameters of up to 500 millimeters. The LGG series follows the successful Liebherr LCS 300 to 500 series. With an impressive range of added features, they offer more flexibility and grinding performance with a significantly reduced footprint.
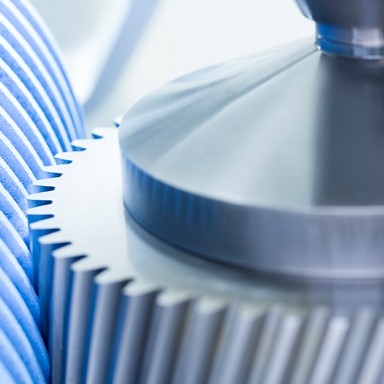
03
Gear skiving is over 100 years old and has recently been experiencing a renaissance as a flexible and economical alternative to other gear cutting methods. However, this complex process frequently presents great challenges to users. In addition to Skiving3, a “complete package” consisting of machine, tool and technology, Liebherr now also offers skiving tools for suppliers and contract gear manufacturers – and the appropriate consultation, if desired.
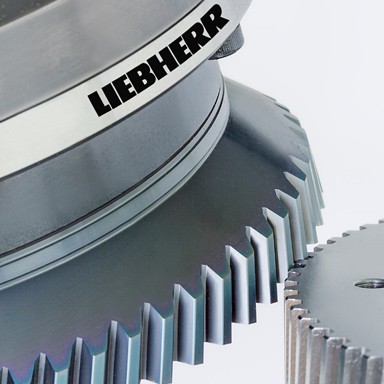
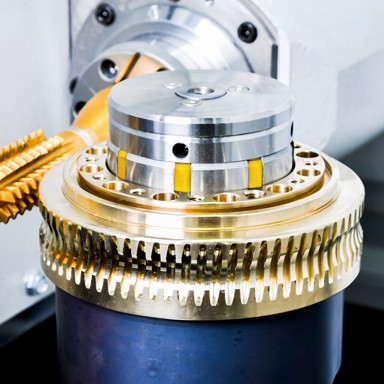
Clamping units for gears with short delivery times at low costs – due to the high level of individualization of clamping devices, these demands were often diffi cult to reconcile. That’s now a thing of the past. The segment clamping arbor SECLA from Liebherr is an innovative, inexpensive standard solution with short delivery times for a maximum application range in gear manufacturing machining.
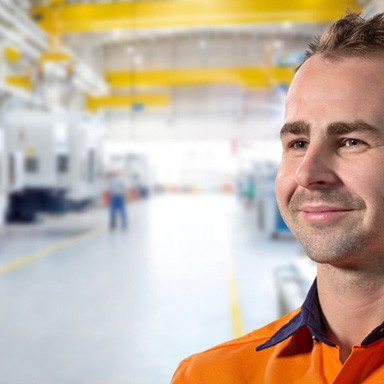
When founding the Industrial Services for Gear Technology and Automation Systems department in 2018, Liebherr already began rolling out the topic of services again from a user perspective. By now, customers can choose the service that fits their individual requirements from a total of five different service packages.
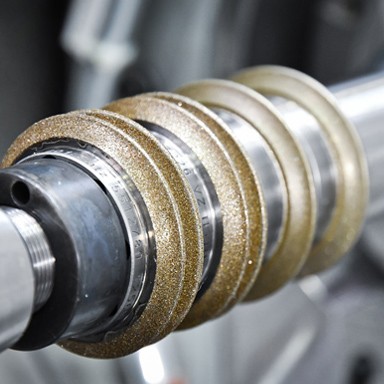
The machining of gears with interfering contours for the aerospace industry places the highest demands on the grinding tool and often cannot be carried out with standard grinding heads due to the small tool diameters. Liebherr has developed an auxiliary spindle for these applications which can be retrofitted. This enables the production of challenging aerospace components on existing LGG gear grinding machines.
