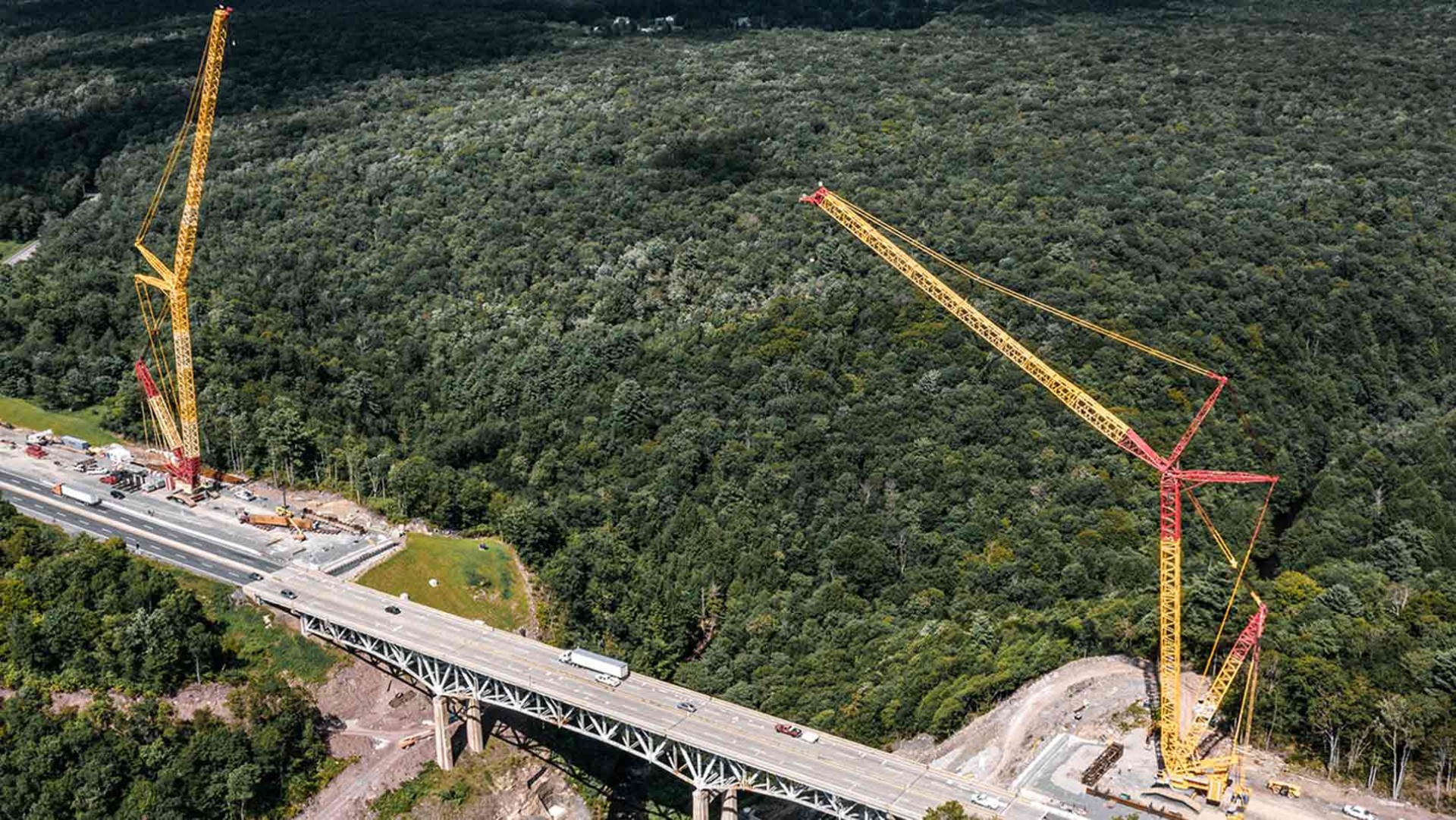
10 minutes - magazine 01 | 2024
Reaching the goal in tandem
Infrastructure expansion on the American east coast.
Reaching the goal in tandem
Infrastructure expansion on the American east coast.
