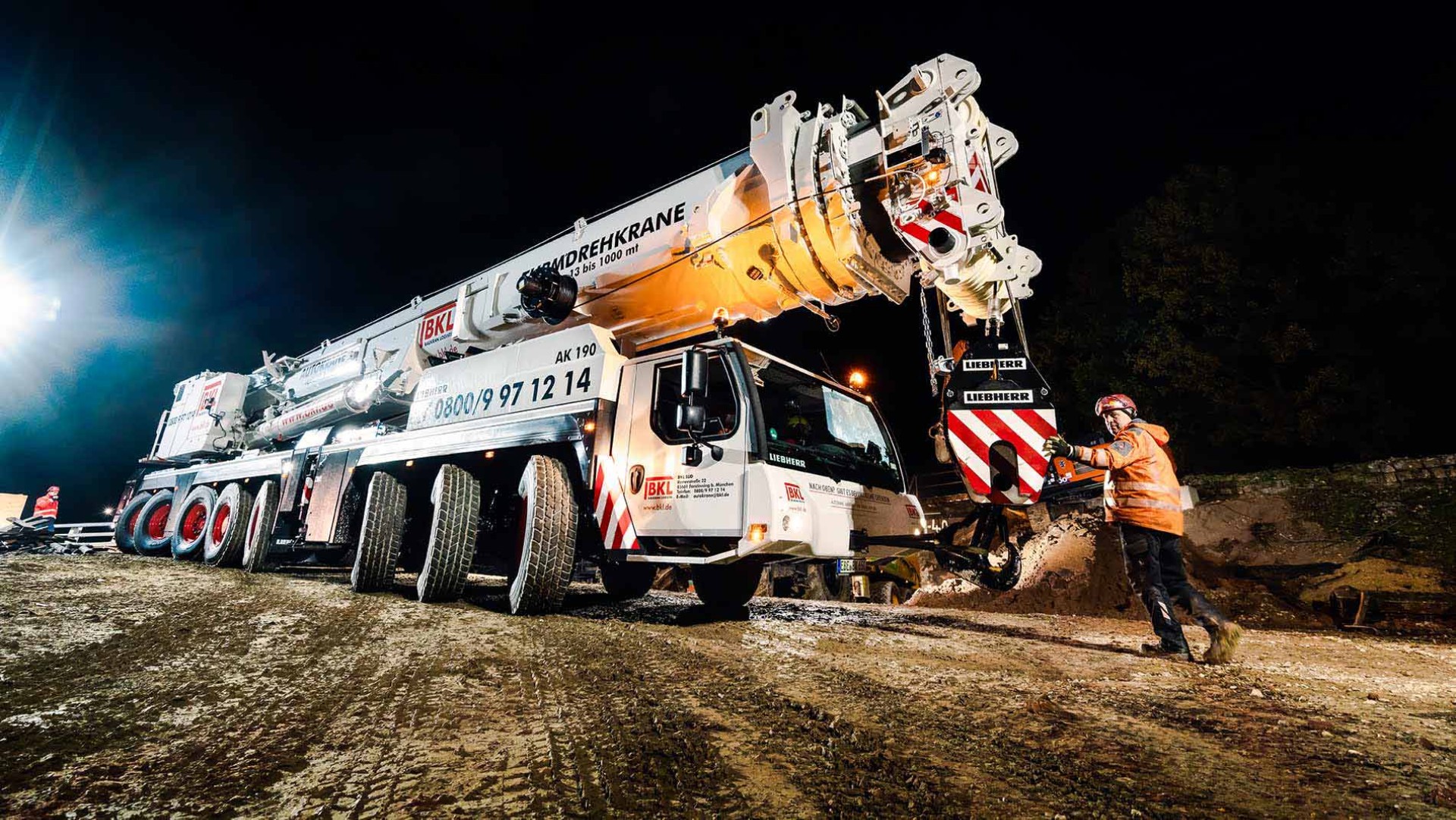
11 minutes | magazine 01/2021
VarioBallast® the problem-solver
Our new LTM 1650-8.1 is off and running. The successor to the legendary Liebherr LTM 1500-8.1 has been working on construction sites around the world for several weeks.
