Technologies for the future
Constant investment into research and development play a key role in our long-term vision and strategy. This allows Liebherr-Aerospace and Transportation Systems to develop technologies that are employed in next generation aircraft and rail vehicles as well as in the automotive industries.
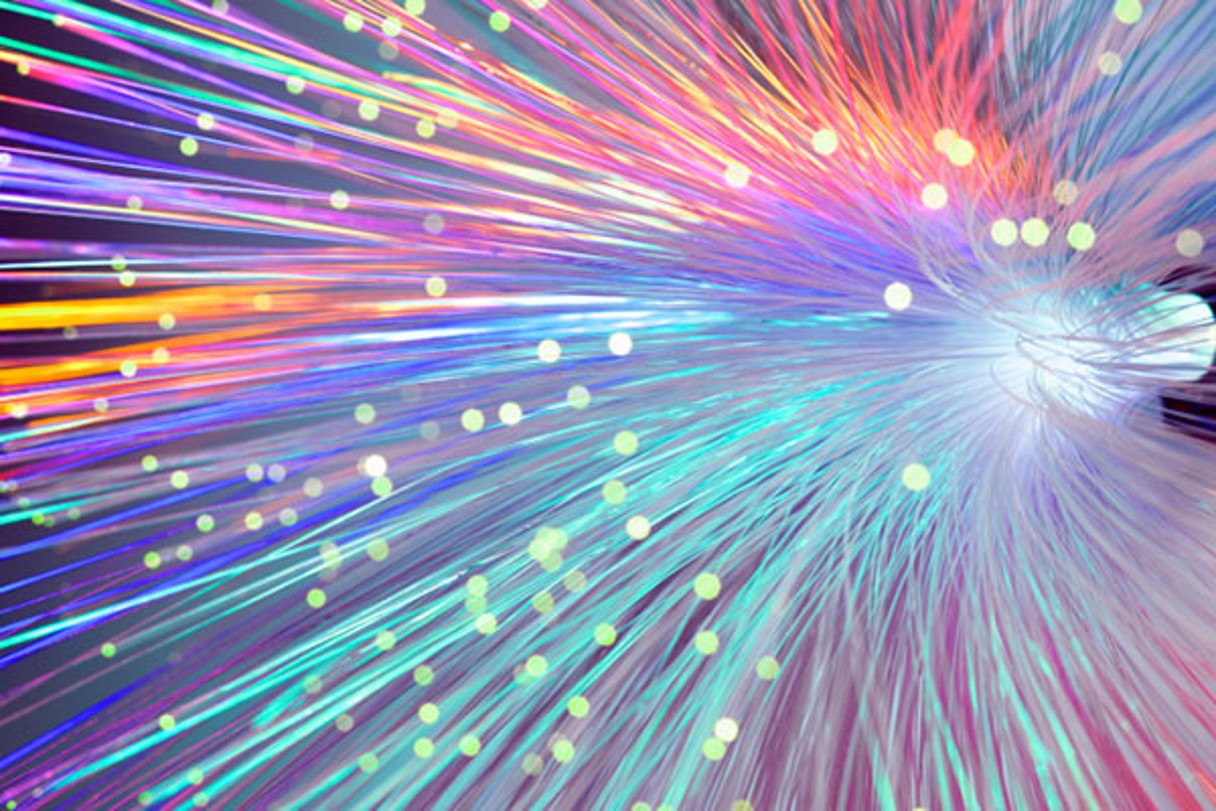
We develop technologies for tomorrow. (Photo: Getty Images / Rafe Swan)
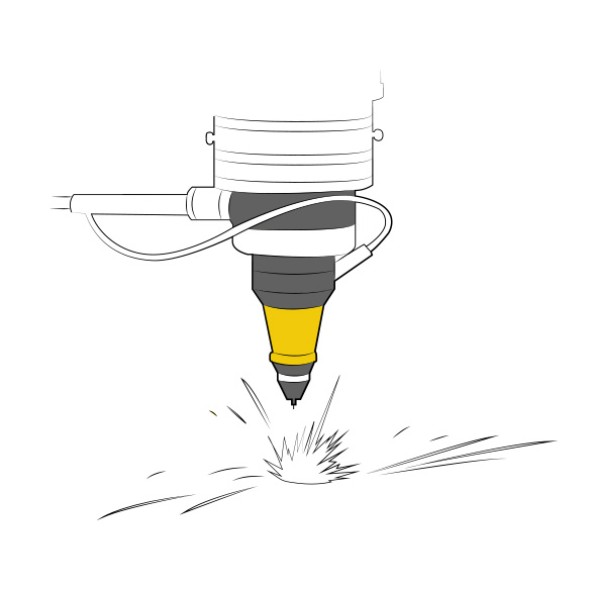
3D printing – the future emerging from the laser melter
Additive manufacturing is the name given to a process which uses digital 3D design data to build up a component layer-by-layer by melting material. The term "3D printing" is used more and more often as a synonym for additive manufacturing. However, additive manufacturing is a better description, indicating that the process involved is a professional production process which differs significantly from conventional subtractive manufacturing methods. Instead of milling a part from a solid block, for example, additive manufacturing builds up components layer by layer from materials which come in fine-powder form. Materials available include a variety of different metals, plastics and composites.
