Successful conversion of production at Halewood
Ford produces electric drive units using Liebherr gantry systems
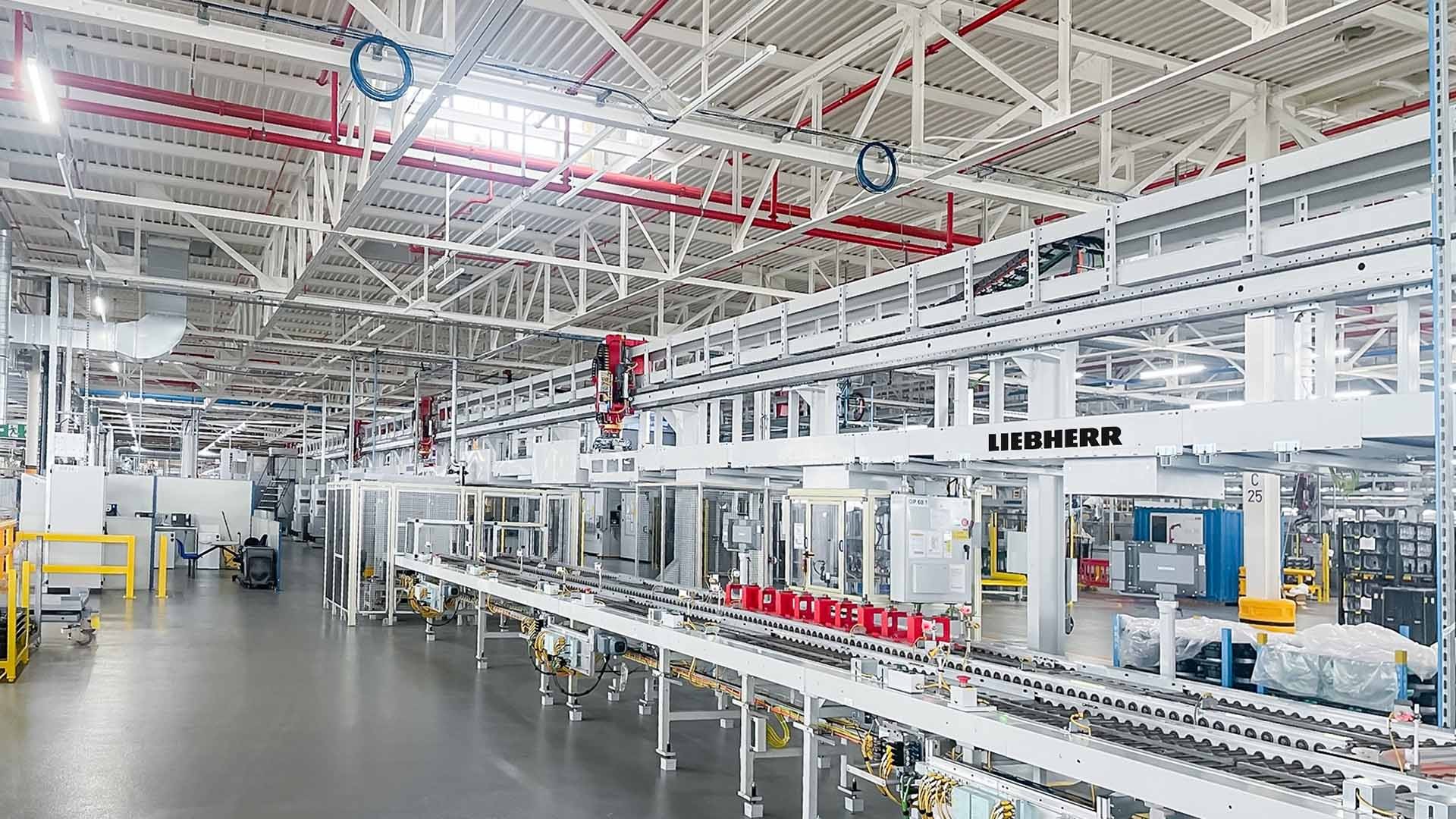
Successful conversion of production at Halewood
Ford produces electric drive units using Liebherr gantry systems
Successful conversion of production at Halewood
Ford produces electric drive units using Liebherr gantry systems
Successful conversion of production at Halewood
Ford produces electric drive units using Liebherr gantry systems
E-mobility is taking hold around the world – and the automotive industry is changing. Many manufacturers are shifting from internal combustion engines to electric powertrains. The Ford Motor Company – a long-term partner of Liebherr-Verzahntechnik GmbH – will be making most of the electric drive units for its European production at its UK transmission plant at Halewood near Liverpool. As before, Ford will be using Liebherr gantry technology, but for electric drive units rather than transmissions for internal combustion engines.
