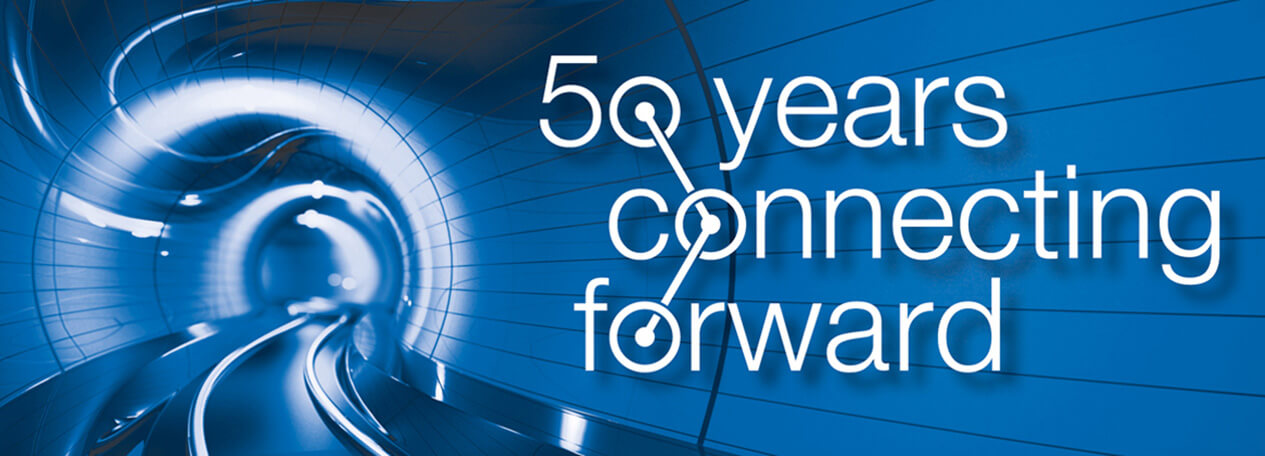
Magazine 2019
Magazine 2019
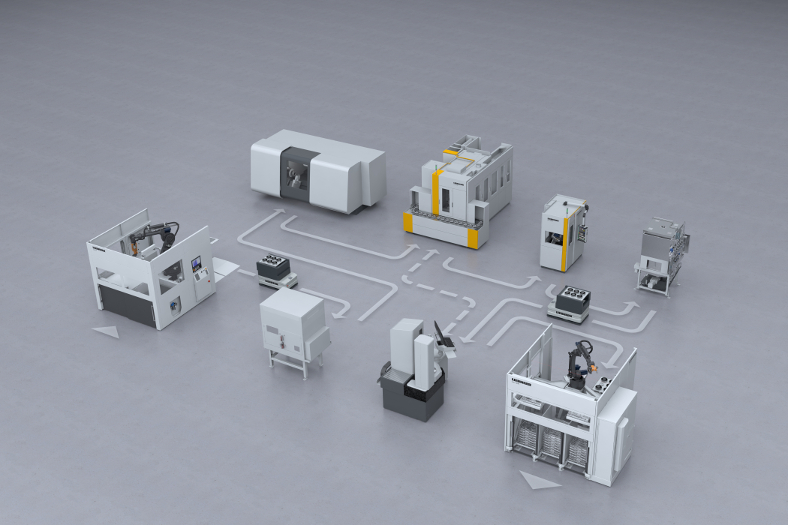
While we still have some way to go to achieve autonomous driving on the road, factories are miles ahead: AGVs (automatic guided vehicles) are already being used in the area of production.
Most read
01
Half a century of Liebherr-Verzahntechnik GmbH means 50 years of commitment to the machinery and plant engineering industry. Gear technology originated in the technology of the revolving tower crane. Hans Liebherr wanted to buy a gear hobbing machine for gear manufacturing, but could not find what he wanted – so he simply built it himself. It’s a typical Liebherr story, since many sectors in the company group have emerged in this or in a similar way. Taking things into one’s own hands: an attitude that can still be found at Liebherr today.