Examples of 3D printed products developed by Liebherr-Aerospace
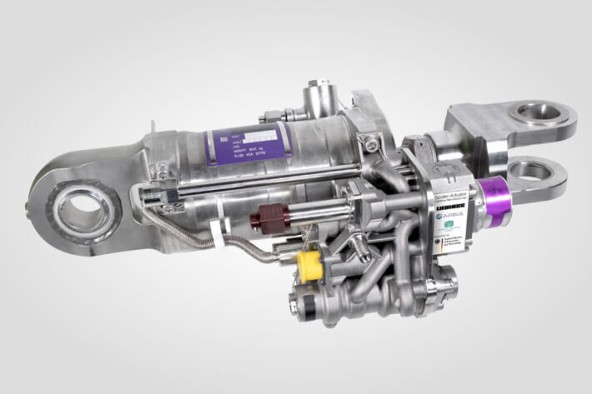
Spoiler actuator with 3D printed titanium valve block
New Technologies, Infinite Possibilities
World premiere: In March 2017, an Airbus A380 took off for the first time with a titanium valve block from Liebherr-Aerospace’s 3D printer and successfully completed its route. Never before has a hydraulic primary flight control component made from titanium powder using an additive manufacturing process been used in an Airbus.
The valve block is part of Liebherr-Aerospace’s spoiler actuator and fulfills a number of important functions on board the A380, when it comes to maneuvering the airplane, for example, and braking after landing. The 3D printed component works like a traditional forged valve block but has two crucial advantages: It is 35 percent lighter and is made up of fewer individual parts.
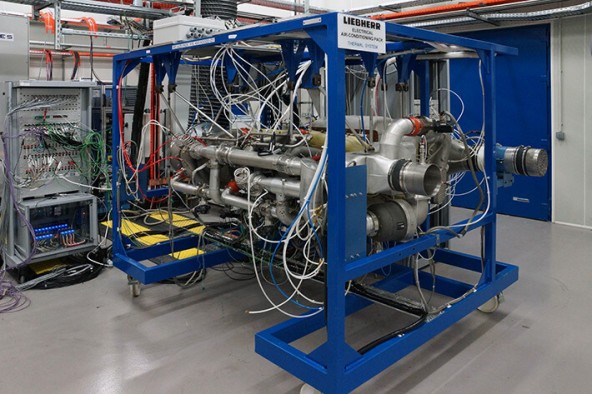
Electrical air conditioning pack test rig at Liebherr-Aerospace in Toulouse (France)
For several years, there has been a strong trend towards more electric systems for the next generation of aircraft. This approach will allow to improve safety and to increase the overall efficiency of the airplane while decreasing noise emissions and fuel burn.
The more electric systems developed by Liebherr are designed to achieve such challenges, decreasing weight and engine consumption thanks to the ability to adjust, for each flight phase, the energy generation to the precise needs of the onboard consumers.
Technologies for tomorrow
To be ready for the aircraft that will enter service in the future, Liebherr-Aerospace, in line with the long-term vision of the Liebherr Group, consistently invests above industry-average ratios into the R&D activities in its fields of expertise: landing gears, flight controls, actuation, gears and gear boxes and air management systems.
In particular, Liebherr works on such topics as next generations of electric actuators, e-taxiing, electric wing, electric environmental control system, auxiliary power generation systems, hydraulic power supply, and thermal and power management on-board the aircraft.
The future of aviation has begun – find out in our story how Liebherr is a part of it.
Video: Clean Sky/Airbus Flight Lab

A Liebherr fuel cell air compressor is part of the PROME P390 fuel cell system built into the EUNIQ 7. - © SAIC Maxus
Already 20 years ago, Liebherr started to develop technologies for power generation based on fuel cells. It all started with motorized compressors for automotive fuel cell systems, which have been developed and matured in cooperation with major automotive manufacturers around the globe. In the meanwhile those efforts have paid off and Liebherr compressors have entered into serial production, for example for the PROME P390 fuel cell system powering the new MPV model EUNIQ 7 of Chinese car manufacturer SAIC Maxus Automotive.
Due to its wide experience of highly-integrated on-board aerospace systems, Liebherr was also one of the first technology companies involved in the development of fuel cell application on board of an aircraft, like the replacement of the ram air turbine or the auxiliary power unit (APU).
In 2018 General Motors and Liebherr announced an agreement to explore opportunities and to collaborate on the development of fuel cell systems for aircraft applications, based on latest fuel cell stack technology developed by General Motors.
The use of hydrogen on board of an aircraft for propulsion or generation of electricity is expected to become reality within the next 15 years. Liebherr is investing research and technology effort to be part of this revolution by supplying a power generation system based on fuel cell technology, to provide electrical power for all aircraft systems. This will relief the next generation aircraft engines from any off-takes, which are today reducing the engine efficiency.
The power generation system development will be supported by Liebherr’s unique component design system integration and test capabilities in its test center in Toulouse, where electrical loads and thermal loads can be coupled in order to optimize the system performance.
