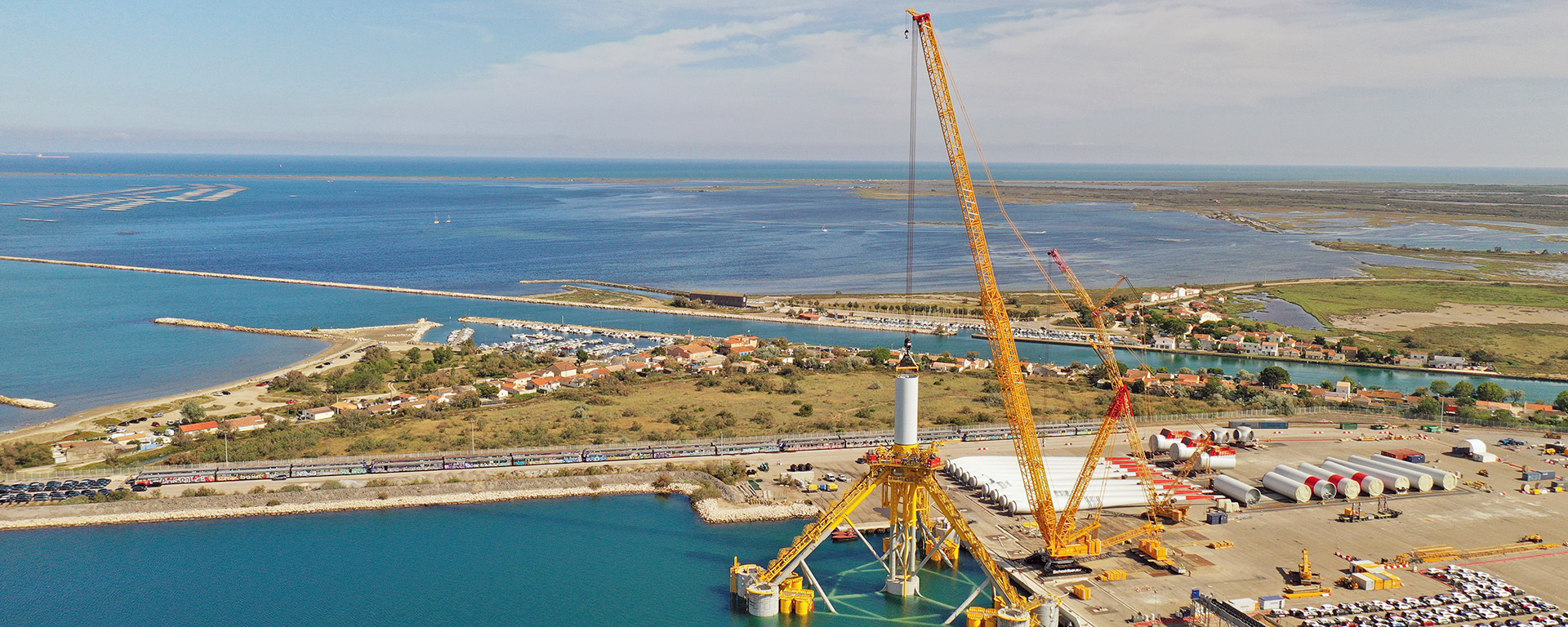
Wind power is learning to swim
Just off the coast of Marseille, a new chapter is being written in the annals of the energy revolution. Provence Grand Large is the very first floating offshore wind farm to be built in France. Standing sentinel over the docks of Port-Saint-Louis-du-Rhône for this history-making moment of engineering innovation, which saw three 8.4 MW wind turbines installed onto floating platforms, was one of the largest crawler cranes, an LR 11350, from Liebherr.
‘The scale of it certainly commands respect!’ So says Werner Schmidbauer, who has seen his fair share of cranes in his lifetime – including some really big ones. But in June when the owner and Managing Director of the Schmidbauer Group travelled to the Mediterranean coast and saw the vast, shimmering yellow crane with its 150-metre boom stretching skyward, even this experienced crane rental expert of many years was in awe.
