Equipped for everything
Machine concept
Increased efficiency thanks to gear skiving
Gear teeth manufacturers are seeking alternative processes that are more productive and cost-effective than the gear shaping method and more flexible than broaching.
Successful gear skiving by means of:
- Machine
- Tool
- Process
The foundation for successful gear skiving is the rigidity of the machine: The cast iron machine bed absorbs the occurring process forces. In the machining head, a high spindle rigidity is achieved by means of a special bearing concept, which means that longer tool holders can also be used. This is particularly important for machining internal gears.
In combination with a burst-proof housing, the machine is suitable for both dry and wet machining with oil or emulsion.
In addition to the machine, the appropriate tool is crucial for a stable process. Our in-house tool development and manufacturing enables us to design the optimal tool for every workpiece - based on our vast knowledge of the gear skiving process.
The planned process must be taken into account when designing tools. Our intensive technological development and extensive tests on customer projects have given us a complete understanding of gear skiving and, with Skiving³, we offer a complete solution consisting of machine, tool and process.
The tailstock makes the machine suitable not only for external and internal gears but also for shafts.
Technical data
Module | 3.00 mm |
Workpiece weight | 25 kg |
Axial travel | 400 mm |
Shift distance | 400 mm |
Swivel angle of gear skiving head | 30 ° |
Max. spindle power | 16 kW |
Hob speed | 4,000 min-1 |
Tool diameter | 150 mm |
Variants
LK 180 | LK 280 | LK 180 DC | LK 280 DC | |
---|---|---|---|---|
Workpiece diameter (mm) | 180 | 280 | 180 | 280 |
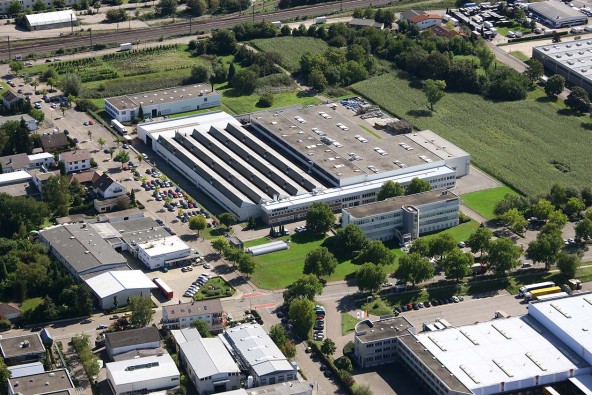
Liebherrs in-house tool production
Liebherr offers a comprehensive range of gear cutting tools, many years of experience in gear manufacturing, and the highest level of product quality down to the smallest detail. Our gear skiving tools are manufactured at our sites in Ettlingen, Germany and Collegno, Italy.