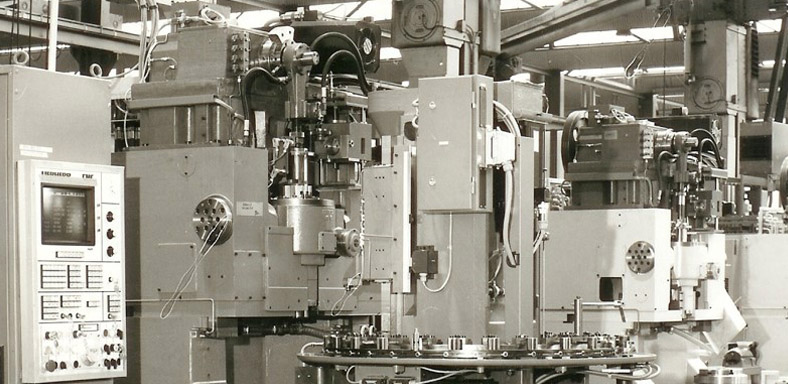
02
Bauer Gear Motor operates two new LC 180 gear hobbing machines at its facility in Slovakia, producing gearing for all facilities. These machines are characterised by their operational versatility, given that they are used to produce around 180 different components in a very wide range of different sizes.
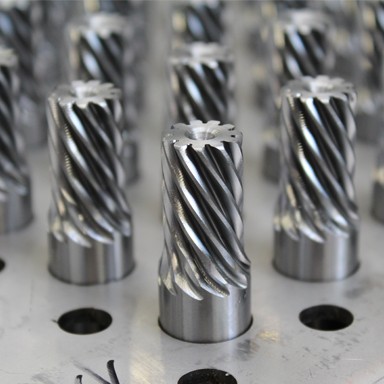
03
“The fire pump is the heart of every fire truck”, explains Michael Schöftner, Head of Mechanical Production at Rosenbauer International AG, the global leader for fire service equipment. The equipment has to withstand enormous loads in cases of operation. Rosenbauer relies on an automation solution for pump manufacturing from Liebherr. The rotary loading system RLS 800 from the Kempten-based automation experts has been deployed in Leonding near Linz for around two years now.
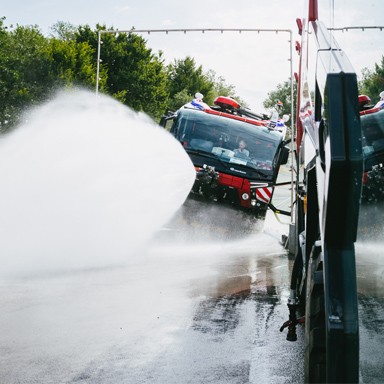
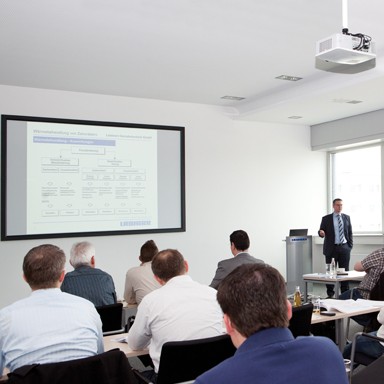
How do you get closer to the customer? For Liebherr the answer is simple: by increasing presence locally.
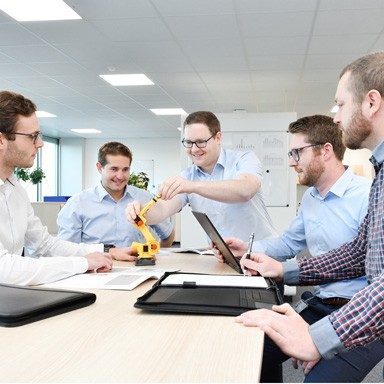
Due to the high demand, the automation division of Liebherr-Verzahntechnik GmbH has restructured the area of robotics and made it a separate department. The editors of Liebherr Magazine went to visit and had a look around.
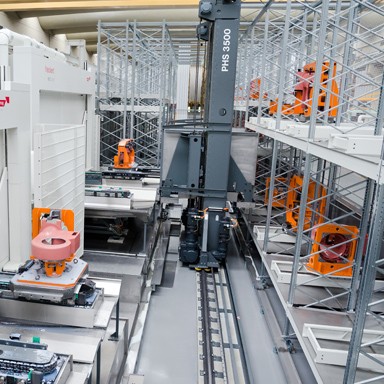
Weishaupt, headquartered in the Upper Swabian town of Schwendi, is a leading provider of burners, heat pumps, heating and condensing-boiler systems, energy recovery solutions, and facility automation. Since mid-2016 Weishaupt’s new burner casing production facility has operated using an automation solution provided by Liebherr-Verzahntechnik GmbH.
