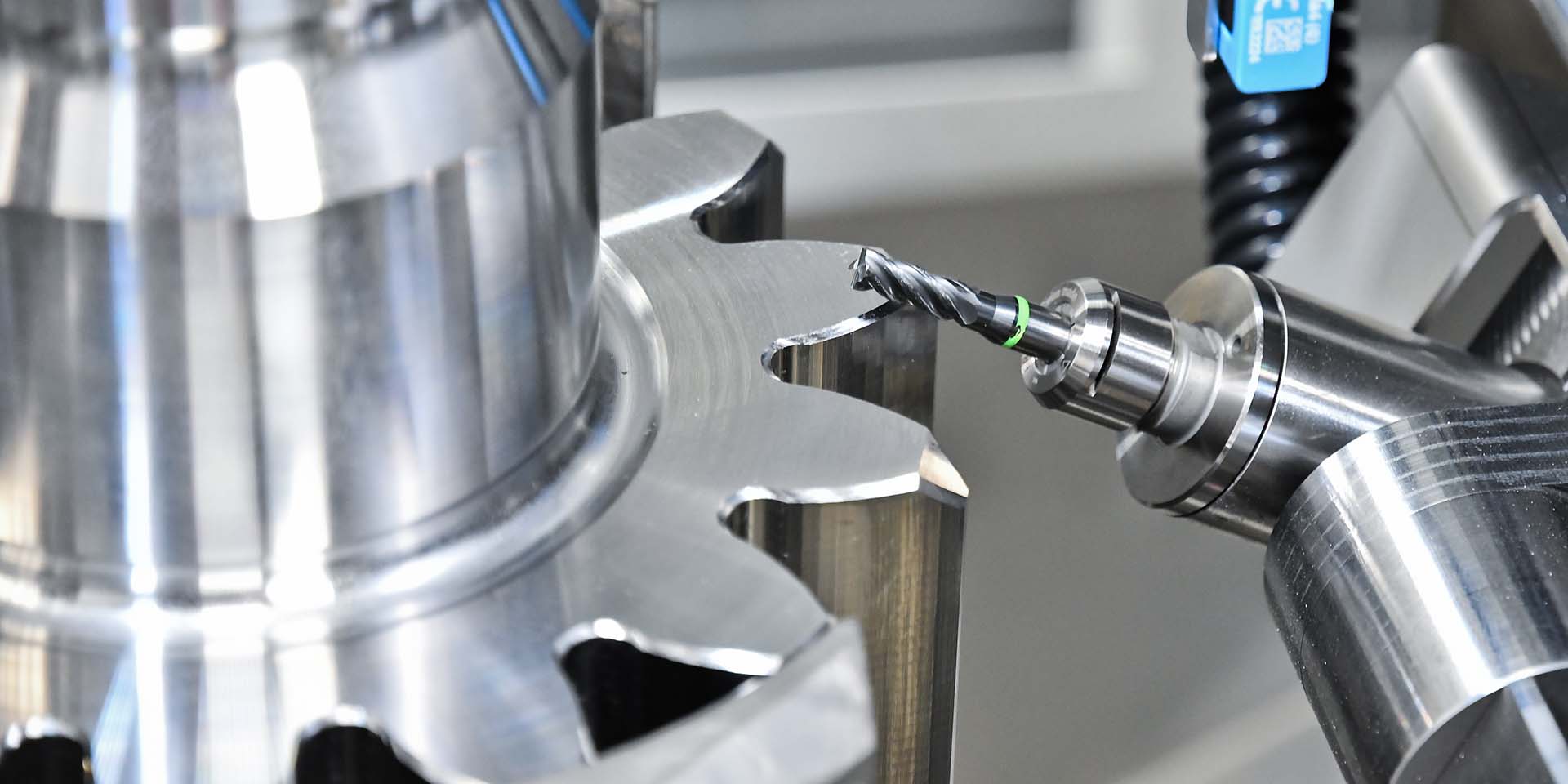
FlexChamfer: Maximum flexibility for deburring and chamfering gears
FlexChamfer
Economical deburring and chamfering even for small batch sizes
As power density increases, more focus is being placed on machining the face edges of gears. Innovative chamfering technologies are required in order to achieve the quality requirements and precise chamfer shapes that are demanded. One promising technology is the precise ChamferCut process, which produces the exact chamfer shape. However, conventional chamfering technologies reach their limits with small batch sizes and difficult component geometries. Particularly in the case of cluster gears, ChamferCut cannot machine all the gear positions.