And that’s before he was even anywhere near Port-Saint-Louis-du-Rhône! The industrial port lies just shy of 50 kilometres north-west of Marseille, in the Provence-Alpes-Côte d’Azur region. In the spring and summer of 2023, the port became the epicentre of a whole new chapter in the revolution of energy. It is where Siemens Gamesa Renewable Energy joined forces with energy providers EDF Renouvables and Enbridge to establish the first floating wind farm in the Mediterranean Sea. This saw three 8.4 MW wind turbines positioned on special floating foundations. They were then towed by tugboats out to the high seas some 17 kilometres from the shores of Port-Saint-Louis-du-Rhône, where they were fixed to the sea bed using anchor ropes for a relatively low impact. The operators, together with the scientists and ecologists involved in the project, are anticipating that this approach will deliver important findings for the future of offshore wind energy generation that is even more efficient while also being kind to marine life and seabirds.
Cranes for the energy revolution
Werner Schmidbauer is fascinated by the complex background to the project and the science and research incorporated into it: ‘We see ourselves as partners and co-creators of the energy transition.We are contributing to the creation of a high-performance infrastructure for renewable energies by providing the right cranes and construction machines, as well as our decades of expertise. Most of these cranes and machines come from Liebherr.’ On Gloria quay in Port-Saint-Louis-du-Rhône, an LR 11350 stretches its 168-metre long lattice boom skyward. In order to lift extremely heavy loads, the crane has been fitted with a PowerBoom for this operation – its dual design allows the lattice boom to extend to a length of 80 metres in parallel in the lower section. This increases the crane’s load capacity by almost 50 percent. The LR 11350 has a maximum load bearing capacity of 1,350 tonnes and was primarily designed for loading heavy cargo in ports or for industrial applications.
You don’t find a crane of this scale just lying around in a yard. It was made specially for us and delivered straight to the building site. A precision landing!
The project was actually supposed to start in late 2021, recalls Minka St. James, Head of Business Development at Schmidbauer. ‘But then we had the COVID-19 lockdowns firstly, and the subsequent supply bottlenecks, which caused major delays to the erection of the floating foundations in particular. It was a real test of patience for all those involved.’
‘Getting the special crane operational for this demanding wind turbine construction was a huge undertaking, and one which we shared with Liebherr,’ explains Werner Schmidbauer. ‘You don’t find a crane of this scale just lying around in a yard. It was made specially for us and delivered straight to the building site. A precision landing!’ Dismantled into individual parts, the LR 11350 was transported directly to France from the Liebherr plant in Ehingen, Germany, on more than 90 articulated lorries. Not to mention another 45 HGVs carrying additional equipment. Awaiting the LR 11350’s arrival in the port, which had itself been stabilised with specialist pads and extra steel plates, were 15 experts from Schmidbauer’s large cranes team. Accompanied by up to four Liebherr engineers, it took the team one and a half months to assemble the crawler crane for the first time.
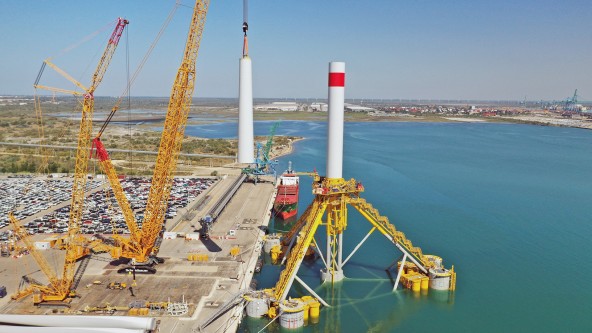
© Iann Hanning
A building site with no blueprint
‘A first-time build is always a bit of an adventure, shall we say. On Friday, 6 June, the safety inspection and the final load test were carried out by the French authorities. On the Monday after that, it was already straight to work,’ reports Matthias Wirtz, Project Manager for Schmidbauer. The 33-year old construction engineer has been with the crane company for two and a half years and specialises in large-scale projects. ‘This job was exceptional in many respects, and that’s what made it so appealing. After all, there was no blueprint for how to install wind turbines on floating foundations. However, we were able to calculate a lot of the process and simulate it digitally. But it was really exciting to see it take shape in reality, for instance when it came to one-sided loading and unloading on the dynamic foundation during rotor assembly.’
