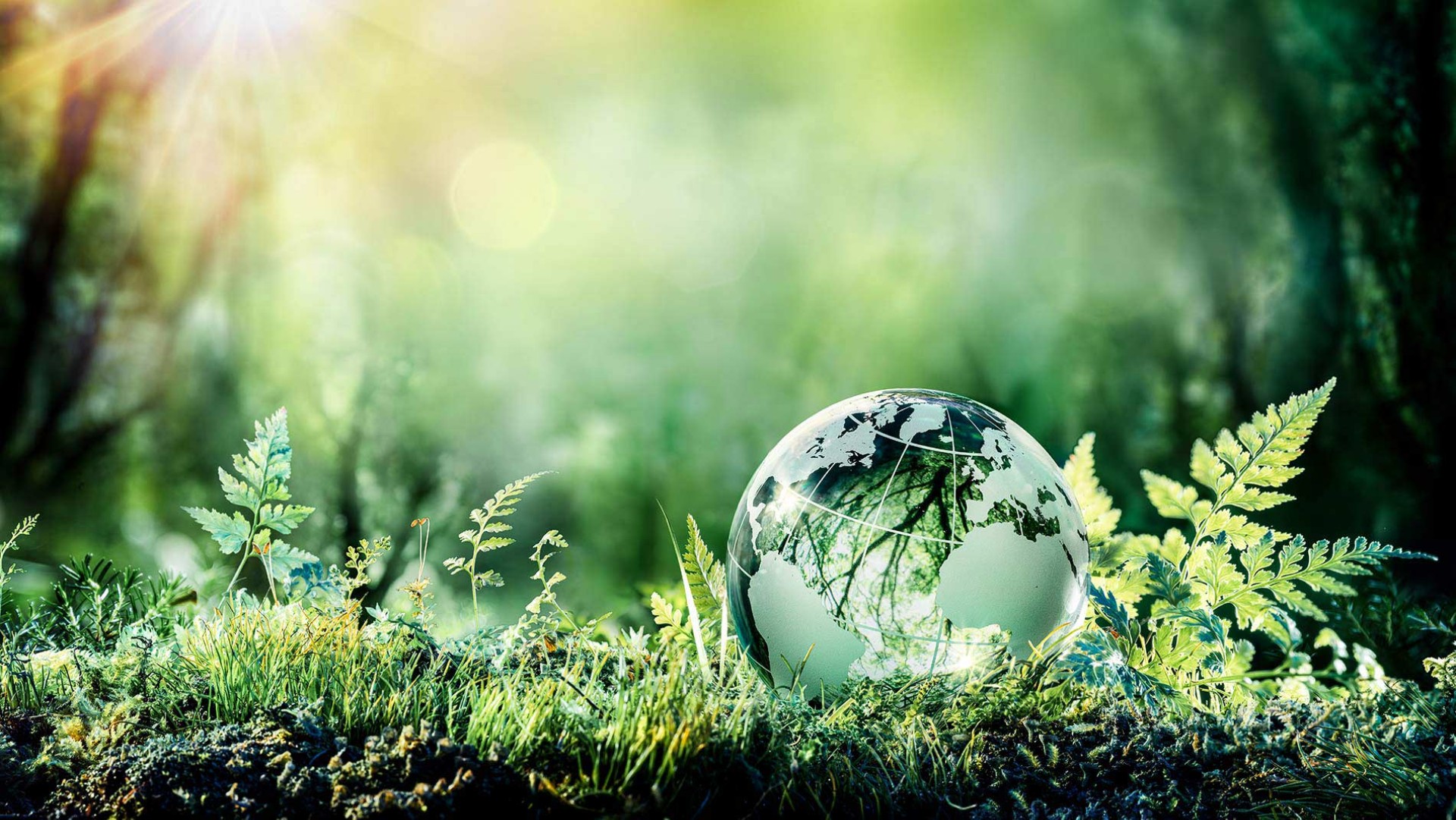
12 minutes | magazine 02/2021
Sustainable
We are delighted to announce the launch of a new series of articles, entitled: “Sustainable”. We have at least three reasons for doing so: Firstly, the topic is extremely important. Secondly, it is much too complex and multi-faceted for a single article. And thirdly, it is constantly changing due to technical developments.
