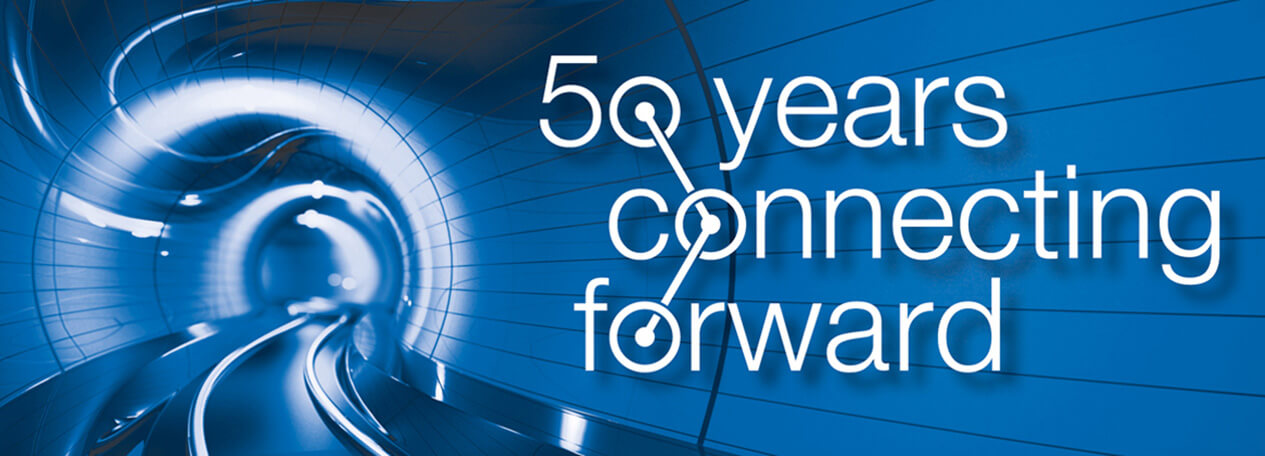
Magazine 2019
Magazine 2019
Most read
01
Half a century of Liebherr-Verzahntechnik GmbH means 50 years of commitment to the machinery and plant engineering industry. Gear technology originated in the technology of the revolving tower crane. Hans Liebherr wanted to buy a gear hobbing machine for gear manufacturing, but could not find what he wanted – so he simply built it himself. It’s a typical Liebherr story, since many sectors in the company group have emerged in this or in a similar way. Taking things into one’s own hands: an attitude that can still be found at Liebherr today.
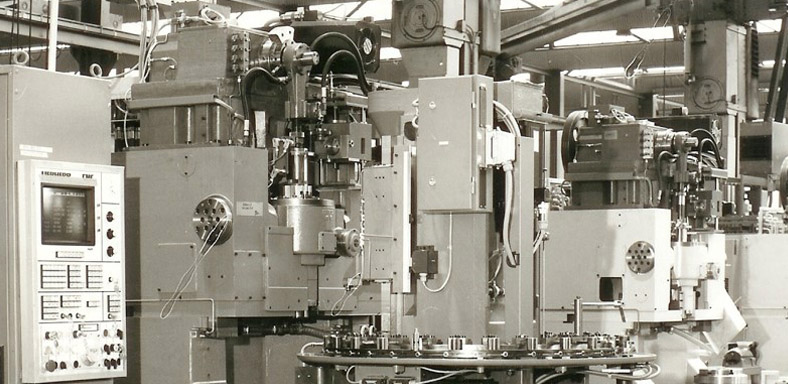
02
Bauer Gear Motor operates two new LC 180 gear hobbing machines at its facility in Slovakia, producing gearing for all facilities. These machines are characterised by their operational versatility, given that they are used to produce around 180 different components in a very wide range of different sizes.