The LR 11350 had reinforcements, in the shape of a 400-tonne crawler crane and a mobile crane for smaller supply jobs. ‘Working in tandem, they were very effective in stabilising the lifts of up to 130 tonnes of hard-steel segments of wind turbine tower,’ explains Wirtz. ‘These giants had to work in perfect harmony, especially when the nacelle had to be lifted to a height of around 120 metres. This is the very heart of the wind turbine and registers some 260 tonnes on the scales. When a suspended load of this scale spans a crane-to-hook distance of almost 50 metres on the PowerBoom, every single movement of the crane has to be made with complete precision.’
It’s good to talk – in fact it’s crucial
This kind of precision work with super-heavy XXL components is all part of the day job for Fabian Ueck. The 48-year-old is an experienced crane operator, whose journey with Schmidbauer’s largest cranes has already taken him to a vast array of major construction sites the world over: ‘In truth, building a wind turbine always follows the same general pattern. But this turbine here in France is something very special for all of us,’ he confirms. He explains that conveying hundreds of tonnes of weight onto a floating, and therefore moving, platform by crane is a physical feat. Everything has to be just right. Matthias Wirtz knows that ‘to work efficiently, and above all, in total safety, complete professionalism and teamwork is needed.’ Fabian Ueck can testify to this: ‘When dealing with large loads and large machines, it’s paramount that everyone talks to each other, openly and honestly, so they are best prepared for anything that might happen.’ He explains how everyone soon grows together as a team on the construction site ‒ across all company and language barriers.
Sitting in his cab some six and a half metres off the ground, Fabian Ueck, assisted by a range of cameras and the high-performance crane control system, has an excellent view of the entire site. This is particularly important when the crawler crane is carrying a part around. That’s because Ueck has to keep an eye not only on the load on his hook, but also the suspended ballast, which keeps the crane balanced while lifting. With the lift complete, Ueck places the 500-tonne suspended ballast down on its own mobile platform, a 48-axle SPMT (self-propelled modular transporter). ‘Every little thing is dependent on everything else,’ he says contentedly.
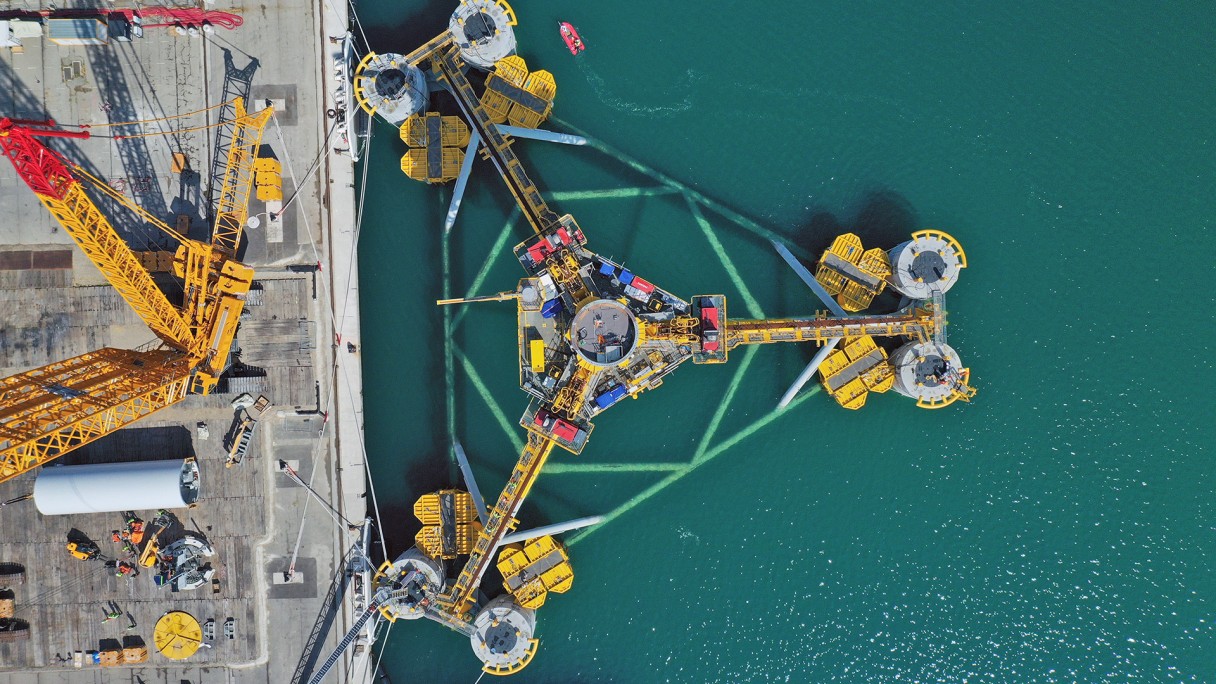
© Iann Hanning
Sheltering from the storm
Much to the disappointment of the project managers from Siemens Gamesa Renewable Energy, it was often necessary to put the crane on Gloria quay completely into idle mode for several hours or even days at a time. That’s because the mistral blows through here every few weeks. The famous Rhône valley wind often sweeps out to the Mediterranean at speeds well in excess of 100 kilometres per hour. ‘When it’s really howling through, just pointing the crane into the wind is not enough. Instead, we have to completely dismantle the boom and the suspended ballast and wait until the storm blows over,’ explains Ueck. However, making the crane safe costs a lot of time. It takes four hours to dismantle and another four hours to reassemble. ‘But, that’s mother nature for you, we can’t do much about it. Once the wind turbine is up, everyone is excited by the prospect of a strong breeze. Just not before!’