The patent-pending FlexChamfer process is ideally suited for small batch sizes, both for simple and difficult workpiece geometries. In contrast to ChamferCut, which has its strengths in larger batch sizes, FlexChamfer allows flexible and cost-efficient production even for small and medium batch sizes. The universal milling cutters used are cost-effective and can be changed quickly and easily without the need for time-consuming retooling. This means that even small batches can be processed very economically.
Highlights
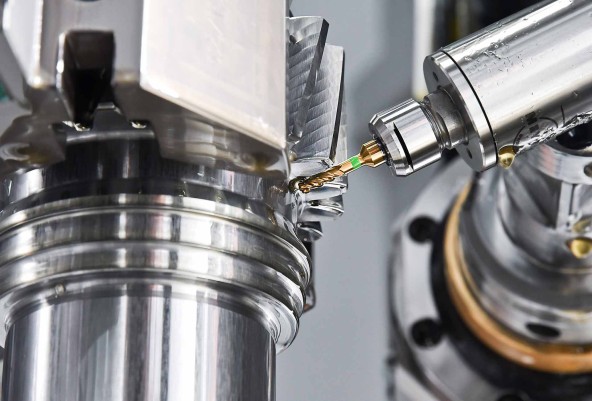
The advantages of FlexChamfer at a glance
- CNC-controlled refinement of chamfering with carbide milling cutters
- Generation of variable chamfer shapes with standard catalogue tools
- Especially suitable for external gears with or without interfering contour, as well as shafts and internal gears
- Can be used in hobbing, shaping and skiving machines
- Takes place during machining (depending on the cycle time for gear cutting)
- Ideal for small and medium batch sizes
- Quick set-up and changeover
- Wet and dry machining
Video
By clicking on “ACCEPT”, you consent to the data transmission to Google for this video pursuant to Art. 6 para. 1 point a GDPR. If you do not want to consent to each YouTube video individually in the future and want to be able to load them without this blocker, you can also select “Always accept YouTube videos” and thus also consent to the respectively associated data transmissions to Google for all other YouTube videos that you will access on our website in the future.
You can withdraw given consents at any time with effect for the future and thus prevent the further transmission of your data by deselecting the respective service under “Miscellaneous services (optional)” in the settings (later also accessible via the “Privacy Settings” in the footer of our website).
For further information, please refer to our Data Protection Declaration and the Google Privacy Policy.*Google Ireland Limited, Gordon House, Barrow Street, Dublin 4, Ireland; parent company: Google LLC, 1600 Amphitheatre Parkway, Mountain View, CA 94043, USA** Note: The data transfer to the USA associated with the data transmission to Google takes place on the basis of the European Commission’s adequacy decision of 10 July 2023 (EU-U.S. Data Privacy Framework).Applications: chamfering with FlexChamfer
FlexChamfer can be used for various technologies:
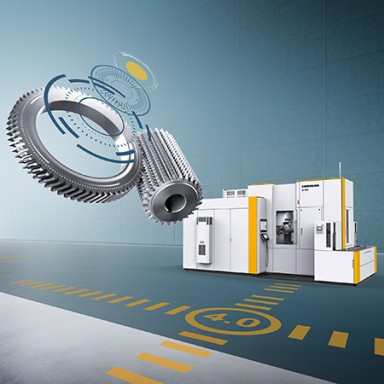
Gear hobbing
Liebherr has manufactured highly productive gear hobbing machines for decades. With its wide range of machine types, Liebherr can serve the needs of customers from a wide variety of industries from automotive to wind turbine manufacturers.
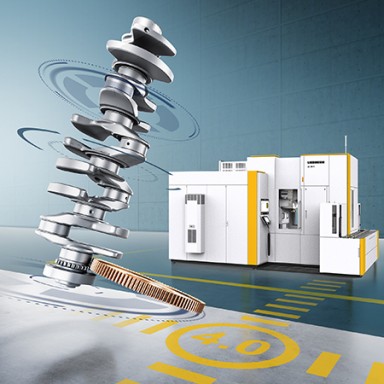
Gear shaping
Liebherr gear shaping machines are used in special applications. We design individual manufacturing solutions for our customers.
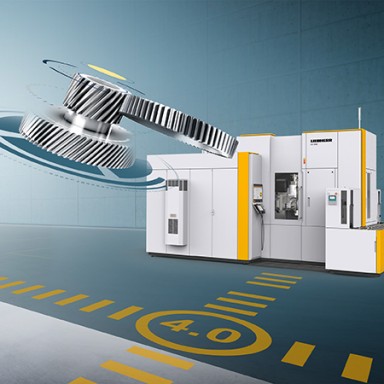
Gear skiving
With Liebherr gear skiving machines, you get the process, tools and machine including tool changer and automation from a single source.