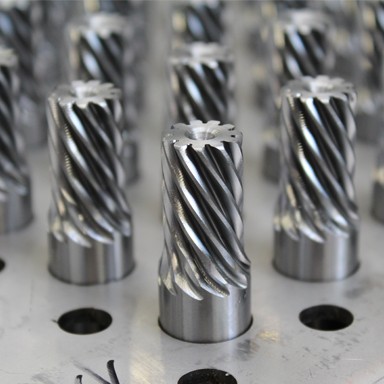
03
“The fire pump is the heart of every fire truck”, explains Michael Schöftner, Head of Mechanical Production at Rosenbauer International AG, the global leader for fire service equipment. The equipment has to withstand enormous loads in cases of operation. Rosenbauer relies on an automation solution for pump manufacturing from Liebherr. The rotary loading system RLS 800 from the Kempten-based automation experts has been deployed in Leonding near Linz for around two years now.
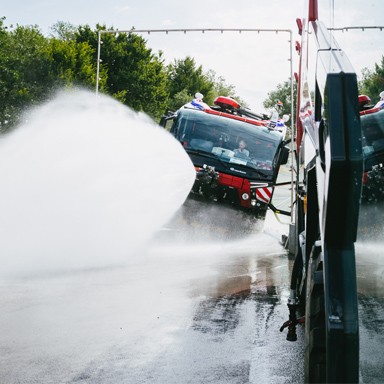
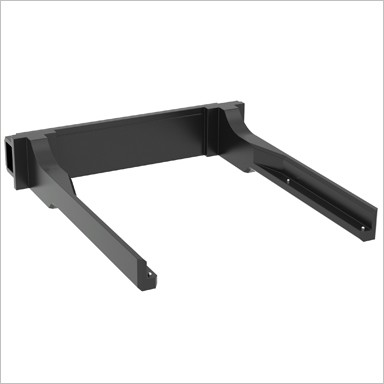
PHS Allround has become a bestseller of Liebherr Automation Systems. The modular pallet handling system appeals to a wide range of different areas of industry with a main selling point being its scalability. It has now been made even more flexible with the new double loader.
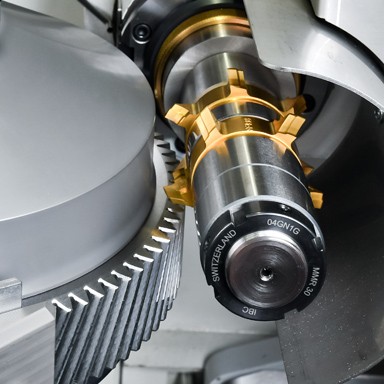
After an upgrade, the universal LC 280 DC gear hobbing machine shines with improved operating comfort and technical refinements.
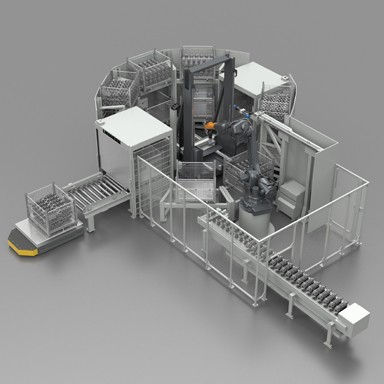
Rotary loading systems and bin picking, a robot system also referred to as pick and place, are a permanent feature in the Liebherr automation division. Together, they form a good team in automating inputs and outputs from production lines.
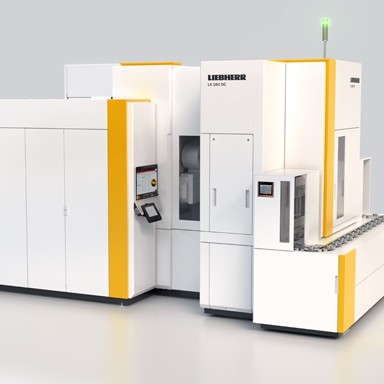
The constantly rising demands from the markets, such as higher accuracy, more effective processes and increased flexibility, require sophisticated machine concepts. For this reason, the new gear skiving machine generation has been equipped among other things with a tool changing system integrated in the machine, multi-machining functions, an integrated measurement device for tools and the option of chamfering during the machining process.
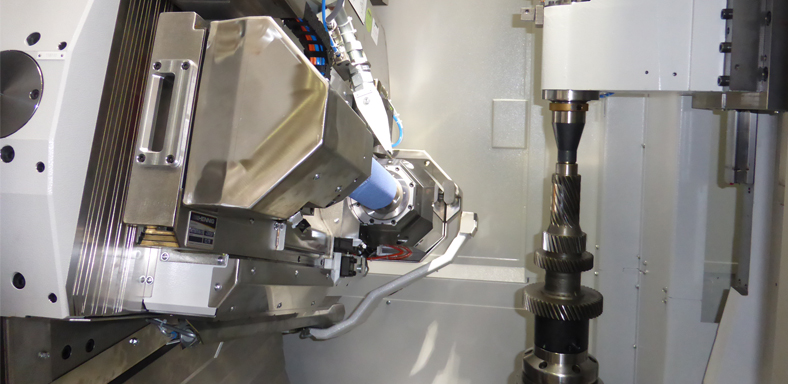
Based on the proven LGG 280 generating grinding machine, Liebherr is presenting the larger LGG 400 M model at IMTS in Chicago.
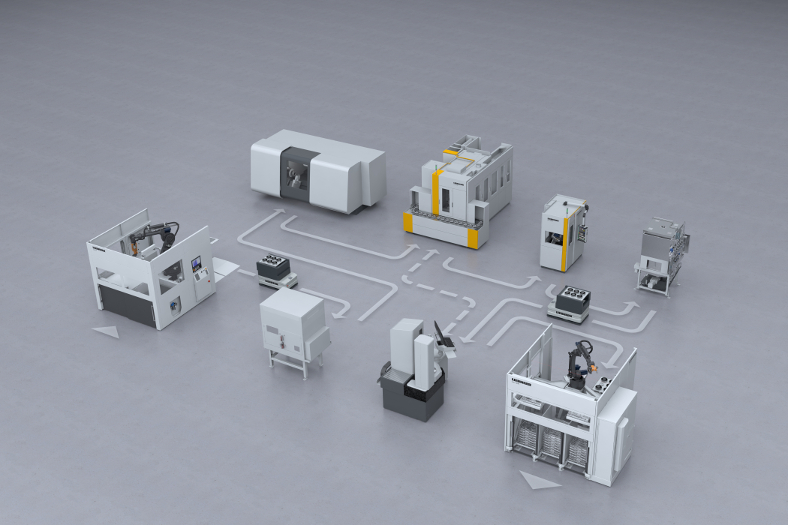
While we still have some way to go to achieve autonomous driving on the road, factories are miles ahead: AGVs (automatic guided vehicles) are already being used in the area of production.
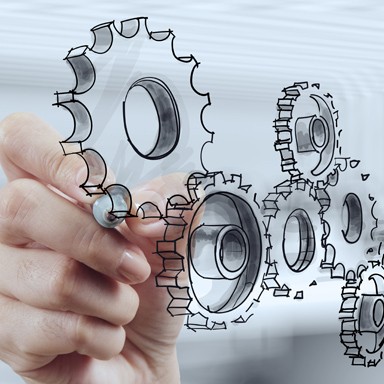
The first LK 500 skiving machine is in use at the Italian gear specialists SIAP. An innovative investment that will increase both productivity and quality.
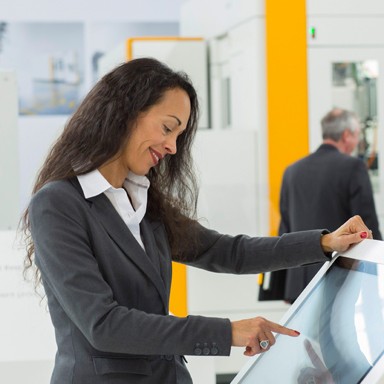
Lisa Bozzi has been with Liebherr in Saline, Michigan, since 2017. She is an office manager and event coordinator for the Liebherr Gear Technology and Automation Systems division, but also supports the HR team in acquiring new talent for Gear Technology and Automation Systems and Aerospace.