Consequently, checking the weather forecast is one of the must-do tasks for the team on the construction site on these high summer days. The tight schedule doesn’t leave the construction team much time to soak up the sun or the holiday atmosphere of the Cote d’Azur. Nevertheless, Fabian Ueck’s crane crew are staying in mobile homes on a nearby campsite that leads straight to the beach. ‘There is plenty to look forward to when the working day is done,’ explains Ueck happily. This is much needed too, especially since what was supposed to be a six-week job turned into three months in total. ‘Of course, it’s lovely to work on a building site in a place where people come to spend their holidays. The weekend day trips to Marseille, to the lagoon in Étang de Berre or to see the flocks of flamingos in the Camargue were really special for us all.’
Floating offshore wind farms take green energy generation to a whole new level. This has great implications for the future.
The construction site as a visitor attraction
Provence Grand Large gave Fabian Ueck something of a new experience in that his work attracted the attention of sightseers. ‘We had busload upon busload of schoolchildren, students, politicians, scientists and media types coming by to find out about the project and to get a tour of the construction site,’ he explains. ‘The whole world is watching what we’re doing here,’ adds Minka St. James. ‘Floating offshore wind farms take green energy generation to a whole new level. This has great implications for the future. And everyone involved in the project really senses that.’
But that doesn’t fluster Fabian Ueck. Once the first wind turbine goes up, the tension just disappears. He keeps full focus while the parts are transported and lifted. ‘It all just came together. The right crane, in the right place, for the right purpose,’ says the crane operator with a look of satisfaction on his face. By 11 October 2023, when the Provence Grand Large project management team announced that three floating wind turbines had successfully been installed at high sea, the LR 11350 and the team from Schmidbauer had long since moved onto the next construction site. High up in the French Alps, in cramped conditions, a bridge across a gorge is being restored. ‘You rise to each and every challenge, learning as you go,’ says the crane operator with a glint in his eye. At least there’s no mistral to worry about. That said, it might well snow soon.
The offshore research field
Floating wind farms open up ‘new territory’ on the high seas. Only a small fraction of the world’s oceans is shallow enough, at less than 60 metres deep, to accommodate conventional offshore wind turbines anchored by what are known as monopiles in the seabed. However, floating wind turbines can now also be used in regions with a water depth of up to 300 metres, since they are anchored to the seabed by steel cables. This makes them a viable solution for generating wind energy in offshore locations around the world that had previously been deemed unusable.
As well as researching the benefits of the location of the Provence Grand Large pilot project, our partners in the field of science are also investigating the ecological and marine biological considerations of expanding offshore wind energy. This includes an ornithological radar to record the movements of migratory birds and seabirds. This involved installing a radar station on the Napoléon beach at Port-Saint-Louis-du-Rhône and another on one of the floating platforms. This will for the first time tell us whether, and if so how, offshore wind farms influence the natural flight routes of the birds.