Stunning crane sight at Hawk Falls bridge
Using not one but two major crawler cranes for a bridge replacement is not a very common sight. Having two LR 11000s operating on a single bridge in Pennsylvania, United States, is worth taking a closer look at this North American infrastructure project.
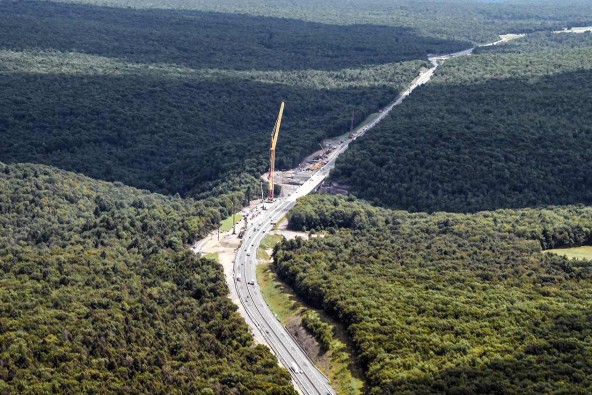
Hawk Falls is maybe better known to outdoor adventure seekers than to the readership of our UpLoad magazine, offering a great hiking and biking trail system in Eastern Pennsylvania. Driving from New York City to Pittsburgh, Hawk Falls is located on Interstate 80. This is a very important road leading from New York through
Pennsylvania to Cleveland and the Great Lakes area. In the rather tranquil area of Hawk Falls, two Liebherr LR 11000 crawler cranes, owned by Buckner HeavyLift Cranes are working simultaneously on a major bridge replacement, changing the quiet landscape into a stunning industrial engineering sight. The entire bridge replacement is done by the Trumbull Corporation.
Facts and figures
But first, let’s go through some figures about the new bridge and project site: The overall length of the new steel arch bridge will be 200 metres (720 ft). The two large crawler cranes will install a 142 metre (465 ft) steel arch span as well as two 18 metre (60 ft) I-girder spans. The new steel structure will at the end stretch over the 73 (240 ft) deep ravine and will carry the turnpike’s Northeast extension (I-496) over Mud Run in Carbon County, Pennsylvania. The huge extension project also includes a single-span steel girder bridge crossing Hickory Run Road. For such a large scale and complex project, the right cranes play an important role.
“Buckner has strategically expanded its fleet of Liebherr LR 11000 crawler cranes to over 30 units in the past decade. The recent surge in demand for higher capacity cranes underscores the LR 11000’s exceptional versatility, positioning it as the ideal solution to address the ever-changing demands of the infrastructure sector, particularly in areas like bridge construction,” said Brian Miller Vice President of Sales, Buckner.
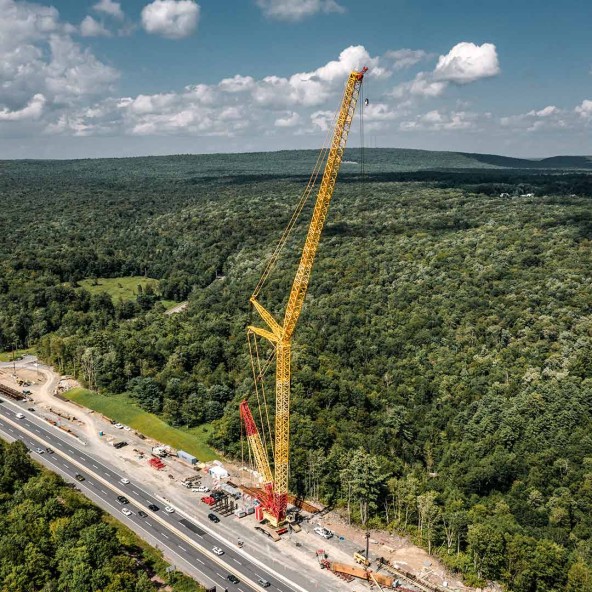
Starting Point
Back in July 2023, both of the Buckner LR 11000s arrived on the Hawk Falls bridge. Starting with the assembly of both cranes, Buckner’s team was already tasked with a huge challenge: limited space. As traffic on the existing part of the road had to continue and a mountainous terrain lies next to the road, space was really confined. Setting up the two large crawler cranes, required a SDWB2 configuration with 66 metre (217 ft) main boom, 90 metre (295 ft) W luffing jib, 210 tonnes (463,000 lb.) superstructure counterweight, 50 tonnes (110,200 lb.) central ballast, and 450 tonnes (992,100 lbs.) of counterweight on the tray.