The ultimate crane on eight axles is off and running.
The first mobile crane of this type in southern Germany was faced with its initial challenge at the beginning of November. The powerful 8-axle crane was driven out of the factory at Ehingen to tackle its first job in northern Bavaria, where the brand new mobile crane in the livery of BKL Baukran Logistik GmbH had to dismantle sections of an old railway bridge. A difficult site in logistical terms, with a lack of space, time pressure and changing site conditions challenged the skill and experience of the crane team from BKL at this night job. Flexibility was required from both man and machine.
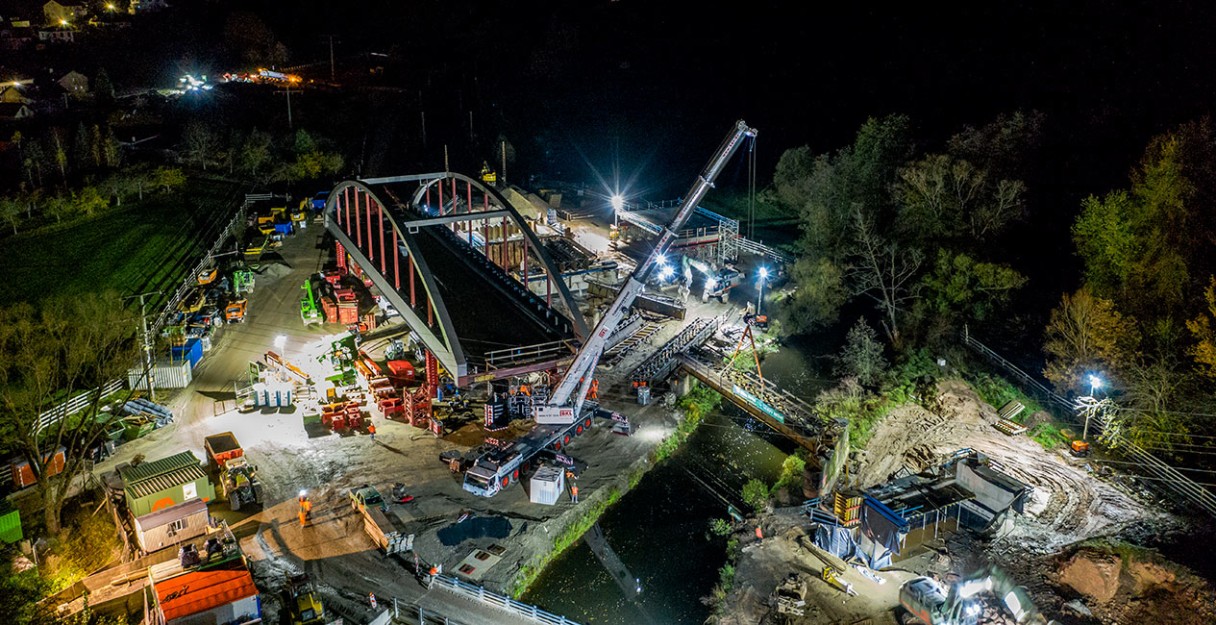
Extremely constricted setting – the LTM 1650-8.1 had very little space for the night job at its very first site. The slewing platform ballast had to be slewed under the new bridge structure, which was jacked up on stilts.
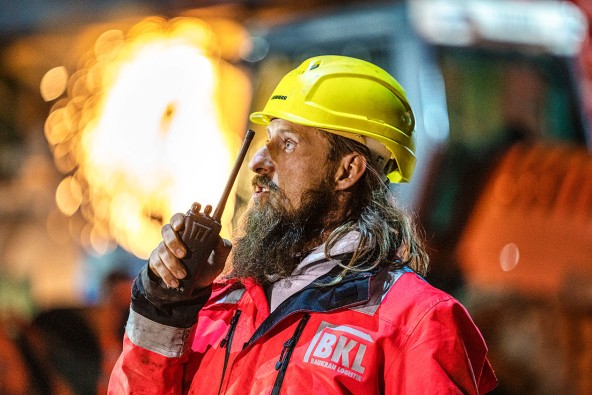
Precise commands – Steve, who interchanges with Steffen in the crane cab, is shown here supporting his colleague on the radio.