The world‘s sixth-largest car manu-facturer aims to “electrify” its portfolio in Europe. The switch to producing electrical components in Halewood plays a crucial part in this. At this plant, Ford has invested for the first time in Europe in the production of components for all-electric vehicles, producing power units consisting of an electric motor and a single-speed transmission. 420,000 units will come off the production line annually instead of the previous 250,000 units, enough for 70% of the 600,000 electric vehicles Ford plans to sell in Europe each year. There are two reasons why Halewood was chosen. Firstly, it has enough space to expand production, and secondly, it is very close to the Liverpool City Region Freeport. This is a special economic zone created following Brexit, which offers special economic regulations, as well as customs and tax incentives.
Using existing technology differently
Ford and Liebherr have been working together for 30 years, implementing numerous projects including retooling projects. However, this was the first one to involve moving existing equipment to another location. “We took equipment from lines that were no longer producing internal combustion engines from Dagenham to Halewood, then upgraded and modernized them,” reports project manager Steve Treweek, Senior Process Engineer at Ford Motor Company. “This saved us a lot of money – buying the lines brand new would have cost an additional 30 to 40 million euros.“ The converted equipment was built in 2010 and is thus still relatively new. Retooling it is cost-effective and the result is production lines that look – and run – like new. The plant is still in the ramp-up phase and production is scheduled to start in October 2024.
Gantry technology and e-mobility
“If the project shows one thing, it‘s that gantry technology is alive and well,” says Roman Buhmann, Key Account Manager and Liebherr‘s project manager for Halewood. “Anyone who thinks that gantry systems will die out along with combustion engines has got it wrong. Gantry technology is still needed – for producing gearboxes for electric drives just as much as for traditional engine blocks.”
Liebherr gantry technology for the entire material flow
The converted plant uses four lines to produce electric motor housings, gearboxes and covers and for assembling the transmission. Liebherr technology plays a leading role everywhere, including gantry robots for tooling the CNC machines (LP 200), gripper systems, connecting belts between gantry lines and maintenance areas, a tower storage system, state-of-the-art part tracking, and SPC stations for removing workpieces for quality assurance.
“Liebherr technology handles the entire material flow of transport, temporary storage, control and tracking – including process reliability, material flow optimization to guarantee cycle times on the production lines, as well as removal and data evaluation,” says Uwe Radigk, Powertrain Manufacturing Sales Manager at Liebherr-Verzahntechnik GmbH. “Only the control technology is completely new; 90% of the hardware is re-used and upgraded. The energy supply chains have also been retrofitted, and the safety systems have been brought up to date to ensure the maximum possible occupational safety.”