Sustainability and protecting the environment
“The energy revolution will be expensive!” The media loves headlines like this and produce them on a regular basis. But one thing has now become very clear – “No energy revolution” is far more expensive. Climate change is already costing incredible amounts of money and, sadly, also people’s lives. Australia is one of the latest examples of this, after the country experienced severe drought with horrendous forest fires followed by once-in-a-century flooding. Millions of climate refugees around the world are looking for new homes. And the situation is only going to get worse.
Unanswered questions
Will the climate targets from the Paris Accord of 2015 be achieved? Do they actually go far enough? We do not know (yet). But what we do know is that we all have our part to play, as consumers and manufacturers. The same applies to both categories – important decisions have to be made. But to make the right decisions, we need knowledge based on science, particularly about what we are trying to achieve. And there is still plenty of uncertainty about this. What heating system should I install in my home? Will it really be sustainable? Should I buy an electric car with a battery or fuel cell? What else will the future bring? We read about the development of new batteries with significantly higher capacities, which can be charged more quickly and are also cheaper to buy. There are also some interesting technical developments in hydrogen and fuel cell technology. But will these only work in laboratory conditions or are they suitable for mass production and also affordable?
Good news
Despite all these unanswered questions, there is at least one piece of good news – the sun, wind and water supply more than enough energy. And the curve for the global use of these renewable energy sources is on a steep upward trend. For example, in 2020 China produced twice as many systems for wind and solar energy than in the previous year – 72 gigawatts of wind energy plus 48 gigawatts of solar energy in just one year. Other countries are also gearing up their expansion of renewable energy sources.
And we as a company also have to make some good decisions, both for us and our customers who will continue to need powerful, economical and high quality products. Sustainability must not result in any compromise in these features.
Openness to technology
Liebherr manufactures machines which must perform reliably in a very wide range of conditions in a whole host of different industries. Machines which our customers use to tackle a wide range of different projects and earn money. Machines which have to satisfy some very complex requirements. So what is the Liebherr approach to these latest challenges? It embraces them by being open to technology! That means that we never turn our back any type of power unit without checking it out very carefully. We look at every one of our machines in great detail and ask ourselves what sort of drive unit we could use to best satisfy our customers’ demands whilst also helping to reduce the level harm they do to the environment. This is why Liebherr carries out research and development work in several very different directions.
Electric motors with a power cable or batteries are a good option for some machines. And hydrogen could be one possible alternative where this technology hits the buffers. With this in mind, Liebherr is working flat out on the development of hydrogen engines. The development of CO2 neutral fuels could also make a valuable contribution to limiting global emissions of greenhouse gases.
You can look forward to lots of interesting articles and topics in our new “Sustainable” series in future editions of UpLoad. And we have another piece of good news. In the past we have managed to achieve a great deal and are currently working on implementing some detailed solutions which will have a massive effect. Let’s look at a few examples from our Mobile and Crawler Cranes Unit.
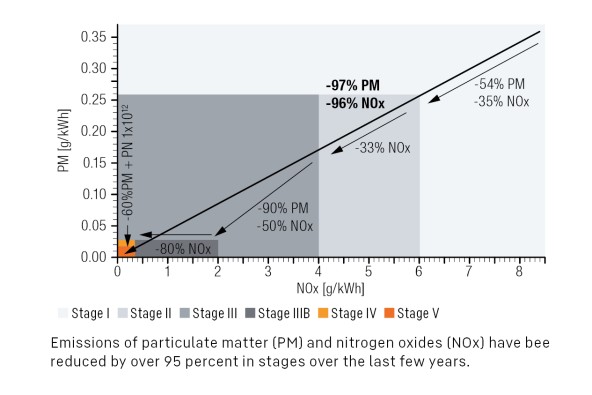
Exhaust emissions reduced by over 95 percent
Liebherr has been developing and building its own diesel engines for almost 40 years. Massive progress has been made, particularly over the last few years, in the reduction of exhaust emissions. This has gone hand-in-hand with the ever more stringent statutory requirements that have been implemented in stages. Emissions standard Stage V currently applies to mobile cranes in Europe. Over the last 20 years, exhaust emissions have been reduced in several phases by over 95 percent, despite the fact that the cranes work very hard every day both on roads and on sites. The standard mainly concerns nitrogen oxides and particulates. Today, you can reach into an exhaust pipe whilst wearing a white glove. It will stay white. Particulates are at the limits of what can be measured whilst a crane is driving and operating. This means that new engines and exhaust treatment systems have an enormous amount of potential because the Stage V limit values have only applied in Europe to date. And even there, they only apply to new models.