“Without VarioBallast® we would have had no chance here,” agreed the two crane operators Steve and Steffen straight away when they arrived at the site with their mobile crane as darkness fell. A short-term change of plan on the extremely constricted site meant that the set-up area originally planned for the vehicle was not available. The dilemma was that the new bridge was waiting to be installed on an area closer to the river on high stilts and would be an obstacle to the top ballast slabs when the crane was slewed. The initial ballasting plan meant that the ballast slabs were a little too high and therefore had to be amended.
The BKL team found a solution – the ballast radius on the LTM 1650-8.1 can be infinitely adjusted using a hydraulic slewing mechanism and set between distances of 6.4 and 8.4 metres. The slewing platform ballast, which can be modified in this way, was originally planned as a reserve for this job if parts of the 150 year old railway bridge proved to be heavier than calculated. Instead, VarioBallast® enabled the BKL team to complete the hoists safely even with reduced counterweight. The team placed less weight on the massive ballast frame at 115 rather than the planned 135 tonnes. The resulting lower height allowed the crane to be slewed under the steel arched bridge. At maximum ballast radius, the team was able to hoist the bridge sections weighing around 55 tonnes off the stone abutments at a radius of 23 metres.
By clicking on “ACCEPT”, you consent to the data transmission to Google for this video pursuant to Art. 6 para. 1 point a GDPR. If you do not want to consent to each YouTube video individually in the future and want to be able to load them without this blocker, you can also select “Always accept YouTube videos” and thus also consent to the respectively associated data transmissions to Google for all other YouTube videos that you will access on our website in the future.
You can withdraw given consents at any time with effect for the future and thus prevent the further transmission of your data by deselecting the respective service under “Miscellaneous services (optional)” in the settings (later also accessible via the “Privacy Settings” in the footer of our website).
For further information, please refer to our Data Protection Declaration and the Google Privacy Policy.*Google Ireland Limited, Gordon House, Barrow Street, Dublin 4, Ireland; parent company: Google LLC, 1600 Amphitheatre Parkway, Mountain View, CA 94043, USA** Note: The data transfer to the USA associated with the data transmission to Google takes place on the basis of the European Commission’s adequacy decision of 10 July 2023 (EU-U.S. Data Privacy Framework).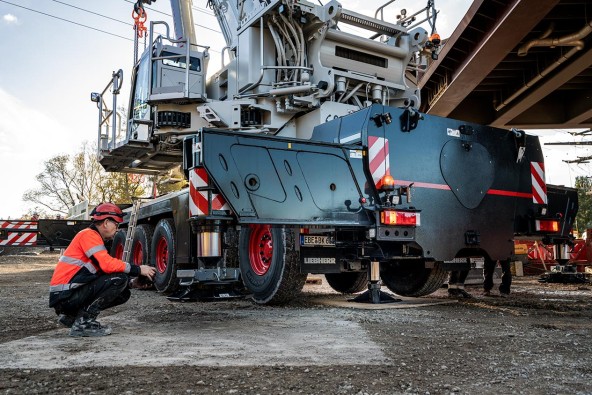
“The crane was on all four supports in just thirty minutes.” BKL employee and operator Steffen retracts the crane outriggers into the outrigger box by remote control after the job has been finished. The fifth support cylinder can be seen clearly under the rear. The LTM 1650-8.1 installs the outrigger box itself and does not require an auxiliary crane for this purpose.