The maximum weight of the lift for this job will be 41 tonnes (90,000 lbs.) at 125 metre (410 ft) radius for both sides. And right from the start it was clear: This is not a quick job, as the two crawlers are projected to remain on site until March 2024.
Variety of challenges
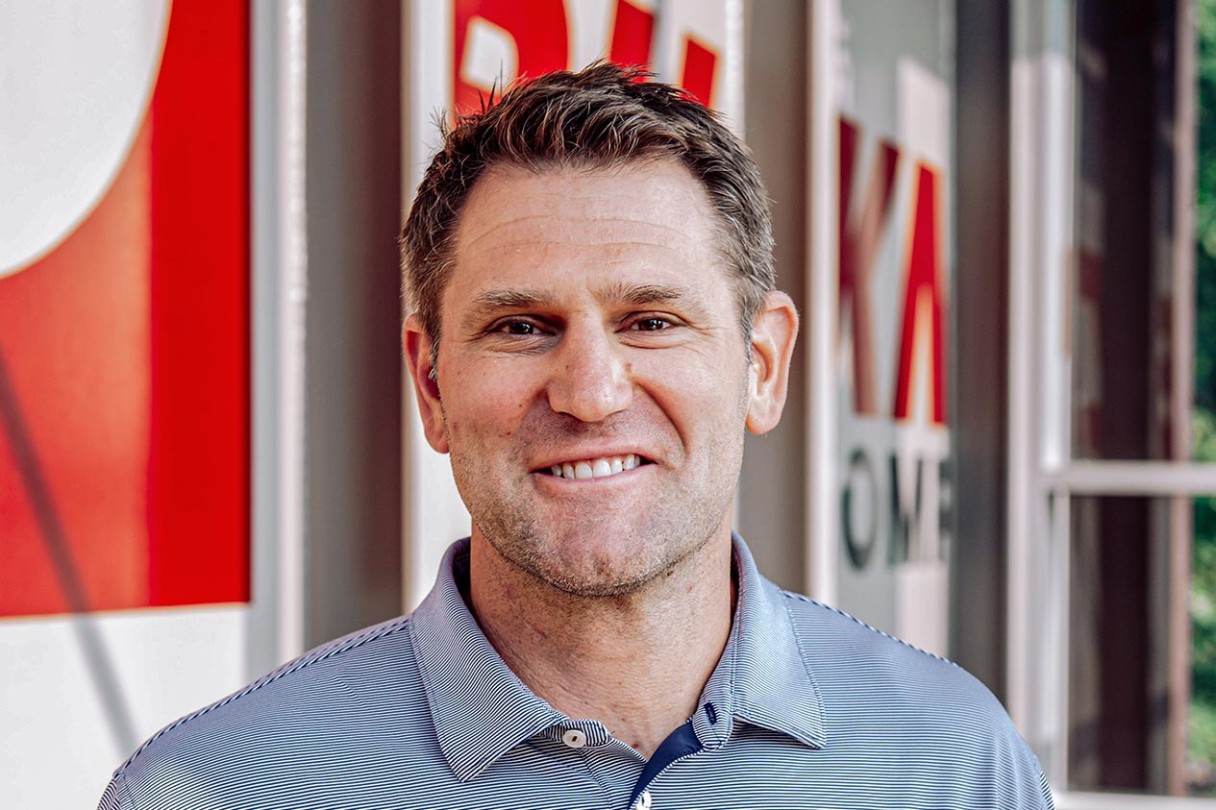
Brian Miller, Vice President of Sales, Buckner
Due to the size and complexity of this bridge replacement, the project team faced a variety of challenges throughout the duration of the project. As both LR 11000 crawler cranes are working simultaneously to complete the installation in a timely manner, there is a limited work area to deliver, prepare and erect the structural steel elements. Once the middle piece is in place and the cranes begin lowering the bridge into position, there is only 0,6 centimetres (¼“) tolerance for positioning the beams. This area of Pennsylvania also has varying weather throughout the year, and the ambient temperature has to be a specific degree in order to keep all the plates from expanding and contracting. Additionally, a ravine runs beneath the bridge replacement causing difficult site access to construct temporary shoring towers as well as environmental constraints with the Pennsylvania park service.