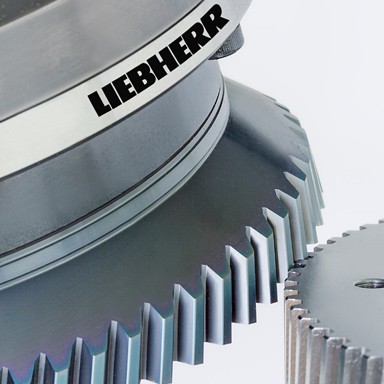
Gear skiving is over 100 years old and has recently been experiencing a renaissance as a flexible and economical alternative to other gear cutting methods. However, this complex process frequently presents great challenges to users. In addition to Skiving3, a “complete package” consisting of machine, tool and technology, Liebherr now also offers skiving tools for suppliers and contract gear manufacturers – and the appropriate consultation, if desired.
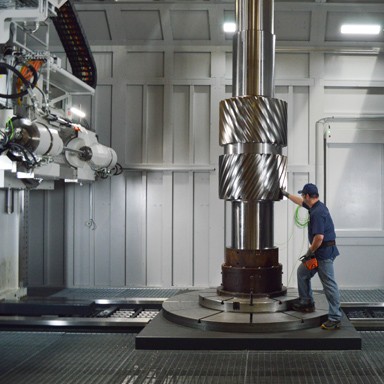
A visit to the HMC Gears plant in Indiana kicked off an extensive project which resulted in the creation of a unique solution for exceptional demands: With the LC 4000, Liebherr forges new paths in large-scale gear cutting production and unites diverse machining methods in one highly efficient machine for the American gear specialist.
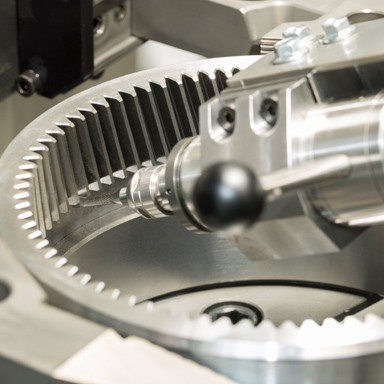
Anyone who manufactures small batch sizes of complex components wants to perform as many work steps as possible with a single machine. This not only saves time and equipment costs but also increases the quality, provided that the clamping fixture does not have to be changed. Liebherr-Verzahntechnik GmbH offers a comprehensive solution for complete machining by integrating a tool changing system and a chamfering device while using the turning, drilling and gear cutting functions of the latest generation of Siemens controls.
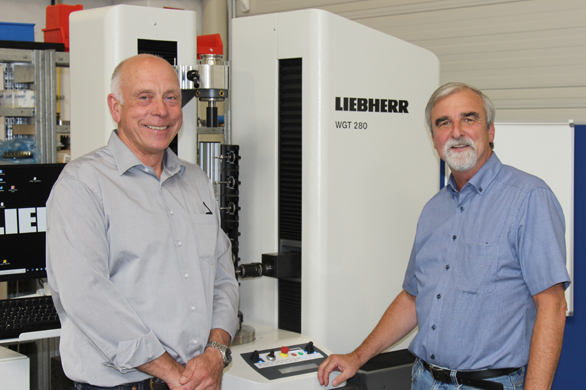
What does the name LHOpenConnect stand for? How can an open data structure help the user? Which software services does Liebherr-Verzahntechnik GmbH offer? Over the past few years, the company has gradually built up an application architecture that focuses not only on the machine, but on the entire process, which means it can support production in many different ways. Thanks to its modular structure, customers can select the tools which best complement their own specific production environment.
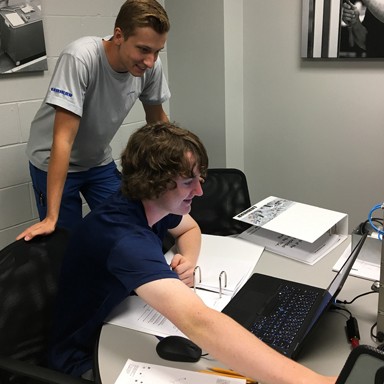
In August 2019, trainees Fabian Altenried and Julia Fetzer participated in the Liebherr Summer Program at Liebherr Gear Technology Inc. / Liebherr Automation Systems Co. (LGT / LAU) in Saline, near Detroit. There, they ran the PLC programming course for pupils of the robotics course from the local high school, which was offered for the first time, and got to know the work routine at the Liebherr site. Fabian reports on his experience here: