Maximum flexibility
- Electronic helical guide
- NC steady column for long shafts
- Additional operations: integrated chamfering during the machining process (FlexChamfer) and pointing
Maximum productivity
- Cluster gears with a single clamping fixture
- Reduced setup times
- Integrated ringloader automation
Improved ergonomics
- Easy and ergonomic operation
- Fold-out steps
- Optimum accessibility for maintenance
Machine design
Liebherr shaping machines set the benchmark for performance. Their production efficiency goes hand in hand with their unparalleled quality.
The basis for their durability and precision is their rigid and heat-proof design, combined with backlash free drives and flat guides. Chamfering during the machining process is made possible thanks to innovative technologies like FlexChamfer.
An internal ringloader provides optional automation for workpieces up to 100 kg. The Liebherr operating concept includes LHStation & LHMobile as well as LHGearTec software, meaning user friendly control is guaranteed. Chip removal has also been improved thanks to an optimized and redesigned machine bed, further increasing the overall performance of the machines.
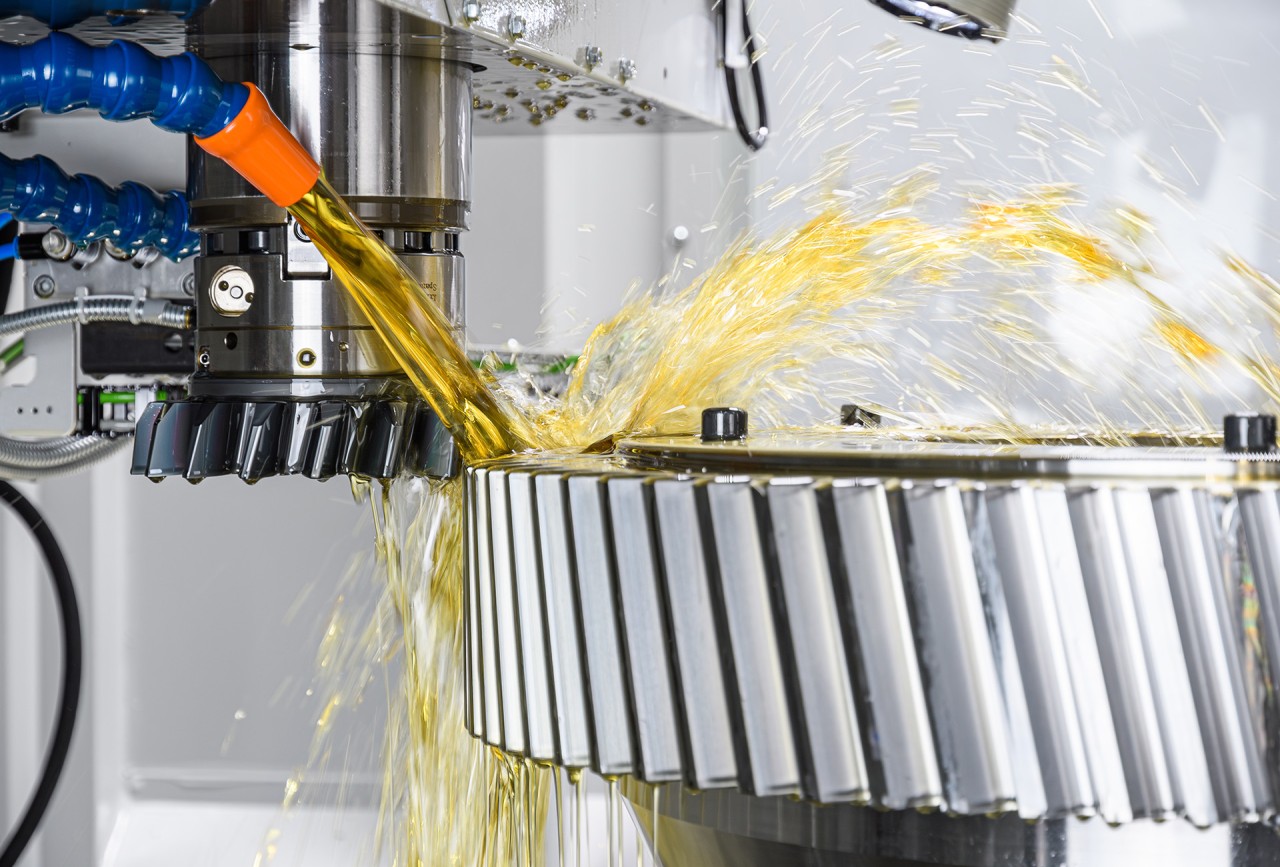
Your advantages when gear shaping with Liebherr
- Versatile machining of external and internal gears for a wide range of applications
- Easy handling of components with interfering contours and limited overrun
- Flexibility – from small batch sizes and individual parts to mass production
- Production of components for the highest power densities
- Machining of complex geometries for the production of high-precision components
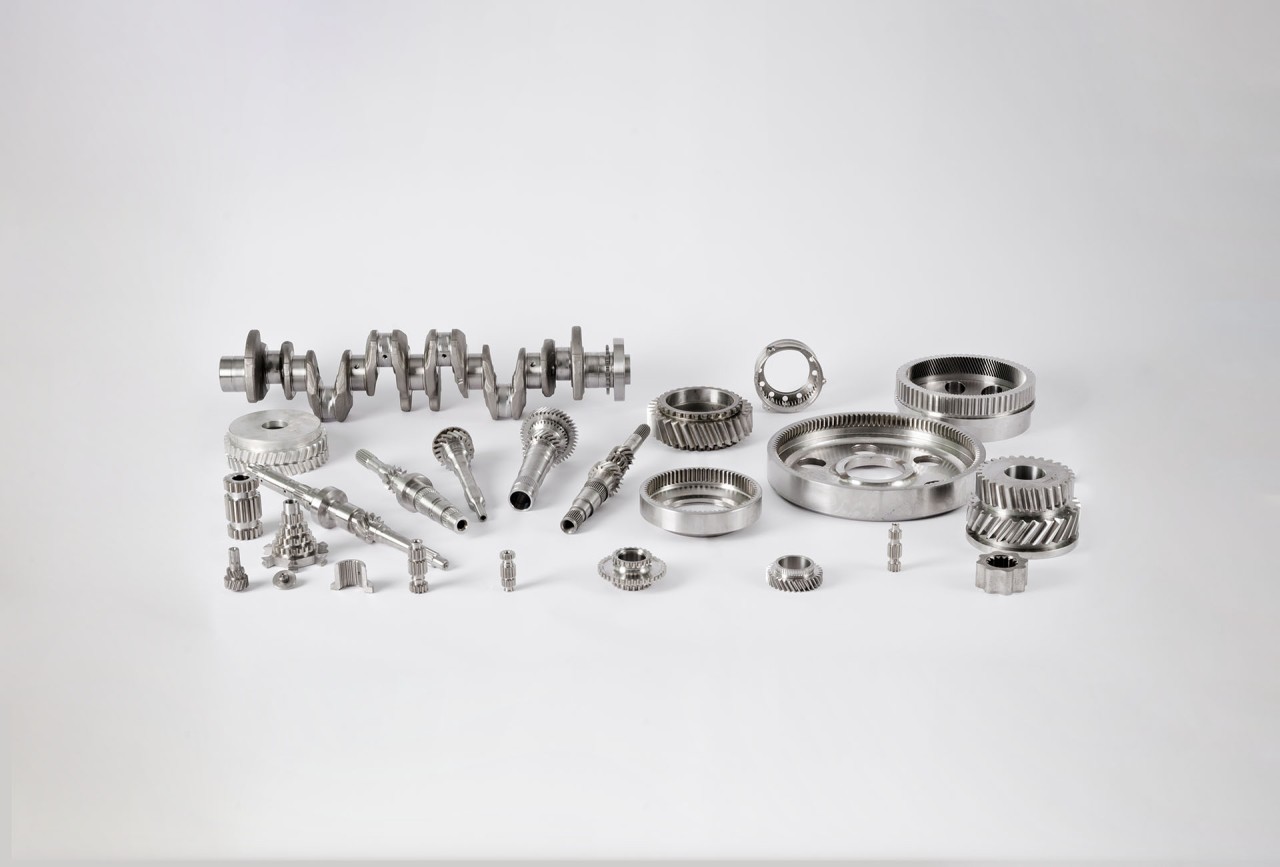
The many applications of the Liebherr LS 300-500 gear shaping machines
The LS 300-500 Series gear shaping machines have many use cases and are ideal for demanding applications such as:
- Internal gears
- Herringbone gears
- Double-helical gears
- Symmetrical and asymmetrical leads
- Segment gears
- Machining of gears with segment tools
- Slotting and conical shaping
- Shifter stop machining of gears
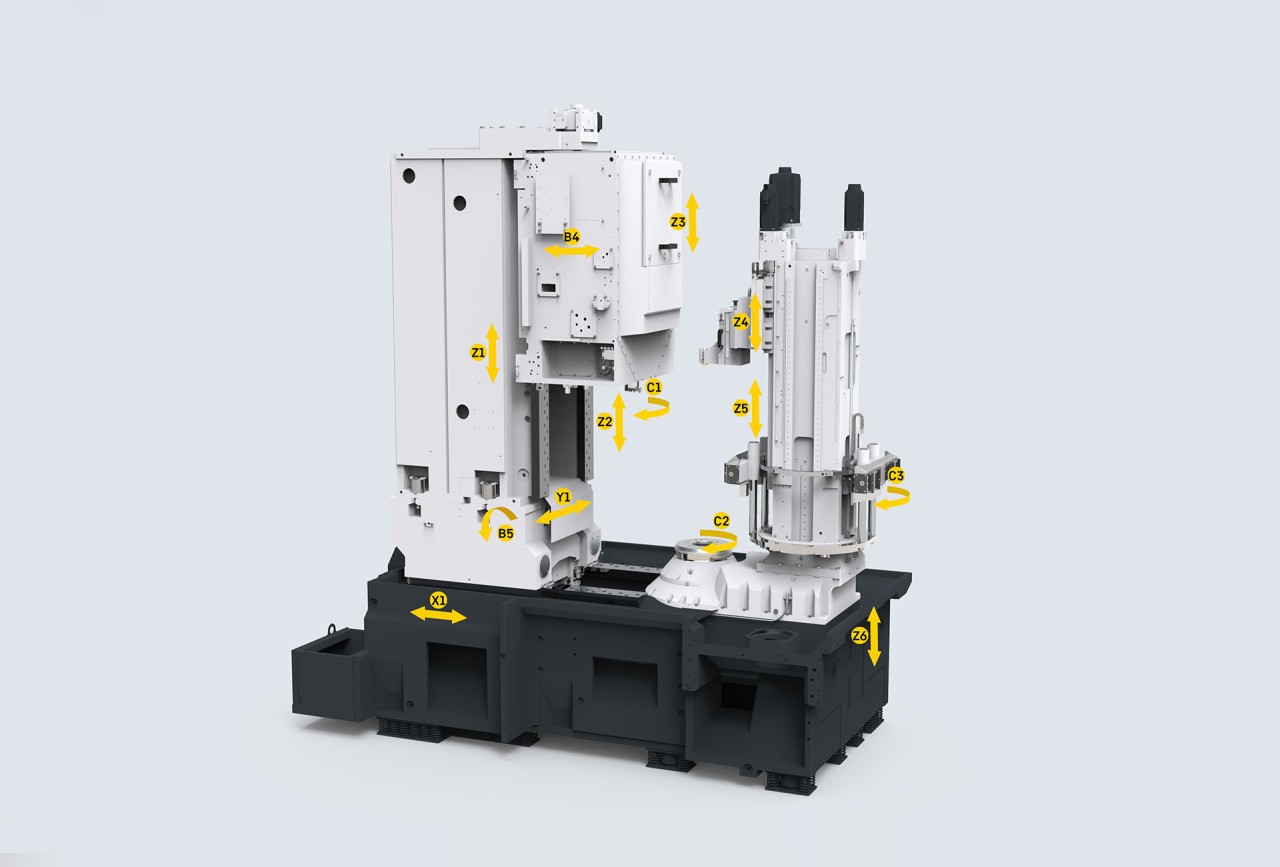
Machine design
- Automatic swivel column for conical shaping and, for crank shafts, application of shaping with crossed axes (B5)
- Automatic lateral column offset value to avoid return stroke collisions – especially with internal gears (Y1)
- Automatic adjustment of the stroke position and stroke length for better flexibility and easy setup (Z1, Z2)
- Fast stroke speed for maximum productivity (Z3)
Effortless precision
Both for the shaping machines LS 300 E/500 E and the 700 EM, two shaping heads are available. What really distinguishes both models are their electronic helical guides and cam systems:
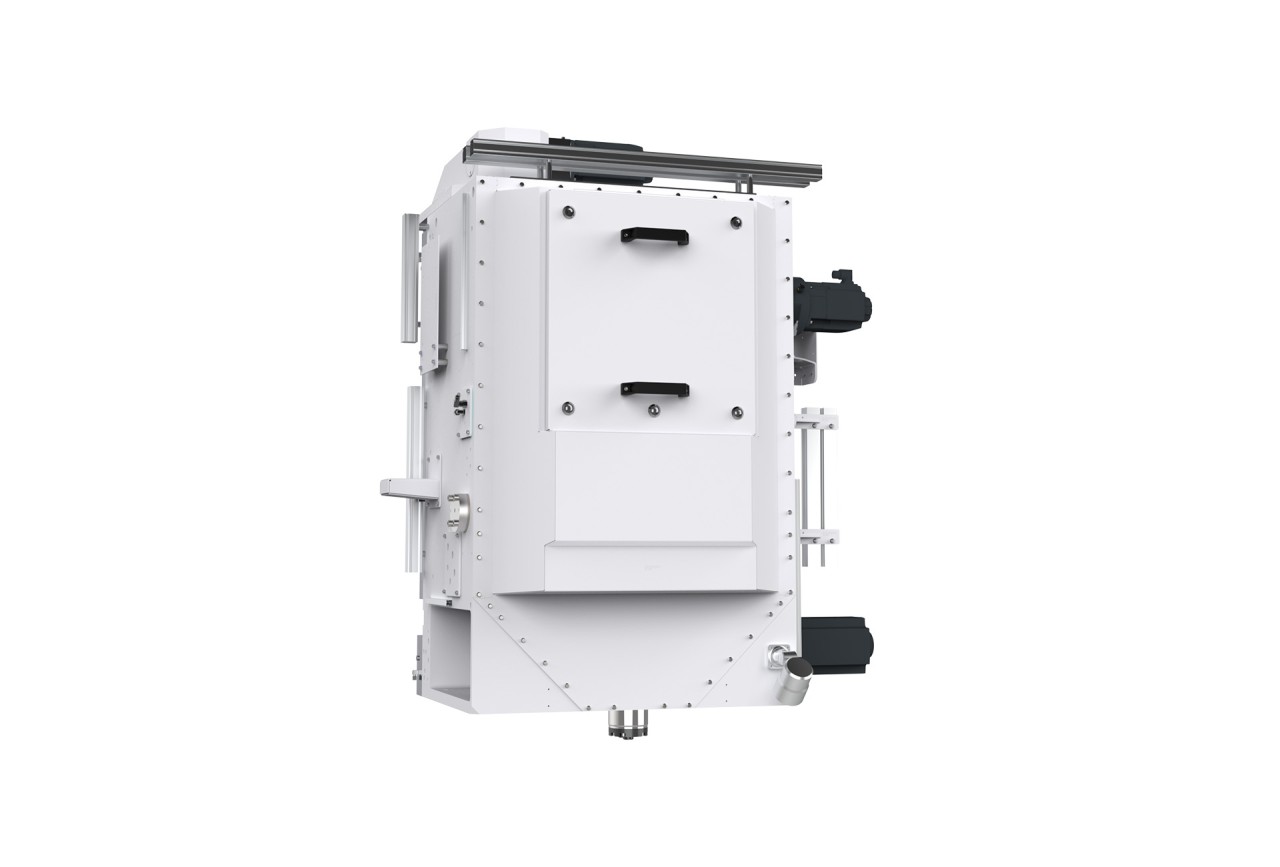
Effortless precision: shaping head SH 120 E
- Multi-track cam systems with automatic switchover and special cams for individual applications
- Additional, programmable flank modifications made possible thanks to the electronic helical guide
- Easy programming of helix angles up to 50°, including correction options
- Shaping several gears with differing helix angles
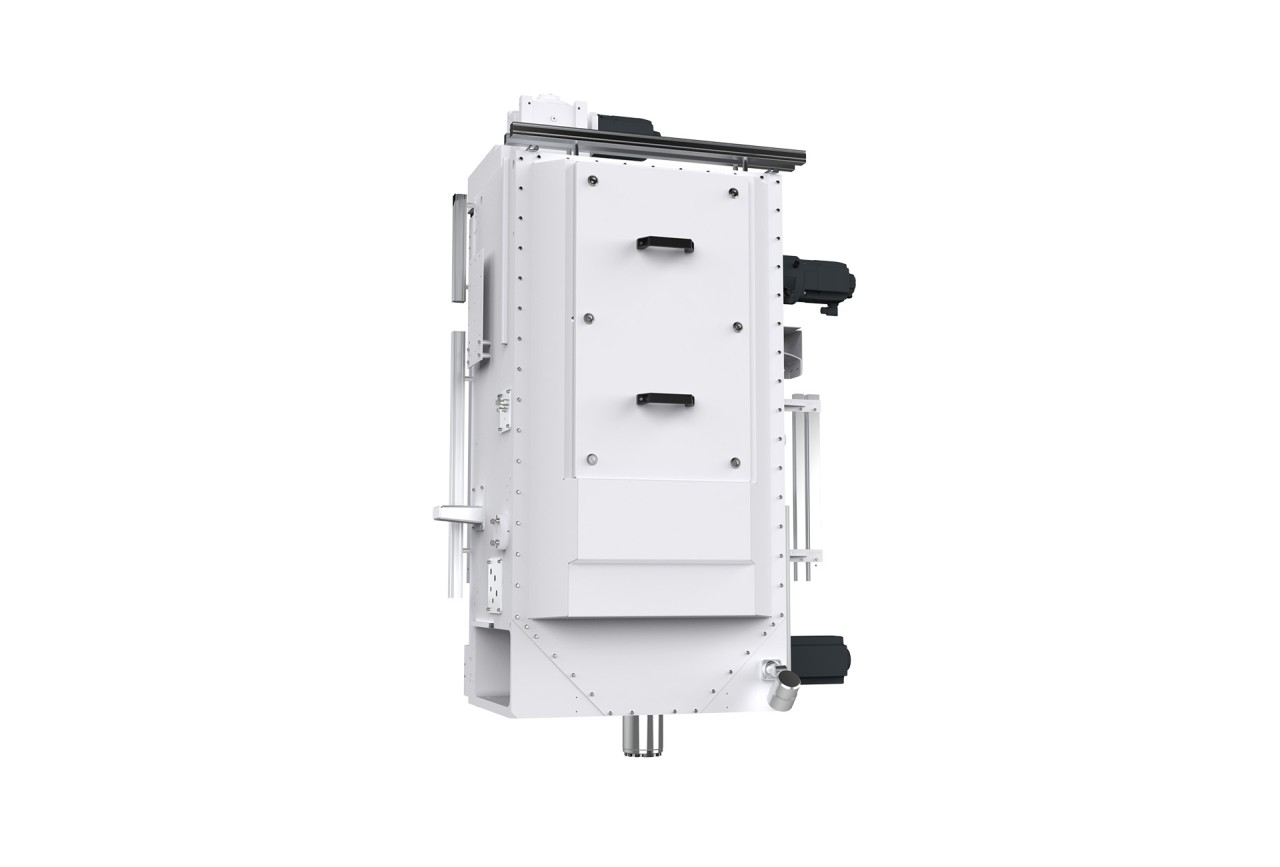
Effortless precision: shaping head SH 240 E
The high-performance SH 240 E shaping head offers the same advantages as the SH 120 E. For broad face widths in particular, the SH 240 E with its larger 240 mm stroke offers distinct advantages. Compared to the 1200 DS/min of the SH 120 E, the SH 240 E reaches a stroke speed of 1000 DS/min.
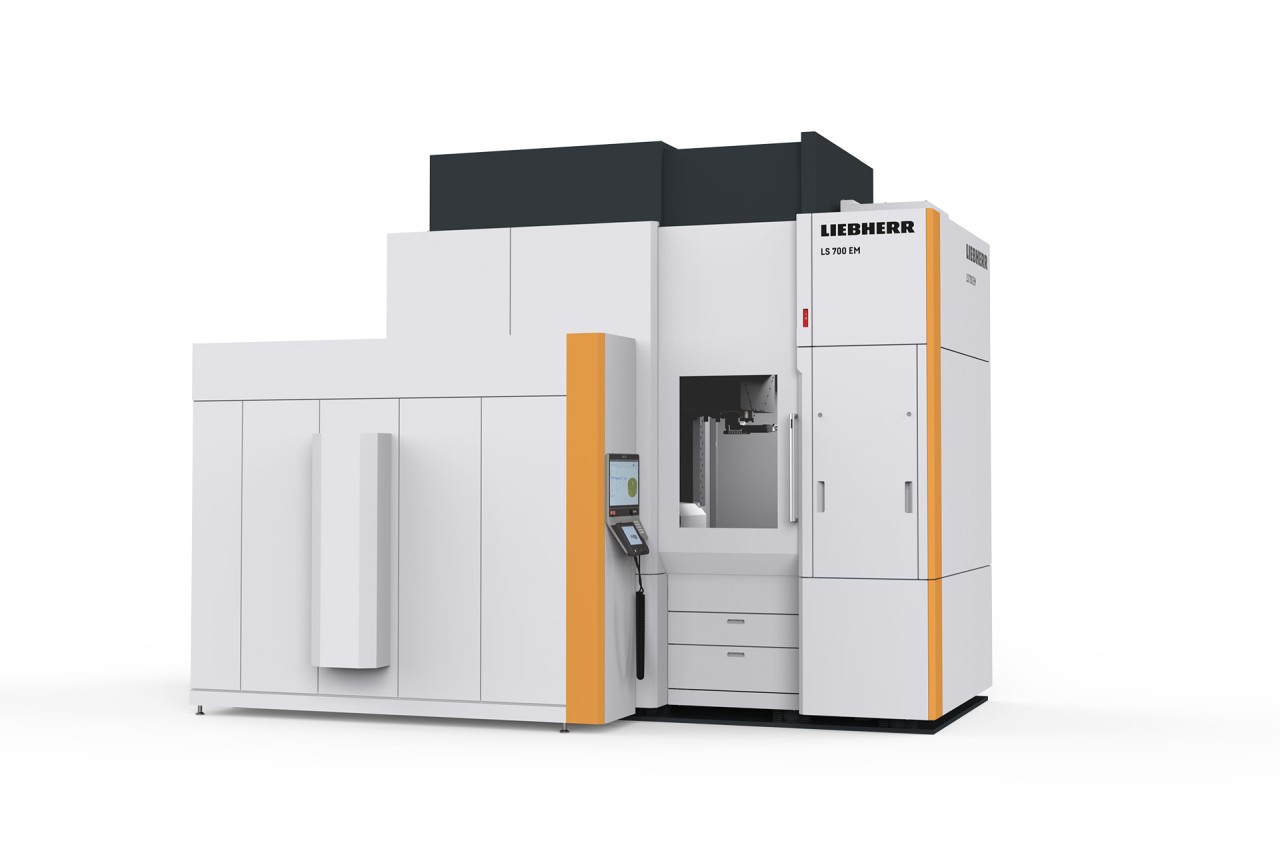
Maximum versatility and efficiency: manually loaded gear shaping machine for parts with a diameter up to 700 mm
Liebherr presents an outstanding solution for small batch sizes and excellent versatility with the manually loaded LS 700 EM gear shaping machine. Specially designed for parts with a diameter up to 700 mm, this machine makes efficient machining of a wide range of workpieces possible. Manual loading is significantly easier thanks to the NC-controlled swivelable tailstock, while the L-doors allow for perfect accessibility – and even make it possible to load from above using a crane. With Liebherr, discover a flexible and high-performance solution for your production needs.
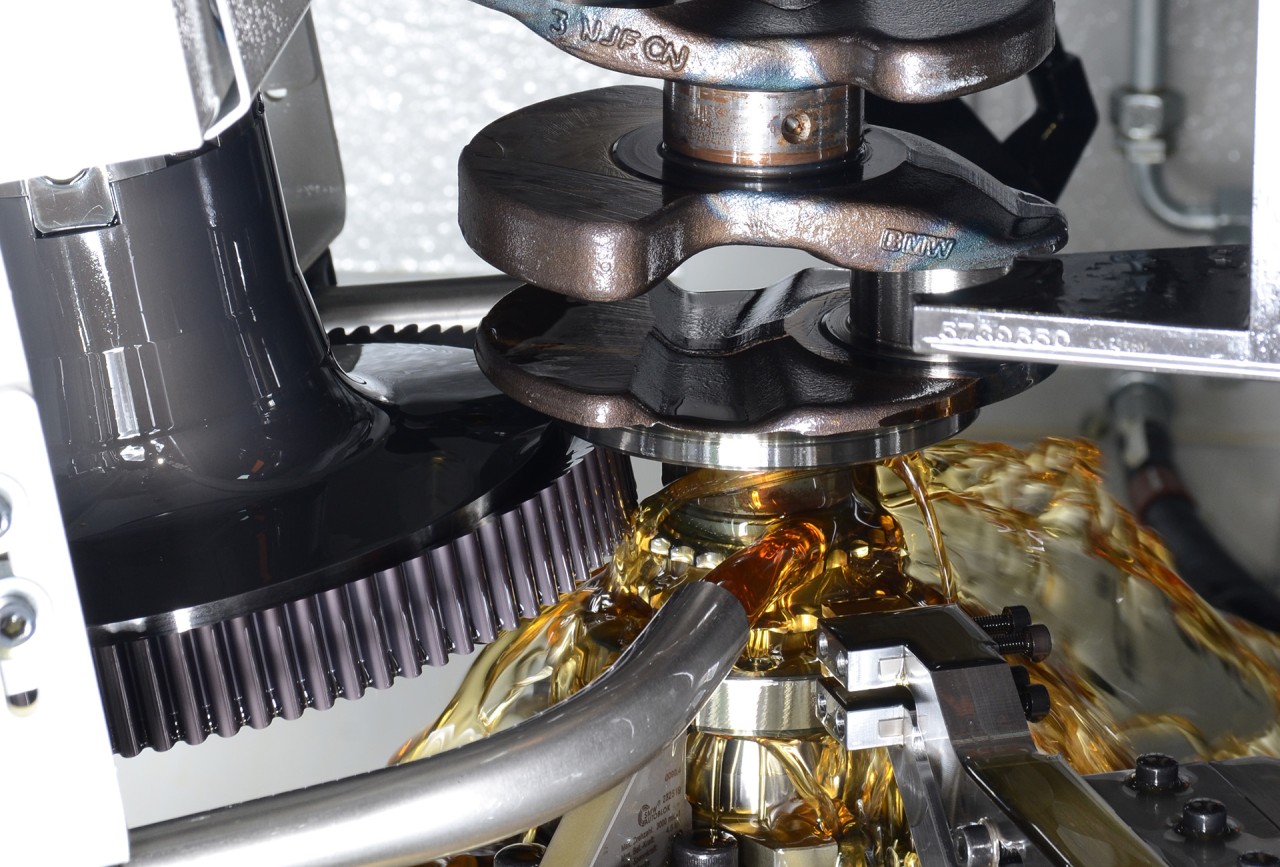
Focus on technological highlights
Multiple technological highlights underscore the excellent performance of the Liebherr gear shaping machines in the LS 300-500 Series.
An outstanding feature is the shaping with crossed axes method, specially developed by Liebherr. It is used in the production of sprockets on crank shafts.
By using cylindrical shaping cutters and special back-off cams, this technology makes it possible to significantly reduce the tooling cost per workpiece.
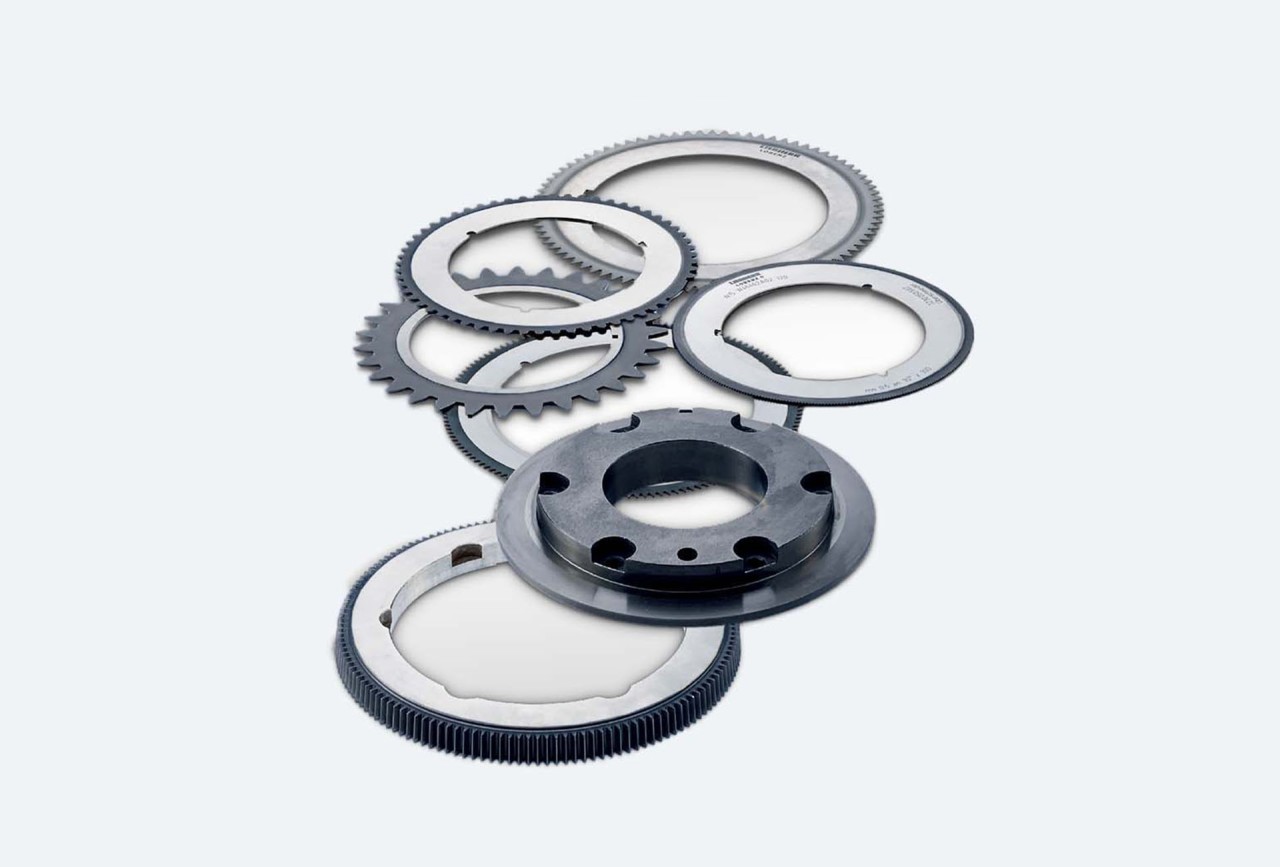
Efficient and cost-saving shaping with wafer tools
Liebherr’s innovative wafer tools are the perfect complement for shaping machines and enable significant reductions in production costs. Clamping thin wafer discs in a special frame and then installing them in the machine provides countless advantages:
- No machine adjustment necessary after switching out the wafers within a workpiece lot
- Economic series production
- Optimal process reliability
- Easy machine adjustments and reduced setup times
Maximum user-friendliness

The optimized LHStation & LHMobile control panel
With the control panel, Liebherr intelligently divides programming and machine operation between two of the system components: “LH Station,” the large, fixed monitoring unit for data input and process monitoring, and “LH Mobile,” the standardized, mobile handheld unit with context-sensitive user guidance during setup. Both devices are equipped with both a multi-touch interface and tactile elements for optimal operational speed and operational safety.
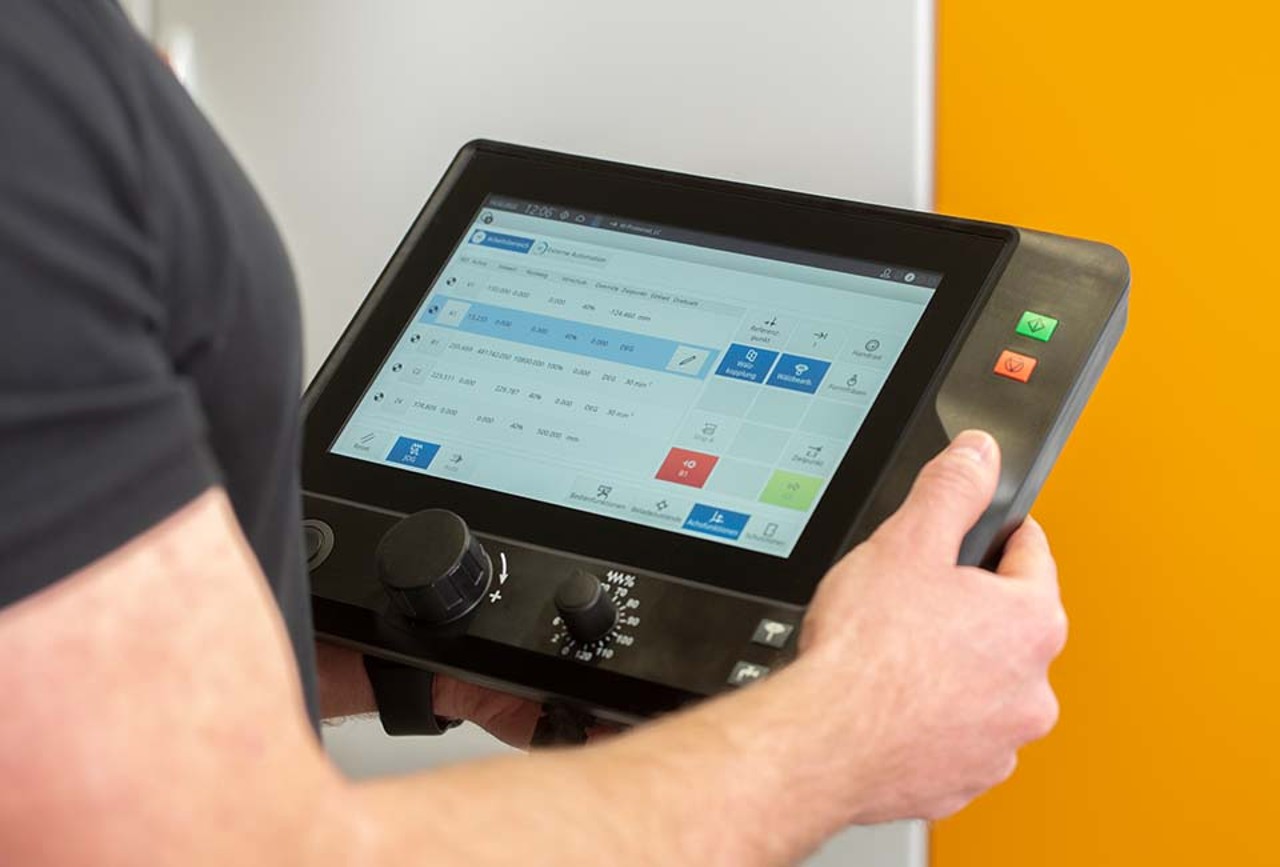
LHMobile – mobile handheld terminal
- Standard 10 inch multi-touch
- Context-sensitive views such as PLC/NC buttons and program statuses
- Wired signal transmission for optimal safety
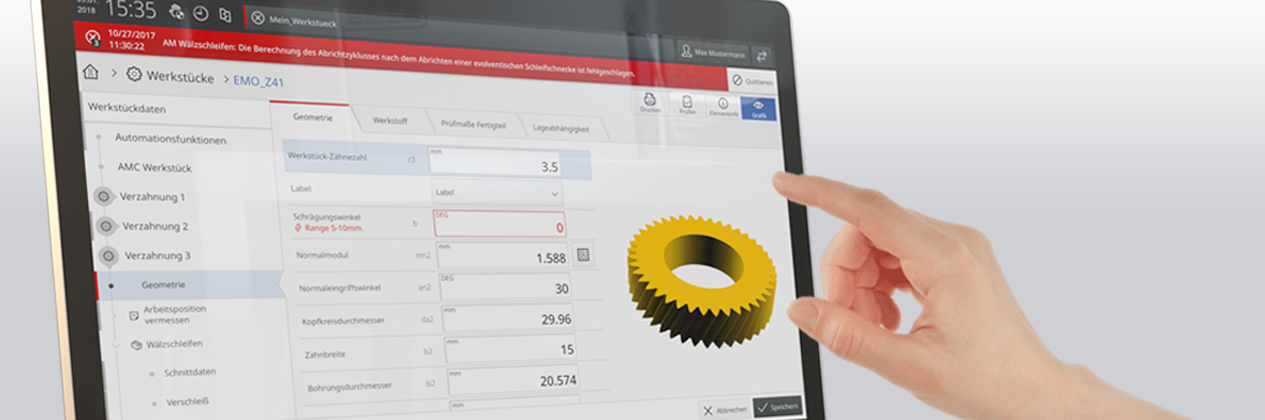
The programming system from Liebherr: 25% faster setup time
With the LHGearTec Software, the user is constantly guided by the system through anything from workpiece and tool data and workpiece correction to process monitoring. This user guidance was developed through intense collaboration between users and designers.
Automation & features
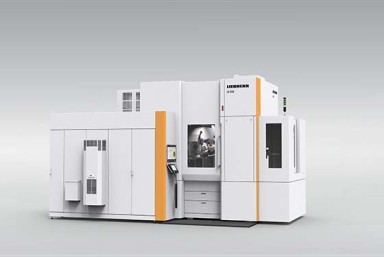
Manual or robot loading
with the NC lifting station
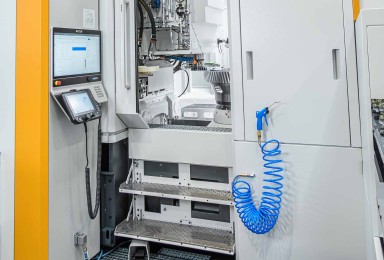
Accessibility and ergonomics
The workplace in front of the machine was designed to provide optimal accessibility and lots of space. The fold-out steps also contribute to improvements in ergonomic accessibility and a comfortable work environment.
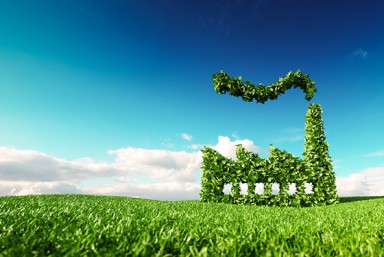
Energy and resource efficiency
Liebherr has conducted comprehensive analyses of its gear cutting machines. Liebherr understands that every 100 watts of savings protect the environment and are worth striving for.
- Regenerative drive technology
- Use of efficient control cabinet cooling
- Lighting with LED technology
- Coolant supply and
- Regeneration with speed-controlled pumps
Technical data
Variants | LS 300 E | LS 500 E | LS 500 E DC | LS 700 EM |
---|