“But with its adaptable boom configurations and heavy lift attachments, the Liebherr LR 11000 seamlessly complements Buckner HeavyLift Cranes’ extensive fleet, embodying a comprehensive solution bolstered by our highly skilled professionals, our collaborative culture, and an industry-leading commitment to safety, which all are highly important points for such a project,” said Miller.
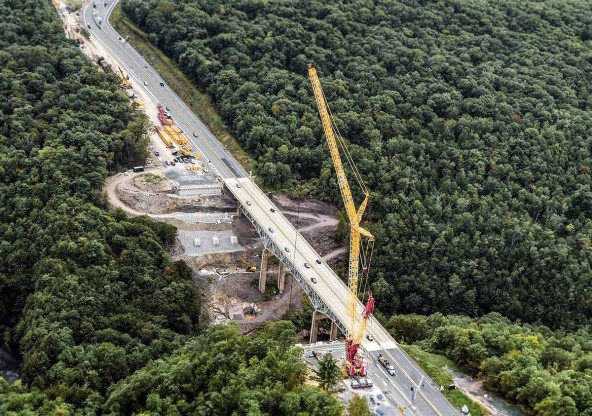
Two partners, one project
Buckner HeavyLift Cranes offers one of the largest crawler crane fleets in the United States, owing the largest LR 11000 crawler crane fleet around the world. With 75 years of experience, Buckner provides reliable, quality, and safe services to the heavy commercial and industrial market. Due to the massive size and undertaking of this project, the Trumbull Corporation turned to Buckner HeavyLift Cranes to rent the two Liebherr LR 11000 crawler cranes to complete the difficult job.
Trumbull Corporation is a family-owned business specializing in heavy and highway contractor and construction management. Established shortly after Buckner in 1955, the company is based out of Pittsburgh and operates throughout Pennsylvania, Maryland, West Virginia, Ohio, New York, and New Jersey offering best-in-class heavy civil and highway construction. Sharing the same values and principles, the two fit well together for such a project.
Standing strong
The LR 11000 crawler crane was presented to the North American market approximately 10 years ago and can cover a wide range of jobs with its various boom versions including port handling, industrial construction, infrastructure, or wind power. The crane’s design is also perfect for constricted areas, such as refineries. The crawler crane is designed for a transport width of 3.5 metre (11.5 ft) and a transport height of 3.2 metre (10.5 ft) ensuring easy manoeuvrability and fast transportation all over the globe.
“The LR 11000 is an extremely flexible crane when equipped with the derrick and ballast tray, allowing for infinitely variable ballast radius for complex lifts. In the case of this project at Hawk Falls, the long luffing jibs allow for a very large lift radius on the jobsite where cranes cannot get closer to their final lift location,” said Jim Jatho, Liebherr USA, Co. Product Manager of lattice boom crawler cranes. “As is normal for Liebherr cranes, the lightweight lattice sections can be slid into the larger sections saving both space and money. Additionally, special wind power configurations for turbines, blades and tower segments all over the globe deliver unique lifting capacities in this crane class.”
Liebherr’s crawler crane portfolio provides an array of choices for customers with heavy-duty needs and specific site requirements to get the job done right.
The pipeline, which is 1 kilometre long in total, has an outer diameter of 90 centimetres, weighs 500 kilograms per metre and weighs a total of 500 tonnes. “Our company prefers to work with Liebherr cranes,” adds Van Dijk. “The main reason for us is that the machines are reliable and of good quality. Liebherr also offers good customer service.”
This article was published in the UpLoad magazine 01 | 2024.