Be ready for docking!
Your ship must go into dock – think about your cranes as well. With a pre-docking inspection, you are ready for a fast and effective dry-docking.
With a predictive inspection, you only order parts that are required and avoid unplanned delays while your upcoming dry-docking.
Delegate resources and benefit from an even better budget planning and our specialists’ years of experience.
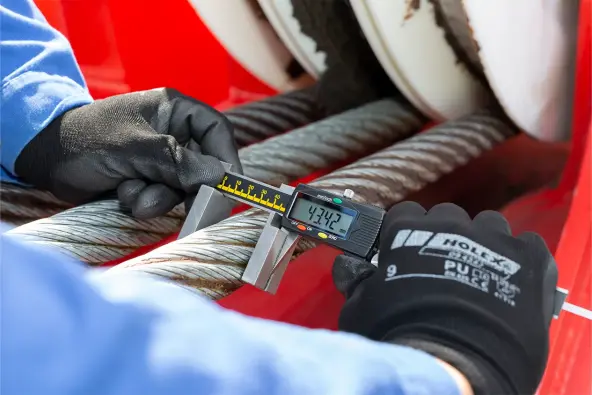
Step 1: Inspection
Four to six months before dry-docking is the time to focus on preparations. Our experienced engineers usually need one day to inspect a crane at a location of your choice worldwide.
- Visual inspection of crane condition
and relevant components - Checking of all electric and electronic configurations
- Monitoring of all hydraulic settings
- Crane function test and rope inspection
- Taking of oil samples for analysis
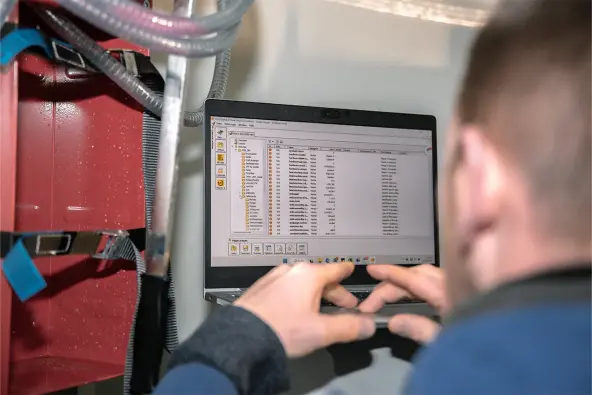
Step 2: Follow-up
Our engineer will issue your individual follow-up report based on the results of the inspection.
It contains:
- Complete check list
- Inspection report
- Oil sample analysis
- Offer of parts and repair solutions if necessary
- General recommendations
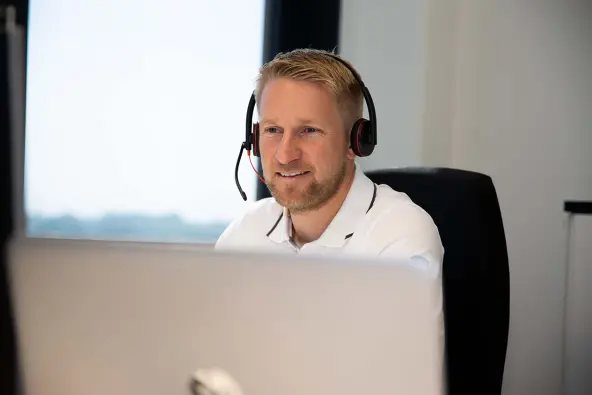
Step 3: Planning and budgeting
We support you in the best possible time and resource management.
Knowing the condition of the crane helps you to avoid unforeseen findings during your dry-docking. A pre-docking inspection gives you the opportunity to avoid unexpected expenses and carefully plan and budget for the eventual work that needs to be done.
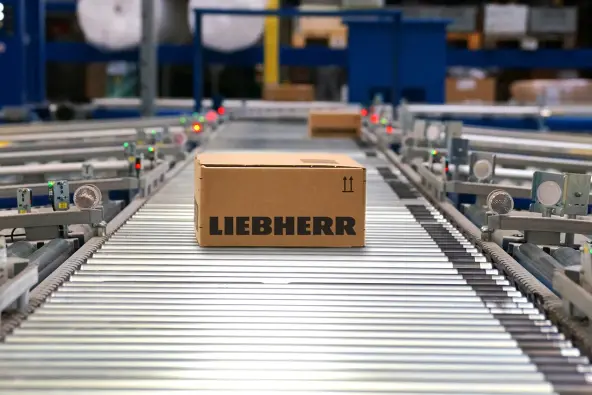
Step 4: Condition-based parts delivery and service
Our global network ensures that all required parts will be available during your dry-docking.
You can decide whether you want them to be delivered to a suitable address before dry-docking or directly to the shipyard.
You have the option that our experienced engineers or other specialists will perform the tasks directly and make your crane fit for new challenges.