Total emissions could be reduced even faster and more effectively than is happening anyway by replacing older cranes with new ones. This would definitely be significantly more effective than imposing even more stringent limit values, which are already very low and have been achieved at massive expense.
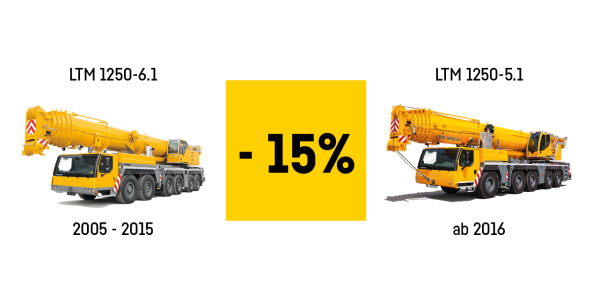
CO2 reductions through technical developments
We launched ECOmode and ECOdrive around ten years ago. ECOdrive reduces fuel consumption and CO2 emissions by around 5 percent when the crane is being driven. The reductions achieved by ECOmode during crane operation are up to 10 percent. This is done exclusively by means of intelligent software. At almost the same time, we converted our entire crane portfolio to the single-engine concept. This means that instead of one engine each for driving and lifting, only one common engine is installed. This also reduces the CO2 footprint during both production and maintenance work.
The progress we have made in lightweight design is another important point. Today, we achieve at least the same performance from a crane which weighs significantly less than previously. One outstanding example of this is that our current 5-axle LTM 1250-5.1 crane can hoist loads which, just a few years ago, had to be handled by the 6-axle LTM 1250-6.1. This means that a crane weighing 60 tonnes rather than 72 tonnes now drives to the site (with a maximum ballast 148 rather than 169.5 tonnes). Within just 10 years we have reduced its weight by around 15 percent. This results in a corresponding reduction in fuel consumption and CO2 emissions while the crane is on the road and on site. This reduction on a 250 tonne crane also applies to all other crane models and the time period can be extrapolated to 30 years – representing an extremely significant reduction in the volume of CO2!
CO2 neutral fuels
One very interesting approach is based on the following consideration – perhaps it is not the engines which require modification but the fuels. Perhaps we do not have to make that many changes to the drive trains, but simply use different fuels in them. The biggest challenge is storing fuel on a crane. Currently, of course, we have a diesel tank for this purpose. However, new problems may arise, for example with hydrogen, due to the fact that as a fuel it is massively different in terms of weight, volume, pressure and temperature.
Hydrogenated vegetable oils (HVOs) do not pose the same problems and may therefore be an interesting alternative. These are edible oils which can be converted into hydrocarbons by adding hydrogen. They are mainly produced from vegetable and other edible oil waste. So waste oil becomes fuel! As it is possible to adjust the oil’s properties fairly accurately, the fuel can be used in various mixtures and even in a pure form. Its use will significantly reduce greenhouse gas emissions.
We also believe that these fuels are very interesting because Liebherr manufactures industrial machines with extremely long service lives. If Germany and the EU continue to reduce their emission limits in the next few years, this does not mean that older machines with diesel engines simply have to be scrapped. On the contrary, in Asia, Africa and South America, these machines continue to operate for many years, which also has an effect on our climate.
Regardless of whether and how quickly we can fit more machines with engines which reduce CO2 emissions, the advanced development of fuels based on hydrogenated vegetable oils or synthetic fuels from renewable energy sources can make a valuable contribution to reducing global emissions of greenhouse gases. It is simply not possible to make the process any faster or more effective than through the use of HVO!
We are currently working on making our entire mobile and crawler crane fleet HVO-ready. Our cranes have already undergone extensive testing and trials. On a 5-axle mobile crane, for example, emissions of CO2 fall by 74 percent if we take into account the whole of the crane’s service life, including the production process. Cradle to grave, in other words. This is a whole new milestone for CO2 emissions. The main reduction comes, of course, during its long operating phase, due to the fact that our cranes deliver such a long service life.
To make HVO or other synthetic fuels attractive for our cranes, they must be available nationwide and in plentiful quantities at filling stations, as is the case today with diesel. That will not be possible from one day to the next. But we are making a start.