“The crane was on all four outriggers after just thirty minutes”
BKL Baukran Logistik GmbH is a major construction and mobile crane logistics contractor operating from six sites with one of the largest, most modern crane fleets in Europe. The company was one of the first customers to order the new 700 tonne crane and the first in Germany to receive one. The lifting capacity values of the new crane in some areas almost reach those achieved by its big brother, the LTM 1750-9.1.
The new mobile crane is available with telescopic boom lengths of either 54 or 80 metres. Jörg Hegestweiler, Managing Director at BKL, says: “The crane with its telescope options and the variable ballasting system is a perfect addition to our fleet. For a complete supplier of crane solutions like BKL, the LTM 1650-8.1 is extremely attractive as we also have a number of large construction cranes in our fleet which extend up to 1050 metre-tonnes, and their erection always requires heavy components to be hoisted.”
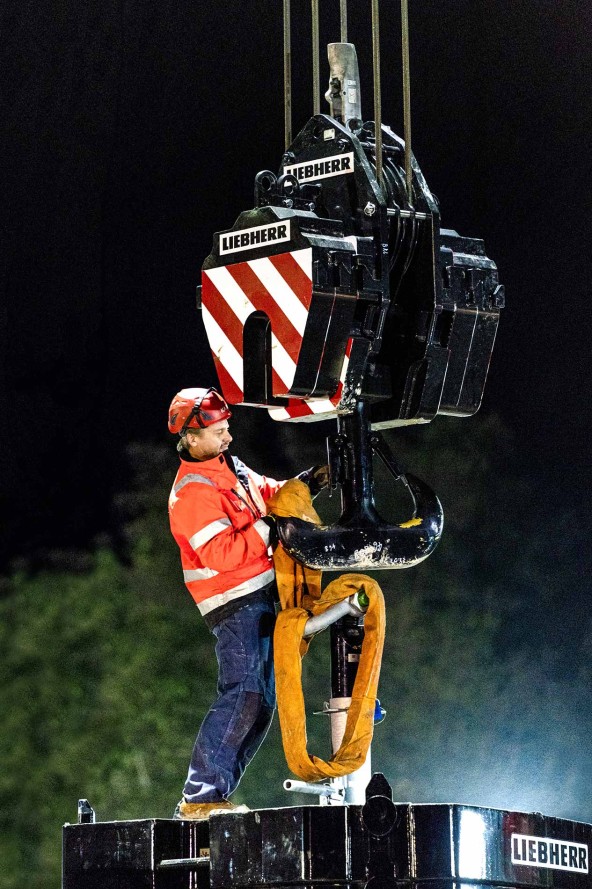
After his initial experience in real-world conditions, operator Steffen is impressed with the new 8-axle crane. “What I'm totally in awe of is the steering programs,” he declares. “They're a great support which enable us to manoeuvre the crane safely in constricted site conditions like here. That’s really great. The benefits of the infinitely adjustable slewing platform ballast enabled us to react quickly to different requirements. The whole system is designed to be very easy on the crane operator.”
The experienced operator includes the separate outrigger box on the LTM 1650-8.1 in his list of positive features. To comply with the maximum axle loads allowed on public roads, the complete rear support system for the crane is not installed until it reaches the site. An auxiliary crane is not required for this purpose. There is a fifth support cylinder on the underside of the large crane, which can be extended behind the last axle. A mobile crane then hoists the outrigger box, weighing around nine tonnes, off the low loader and can install it on itself. “It’s really fast,” says Steffen in awe. The box is simply docked into place and connected using quick-release couplings. The crane was on all four outriggers within just thirty minutes.”
The LTM 1650-8.1 – a new legend?
We have once again redefined the standards of progressive mobile crane technology with the new LTM 1650-8.1. The new crane has everything that you could possibly want. We are therefore absolutely convinced that we have created a tool for our partners which more than satisfies the high requirements for a modern mobile crane. You, our business partners, will decide whether we have once again managed to create a legend of the future with the LTM 1650-8.1. We have done our very best.
This article was published in the UpLoad magazine 01 | 2021.