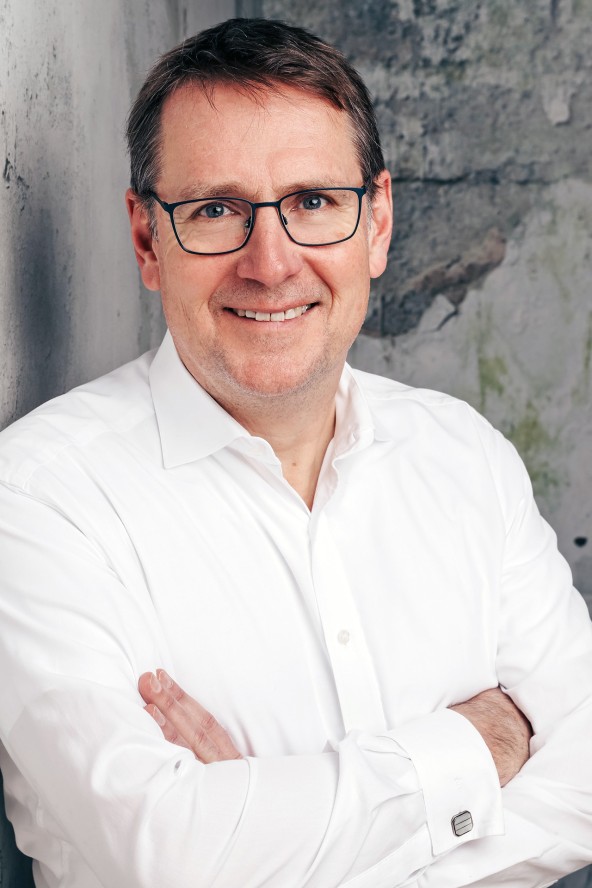
First movers in a new dimension of offshore wind energy generation
Is the pilot project Provence Grand Large setting new standards in the field of offshore wind energy generation? We asked Jan Vollrath, VP of Sales at Siemens Gamesa Renewable Energy.
Mr. Vollrath, what does the pilot project Provence Grand Large mean to Siemens Gamesa?
PGL is both our first offshore and our first floating project in France. It is also the first project in which the so-called tension-leg platform (TLP) with a vertically anchored, floating structure is being used. This has several advantages over other concepts, and we anticipate that they can be used on other even larger floating projects in the medium term.
How much did project partners need to be involved in the pilot project?
The PGL project was, in many respects, ‘a first of its kind’. It brings with it many specific demands on all of those involved in the project. A whole series of measures were planned and completed for the first time ever, such as installing the hub straight onto the floating foundations. New tools, processes and crane technologies were put into action. And, even for our teams, much of this represented uncharted waters.
What does that mean for the cooperation between the companies involved?
By their very nature, pilot projects pose a very particular challenge for the working relationship between project partners. This requires communication and coordination on another level of intensity. And it is absolutely paramount that the project partners have total faith in the abilities of others involved. The collaboration on the PGL project was fantastic; it was what made it the success it is.
What were the takeaways from the project, in regard to the future of offshore wind energy?
We learned that we could be even better prepared for specialist projects like this, both in terms of training and technical preparation for employees, and in terms of preparing our equipment. We generally build our offshore plants in northern European waters, where the conditions are different to those in the Mediterranean.
Like what, for instance?
Specifically, high external temperatures combined with strong winds were something we hadn’t encountered before and limitations were revealed in some areas, which we are now working on. I am very confident we will continue to see more and more offshore wind turbines cropping up in warmer regions. That’s why PGL was such a valuable experience.
By clicking on “ACCEPT”, you consent to the data transmission to Google for this video pursuant to Art. 6 para. 1 point a GDPR. If you do not want to consent to each YouTube video individually in the future and want to be able to load them without this blocker, you can also select “Always accept YouTube videos” and thus also consent to the respectively associated data transmissions to Google for all other YouTube videos that you will access on our website in the future.
You can withdraw given consents at any time with effect for the future and thus prevent the further transmission of your data by deselecting the respective service under “Miscellaneous services (optional)” in the settings (later also accessible via the “Privacy Settings” in the footer of our website).
For further information, please refer to our Data Protection Declaration and the Google Privacy Policy.*Google Ireland Limited, Gordon House, Barrow Street, Dublin 4, Ireland; parent company: Google LLC, 1600 Amphitheatre Parkway, Mountain View, CA 94043, USA** Note: The data transfer to the USA associated with the data transmission to Google takes place on the basis of the European Commission’s adequacy decision of 10 July 2023 (EU-U.S. Data Privacy Framework).