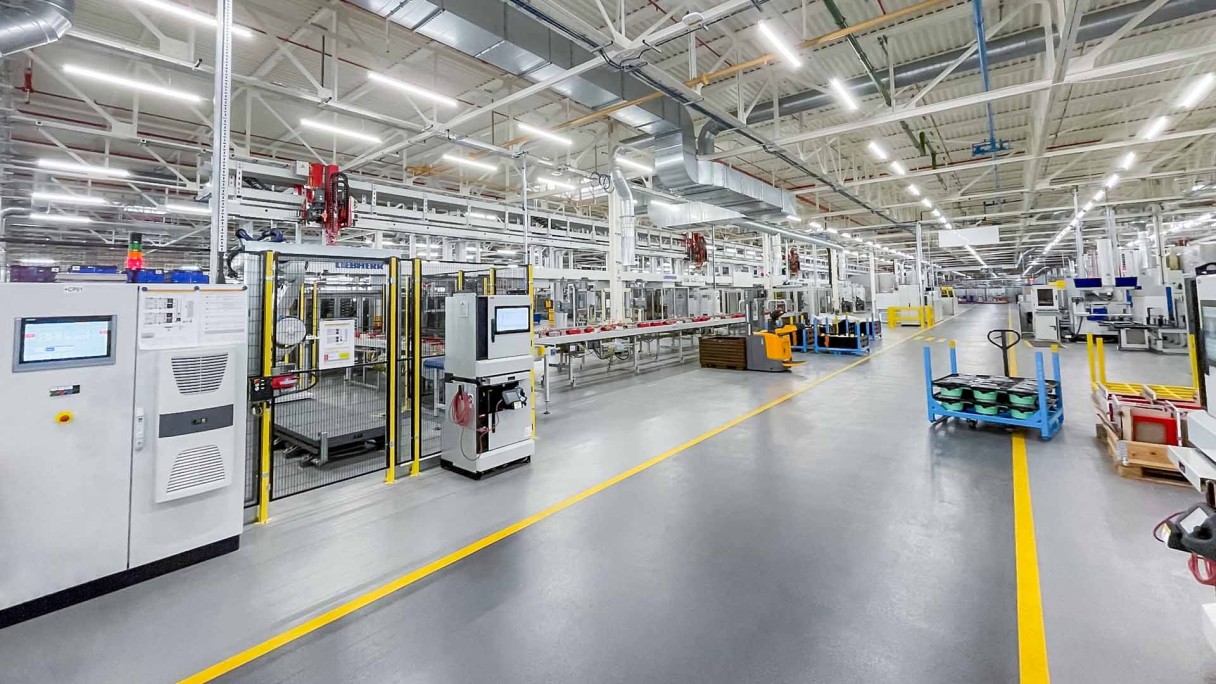
The friction roller outfeed conveyor with the interface for unloading the good parts, behind it the gantry system with the telescopic axes
Productivity, quality and flexibility
The new plant offers a significant increase in productivity: availability will increase from 80% to 87.5% in the first step and up to 90% in the future. In terms of the gantry technology alone, it is no less than 98%. “The advantages of Liebherr gantry technology are clearly productivity, quality and flexibility in equipment and engineering – and also tidiness,“ says Steve Treweek. “Looking around the factory, you can‘t tell that it‘s used equipment. Everything looks brand new.“
Challenges during the conversion
Seamless collaboration
Ford Project Manager Steve Treweek knew from the start that he would carry out this project with Liebherr. The decisive factors for him were not just the quality of the equipment, but also the know-how, comprehensive expertise in Ford projects and the reliability of the Liebherr engineering team. “Over the last 15 years, I have had all my gantry technology supplied by Liebherr,” he says. “I‘m very experienced and know exactly what I need – but even with less experienced Ford project managers, the Liebherr team would have mastered the task. I know what the teams, assembly crews and project managers can do. When it comes to the whole system, there‘s no one comparable.”
The excellent collaboration between the Ford and Liebherr teams was crucial in ensuring that the Halewood project ran smoothly despite all the challenges. “This kind of thing is only possible with Liebherr,” Steve Treweek emphasizes. “We have a deep mutual understanding and both teams complement each other perfectly. I would always argue for Liebherr as a supplier. As a Ford project manager, I need quality, reliable project partners and a good team on my side – and this is exactly what they give me. It‘s a pleasure to work with Liebherr.”
Ford Motor Company
Sector:
Automotive
Company headquarters:
Dearborn, MI (USA)
Employees:
approx. 186,000 employees
Founded:
1903
Website:
ford.com