Local zero emissions
In addition to achieving the goal of climate neutrality, more and more towns and regions would also like to achieve the status of local zero emissions. We are therefore also continuing our development work to meet this local zero emissions strategy. At the start of 2022, we are planning to unveil a standard, practical machine fitted with an additional electric crane drive unit. We do not want to give away too much at this stage. But it will be a particularly compact crane with a hybrid drive which will also be very useful for operating inside buildings.
One thing that all these extremely important changes and developments have in common is that progress and innovation are evolutionary processes. You have to stay on the ball and you can never relax. So, let’s do what is required using the same method we always use – working together in a successful team.
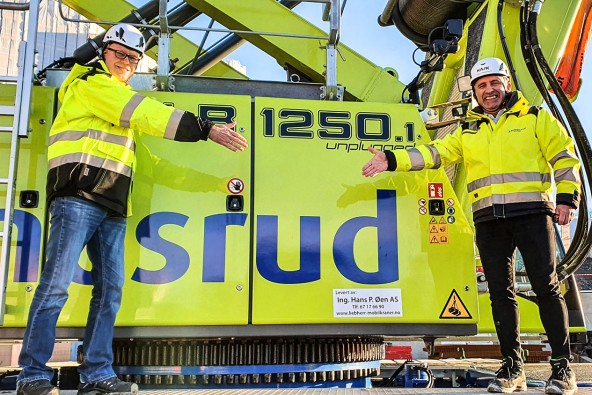
Liebherr Representative Thomas Bohlin and Eirik Kynningsrud (right) at the crane handover.
Inspiration in Oslo
In 2019, the EU Commission named Oslo as the European Environmental Capital – mainly because of its conservation of natural areas and low pollution levels. However, the capital of Norway is by no means resting on its laurels. On the contrary, it plans to reduce its emissions by 95 percent by 2030 and be an inspiration for other cities.
The no less ambitious crane and transport contractor Kynningsrud Nordic Crane AS is based not far from the aspirational capital city. “In Norway we have to face the challenge that our government wants construction sites with zero emissions”, explains company boss Eirik Kynningsrud. “And we want to be a leading contractor for these projects. We always try to win orders by being the green alternative.”
Kynningsrud has therefore already replaced lots of its older mobile cranes with new machines whose engines comply with the Stage V emissions standard. In addition, it has purchased its first MK 88-4.1 mobile construction cranes which can be operated with electricity on site to meet the local zero emissions requirement. The company already has firm plans in place to purchase more cranes.
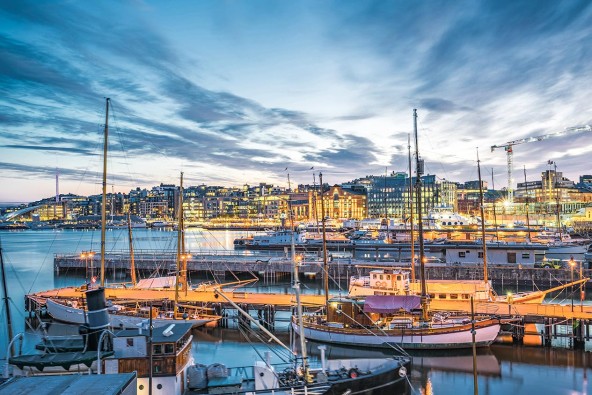
Kynningsrud’s latest addition to its fleet is an LR 1250.1 unplugged, a battery-powered crawler crane from the Liebherr plant in Nenzing. Eirik Kynningsrud placed the order for the crane before he had actually seen it: “It’s great that we can work without creating any emissions and, of course, that is attracting certain amount of attention and generating a lot of positive publicity for us. We want to be the leading company for providing zero emissions cranes. The future of the crane industry in Norway is zero emissions.”
Kynningsrud is open to any alternatives which can reduce exhaust fumes and CO2 emissions. The company was therefore a valuable partner for testing the use of HVO fuel in Liebherr mobile cranes. The field test with HVO, which is already well established in Scandinavia, lasted for a year involving 2200 hours of operation. The positive results confirmed the tests carried out in-house at Liebherr in Ehingen using around 7000 litres of HVO.
This article was published in the UpLoad magazine 02 | 2021.