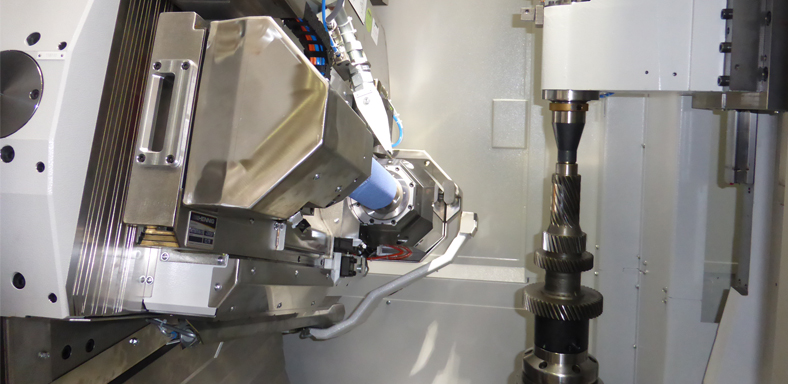
Based on the proven LGG 280 generating grinding machine, Liebherr is presenting the larger LGG 400 M model at IMTS in Chicago.
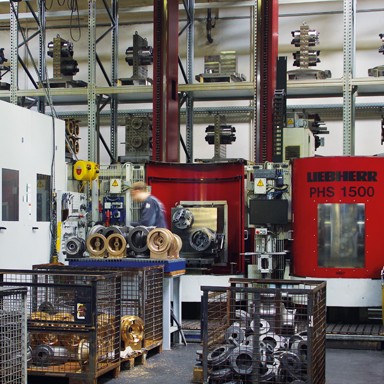
The first PHS 1500 Pro is at Herborner Pumpentechnik. Following an extension and machine change, the third expansion will start soon.
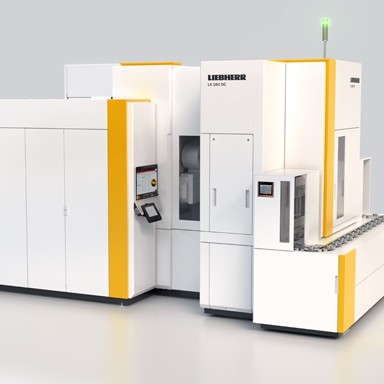
The constantly rising demands from the markets, such as higher accuracy, more effective processes and increased flexibility, require sophisticated machine concepts. For this reason, the new gear skiving machine generation has been equipped among other things with a tool changing system integrated in the machine, multi-machining functions, an integrated measurement device for tools and the option of chamfering during the machining process.
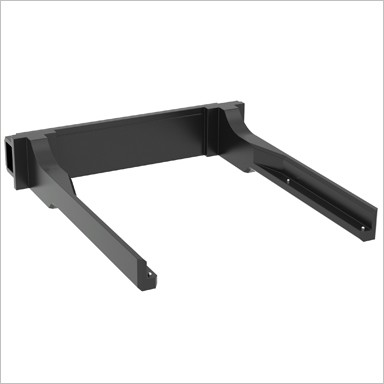
PHS Allround has become a bestseller of Liebherr Automation Systems. The modular pallet handling system appeals to a wide range of different areas of industry with a main selling point being its scalability. It has now been made even more flexible with the new double loader.
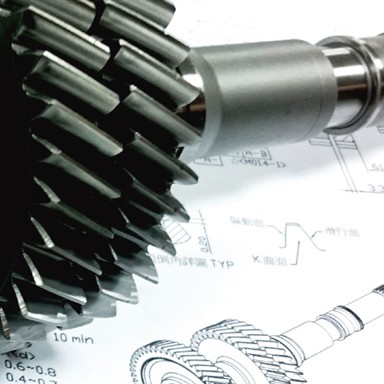
E-cars are very demanding in terms of gear quality. Great Taiwan Gear relies on Liebherr machines.